Compared to many metals, aluminum naturally has excellent lightweight and corrosion-resistant properties, making it popular in the marine industry.
We are a trusted marine aluminum supplier, offering a variety of aluminum alloys and extrusions for your marine applications.
Quick Quote
Marine aluminum product specifications
Chalco provides a range of standard and custom aluminum products for marine and shipbuilding projects.
- Classification society certifications: DNV GL, ABS, LR, BV, Rina
- Standards: ASTM B211, EN754, EN755, EN573, EN485, ISO 9227, ASTM B928, ASTM B117, ASTM G85
We offer free certification documents, quality inspection reports, technical data sheets, and application case PDFs. Factory visits can also be arranged upon request.
Marine corrosion resistant aluminum alloy
-
Marine aluminum 5083 H116 H32
The strongest non-heat-treated marine-grade aluminum alloy with excellent seawater corrosion resistance.
-
Marine aluminum 5251 H22
A medium-strength aluminum alloy with good ductility.
-
Marine aluminum 5754 H114
Excellent seawater corrosion resistance.
-
Marine aluminum 6082 T6 T651
The highest-strength structural aluminum alloy in the 6000 series.
-
Marine aluminum 6061
Excellent machinability and seawater corrosion resistance.
-
Marine aluminum 5052e
High fatigue strength and good machinability.
-
Marine aluminum 5383
High strength, excellent corrosion resistance, good plasticity, and superior welding performance.
-
Marine aluminum 5456
Extremely high strength and outstanding seawater corrosion resistance.
-
Marine aluminum 6063
For decorative and structural applications.
Here is a quick comparison table to help you visualize the differences:
Alloy | Strength | Corrosion resistance | Common applications |
5083 | High | Excellent | Hull, pressure vessels |
5086 | High | Excellent | Hull, gangways |
5456 | Very high | Excellent | Shipbuilding, storage tanks |
6061 | Medium to high | Good | Structural components, marine fittings |
6063 | Medium | Good | Rails, frames, pipelines |
Whether you need high strength, excellent corrosion resistance, or easy machinability, marine aluminum alloys can meet your requirements.
Understanding the properties of marine aluminum is essential for making the right choice for your shipbuilding applications.Quick Quote
Marine aluminum products
Different alloys are available in various stock forms, including sheet, plate, coil, tube, extrusion, tri-plate transition joints, and bar.
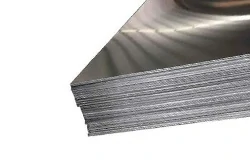
Marine Aluminum Sheets
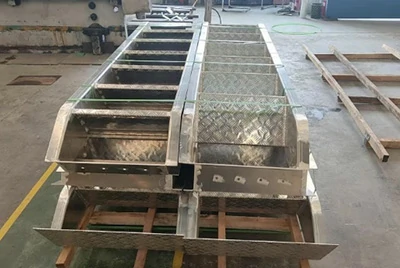
Marine aluminum Boat
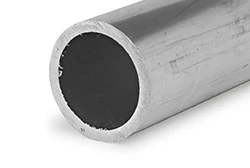
Marine Aluminum Tubing
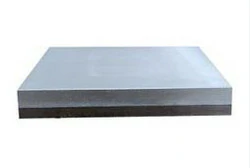
Marine Aluminum Transition Joint
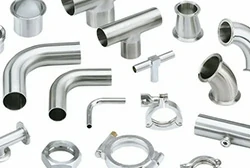
Marine Aluminum Fittings
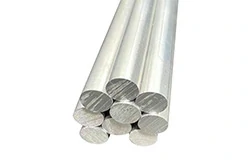
Marine Aluminum Bar
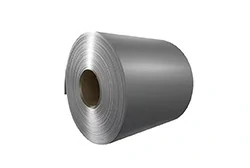
Marine Aluminum Coil
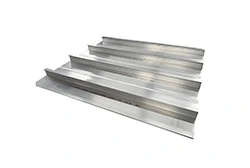
Marine Ribbed Plate
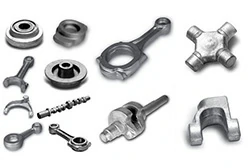
Marine Aluminum Forgings
Marine aluminium sheets plates
Alloy | 5052 5083 5086 5754 6061 6063 6082 |
Temper | O, H12, H13, H14, H15, H16, H18, H19, H20, H111, H112, H114, H116, H321, etc |
Size | 4x8 aluminum sheet, 4x10 aluminum sheet, 5x10 aluminum sheet |
Thickness | 2mm, 2.5mm, 3mm, 3.5mm, 4mm, 5mm, 6mm, 10mm, 30mm thick, etc |
Width mm | 100-2600 |
Length mm | 500-16000 |
Popular marine-grade aluminum sheets products
Marine aluminum alloys mainly include 5000 series aluminum magnesium alloy materials (5083, 5086, 5383), 6000 series aluminum magnesium silicon alloy materials, and aluminum zinc magnesium alloy materials (6061, 6063, 6082). The tempers include O, H111, H112, H116, H321, etc. Sizes can be customized.
-
5052 marine plate O H111 H112 H22 H32
Applications: hull, bottom, cabin walls, and ship partitions; ship deck covering materials, etc.
Machinability Impact resistance -
5083 marine plate O H111 H116 H321
Applications: internal and external panels of the hull; marine storage tanks and fuel tank panels.
Strong corrosion resistance Lightweight design -
5086 marine plate H32 H116
Applications: Ship electrical systems, pipelines and other components
Corrosion resistance weldabilityelectrical conductivity -
2024 marine plate T3 T4 H112
Applications: ship engine parts
Good strengthhigh temperature resistance -
7075 marine plate T6 T651
Applications: Ship high speed boat and other parts
Good strengthhigh temperature resistance -
6061 marine plate T6 T651
Applications: Ship outfitting, cabins and other components
processability Good strengthcorrosion resistance -
5754 marine plate O H111 H112
Applications: used in ship structures such as welded structures, storage tanks, and pressure vessels.
Medium strength Easy processing -
5454 marine plate O H111 H22 H32 H112
Applications: hull structural components, deck covering plates, and internal decorative panels.
High impact resistance Recyclable -
5059 marine plate O H111 H116 H321
Applications: hull structure and internal cargo hold panels, compartment partition panels, and ship deck.
Lightweight Good welding performance -
5A01 marine plate O, H32, H111
Applications: hull structure, deck, cargo hold walls, partitions, storage systems, etc.
Good formability High fatigue strength -
5A05 marine plate O H112
Applications: structural components of hull, ship bulkheads, deck; and ceilings, floors cabin doors.
Corrosion and oxidation resistance -
5A06 marine plate O H112
Applications: commonly used for the construction and repair of ship shells, hull structures, decks, and cabins.
High strength Processing performance -
Applications: used for shell components of ships; ship's fuel tanks and storage compartments.
Corrosion resistance Weldability
Aluminum honeycomb panels
In the shipbuilding industry, aluminum honeycomb panels play a crucial role due to their fire resistance and lightweight properties. They provide optimal strength values in all applications.
Thanks to their lightweight and cost-effectiveness, aluminum honeycomb composite panels are particularly suitable for ship interiors, such as ceilings, walls, and furniture, as well as exterior balcony partitions.
Contact us now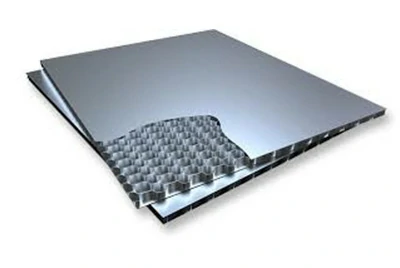
Aluminum honeycomb panel size range
Sheet Size mm | Thickness mm |
2500 × 1250 | 5, 6, 10, 15, 20 |
3000 × 1500 | 25 |
3050 × 1500 | 20 |
3125 × 1250 | 20, 25 |
3125 × 1500 | 6, 10, 15 |
6250 × 1250 | 6, 20 |
6250 × 1500 | 10, 15, 20 |
Aluminum Treadplate
We supply 3003 and 6061 aluminum tread plates.
The 3003 aluminum tread plate has a bright finish and excellent corrosion resistance. The 6061 aluminum tread plate has lower corrosion resistance but higher strength than 3003.
Chalco offers aluminum tread plates in various thicknesses, sizes, and surface treatments to meet different needs and requirements.
Aluminum tread plates, also known as flooring or pattern plates, are commonly used in marine applications. Chalco provides aluminum tread plates in H22, H114, F, and O tempers.
Contact us now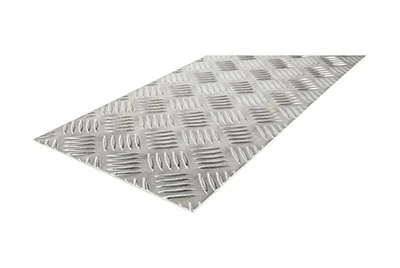
Available Stock Sizes:
1ft x 1ft, 1ft x 2ft, 1ft x 4ft, 2ft x 2ft, 2ft x 4ft, 4ft x 4ft, 4ft x 8ft, 4ft x 10ft, 5ft x 8ft, 5ft x 10ft, 5ft x 12ft, or Cut to Size and Custom Shapes. Stock sizes may vary +/- 1/8"
Marine ribbed plate
High-strength 6061 and 5083 aluminum alloys are commonly used to enhance corrosion resistance and mechanical strength. Chalco offers single-rib panels, double-rib panels, and multi-rib panels.
For size information, please contact us!Quick Quote
Marine ribbed panels offer an excellent strength-to-weight ratio, making them ideal for marine applications where weight reduction is required without compromising structural integrity.
Contact us now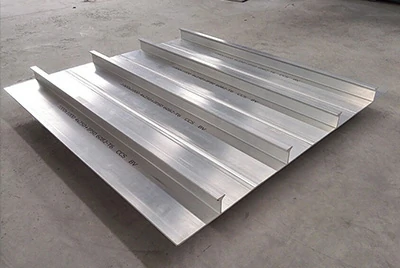
Aluminum foam panels
- Produced using a continuous casting method, creating a honeycomb-like cast aluminum foam with a visually appealing continuous skin on all panel surfaces.
- Standard panel size is 4 ft × 8 ft (1220 mm × 2440 mm), with custom lengths available up to 12 ft (3657 mm).
- Foam density ranges from 0.14 g/cc to 0.52 g/cc, with a weight of 2.96 kg/m² to 10.42 kg/m² (0.61 lbs/ft² to 2.13 lbs/ft²).
- Class A fire rating with a flame spread index of "0".
- Made from up to 100% recycled materials and is 100% recyclable.
- Functions as a sound-absorbing, soundproofing, and vibration-damping material.
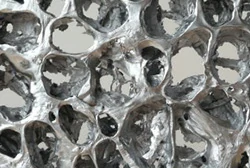
Large Cell
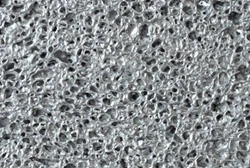
Mid Cell
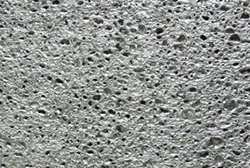
Small Cell
Extra wide aluminum coil for ship
Chalco offers extra-wide aluminum plates with widths ranging from 800 mm to 2000 mm, with a maximum width of up to 2650 mm.
Contact us now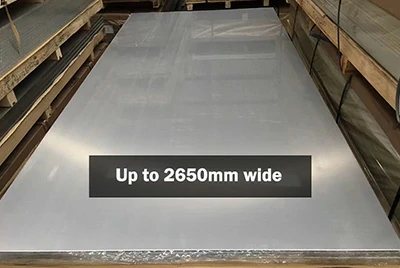
Marine transition joints
Marine transition joints consist of three metals: a steel base, a corrosion-resistant aluminum alloy top layer, and a pure aluminum intermediate layer to enhance bonding.
These transition joints are uniformly bonded through vacuum explosion welding and are commonly used in shipbuilding to weld aluminum superstructures to steel hulls.
Contact us now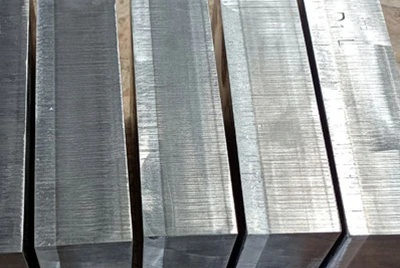
Chalco manufactures aluminum-steel transition joints using parent plates with standard dimensions of 1300 × 3800 mm, with a maximum size of up to 4 × 12 meters and thicknesses ranging from 1 mm to 100 mm.
After sawing or water jet cutting, various shapes and sizes can be obtained, including plates, blocks, discs, rectangles, and rings.
For stock size sheets, please contact us!Quick Quote
Marine aluminum tubing
We have a large stock of anodized marine-grade aluminum tubes with polished and brushed surface finishes. Made from durable 5052, 5083, 5754, 6060, 6082, and 6463 alloys, they enhance the performance of your marine projects.
These tubes are ideal for constructing T-tops, tuna towers, Bimini tops, outrigger platforms, leaning posts, and bow railings, ensuring durability and corrosion resistance in marine environments.
For custom solutions, including tailored sizes, lengths, alloys, or finishes, please contact us.
-
5083 marine tube O H112
Applications: Manufacture of hulls, decks, marine tanks, offshore platforms and diving equipment.
High strength excellent ductility corrosion resistance -
5086 marine tube H32 H111
Applications: Desalination plants and ship structures
High strength good corrosion resistanceExcellent weldability -
6061 marine tube T5 T6
Applications: Hull frames, bulkheads, railings, doors and windows, etc.
preservative good weldability processing performance -
5052 marine tube O H112
Applications: Ventilation pipes, drainage pipes, lifeboats, anchor chains, etc.
preservative good weldability price is relatively cheap -
3003 marine tube O H14
Applications: Ship's piping system, cooling equipment, deck structure.
Corrosion resistant lightweight easy to process -
6063 marine tube T5 T6
Applications: Ship's piping system, structural parts, deck handrails.
Corrosion resistant lightweight -
6082 marine tube T5 T6
Applications: Ship's piping system, structural parts, deck handrails.
Corrosion resistant lightweight -
2024 marine tube T3 T351 T4
Applications: Structural components of ships, hull frames, bulkheads, etc.
High strength good corrosion resistance
Marine aluminium extrusion
Aluminum extrusions are a popular choice for marine projects due to their lightweight, high strength, and excellent corrosion resistance. Extruded aluminum can be provided with DNV certification.
Suitable aluminum alloys for marine extrusions include 5083, 5086, 6082, and 6061.
Chalco offers a wide range of aluminum extrusions for marine applications, from commercial ferries, ships, and small boats to large barges and floating docks.
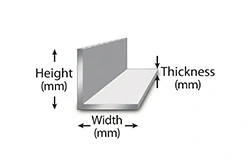
Angle aluminum
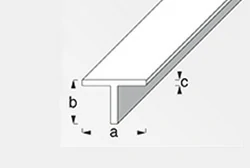
T-profile
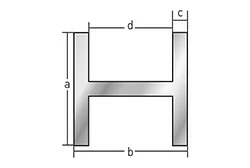
H-profile
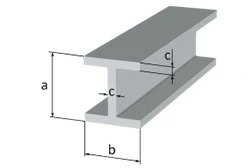
I-beam

U-channel
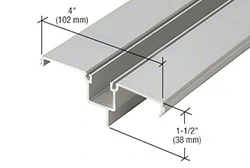
Glass extrusions
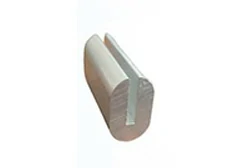
Boat windscreen aluminium extrusions
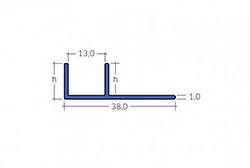
F-profile
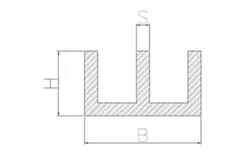
Aluminum double-duct profile
We offer customized marine aluminum profiles, precisely designed to meet your project requirements in terms of dimensions, cross-sectional shapes, and alloy types. Feel free to contact us for a tailored solution! Quick Quote
Custom marine aluminum alloy components series
Custom Aluminum Plates and Profiles Integration
Manufactured using skin pressing/bending and modular integration technology.
Contact us now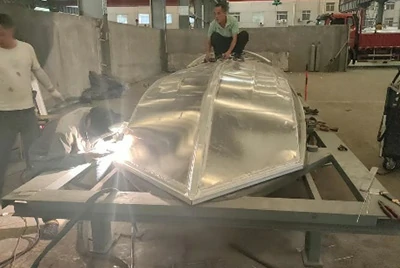
Custom Marine Fuel Tanks, Water Tanks, and Consoles
Made from 5083-111 aluminum, combining laser cutting and bending-formed components.
Contact us now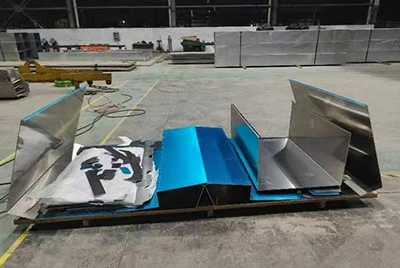
Custom Marine Ladders
Constructed with aluminum plates and tread plates, using laser-cut perforation, bending-formed components, and plug-in welding technology.
Contact us now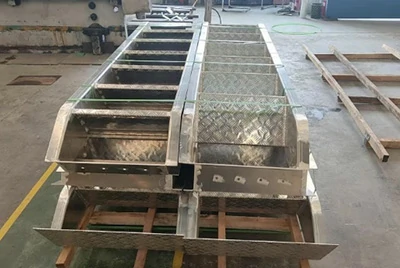
Custom Marine Gooseneck Vents and Bollards
Made from aluminum plates and 6-series alloy tubes, combining laser-cut profiles, sheet cutting, and bending-formed components.
Contact us now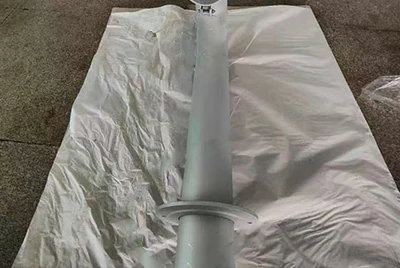
Custom Marine Watertight Hatches, Manhole Covers, Weatherproof Doors
Manufactured with aluminum plates and 6-series alloy profiles, using laser-cut profiles, sheet cutting, and bending-formed component integration technology.
Contact us now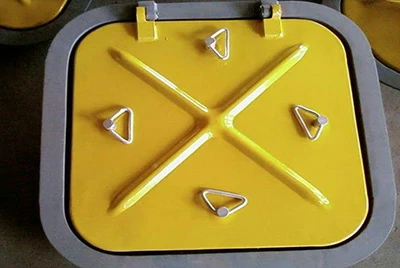
Aluminum hull vessel fittings
Our aluminum hull marine fittings can be directly welded to aluminum hulls, ensuring high-strength bonding, corrosion resistance, and long-lasting durability, making them suitable for various marine applications.
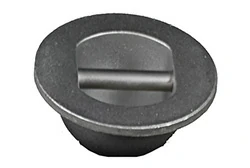
Aluminum Tie Down Points
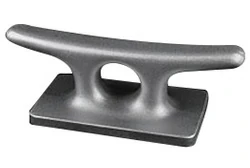
Aluminum Marine Cleats
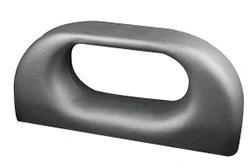
Aluminum Marine Deck Chocks
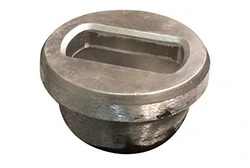
Aluminum Container Foundation
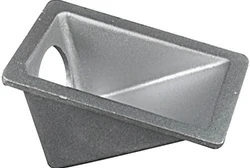
Aluminum Deck Scupper
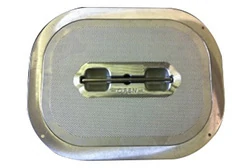
Aluminum Boat Hatches
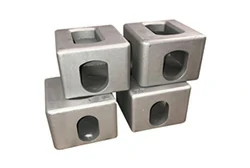
Aluminum Container Corner Castings
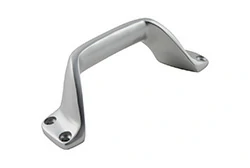
Aluminium Handle
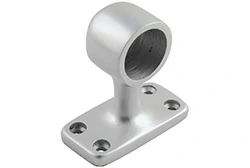
Aluminium Handrail Brackets
Marine aluminum anodes
Provide the most effective protection in saltwater and brackish water.
- Significant cost savings compared to traditional zinc anodes.
- Compliant with U.S. MiL standard (MiL-A-24779(SH)).
- Performs at least 5% better in saltwater than traditional zinc anodes, with 50% longer protection time.
- 0% cadmium content, eliminating toxic substances found in traditional zinc anodes, making it environmentally friendly.
- 50% lighter than traditional zinc anodes.
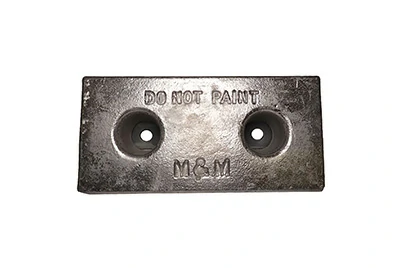
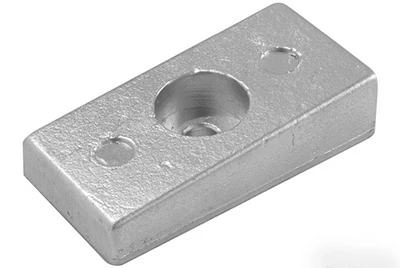
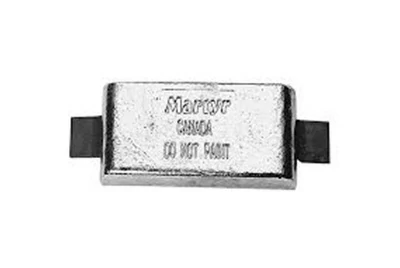
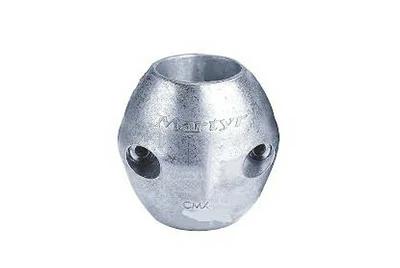
Marine aluminium pipe fittings
- Lightweight: 50% lighter than traditional steel pipe fittings, reducing vessel weight and improving fuel efficiency.
- Corrosion-resistant: Made from premium marine-grade aluminum alloys such as 5083, 6061, and 6063, offering excellent seawater corrosion resistance.
- High strength & easy welding: Suitable for marine piping welding processes, ensuring long-term stability.
- Wide applications: Ideal for seawater pipelines, fuel pipelines, drainage systems, and air ventilation systems.
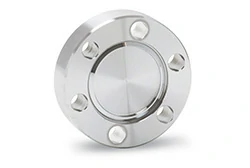
Aluminium Flanges
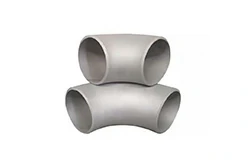
Aluminium Elbows
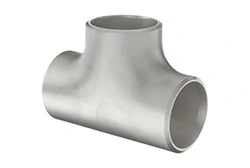
Aluminium Tees
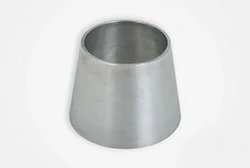
Aluminium Reducers
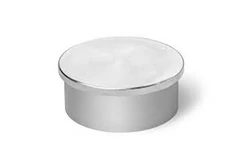
Aluminium End Caps
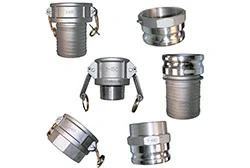
Aluminium Couplings
Marine aluminium bars
Marine-grade aluminum round bars are commonly made from 5-series (5083, 5086) and 6-series (6061, 6063) alloys. Different tempers such as O, H32, and H116 are selected based on application requirements to balance strength and corrosion resistance.
Marine grade aluminum round bar
Commonly used alloys for marine-grade aluminum round bars include 5-series (e.g., 5083, 5086) and 6-series (e.g., 6061, 6063) aluminum alloys.
The temper of marine-grade aluminum round bars is typically chosen from O (annealed), H32, H116, etc., to meet specific application requirements. H32 and H116 conditions indicate stabilization treatment, providing a balance of strength and corrosion resistance.
-
5052 marine round bar O H112
Applications: deck support and ship frame, ship mast, rigging, etc.
Lightweight Weldability -
5059 5086 marine round bar O H112
Applications: ship rudder posts, guardrails, handrails, and ship door and window frames, etc.
High strength Corrosion resistance -
Applications: Structural support components, protective equipment, sail support rods, etc.
Lightweight Good weldability -
5083 5383 marine round bar O H112
Applications: Manufacturing of hull skeleton, oars, ship equipment, and ship accessories.
High strength Processability -
6060 6061 6005 6082 marine round bars T4 T3511 T5 T6 T8511
Applications: hull skeleton, keel, ladder, railing, handrail, etc.
Easy to cut and drill -
Applications: hull skeleton, ship railing, ship ladder, deck guardrail, and electrical system.
Low density Conductivity -
5A02 marine round bar O H112
Applications: gangway, guardrail, railing; manufacture various ship accessories.
Processing performance Thermal conductivity
Marine grade aluminum flat bar
Lightweight, sharp edges, smooth surface, versatile material with good corrosion resistance.
Contact us now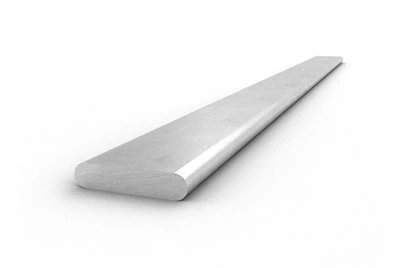
Marine grade aluminum square bar
Marine-grade aluminum square bars are extensively utilized in marine engineering and shipbuilding, employed in the fabrication of ship hull structures, masts, deck structures, marine platforms, and various components for marine engineering projects, including offshore platforms, marine pipelines, and seabed facilities, among others.
-
5052 marine square bar O H112
Applications: deck support and ship frame, ship mast, engine, pipeline support, etc.
Easy to process Weldability -
5059 5086 marine square bar O H112
Applications: ship rudder posts, guardrails, handrails, and ship door and window frames
High strength and rigid -
5083 5383 marine square bar O H112
Applications: manufacturing of hull skeleton, oars, ship equipment, and ship accessories.
High strength Processability -
Applications: structural support components, protective equipment, ship accessories, etc.
Lightweight Good weldability -
6060 marine square bars T4, T3511, T5, T6, T8511
Applications: hull skeleton, keel, ladder, railing, handrail, etc.
Easy to cut Good decorative performance -
Applications: the ladders and handrails inside the ship, between decks.
Easy to process Strong and sturdy -
6082 marine square bar O, T4, T3511, T6, T8511
Applications: structural support materials used for manufacturing ship hulls, etc.
Corrosion resistance Can be heat treated -
6061 marine square bar T4, T3511, T6, T8511
Applications: making equipment brackets on ships, such as support structures for navigation and equipment, etc.
High strength Corrosion resistance -
Applications: hull skeleton, ship railing, ship ladder, deck guardrail, and electrical system.
Low density Conductivity -
5A02 marine square bar O H112
Applications: gangway, guardrail, railing; manufacture various ship accessories, etc.
Processing performanceThermal conductivity
Marine grade aluminum hexagon bar
Marine-grade aluminum hexagonal bars find diverse applications in marine engineering and shipbuilding, serving as essential components for ship hull structures, masts, support structures, offshore platforms, marine engineering components, connectors, fasteners, and ship accessories. Overall, they play a crucial role by providing strength, lightweight properties, and corrosion resistance in marine projects and ship manufacturing.
-
5052 marine hexagon bar O H112
Applications: Ship equipment and components, such as steering wheels, ship propellers, propeller shafts, etc.
Good surface treatment Seismic performance -
5059 5086 marine hexagon bar O H112
Applications: Ship rudder posts, guardrails, handrails, and ship door and window frames
High strength Rigid corrosion resistance -
5083 5383 marine hexagon bar O H112
Applications: Manufacturing of hull skeleton, oars, ship equipment, and ship accessories.
High strength Corrosion resistance -
Applications: Structural support components, protective equipment, sail support rods, etc.
High-strength Good weldability -
6060 6005 6082 6061 marine hexagon bars T4, T3511, T5, T6, T8511
Applications: Hull skeleton, keel, ladder, railing, handrail, etc.
Excellent extrusion performance -
Applications: Used for hull structure, ship equipment support, ship decoration, and interior design.
Lightweight High-strength Easy to process -
5A02 marine hexagon bar O H112
Applications: Ship equipment and accessories, ship pipeline supports, welding components.
Thermal conductivity
Cast and forged marine-grade aluminum alloys
Marine-grade forged aluminum alloys are commonly used in docks, boat lifts, structural shipbuilding, and other offshore structures.
Contact us now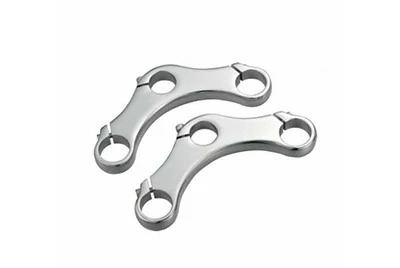
Marine Aluminum Welding Wire
Marine-grade aluminum MIG welding wire is specifically designed for welding aluminum alloys used in marine environments. It is available in various diameters, ranging from 0.025 inches to 0.045 inches.
5356 and 5183 alloy wires are commonly used for marine applications due to their excellent corrosion resistance, strength, and durability, even under harsh conditions such as saltwater exposure.
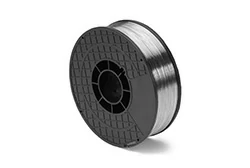
5356-grade wire
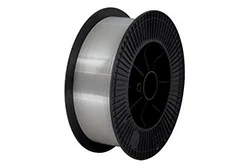
5183-grade wire
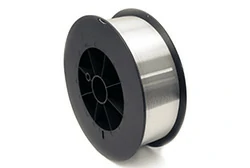
4043-grade MIG wire
Marine Stainless Steel Products – Also Available
If you are interested in our marine-grade stainless steel products or have any technical inquiries or requirements, please feel free to contact our professional team.
- Super Duplex Stainless Steel:UNS S32750(SAF 2507), UNS S32760(Zeron 100)
- HSLA Steel:A131 Grade AH36/DH36/EH36, EN 10225 S355G10+M
- Nickel-based Alloys:Inconel 625(UNS N06625), Monel 400(UNS N04400)
- Specialty Stainless Steel Fasteners:A286(UNS S66286), .17-4PH(UNS S17400)
- High-performance Marine Steel Plates:NV F690(NORSOK), API 2W Grade 60/Grade 80
DNV-Certified Aluminum Extrusion Stock List
All materials are fully certified. Additionally, Chalco can provide Lloyd’s Register (LR) certification as well as materials certified by DNV, ABS, and GL, upon request.
We offer comprehensive cutting services for all products, including length cutting for bars, tubes, and extrusions, as well as straight and profile cutting for plates.
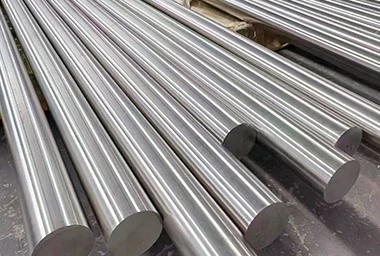
5052 Aluminum Bar Stock
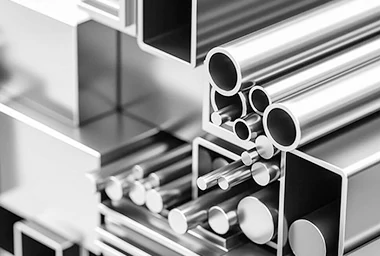
6061 Aluminum Tube Stock
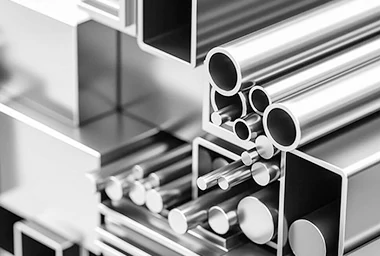
6063 Aluminum Tube Stock
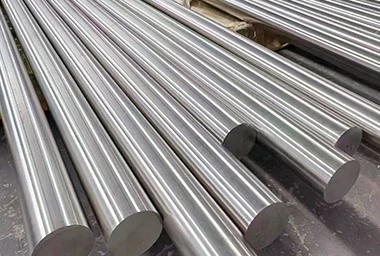
6063 Aluminum Bar Stock
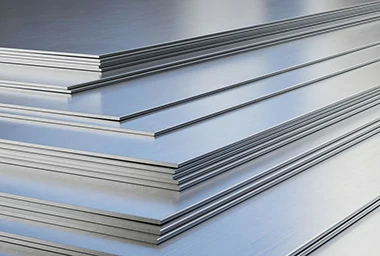
6063 Aluminum Flat Bar Stock
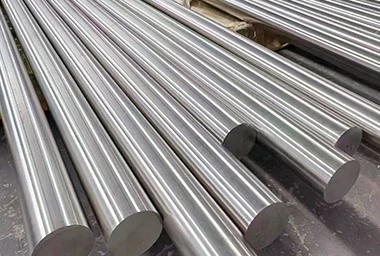
6082 Aluminum Bar Stock
Marine aluminum properties
- The density of marine-grade aluminum alloys is approximately 2.7 g/cm³, only one-third the weight of steel.
- Aluminum alloys offer excellent corrosion resistance in marine environments, especially 5083 and 5086 alloys.
- Marine-grade aluminum alloys provide high strength and hardness. For example, 6061-T6 aluminum alloy has a Brinell hardness of approximately 95, a tensile strength of 310 MPa, and a yield strength of 276 MPa.
- Aluminum alloys have good oxidation resistance, and surface treatments such as anodizing enhance protection against UV exposure and marine environments.
- Aluminum alloys are easy to process, allowing for polishing and anodizing to achieve a high-quality surface finish, improving aesthetic appeal and durability.
- Marine-grade aluminum alloys have excellent weldability and manufacturability, making them suitable for various welding and forming processes, meeting the needs of complex structures.
Advantages of marine aluminum
- Lightweight: 50-65% lighter than steel, reducing vessel weight, improving fuel efficiency, and increasing payload capacity.
- Excellent corrosion resistance: Protective oxide layer effectively resists saltwater corrosion.
- High strength: Superior strength-to-weight ratio.
- Low maintenance: Long-term durability with minimal maintenance, reducing costs and labor expenses.
- Easy to process: Easily cold-formed and bent, making it ideal for complex structural manufacturing.
- Fire-resistant: Aluminum is non-combustible in marine environments and offers better fire resistance than carbon fiber, meeting ABS, DNV, and Lloyd’s international certification standards.
Marine Aluminum Applications
Shipbuilding structural applications
- Hull structures: 50-65% weight reduction compared to steel, improving fuel efficiency.
- Superstructures: Used for decks, cabins, and helicopter decks, reducing ship center of gravity and enhancing stability.
- Fishing boats & patrol boats: Saltwater corrosion resistance, reducing maintenance costs and extending service life.
Marine hardware & accessories
- Handrails & walkways: Made from NORSOK standard aluminum extrusions, strong, durable, and corrosion-resistant in marine environments.
- Ladders & stair towers: Lightweight yet strong, customizable to various requirements, and pre-fabricated for easy installation, reducing on-site workload.
- Mooring bollards, railings, hatch frames: Long-lasting with minimal maintenance or replacement needs.
Marine propulsion & equipment systems
- Propellers: Some high-performance vessels use aluminum propulsion components, reducing overall weight.
- Pipelines & cable trays: Corrosion-resistant aluminum pipes & wire ducts, enhancing marine equipment safety.
- Marine trailers & storage facilities: Made of aluminum alloy, rust-free, and longer service life.
Aluminum modules
- Office & living space extensions: A60 fire-resistant glass curtain walls, high-strength lightweight structures, ideal for offshore platforms.
- Helicopter decks: Meets international certification standards such as ABS, DNV, and Lloyd's, ensuring high reliability and strength.
- Elevator shafts: Aluminum elevator shafts are 50% lighter than steel, lower maintenance costs, and easy to install.


High-Precision marine aluminum alloy processing & prefabrication services
We offer a range of cutting and prefabrication services, including coil slitting, sheet cutting to size, extrusion and tube length cutting, polishing, coating, drilling, grooving, bending, and edge welding preparation.
We can also process all forms into finished products with ease using various techniques.Quick Quote
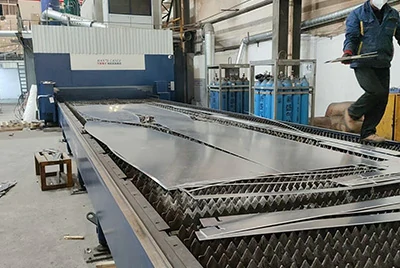
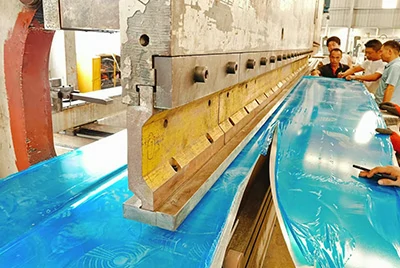
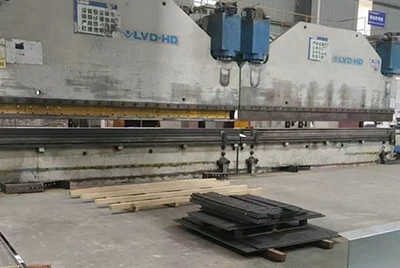
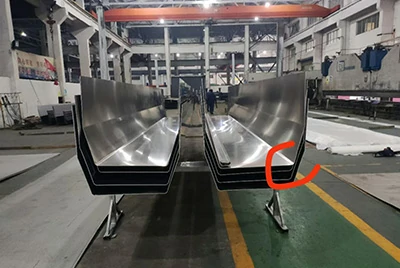
Corrosion-resistant treatment of aluminum alloy for ships
Here are some tips to ensure the durability of aluminum structures in marine and offshore environments, in addition to selecting the right aluminum alloy:
Anodizing
Anodizing enhances the natural oxide layer on aluminum, protecting marine aluminum extrusions from corrosion and other external damage.
Contact us now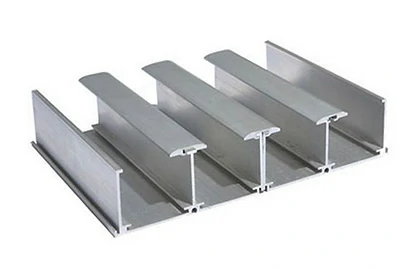
There are different types of anodizing, including sulfuric acid anodizing, hard anodizing, and chromic acid anodizing. The anodized film thickness typically ranges from 5 to 25 microns, depending on the corrosion level of the final application.
Compared to chemically produced coatings, anodizing provides better corrosion resistance and strength. The anodized layer can also serve as a base for any color dye.
Aluminum coatings
Organic coatings such as paint, varnish, and powder coatings create a physical barrier against corrosive elements.
Common types of aluminum coatings include polyurethane coatings, epoxy coatings, and powder coatings.
Contact us now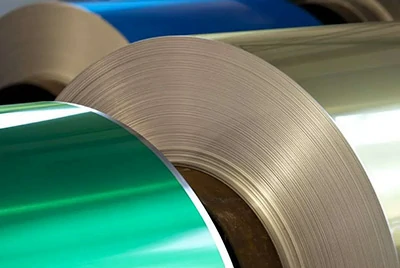
- Below the waterline: coatings must resist penetration corrosion and biofouling. polyurethane topcoats, epoxy primers, and specialized antifouling paints are commonly used.
- Above the waterline: coatings need good weather resistance, gloss retention, and compatibility with primers. common choices include polyurethane topcoats, alkyd resin paints, acrylic paints, and advanced fluorocarbon coatings.
Sacrificial anodes
Cathodic protection involves using sacrificial anodes (such as zinc or magnesium) to corrode instead of aluminum. Impressed current systems use an external power source for protection.
In submerged areas of ships, using about 10% of the sacrificial anodes (zinc, magnesium) required for carbon steel can effectively protect aluminum.
Contact us now
Electrochemical insulation
When different metals are used together, electrochemical corrosion can be prevented by electrically insulating them from each other. Insulation must completely eliminate metal-to-metal contact.
Another insulation alternative is using sealing wax or covers on bolt heads, nuts, and washers.
Chromate conversion coating
Chromate conversion coatings form a protective chromium layer on the aluminum surface, providing good corrosion resistance and serving as a base for additional coatings.
Electroplating
Electroplating involves depositing a metal layer, such as nickel or chromium, onto the aluminum surface to enhance corrosion resistance.
Inhibitors
Inhibitors are chemicals added to the environment to slow down the corrosion process. these can be organic or inorganic inhibitors.
others
Surface treatments such as laser surface melting, ion implantation, and shot peening can modify the aluminum surface to improve corrosion resistance.
Marine aluminium best welding techniques
TIG (tungsten inert gas) welding: suitable for thinner aluminum sections, providing precise control and high-quality welds.
MIG (metal inert gas) welding: ideal for thicker sections, offering faster welding speeds and good penetration.
FSW (friction stir welding): a solid-state joining process that creates high-strength welds without melting the base material, especially suitable for marine aluminum with high damping and resistance properties.
Challenges of welding marine-grade aluminum
- Oxidation: aluminum quickly forms an oxide layer when exposed to air, affecting welding. cleaning the surface before welding is crucial.
- Thermal conductivity: aluminum has excellent heat conductivity, making it difficult to maintain the necessary heat in the welding area. preheating the material may help.
- Deformation: due to aluminum's high thermal expansion coefficient, it may bend or deform during welding. using proper clamping and fixturing can minimize this issue.
- Crack sensitivity: some aluminum alloys, especially heat-treatable ones, are more prone to cracking in the weld zone. proper joint preparation, welding techniques, and post-weld heat treatment are essential to prevent cracking.
Why choose us? – professional marine aluminium supplier
- Years of experience in providing corrosion-resistant, high-strength marine aluminum alloys for ships, offshore structures, and more.
- From raw material selection to production inspection, our products meet international classification standards such as DNV and ABS, ensuring higher reliability.
- Advanced digital equipment and mature heat treatment and rolling processes guarantee product consistency and high performance.
- Customized grades and specifications available upon request, with fast delivery to shorten project timelines.
- Expert consultation on material selection and application to simplify the entire project process for customers.
- Seamless service from quotation, production, and logistics to after-sales support, saving time and effort for our clients.