In CNC precision machining, mold base or fixture manufacturing, the selection of aluminum mold plate is crucial. Two common materials - 6061 aluminum plate and the well-known MIC-6 cast plate - are often compared. Although they have mature applications in the industry, understanding their differences in performance, structure and cost can help you make a choice that is more suitable for your project.
Materials overview: what are 6061 and MIC-6?
6061 aluminum alloy is a heat-treated and strengthened deformed aluminum alloy (T6/T651 state) with good strength, processability and weldability. It is widely used in structural parts, precision machining, and even as a high-quality casting mold plate material.
MIC-6® is a cast aluminum tooling plate produced by Arconic (formerly Alcoa), known for its excellent flatness and dimensional stability, and is a mainstream product in the traditional tooling market.
- View 6061 Aluminum Mold Plate product details page
- Visit the Chalco Aluminum Tooling Plates product overview page
Performance comparison: 6061 vs MIC-6
project | MIC-6 Cast Plate | 6061 Aluminum Plate (T6/T651) |
Material Type | Cast aluminum (proprietary formula) | Deformed aluminum (Al-Mg-Si system) |
Flatness | Very high (±0.005"/ft) | High (up to ±0.005"/ft, depending on condition and processing) |
Dimensional stability | Very high (good long-term stability) | Excellent stability in stress-free state |
Processability | Excellent, suitable for high-precision machining | Very good, suitable for CNC, tapping, drilling and other conventional processing |
tensile strength | Medium (~165 MPa) | Higher (T6/T651 can reach 240–310 MPa) |
Anodizing performance | Inconsistent, sometimes uneven color | Excellent, suitable for conventional and hard anodizing |
Weldability | Generally, not recommended | Very good for MIG/TIG welding |
Availability | Limited in size, dependent on imports | Rich in size, support customization and large-scale supply |
cost | High (obvious brand premium) | More cost-effective, especially suitable for large-volume projects |
MIC-6 adopts the casting process, so the plate has extremely high flatness and low internal stress when it leaves the factory, which is suitable for high-precision fixtures and inspection platforms. However, its strength is low and its surface treatment compatibility is poor, so it is not suitable for anodizing or high-load structure scenarios.
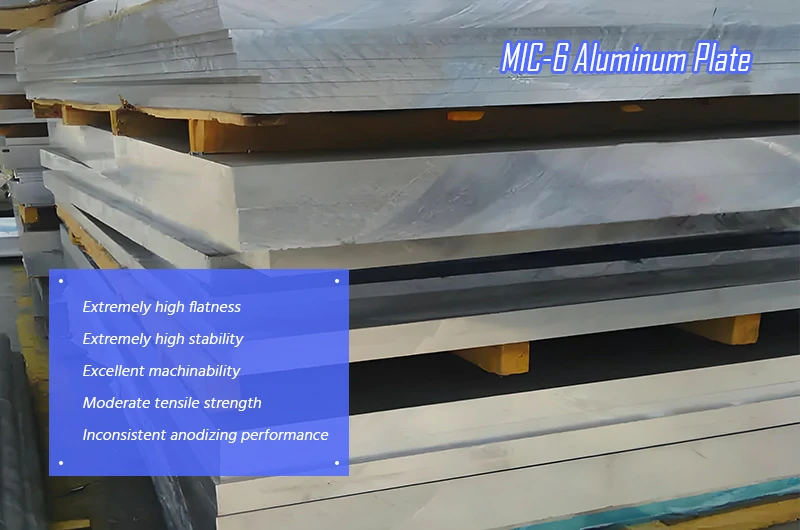
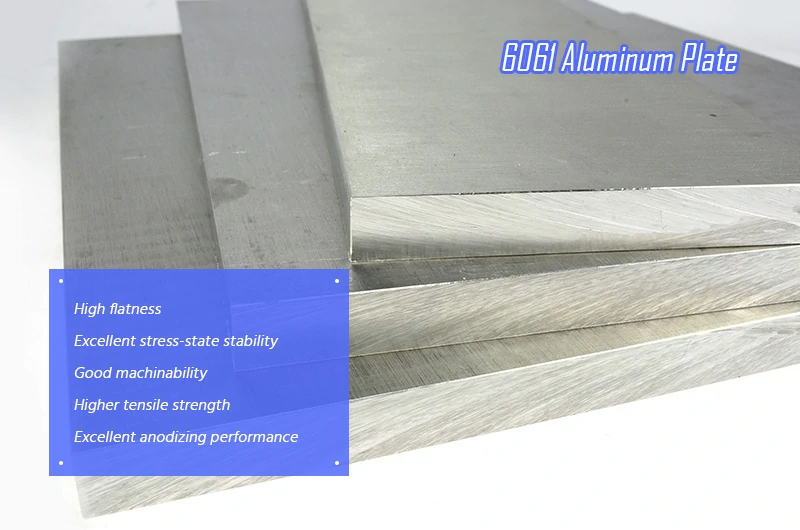
6061 aluminum plate, especially the version that has been cast, T6/T651 heat treated and stress relieved (such as the cast tooling plate provided by Chalco), has high strength, good processability and flatness. It also supports secondary processing such as anodizing, electrophoresis, welding, etc., and has outstanding cost-effectiveness.
Differences in manufacturing structure and process principles
MIC-6 is a cast aluminum plate that is formed by continuous casting and cooling. It has uniform grains and low internal stress, so it has excellent flatness and dimensional stability.
6061 is a hot-rolled or forged aluminum plate. After solution treatment and artificial aging (T6/T651), it has higher strength and durability. After stress release and flat processing, cast 6061 tooling plate can also achieve a flatness comparable to MIC-6, while having higher structural strength and corrosion resistance, and is suitable for more complex working conditions.
Recommended usage scenarios and industry applications
Industry application recommendation | ||
Application Type | Recommended board | reason |
CNC parts clamping platform | MIC-6 | No further processing required, ready for use, high dimensional stability |
Mould support base | 6061 | High strength, impact resistance, customizable size |
Large size vacuum fixture table | 6061 Cast | Can support customized oversized boards with better cost performance |
Injection mold base, mold opening motherboard | 6061 | Can be anodized and welded, long service life |
Check fixture, measuring base | MIC-6 | No deformation, suitable for high-precision static measurement |
Automatic lathe automation platform | 6061 | Good seismic performance and large processing window |
When to choose MIC-6?
- When your application requires extremely high flatness of the plate
- When anodizing or welding is not required
- When you want to machine directly without having to deal with stress


When to choose 6061?
- Need higher strength or load capacity (such as mold support, structural clamps)
- Project budget is sensitive and cost-effective Anodizing, electrophoresis or welding is required
- Customized board size required, more flexible delivery time


More FAQ
Q1: Can 6061 completely replace MIC-6?
A1: In most non-ultra-high precision fixture applications, especially where strength, anodizing, or weldability are required, 6061 (especially the Cast T651 version) is a good alternative to MIC-6.
Q2: Can the flatness of 6061 mold plate be the same as that of MIC-6?
A2: Chalco's 6061 cast mold plate uses double-sided precision milling and plane control, with a flatness of ±0.005"/ft, which is basically equivalent to MIC-6 in practical applications such as CNC machining and assembly fixtures.
Q3: Which material is more suitable for parts that require secondary anodizing?
A3: 6061 is recommended. Due to its special casting alloy system, MIC-6 has unstable surface treatment and poor color consistency.
Summary
If you are making a high-precision fixture or test platform and have extreme requirements for the initial flatness of the material, MIC-6 is undoubtedly still a mature choice.
But if you value strength, processing flexibility and cost-effectiveness more, then stress-relieved 6061 aluminum mold plate will bring you a more competitive solution.
Still wondering which board to choose?
Contact Chalco, we will provide technical support and alloy recommendations based on your application!
Chalco can provide you the most comprehensive inventory of aluminum products and can also supply you customized products. Precise quotation will be provided within 24 hours.
Get a quote