What is anodizing of aluminum?
The anodizing process of aluminum and aluminum alloy is a process that uses aluminum or aluminum alloy products as anodes, places them in electrolyte solution for electrification, and then uses electrolysis to form aluminum oxide film on their surfaces.
After anodizing treatment, aluminum surface can generate several microns to hundreds of microns of anodized film. Compared with the natural oxide film of aluminum alloy, its corrosion resistance, wear resistance and decorative properties have been significantly improved.Quick Quote
Why is anodizing of aluminum essential?
In order to overcome the defects in the surface hardness and wear resistance of aluminum alloys, expand the scope of application and prolong the service life, the surface treatment technology is indispensable in the use of aluminum alloys, and the anodic oxidation is the most widely used and successful technology.
Anodized metal aluminum films can change the surface state and properties, such as surface coloring, improving corrosion resistance, enhancing wear resistance and hardness, and protecting metal surfaces. Because of these special properties, it has been widely used in all aspects.
What is the principle of aluminum anodizing?
The principle of aluminum anodizing is essentially the principle of water electrolysis.
Aluminum and its alloys are placed in the corresponding electrolyte (such as sulfuric acid, chromic acid, oxalic acid, etc.) as anodes for electrolysis under specific conditions and under the action of impressed current. Aluminum or its alloy of the anode is anodized, and a thin layer of aluminum anodizing is formed on the surface, with a thickness of 5-30 microns, and a hard anodized film of 25-150 microns.Quick Quote
The anodized aluminum or its alloy has improved its hardness and wear resistance, which can reach 250~500 kg/mm2. It has good heat resistance, the melting point of the hard anodized film is up to 2320K. It has excellent insulation, and the breakdown resistance voltage is up to 2000V. It has enhanced the corrosion resistance, and will not be corroded after thousands of hours in the ω= 0.03 NaCl salt spray.
There are a lot of micropores in the thin anodizing film, which can absorb various lubricants, and is suitable for manufacturing engine cylinders or other wear-resistant parts. The membrane has strong microporous adsorption capacity and can be colored into various beautiful colors. Nonferrous metals or their alloys (such as aluminum, magnesium and their alloys) can be anodized. This method is widely used in mechanical parts, aircraft and automobile parts, precision instruments and radio equipment, daily necessities and architectural decoration.
The aluminum anodizing process is divided into three types.
Type I - Chromic Acid Anodizing
Using chromic acid as the electrolyte, it produces the thinnest coating, with a thickness of about 2.5 micrometers (0.0001 inches). Although the coating is thin, its corrosion resistance is comparable to other processes. The coating is typically darker and cannot be colored.
Type II - Sulfuric Acid Anodizing
Using dilute sulfuric acid as the electrolyte, it is the most commonly used process. The coating thickness ranges from 5.1 to 30.5 micrometers (0.0002-0.0012 inches). Typically following industry specifications such as MIL-A-8625 Type II, Class 1 (non-dyed) or Class 2 (dyed). This type of coating is harder than Type I and is easy to dye.
Type III - Hardcoat Anodizing
Using sulfuric acid as the electrolyte, it produces a thicker coating compared to Type II, typically ranging from 12.7 to 50.8 micrometers (0.0005 to 0.002 inches). This type of coating is harder than tool steel and is used in applications that require high levels of wear resistance.Quick Quote
Although it is not colored, the surface treatment will darken the part surface, with colors ranging from light gray to dark gray or brown.
What colors are available in anodized aluminum?
Anodized aluminum is available in various colors, including black, red, blue, green, gray, brown, and gold. Its porous nature allows it to absorb dyes effectively, and subsequent sealing helps prevent color loss during use.
While anodized aluminum can be dyed in nearly any color, precise color matching is often impractical. Expect some degree of color variation in anodized parts' color consistency.Quick Quote
If parts undergo sandblasting before anodizing, the resulting rougher surface will produce a matte finish.
What types of aluminum can be anodized?
Not all types of aluminum can be anodized effectively.
5XXX Series
Alloys in the 5XXX series (such as 5052) produce a strong and transparent oxide layer during anodizing. Common products in this series include those used in construction, welding, and lighting applications.Quick Quote
6XXX Series
Alloys in the 6XXX series are excellent candidates for anodizing. The oxide layer produced after anodizing is transparent and offers excellent protection.
Due to their outstanding mechanical properties and ease of anodization, alloys in the 6XXX series, including 6061 (bar), 6061 (tube), 6061 (sheet), 6063 (bar), and 6063 (tube), are commonly used in construction and structural applications.Quick Quote
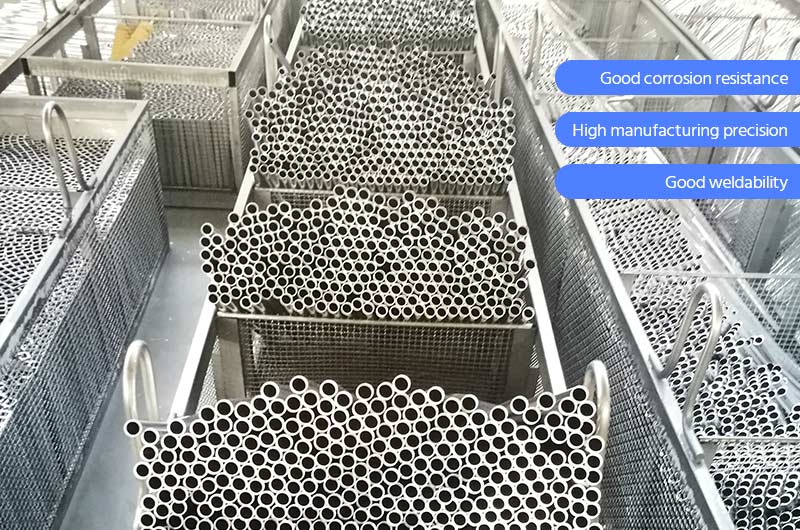
6061-aluminum-tube
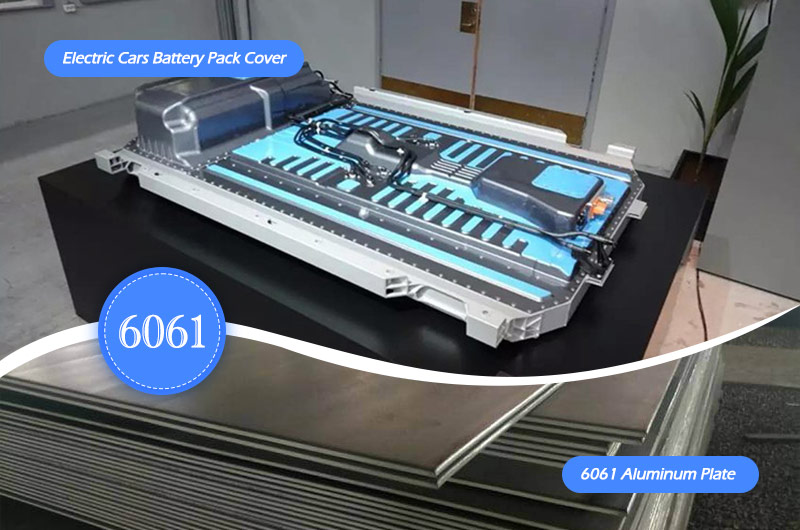
6061-aluminum-plate
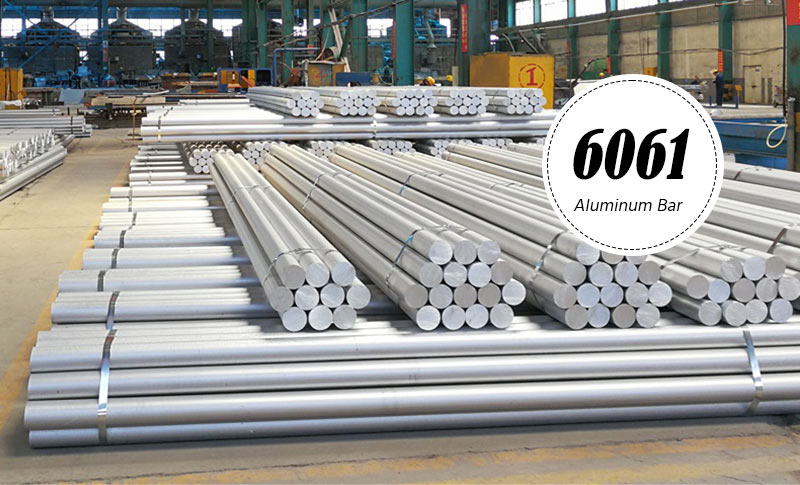
6061-aluminum-bar
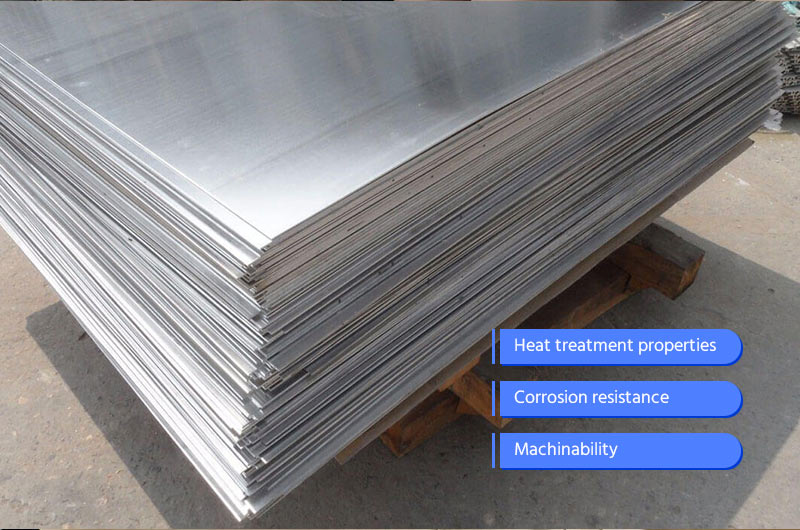
6063-aluminum-sheet
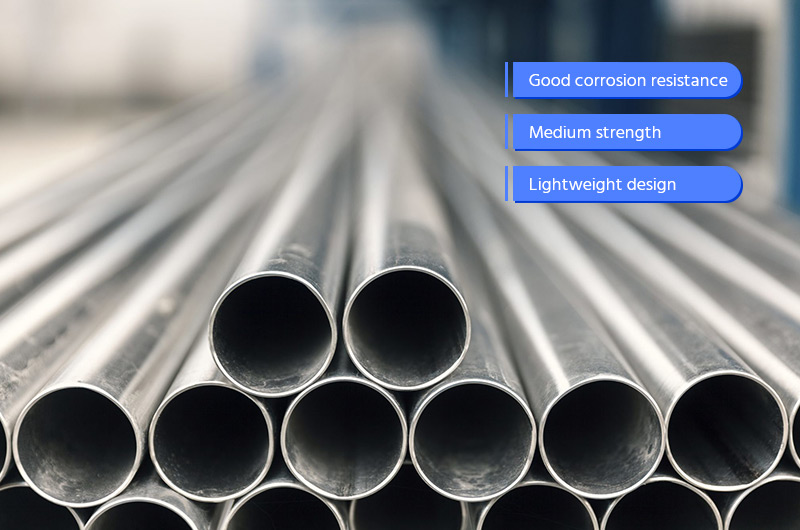
6063-aluminum-tube
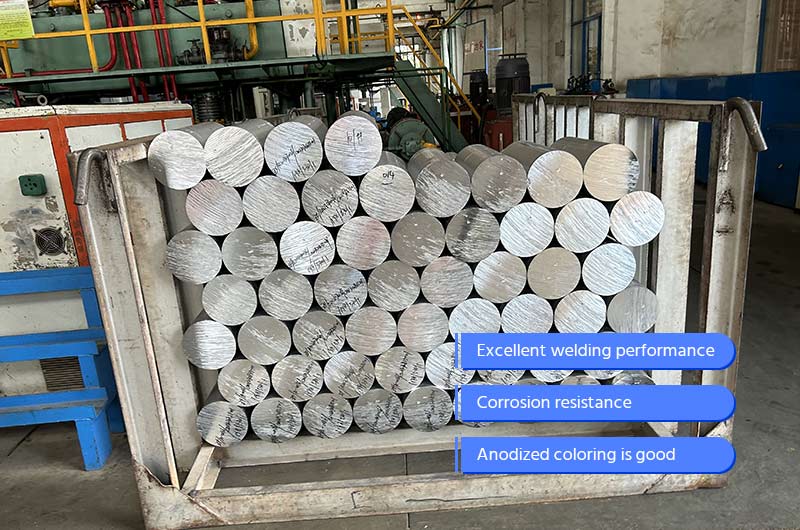
6063-aluminum-rod
7XXX Series
Aluminum alloys in the 7XXX series primarily contain zinc as the main alloying element. They are highly suitable for the anodizing process, producing a transparent oxide layer that provides excellent protection. They are commonly used in automotive applications.
IMPORTANT: Even within the recommended 5XXX and 6XXX series, not all alloys are suitable for anodizing. Some may not produce optimal results. It is best to consult with the manufacturer or metal finishing expert to determine which aluminum alloy is best suited for your specific anodizing needs.
Popular anodized products
Anodized aluminum is a truly versatile material that can be used to create a wide variety of products. Its durability, corrosion resistance, and attractive appearance make it a popular choice for many different applications.
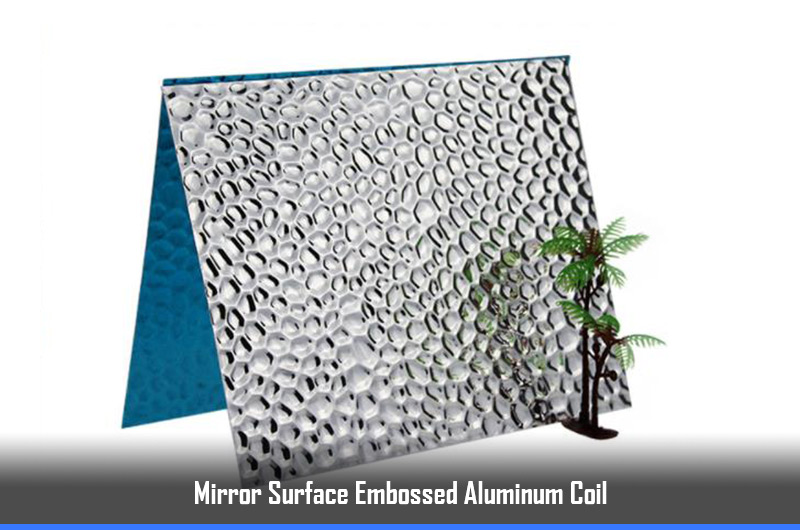
stucco-embossed-coil
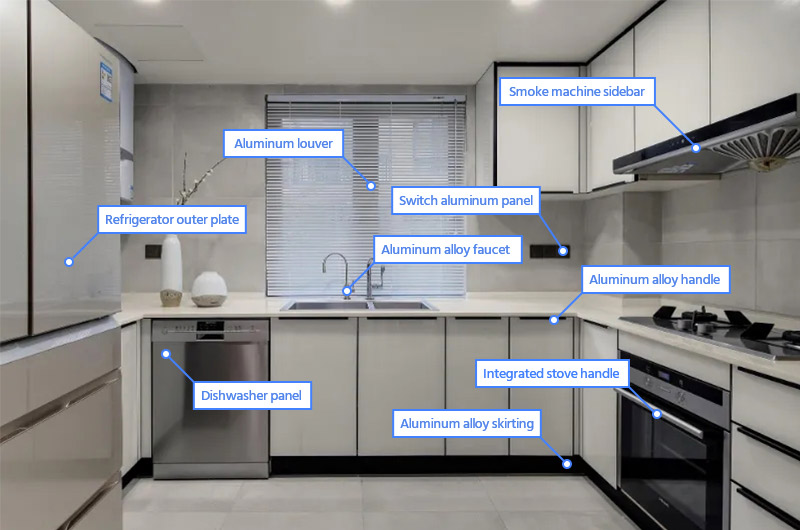
aluminum-in-kitchen
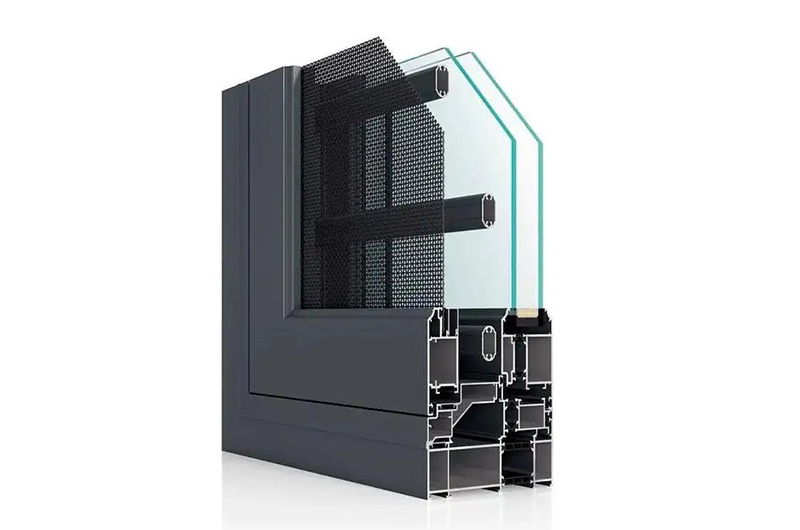
aluminum-profile-door-window
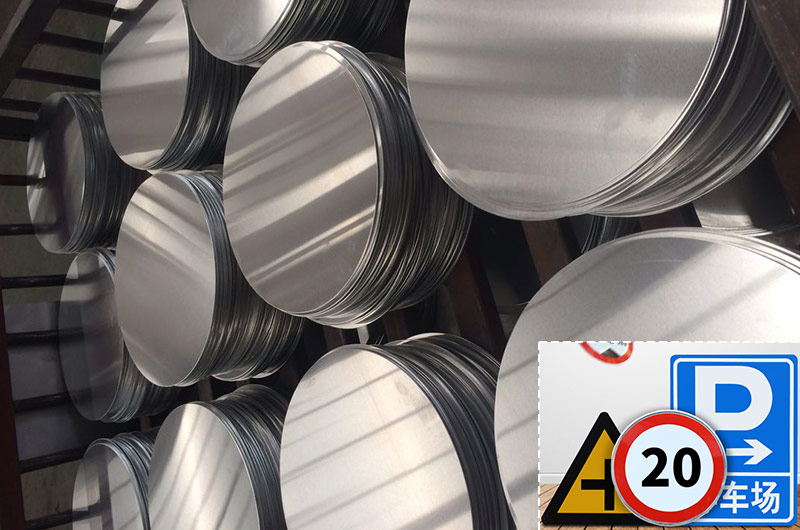
aluminum-sign-blank
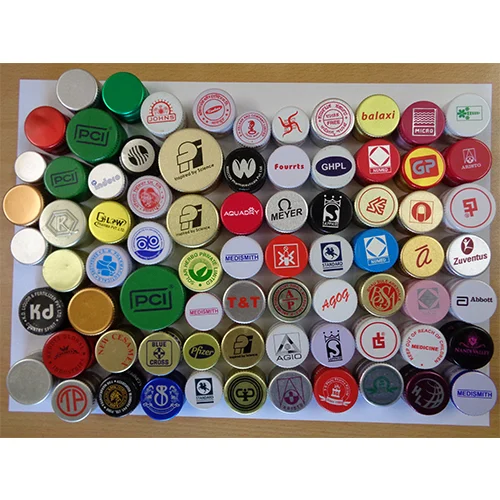
8011-cap
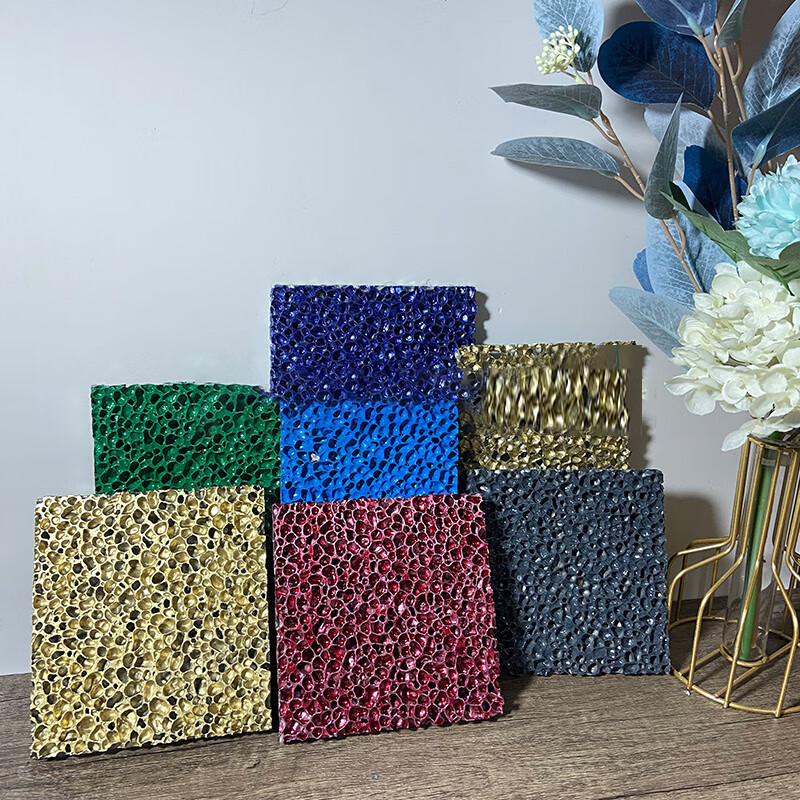
porous-foam-sheet-plate
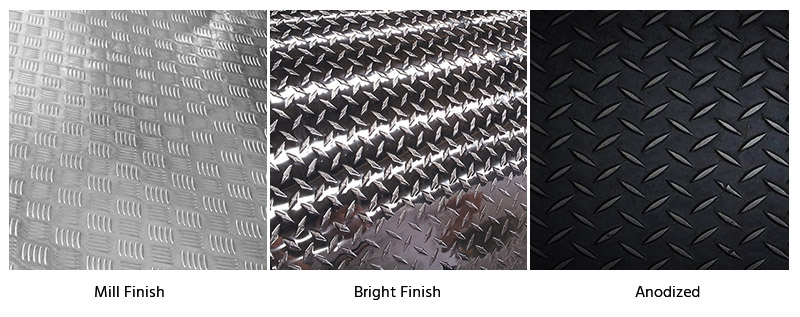
tread-checkered-plate
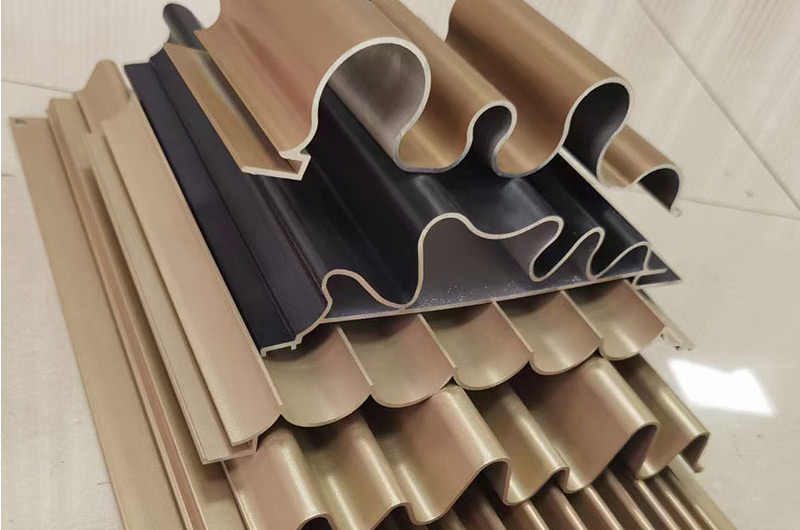
corrugated-sheet
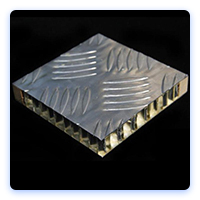
aluminum-honeycomb-plate
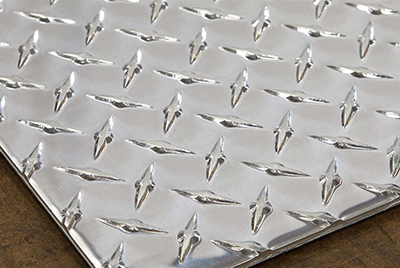
diamond-plate
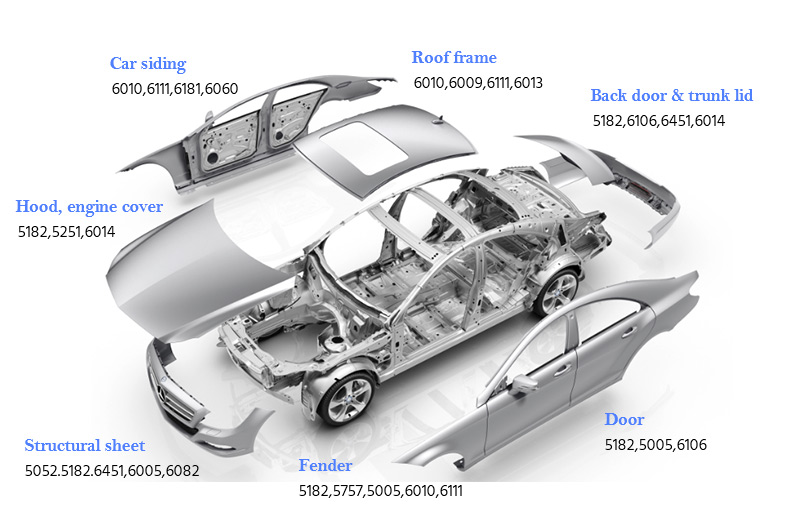
auto-body-aluminum-panel
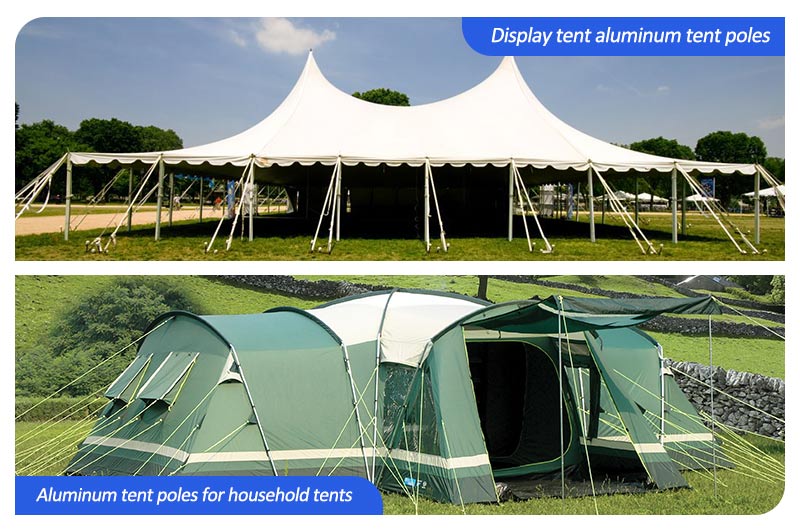
tent-pole
Differences between Anodising vs Powder Coating
Anodizing
- Chemical process that creates a durable oxide layer on metal surfaces, primarily aluminum.
- Enhances corrosion resistance and surface hardness.
- Can be clear or colored, offering aesthetic options.
- Provides a uniform finish that is integrated into the metal surface.
- Resistant to fading, chipping, and scratching.
- Suitable for outdoor applications due to its durability.
- Limited color options compared to powder coating.
Powder Coating
- Coating cheaper than anodizing
- Application of dry powder onto metal surfaces electrostatically, followed by curing in an oven.
- Provides a thicker coating compared to traditional liquid coatings.
- Offers a wide range of color options, including metallic and textured finishes.
- Can be used to create decorative effects like gloss, matte, and satin finishes.
- Resistant to impact, chemicals, and weathering.
- Requires proper surface preparation for optimal adhesion.
- May require periodic touch-ups or recoating over time, especially in high-wear areas.
These differences highlight the distinct advantages and applications of each coating method based on factors like durability, aesthetics, and color options.Quick Quote
The application of aluminum anodizing
- Anti static workbench and frame on the assembly line.
- Building decoration materials such as curtain walls, buildings, offices, shopping malls, metal ceilings, etc.
- 3C electronic products such as mobile phone case and computer case.
- Household appliances and furniture, such as electrical panel, cabinet panel, refrigerator panel, furniture panel, etc.
- Aluminum anodizing is also widely used in mechanical parts, aircraft and automobile parts, precision instruments and radio equipment, machine shells, lamps and lighting, handicrafts, interior decoration, signs, automobile decoration and other industries.