Microchannel aluminum tubes are thin-walled, multi-channel flat aluminum profiles widely used in key components such as automotive air conditioning condensers, evaporators, and oil coolers. As the demands for heat transfer efficiency and system lightweighting in modern vehicles continue to increase, the design of microchannel aluminum tubes is evolving towards higher channel counts and ultra-thin walls.
Chalco's microchannel aluminum tubes offer designs with up to 60 channels and a minimum wall thickness of 0.15 mm, effectively enhancing cooling performance, reducing system weight, and significantly improving fuel efficiency and cooling effectiveness.Welcome to contact
Furthermore, our strict quality control measures and advanced production processes ensure that every aluminum tube meets the highest standards, making them the preferred choice for automotive manufacturers and heat exchanger suppliers worldwide.
Chalco Aluminum Microchannel Tube Hot Products
Aluminium Micro-channel Tube
Alloys:1050, 1100, 3003, 3102
Width:8mm-60mm
Wall thickness:>0.35mm
Contact us now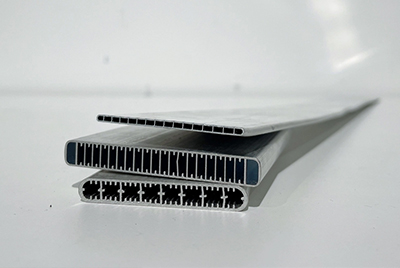
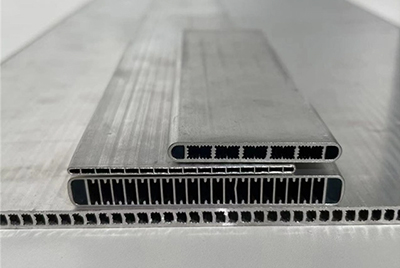
Wide multi-port extrusions (MPEs)
Alloys:6061, 6063
Width:60-460
Channels:9-80
Applications:Battery cooling in electric vehicles
Contact us now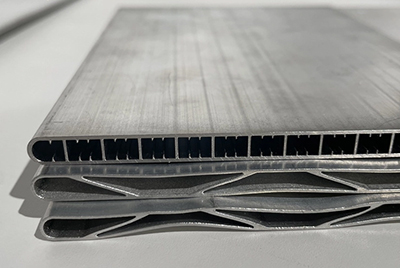
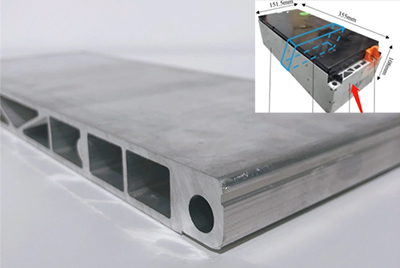
CNC Aluminum Extrusion Battery End Plate
Alloys:6061, 6063
Surface:anodized, polished, milling process
Applications:EV battery module
Contact us nowAlu HF Welded Dimple Hourglass Tube
Alloys:4343/3003/4343, 4343/3005/4343
Wall thickness:0.22-0.5mm
Applications:Heavy Truck And Off-road Vehicle Heat Exchanger
Contact us now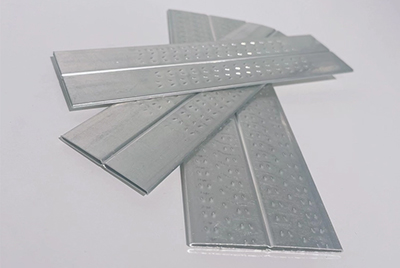
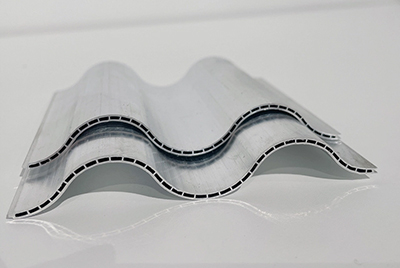
Alu Micro Channel Serpentine tube
Alloys:1050, 1100, 3003, 3102
Size:2.4*50mm
Applications:Aluminum Water Liquid Cooling Serpentine Tube for EV Battery Packs.
Contact us nowWhat are the common shapes of microchannel aluminum tubes?
Microchannel aluminum tubes are composed of multiple microchannels, which come in various shapes, including rectangular, triangular, and circular. The channel width is typically less than 0.5 mm. The microchannels can be arranged in parallel or serpentine patterns to maximize the heat transfer surface area. This flexible design helps optimize heat transfer efficiency across a wide range of applications.
If you need assistance in selecting the best microchannel design for your specific heat exchange requirements, we can provide professional consultation and solutions.Get the solution
Why do microchannel aluminum tubes need surface coating?
Microchannel aluminum tubes are susceptible to corrosion in harsh environments, which can affect their performance and lifespan. Applying coatings to the aluminum surface can significantly reduce corrosion rates, thereby protecting the integrity and performance of the tubes.
Pushing the Limits: Chalco's Six Core Technologies for Microchannel Aluminum Tubes, Redefining Efficient Heat Dissipation Solutions
Chalco's microchannel aluminum tubes redefine efficient heat dissipation solutions with high technological content and complex processes. They feature six core technologies that demonstrate superior production capabilities and product performance.
1. Exceptional Extrusion Ratio
Chalco's microchannel aluminum tubes achieve an extrusion ratio exceeding 400 times, pushing beyond the limits of aluminum extrusion technology. This extreme extrusion ratio ensures better mechanical properties and a compact structure, meeting the stringent requirements for efficient heat transfer.
2. Ultra-High Dimensional Accuracy
The dimensional accuracy of Chalco's microchannel aluminum tubes surpasses national standards, ensuring that each tube meets strict dimensional tolerance requirements, thereby enhancing the overall performance and consistency of heat exchange systems.
3. Outstanding Air Tightness
Each microchannel heat exchanger contains 50-150 microchannel tubes, and any defect in air tightness could render the entire unit useless. Chalco maintains stringent quality control to keep air tightness standards below 15 PPM, ensuring product reliability.
4. High-Purity Refined Aluminum Billets
With extremely thin walls, Chalco's microchannel aluminum tubes demand billets of exceptional purity and low hydrogen content. Chalco utilizes high-purity refined billets with hydrogen content ≤0.09%, reducing leakage risk and extending product lifespan.
5. Surface Zinc Spraying Technology
To prevent corrosion, Chalco applies a zinc spray coating to the surface of microchannel aluminum tubes. Chalco's unique capability in this area effectively provides anti-corrosion protection, enhancing suitability in harsh environments.
6. Online Flaw Detection and Quality Inspection Technology
The production of microchannel aluminum tubes is highly challenging, making quality control crucial. Chalco utilizes advanced online flaw detection and surface quality inspection technologies to promptly identify and mark defective products, ensuring high quality and consistency.Free Samples
What are the characteristics of parallel flow aluminum tube?
Higher Thermal Conductivity
The thermal conductivity of microchannel aluminum tubes is approximately 230 W/m·K. Although this is lower than copper's 400 W/m·K, it is higher than standard aluminum's 237 W/m·K. This means that microchannel aluminum tubes can effectively transfer heat while maintaining a lightweight profile, making them highly suitable for demanding heat transfer applications, particularly in cooling and heating systems.
Compact Design with High Surface Area to Volume Ratio
Microchannel aluminum tubes feature a high surface area to volume ratio, which helps achieve efficient heat transfer in limited spaces. This compact design is ideal for applications with space constraints, saving equipment space and reducing both material and installation costs.
Outstanding Corrosion Resistance and Lightweight Design
Chalco Aluminum's tubes feature excellent corrosion resistance and a lightweight design, helping automotive manufacturers significantly improve cooling system efficiency while reducing overall vehicle weight and enhancing fuel efficiency. These advantages make our products particularly effective in electric vehicles.
Microchannel aluminum tube lightweight solutions in various fields
Automotive Heat Exchange Systems
Microchannel aluminum tubes are widely used in automotive radiators, condensers, and evaporators. Their lightweight structure, excellent heat transfer capability, and corrosion resistance make them essential for managing engine temperature, improving fuel efficiency, and enhancing overall vehicle performance.
Automotive Battery Cooling Systems
New energy vehicles require efficient battery temperature management. Wide multi-port extrusion (MPE) aluminum, with its optimized heat transfer design, is widely used in battery cooling systems to maintain optimal battery temperatures. This design is also effective in agricultural equipment and other industrial applications.
HVAC Systems (Heating, Ventilation, and Air Conditioning)
Microchannel aluminum tubes are used extensively in HVAC system condensers and evaporators due to their efficient heat transfer, HVAC Cooling System Components and compact design. They offer optimal cooling performance and help save energy, making them ideal for residential, commercial, and industrial HVAC systems.
Electronic Device Cooling Systems
As electronic devices become more compact and powerful, microchannel aluminum tubes are increasingly used for cooling electronic components. They have excellent heat dissipation capabilities, making them ideal cooling solutions for laptops, smartphones, gaming consoles, and LED lighting.
Why choose Chalco parallel flow Micro-channel aluminum tube?
1. International Quality Standard Certification
Chalco Aluminum has passed the requirements of the automotive IATF16949 standard audited by BSI (British Standards Institution), providing quality compliance for continuously expanding the automotive product market and achieving high-quality development.
2. Serving Global Renowned Automotive Manufacturers
Chalco Aluminum serves Tesla, Ford, Shanghai Automobile, Weilai Automobile, Beiqi New Energy, Changan Automobile and other famous new energy automobile manufacturers. Some models of automotive plate material certification.Purchase Now
3. High-Quality Raw Materials and Superior Production Capabilities
Chalco Aluminum uses premium raw materials combined with advanced extrusion capabilities to ensure product consistency and exceptional performance. Through stringent material selection and sophisticated production processes, we guarantee the high quality of every microchannel aluminum tube, providing our customers with reliable heat dissipation solutions.
4. Multiple Molds and Customized Solutions
We possess multiple sets of molds, enabling us to offer customized product designs based on specific customer needs. Regardless of how unique a customer's requirements may be, we can provide tailored design and production support to ensure perfect compatibility in practical applications.
5. Complete Heat Exchange System Solutions
In addition to microchannel aluminum tubes, Chalco Aluminum offers a complete range of heat exchange system materials, including brazing sheets, aluminum tubes for heat exchangers, and composite brazing foil, meeting customers' comprehensive needs in heat exchange systems.
One-stop Heat Exchange System Solutions
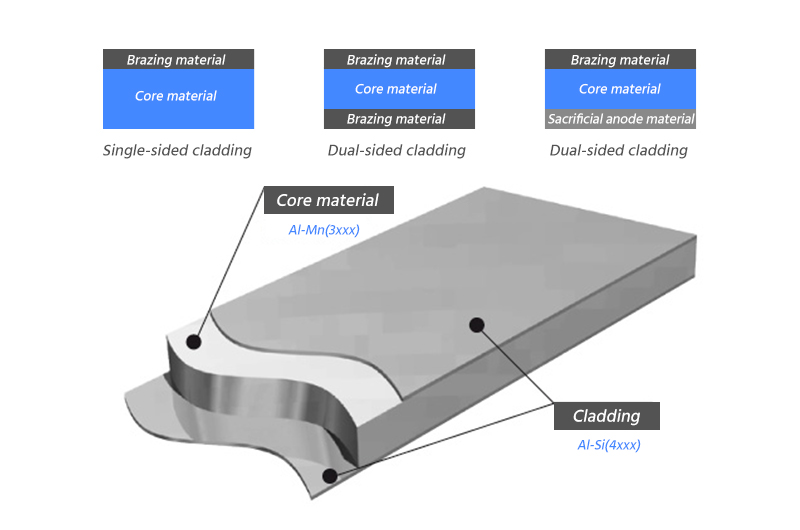
Brazing Sheet in Auto
Brazing sheet is a layered aluminum alloy with a lower……
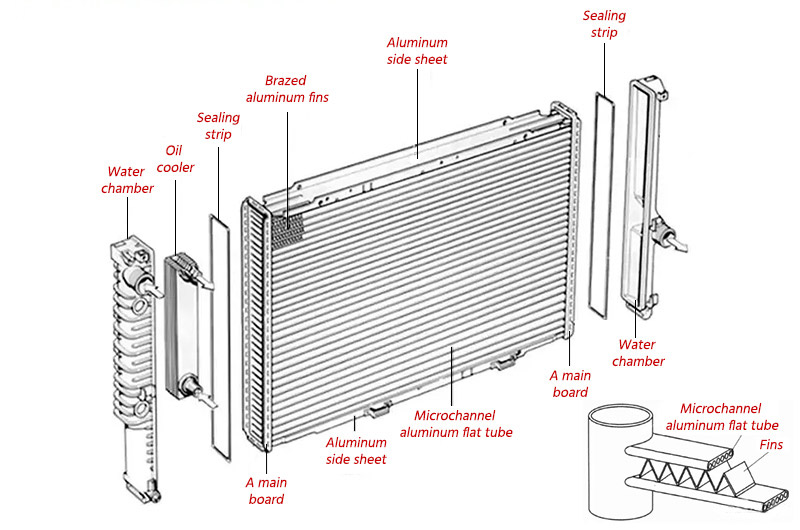
Alu tubes for heat exchangers
The aluminum heat exchanger is composed of aluminum tubes……
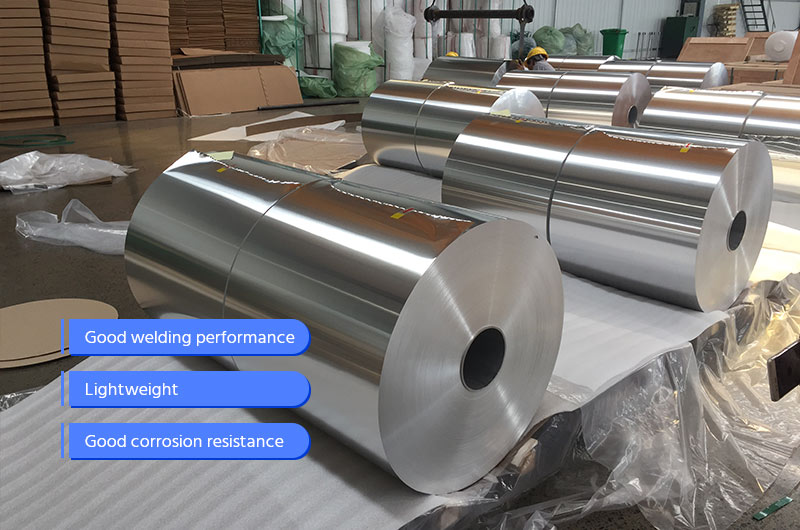
Auto Brazing Clad Foil
Brazing composite foil for automobiles is mainly used in pipelines……
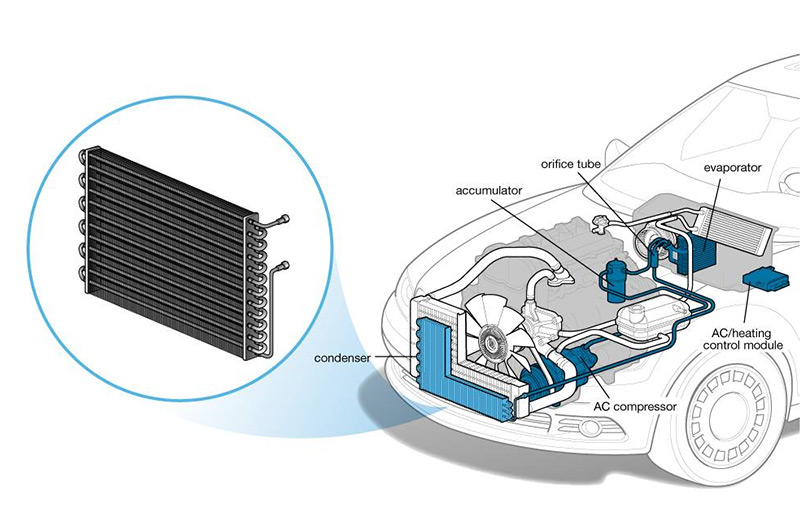
Alu Brazing Welding Material
Aluminum brazing welding material are usually used to wet……
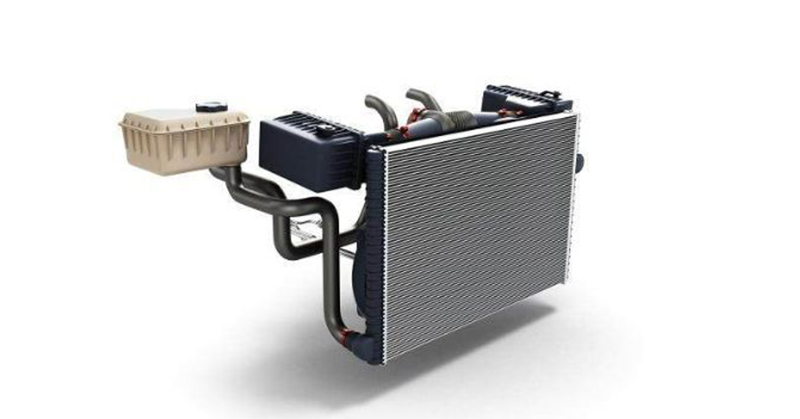
Auto Brazing Clad Alu Coil
Chalco Aluminum produces Automotive Brazing Composite Aluminum Coil……
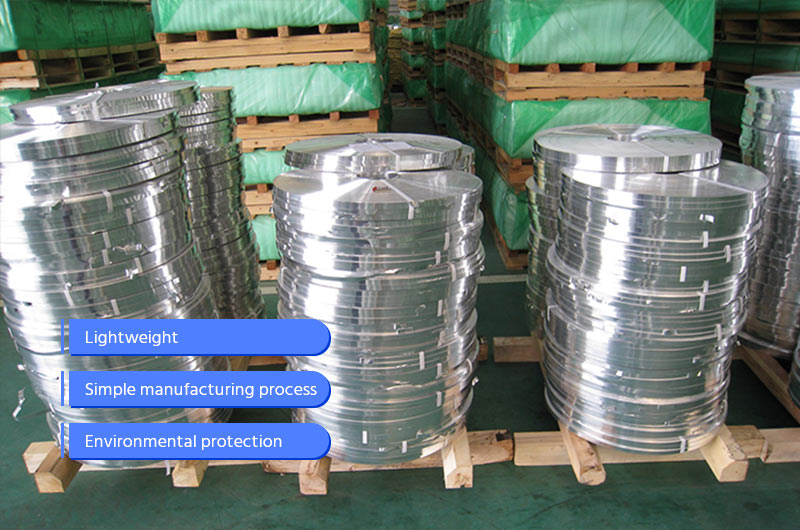
Non-clad Brazing Alu Strip
4104 4004 4047 6951 4045 Non clad brazing aluminum strip……
Are You Looking for an Aluminum Supplier?
If you need a professional aluminum supplier to provide you with high-quality, cost-effective aluminum, we will be your best choice.
The specification introduction of micro-channel tubes for heat exchanger
Alloy | Temper | Supply type | Dimensions | |
Size name | Size range mm | |||
1050, 1100, 1197, 3003, 3102, 3026 | H12 | Straight plate (neck, no neck) | Length L | 50.0-6000.0 |
Coil | Coil ID | 400-550 | ||
Coil OD | 700-1500 | |||
Coil Width | 300-1000 |
Cross Section Dimensions | |||||
Width w | Height H | Plane wall thickness t1 | Thick ribs t2 | Side wall thickness t3 | Hydraulic diameter De |
6.00-60.00 | ≤3.50 | 0.15-0.45 | 0.15-0.45 | 0.30-0.80 | 1.0 |
The mechanical properties of automobile aluminum radiator flat tube
Alloy | Temper | Tensile Strength Rm MPa | Yield Strength Rp0.2 MPa | Elongation A50mm % |
not less than | ||||
1050 | H112 | 60 | 20 | 23 |
1100 | 75 | 20 | 20 | |
3102 | 75 | 30 | 22 | |
3003 | 95 | 35 | 20 | |
3026 | 85 | 35 | 20 |
Burst pressure of heat exchangers for automotive air conditioners | ||
non electric vehicle | electric car | |
condenser | Evaporator | |
≥11.5 | ≥5.5 | ≥11.5 |
The dimensional deviation of micro channel condenser aluminum flat tubes
Cross-sectional dimension deviation | ||||
Width | Height | Plane wall thickness | Thick ribs | Side Wall Thickness |
±0.05 | ±0.02 | ±0.05 | ±0.08 | ±0.08 |
Supply length of straight flat tube and its shrinkage size deviation | |||
category | size | Allowable deviation | |
Length L | ≤1 000.0 | ±0.5 | |
>1 000.0-2 000.0 | ±1.5 | ||
>2 000.0-6 000.0 | ±2.0 | ||
end necking | For positioning | Width W1 | ±0.05 |
Height H1 | ±0.03 | ||
Neck length L1 | ±0.3 | ||
Non-positioning | Width W1 | ±0.1 | |
Height H1 | ±0.03 | ||
Neck length L1 | ±0.5 |
Longitudinal curvature and longitudinal side curvature of flat tubes | |
Curvature at the following lengths | |
Every 300 mm length | Overall length (L m) |
≤0.3 | ≤1.0×L |
Twist degree of straight flat tube | |
Twist on the following overall length (L meters) | |
L≤1 | L>1 |
≤1.0×L | ≤1.0 |
Microchannel Aluminum Tubing Buyer's Guide
Microchannel aluminum tubes require careful selection to match specific application needs. Consider the following key factors when making a purchasing decision:
1. Material Quality
Select high-quality aluminum alloys to ensure that the microchannel tubes offer excellent corrosion resistance and thermal conductivity. High-grade materials help extend the lifespan of the product.
2.Size and Design
The number of channels, wall thickness, and shape of the tubes directly affect heat transfer efficiency and overall system performance. Select the appropriate design, such as rectangular, circular, or triangular microchannels, based on your specific application.
3. Coating Type
Consider different coating options during purchasing, such as pre-brazing agent coating, galvanization, or e-coating, to ensure that the tubes have good corrosion resistance in various environments, especially in coastal or industrial settings.
4. Customization Requirements
If your project has specific needs, opt for suppliers who provide customization services to ensure that the microchannel tubes meet your application standards in terms of shape, size, and surface treatment.
5. Supplier Credentials and Certification
Ensure that the supplier holds international certifications, such as IATF 16949, ISO 9001 Quality Management System certification, and ISO 14001 Environmental Management System certification, to guarantee that their products meet the stringent quality requirements of automotive and industrial applications.
6. Price and Supply Capacity
Price and supply capacity are also crucial when choosing a supplier. Partner with suppliers who offer stable supply capabilities and competitive pricing to ensure timely project completion and cost control.
Frequently Asked Questions About Microchannel Aluminum Tubes
Here, we have compiled some common questions about microchannel aluminum tubes to help you better understand the product's features and applications. We hope these FAQs can address your concerns during the use and purchase of microchannel aluminum tubes.
1. What is an Aluminum Microchannel Heat Exchanger?
An aluminum microchannel heat exchanger (MCHE) is a highly efficient fin-and-tube type heat exchange device commonly used in automotive, air conditioning, and refrigeration applications. Its design allows efficient heat exchange between air and fluid, resulting in high heat transfer efficiency.
2. How Are Aluminum Microchannel Tubes Different from Traditional Heat Exchanger Tubes?
Aluminum microchannel tubes use a multi-channel structure that increases the surface area per unit volume, thus enhancing heat transfer efficiency. Compared to traditional heat exchanger tubes, microchannel designs allow for more efficient heat transfer and a lighter structure, making them ideal for modern high-efficiency heat exchange systems.
3. What Are the Advantages of Aluminum Microchannel Tubes in Automotive Applications?
Aluminum microchannel tubes are lightweight, highly efficient in heat transfer, and corrosion-resistant. In automotive cooling systems, they can effectively reduce vehicle weight, improve fuel efficiency, and provide excellent cooling for engines, thereby extending engine lifespan.
4. How Do Microchannel Aluminum Tubes Improve HVAC System Energy Efficiency?
Microchannel aluminum tubes increase the heat transfer surface area, improving heat exchange efficiency and reducing compressor load, thereby lowering energy consumption. Thus, they are crucial components for enhancing the energy efficiency of HVAC systems.
5. Can Microchannel Aluminum Tubes Be Bent?
Yes, microchannel aluminum tubes can be bent according to application requirements to fit various equipment and system installation needs. Proper bending methods can ensure the integrity and performance of the tubes.
6. What Aluminum Grades Are Used to Manufacture Microchannel Tubes?
Microchannel aluminum tubes are typically made from 1050, 1100, 3003, 3102, 6061 and 6063 aluminum alloys, which offer excellent corrosion resistance and good workability, suitable for efficient heat exchange requirements.
7. What Are the Key Steps in Manufacturing Aluminum Microchannel Tubes?
The manufacturing of aluminum microchannel tubes involves multiple steps, including aluminum billet collection, impurity removal, ultrasonic cleaning, heating and extrusion, zinc spraying, straightening, and cutting. Each step is designed to improve the quality and durability of the product.
8. How to Choose Suitable Microchannel Aluminum Tubes?
When selecting microchannel aluminum tubes, consider factors such as material quality, coating type, dimensional accuracy, production process, and supplier credentials. High-quality materials and appropriate coatings can significantly enhance the performance and lifespan of the tubes.
Chalco can provide you the most comprehensive inventory of aluminum products and can also supply you customized products. Precise quotation will be provided within 24 hours.
Get a quote