Aluminum tube coil, also known as coiled aluminum tube, is an aluminum alloy tube produced through continuous extrusion or drawing processes. This coiled form can be cut to any desired length, reducing the number of connections and thereby minimizing the risk of leaks. It is highly malleable and easy to bend, making it suitable for complex piping arrangements. As a result, aluminum tube coils are widely used in HVAC systems, automotive heat exchange pipelines, and aerospace fuel lines.Quick Quote
In the automotive sector, aluminum tube coils are especially prevalent and are used in various components such as air conditioning lines, radiator/cooler lines, hydraulic systems, and fuel lines. Aluminum tube coils typically need to meet the following standards and certifications:
Aluminum Tube Industry Standards: ASTM B241, ASTM B210, ASTM B221, ASTM B483, ASTM B234
Automotive Industry Certification: IATF 16949
Automotive Brand Material Approvals: Tesla, Ford, SAIC, NIO, BAIC New Energy, Changan Automobile
Aluminum Tube Coil Specifications
Alloys: 3003, 1050, 1060, 1070, 1100, 3103
Outer Diameter: 4-28mm
Wall Thickness: 0.3-1.5mm
Coil Dimensions:OD, 750-1200mm;Height, 310-400mm
Colors: Silver, Antique Bronze, Champagne, Black
Surface Finishes: Polished, Mirror Polished, Sandblasted, Anodized, Powder Coated
Deep Processing: Cutting, Drilling, Bending
Quality Certifications: ISO9001, RoHS
Hot-selling Aluminum Tube Coil sizes
3003/3105 O H14 aluminum Tube Coil
3003 offers about 20% higher strength than 1100 alloy, while maintaining excellent corrosion resistance, workability, and suitability for brazing and welding.
Contact us now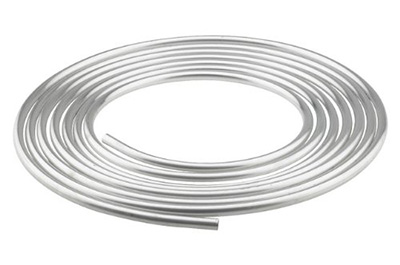
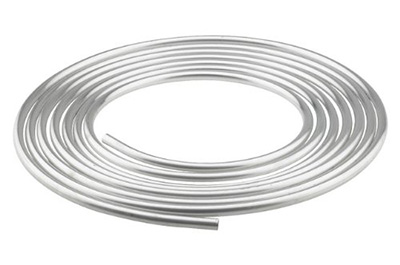
1050/1060/1070 O H12 alu Coil Tube
The 1000 series is pure industrial alu, valued for its enhanced ductility, corrosion resistance, thermal conductivity, and ease of processing, bending, and stretching.
Contact us now1100/1200 O H112 aluminum Coil Tube
1100/1200 Aluminum Tube Coils feature high-purity aluminum for excellent thermal conductivity, corrosion resistance, and versatile processing capabilities.
Contact us now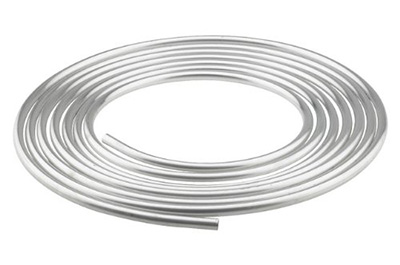
Aluminum Tube Coil Hot Products
Aluminum Coil Tube in Automotive Applications
Air Conditioning Systems:They are employed in AC piping to transport refrigerants.
Fuel Systems:Used for fuel lines to transport and supply fuel.
Braking Systems: Applied in brake lines to transmit brake fluid.
Cooling Systems: Utilized in radiator and cooler connections for cooling purposes.
Chalco—Premier Supplier of Aluminum Tube Coil
Raw Material Assurance: All extrusion billets adhere to international standards, ensuring high-quality products from the source.
Production Capacity: Equipped with advanced extrusion and drawing lines to swiftly fulfill large-volume orders.
Pre-Delivery Inspection:Rigorous testing ensures each batch meets or exceeds industry standards for dimensional accuracy, mechanical properties, and surface quality. Leakage testing ensures Aluminum Tube Coil are leak-free before shipment.
Quality After-Sales Service: Comprehensive support includes technical assistance and quality tracking, ensuring prompt resolution of any post-sales issues to guarantee customer satisfaction.
Bulk Purchase Price Advantage:Economies of scale enable cost control, offering competitive pricing and favorable policies to help customers reduce costs effectively.
Related Products of Aluminum Coil Tubes
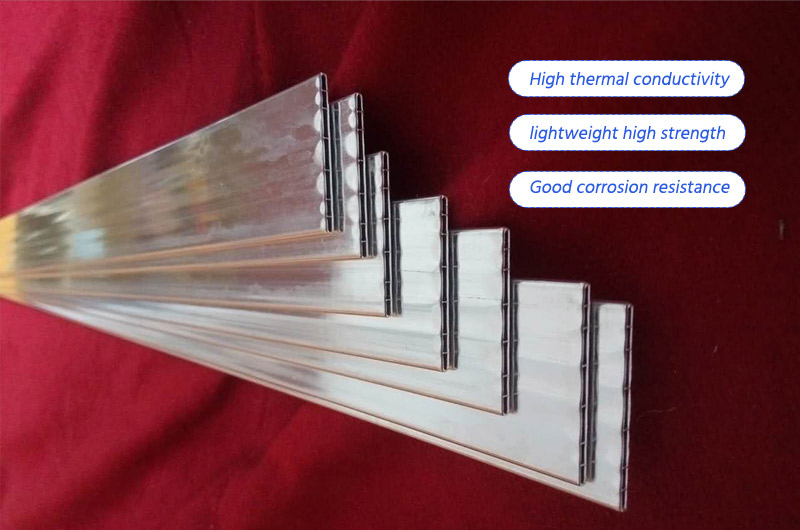
Micro-channel Alu Tubes
Aluminum microchannel tube is a thin-walled, porous, flat-shaped alu……
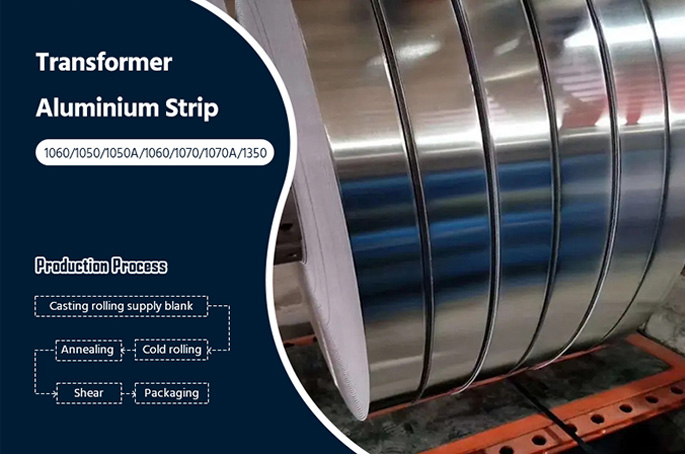
Automotive Flat Alu Tube
1100 1200 flat aluminum tube is a square tube made of pure alu ……
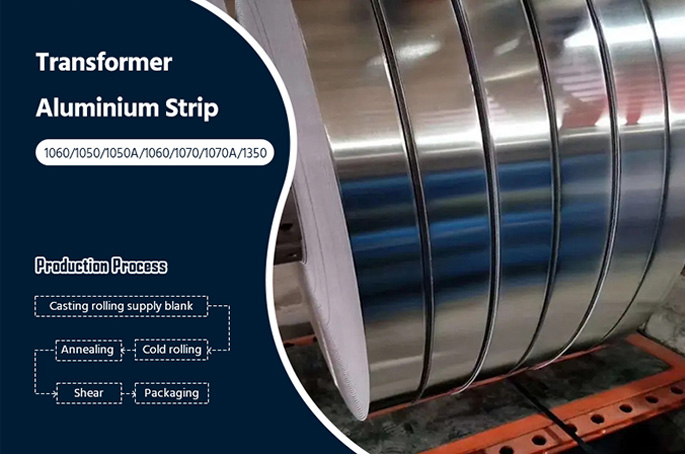
Clad Alu HF Welded Tubes
Cladding aluminium tube is mainly used in condensers, oil coolers……
Aluminum Coil Tube vs Copper Coil Tube: Pros and Cons
Thermal Conductivity
Aluminum Tube Coil : Good thermal conductivity, but thermal conductivity coefficient is about half of copper, slightly lower heat transfer efficiency compared to Copper Tube Coil.
Copper Tube Coil: Excellent thermal conductivity, thermal conductivity coefficient is twice that of aluminum, able to transfer heat more quickly.
Weight
Aluminum Tube Coil : Low density, approximately one-third that of copper, significantly reduces system weight, suitable for applications requiring weight reduction.
Copper Tube Coil: High density, heavier weight, despite superior thermal conductivity, increases overall system weight.
Cost
Aluminum Tube Coil : Low material cost, lower manufacturing cost, suitable for mass production.
Copper Tube Coil: High material cost, leading to higher manufacturing costs, economically less favorable.
Corrosion Resistance
Aluminum Tube Coil : Forms an aluminum oxide protective layer in air, excellent corrosion resistance, particularly suitable for humid and marine environments.
Copper Tube Coil: Naturally strong corrosion resistance, suitable for most environments, but may experience galvanic corrosion when in contact with aluminum or other metals.
Strength and Durability
Aluminum Tube Coil : Lower strength, requires increased wall thickness for high-pressure applications, limiting its range of applications.
Copper Tube Coil: High strength and durability, strong resistance to mechanical damage, suitable for high-pressure and harsh environments.
Common Q&A
1.What are the advantages of Aluminum tube coil over straight tubes?
Ease of transportation and storage: Aluminum tube coil are compactly coiled, saving space and reducing transportation costs.
Ease of processing and installation: They can be cut to any required length, minimizing joints and reducing the risk of leaks.
High flexibility: Coiled tubes are easier to bend, making them suitable for complex piping layouts.
2.Why are Aluminum tube coil the best choice for automotive heat exchange systems?
Excellent corrosion resistance: Aluminum forms an oxide layer that significantly enhances corrosion resistance and prolongs lifespan.
Seamless design: With no joints, Aluminum tube coil reduce the risk of leaks, enhancing system reliability.
Compact layout: They can be tightly arranged in limited spaces, meeting the compact design requirements of modern vehicles.
Small diameter spiral design: Using small-diameter aluminum tubes allows for spiral arrangements, increasing heat transfer surface area and efficiency.
Cost-effectiveness: Compared to copper, aluminum is more cost-effective, lowering manufacturing and maintenance costs.
3. Why is leak testing necessary for Aluminum tube coil?
Aluminum tube coil undergo leak testing because even the smallest leaks can adversely affect heating and cooling systems. Each coil is immersed in a water tank, filled with nitrogen using a compressor, and tested at 400 PSIG to ensure no leaks. This test ensures proper connection of heat pumps to the coils and smooth airflow, guaranteeing product reliability and performance.