Structural transition joint (STJ) are manufactured using vacuum explosive welding, specifically designed for shipbuilding to provide a strong and reliable aluminum-steel connection.
These transition joints effectively reduce the overall weight of vessels, help control production costs, and ensure greater structural stability and economic efficiency.
Specification of structural transition joint
- Lloyd's 3.2 certification
- MIL-J-24445A certification
- CB 1343 standard for aluminum-steel composite transition joints
- CB 20091 standard for aluminum-aluminum-steel (stainless steel) composite transition joints
- YST 850-2012
Popular structural transition joint products
Chalco manufactures structural transition joint using standard mother plates of 1300 x 3800 mm, with a maximum size of 4 x 12 meters and thickness ranging from 1mm to 100mm.
After saw cutting or water jet cutting, these joints can be customized into various shapes and sizes, including plates, blocks, discs, rectangles, and rings.
We offer customized transition joints with various metal interlayers, shapes, and sizes based on customer requirements. With short lead times, we ensure that clients can meet their project demands on time.Quick Quote
The transition joint consists of three layers: steel, pure aluminum, and seawater-resistant aluminum.
Steel | Interlayer | Aluminum alloy | Thickness (mm) |
Shipbuilding steel Grade D | 1050 | 5083 | 28(15+3+10) |
Shipbuilding steel Grade D | 1050 | 5083 | 33(20+3+10) |
AMarine plate Grade A | 1050 | 5083 | 28-34 |
A516-55 | 1050 | 5086 | 34.5(19+9.5+6) |
A516-55 | 1050 | 5083 | 19(10+5+4) |
A516-55 | Grade 1 titanium | 3003 | 31.5(19+1.5+10) |
A516-55 | 1100 | 5086 | 19.05(9.525+6.35+3.175) |
A516-56 | 1100 | 5456 | 34.925(19.05+9.525+6.35) |
Stainless steel 316L | Grade 1 titanium | 3003 | 31.5(20+1.5+10) |
Stainless steel 316L | 1100 aluminum Grade 1 titanium N02200 nickel | 5086 | 24(9.5 +6.5+2+3+3) |
Stainless steel 316L | 1100 aluminum Grade 1 titanium N02200 nickel | 5456 | 31(19+9.5+2+3+6.5) |
We also offer other structural transition joint products:
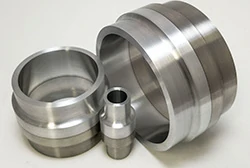
Aluminum-steel pipeline transition joint
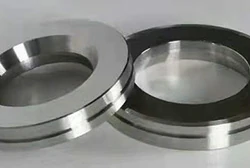
Low-temperature transition joint
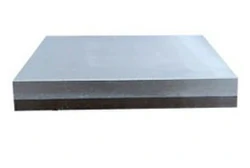
Aluminum-steel electrical transition joint (ETJ)
Mechanical properties of structural transition joint
Our structural transition joint offer exceptional mechanical properties, ensuring strong and reliable connections!
Shear strength - Basemetal/Intelayer | >55N/mm² |
Tensile strength (through thickness) | 75N/mm² |
Processing temperature | Max 315℃×30min |
Bend test base material in compression | Acceptable |
Bend test base material in tension | Acceptable |
Side Bend Test | Acceptable |
Advantages of structural transition joint
- No maintenance required after installation, reducing long-term repair, refurbishment, and replacement costs.
- Ensures a continuous joint with even stress distribution at the connection.
- Offers excellent waterproof performance, minimizing the risk of corrosion.
- Supports lightweight ship design, improving overall efficiency.
- Manufactured using vacuum explosive welding, preserving the original metallic properties and ensuring high joint strength.
- Cost-effective by layering thin, expensive materials over thicker, more affordable ones.
- Achieves the desired cladding thickness in one step, with a smooth surface, reducing post-processing requirements.
Compared to traditional bolted and riveted connections, structural transition joint provide superior strength, corrosion resistance, easier installation, and lower maintenance needs.
Applications of structural transition joint
For cost and durability reasons, aluminum is typically not used for the entire ship structure. The main hull structure is usually made of steel.
- Connecting aluminum superstructures to steel decks.
- Joining aluminum decks and bulkheads to steel hulls.
- Installing windbreak decks on steel ships.
- Creating permanent joints between steel (or stainless steel) and aluminum for components like pillars and partitions.
- Upgrading containerized electronic equipment to steel decks.
- Attaching steel components to aluminum hulls.
- Providing wear-resistant keels for aluminum vessels.
- Installing helicopter decks on ships or offshore drilling platforms.
- Mounting aluminum walkways or accommodation modules on offshore drilling platforms.


Testing and quality control
To ensure the superior performance and long-term reliability of structural transition joint, we implement strict testing procedures, covering every stage of production from raw materials to finished products.Quick Quote
- 100% Ultrasonic Testing (UT): Ensures each product is free from internal defects and meets thickness requirements.
- Penetrant Testing (PT): Uses dye penetration to effectively detect micro-cracks and surface flaws.
- Dimensional Inspection: Every structural transition joint undergoes precise measurement checks.
- Raw Material Testing: Ensures materials meet specific specifications, guaranteeing quality from the source.
- Torsional Fatigue Test: Evaluates the joint’s durability under long-term torsional stress.
- Tensile/Compression Fatigue Test: Simulates real-world tensile and compression forces to assess fatigue life.
- Shear Stress Test: Verifies the joint’s ability to withstand various stress conditions.
- Flatness Test: Ensures precise installation and interchangeability.
Atmospheric explosive welding vs. vacuum explosive welding
The secret behind Chalco's superior joint strength and corrosion resistance lies in its vacuum explosive welding technology.
Atmospheric Welding | Vacuum Welding |
Coarse oxide clusters and voids at the steel-aluminum interface | 100% dense and homogeneous joints |
Oxide clusters and voids can lead to fractures | No oxide clusters or voids |
Oxide clusters and voids can cause corrosion | No risk of fractures or corrosion |
Bending may be difficult | High ductility and excellent formability |
Production is weather-dependent | Unaffected by weather conditions |
Saw cutting and forming are challenging | Easy to saw cut |
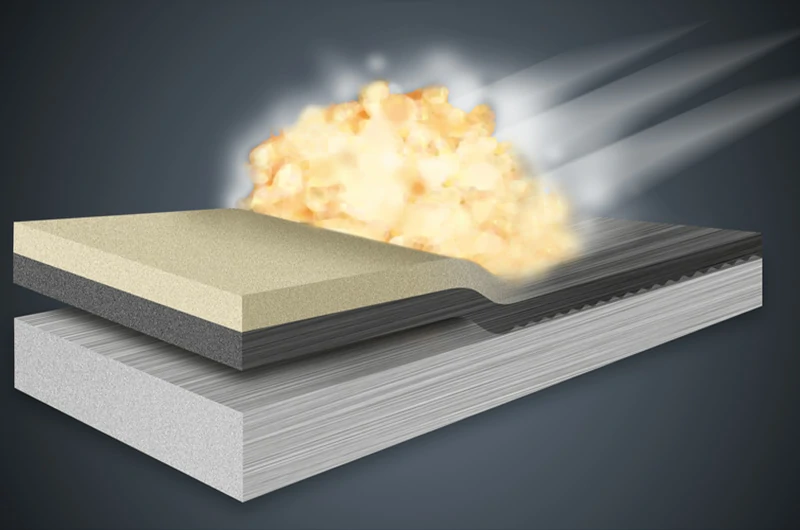
Why choose us?
With cutting-edge equipment, superior craftsmanship, and a comprehensive customer service system, we consistently provide high-quality and reliable structural transition joint solutions.
- Customized solutions: We offer not only standard products but also highly tailored solutions to meet your specific needs, including special sizes, shapes, and material combinations.
- Advanced manufacturing capabilities: Our state-of-the-art rolling, welding, and testing equipment ensures the efficient and precise production of structural transition joint that meet international standards.
- Strict quality management: Our production process strictly follows the ISO 9001 quality management system, guaranteeing stable and reliable product quality.
- Short lead times: We maintain a sufficient inventory of raw materials to ensure the shortest possible delivery times.
- Expert technical support: Our engineers and technical specialists have years of industry experience, providing professional guidance and customized solutions.
We have full confidence in our product quality! We make this commitment: As long as our aluminum-steel transition joints are manufactured and used according to our guidelines, delamination will never occur! Quick Quote
Welding recommendations for structural transition joint
- Do not preheat the transition joint before welding.
- During processing, material temperature must not exceed 315°C.
- Welding is not allowed within 3mm of the aluminum-steel composite interface.
- Before welding aluminum, remove the aluminum oxide layer using a wire brush.
- For better temperature control, weld the steel side first, then the aluminum side.
- Use 1.2mm welding wire for the aluminum side and 2.5mm welding rod for the steel side.
We recommend protecting the joint with paint, but avoid paints containing copper, mercury, or lead salts, as they may cause electrochemical corrosion.
Shipping and packaging
To ensure a secure and worry-free delivery, we meticulously optimize packaging design and shipping processes, guaranteeing that every order arrives intact and undamaged.
- Customized packaging solutions: We tailor exclusive packaging plans based on the size, shape, and specifications of each product.
- Multi-layer protective packaging: We use wooden crates, reinforced cartons, shockproof foam, and pearl cotton to create a durable protective structure, effectively resisting impact, vibration, and compression during transportation.
- Enhanced moisture and rust protection: We apply desiccants, anti-rust films, and multiple protective measures to effectively shield products from humidity and seawater corrosion.
- Secure internal fixation: Custom brackets and cushioning materials firmly secure products within the packaging, preventing shifting, collisions, and surface wear during transit.
- Flexible shipping options: We offer sea, air, and land transportation to accommodate different order requirements.
- Real-time shipment tracking: We provide comprehensive cargo tracking services, allowing you to monitor the shipping status at all times.
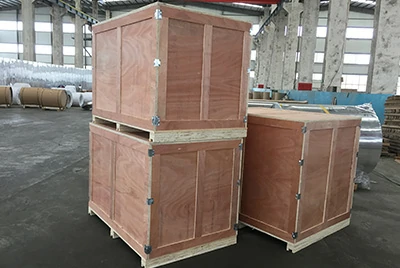

Other popular marine aluminum products
Frequently asked questions about structural transition joint
Why is it necessary to weld aluminum to steel in shipbuilding?
Composite metals and structural transition joints are mainly used in the shipbuilding industry. The hull is typically made of steel, while other parts are constructed with aluminum.
How do transition joints accommodate the different expansion coefficients of aluminum and steel?
With transition joints, force is evenly distributed rather than being applied at specific points like in mechanical joints. This ensures that all stresses remain within the shear load capacity.
I operate in extremely harsh conditions. Are there other transition joints suitable for my application?
Yes, we also manufacture joints with a titanium layer, which are particularly suitable for LNG storage tanks or environments where welding temperatures may be elevated.
What is the lifespan of an structural transition joint?
Under normal ship operating conditions, its lifespan fully matches the service life of the hull structure.
What are the cost advantages of structural transition joint?
The initial purchase cost may be slightly higher than traditional connection methods, but in the long run, it offers significant overall cost savings, providing a higher return on investment.