When purchasing aluminum alloy products, common surface treatment options include Mill Finish, Anodizing, Color coating, heat sublimation printing and surface mechanical treatment. Surface treatment of aluminum alloys not only enhances their appearance but also improves durability, corrosion resistance, and weather resistance, thereby extending the product's lifespan and enabling it to withstand more demanding environmental conditions.
Chalco offers comprehensive aluminum alloy surface treatment services, covering all of the above methods, to ensure that each product achieves optimal performance and aesthetic appeal. Whether you require a mill finish, professional anodizing, vibrant color coating, or personalized heat transfer printing, we provide high-quality solutions tailored to your needs. Quick Quote
Why does your aluminum alloy project need surface treatment?
Aluminum is a widely used high-tech material, but if not properly treated, it may face problems such as corrosion, wear and tear, poor conductivity, or friction. Correct aluminum surface treatment can effectively prevent the occurrence of the above issue.
- Exclusive high-end appearance;
- Improve durability and extend service life;
- Corrosion prevention; Improve wear resistance;
- Reduce wear and friction;
- Electrical insulation or conductivity;
- Improve surface structure and roughness;
- Obtain the required reflectivity;
- Better adhesion or painting adhesion.
Chalco available surface treatment technologies for aluminum alloys
Durable anodization
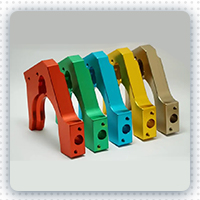
Anodizing is the process of using a substrate as an anode and electrolyzing it in an electrolyte to form a protective oxide film on the surface of the substrate. Chalco aluminum anodizing process can achieve a maximum length of up to 16 meters. Chalco offers colors such as black, red, silver white, glossy silver white, oxidized snow white, and bronze from light to black. Double color anodizing can also be customized according to requirements.
Basic principle
Anodizing is essentially based on the principle of water electrolysis. Aluminum and its alloys are placed in an electrolyte solution under specific conditions and an applied electric current, where they act as the anode during the electrolysis process.
Electrolysis process
When aluminum or its alloys serve as the anode and come into contact with electrolytes such as sulfuric acid, chromic acid, or oxalic acid, an oxidation reaction occurs on the surface, forming an aluminum oxide layer.
Oxide layer thickness
The thickness of a standard anodized layer ranges from 5 to 30 microns, while the thickness of a hard anodized layer ranges from 25 to 150 microns.
Performance enhancement
- The hardness and wear resistance of aluminum and its alloys are significantly improved after anodizing, with hardness reaching 250 to 500 kg/mm².
- The anodized layer has excellent heat resistance, with the melting point of the hard layer reaching up to 2320K.
- Insulation properties are enhanced, with breakdown voltages exceeding 2000V.
- Corrosion resistance is greatly improved, with the anodized layer enduring thousands of hours in a 0.03% NaCl salt spray without corrosion.
Special functions
- The thin anodized layer contains numerous micropores with strong absorption capacity, capable of holding various lubricants, making it suitable for manufacturing engine cylinders or other wear-resistant parts.
- The micropores in the anodized layer can also absorb dyes, allowing it to be colored into various beautiful hues.
Anodized Products
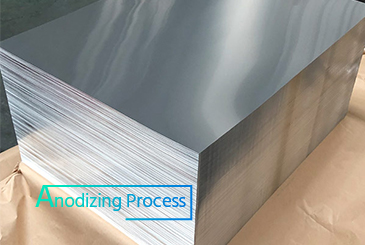
Anodized aluminum sheet plate
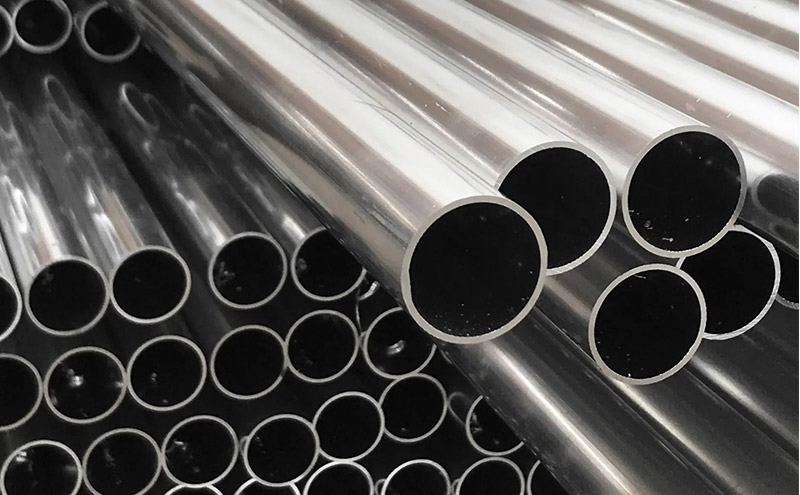
Anodized aluminum tube
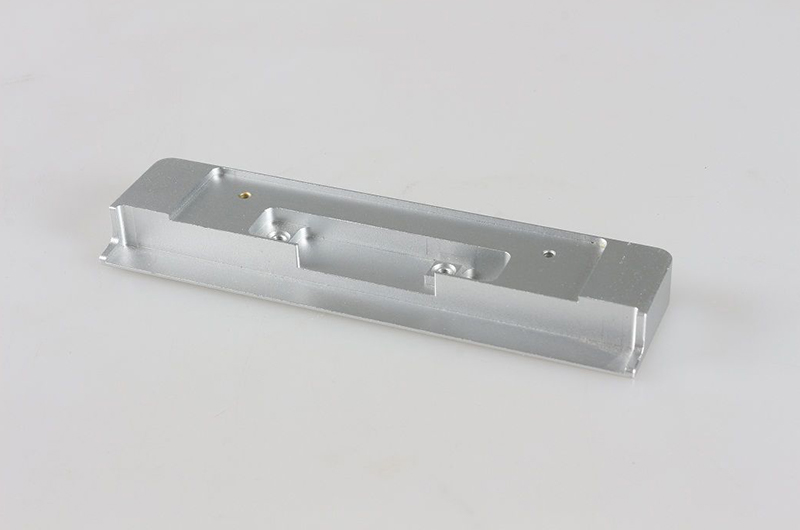
Anodized aluminum profile
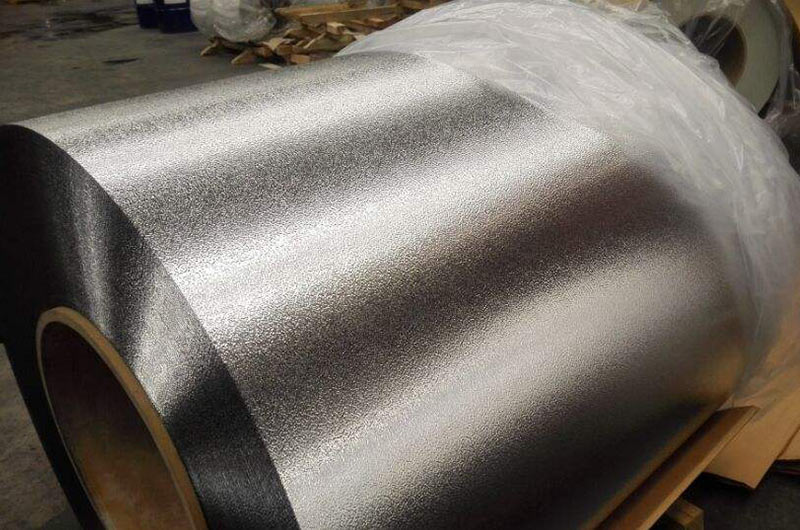
Anodized embossed aluminum coils
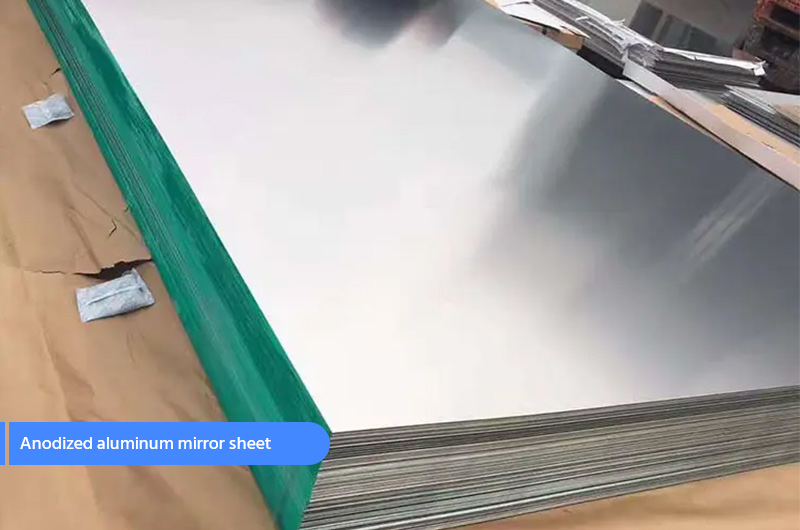
Anodized mirror aluminum
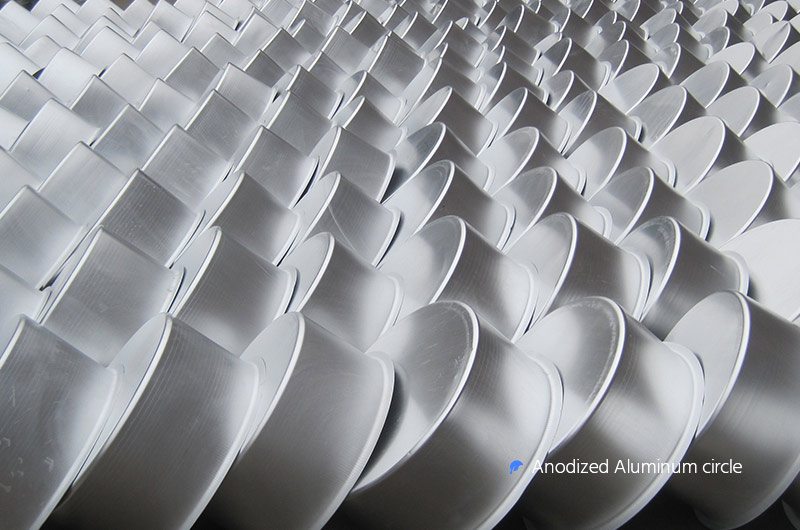
Anodized aluminum discs
For more knowledge, you can click [All about aluminum anodizing] to learn more, or consult our expert technicians. Quick Quote
Vibrant color coated
Color coating for aluminum alloy is a surface treatment process where different colors and types of coatings are applied to aluminum products, giving them a variety of colors and surface effects. This process not only enhances the aesthetic appeal of the products but also improves their corrosion resistance, weather resistance, and surface hardness. The main methods include powder coating, liquid coating, and spray painting.
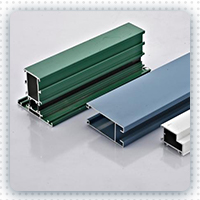
Powder coating
Its coating has strong adhesion, weather resistance, peeling resistance, and UV resistance.
Chalco currently has various types of powder spraying and coloring colors, which can be adjusted with incoming materials and are rich in colors.
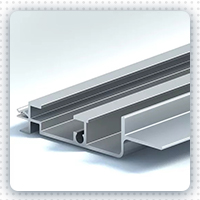
Fluorocarbon paint spraying
It has extraordinary functions of resisting adverse weather, acid and alkali erosion, and being unaffected by air pollution, ozone, and acid rain. Fluoropolymer has uniform color and excellent resistance to fading and contamination. Even if the building is expanded many years later, the new and old colors can still be highly matched. The types of fluorocarbon paint spraying coatings include two coats (primer plus topcoat), three coats (primer, topcoat plus varnish), and four coats (primer, barrier paint, topcoat plus varnish).
- Width: the maximum width of the colour coated aluminum coil produced by Chalco can reach 2 meters. Length: according to the requirements, the length is unlimited.
- Thickness: usually 0.2mm-6mm, coating thickness 5-25UM. Alloy: 1100, 1050, 1060, 1070, 3003, 3004, 3105, 5052, 5005 and other aluminum alloy
- Standards: ASTM-B-209M, BS EN 485-2, BS EN 573-3, GB/T3880-2008
- Surface: our colored aluminum sheet metal rolls has rich colors, including single color aluminum plate, both side coated aluminum, mirror finish coated aluminium coil sheet, stone and marble finish coated aluminum coil, wood finish powder coating aluminum, printed coated aluminum, and brushed coated aluminum , stucco embossed finish coated aluminium coil sheet, ect.
- General dimensions: 1.0 * 1219 * 2438mm, 2.0 * 1220 * 2440mm, 3.0 * 1200 * 2400mm, 3.0 * 1500 * 3000mm, 2.5 * 1250 * 2500mm, etc.
Color coated products
Vivid sublimation printing
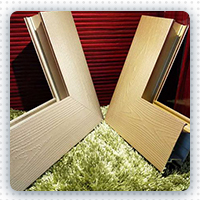
Sublimation is a technique that uses heat to turn solid dye into gas, which then penetrates the aluminum alloy surface. Through high temperature and pressure, the dye bonds with the surface, creating a durable pattern. This technique is ideal for producing high-resolution, vibrant images and is widely used in home decor, signage, and personalized gifts, offering lifelike patterns with excellent durability.
- Alloy: 1060, 1100, 1050, 1070, 3003 and other alloys.
- Thickness: 0.22-1.1mm, common thickness is 0.45, 0.55, 1.0mm
- Dimensions: 1200x600mm, 600x400mm, 600x300mm, 610x305mm or other customized dimensions.
- Surface: it can be made into brushed sublimation plate, mirror sublimation plate, high gloss sublimation plate, matte sublimation plate, etc.
For more knowledge, you can click [Sublimation Aluminum Sheet] to learn more, or consult our expert technicians. Quick Quote
Uniform electrophoretic coating
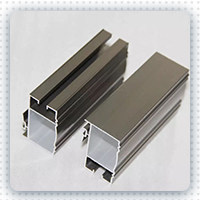
Electrophoretic painting is based on anodic oxidation, and a layer of water-soluble acrylic paint film is covered on the oxide film through the action of electrophoresis.
Therefore, the surface facial mask of electrophoresis products is a composite film of anodic oxide film and water-soluble acrylic paint film.
It has better corrosion resistance, weather resistance, and wear resistance than anodizing, making the surface of aluminum alloy products smoother and more beautiful. Suitable for outdoor buildings or vehicle components.
Chalco electrophoretic paint color types include silver white, frosted silver white, champagne, frosted champagne, pearl electrophoresis, etc.
Precision Mechanical Treatment
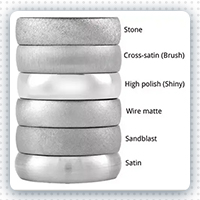
Use grinding media to apply mechanical force to make the aluminum surface smooth. This can improve its appearance or prepare for another finishing process.
Common examples include sandblasting, grinding, polishing, and embossing.
Chemical impregnation
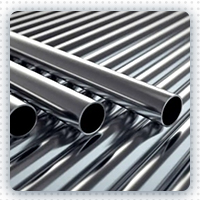
Apply chemical finishes by immersing aluminum alloy products in a chemical mixture.
The most popular chemical finishes include etching, creating a matte surface, and glossy impregnation, creating a very shiny mirror finish.
Plasma-enhanced electrochemical surface ceramic aluminum alloy
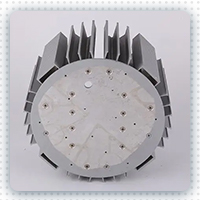
This type of material is the most advanced processing technology in the world today. This aluminum alloy product has good quality, although the cost is relatively high.
Plasma-enhanced electrochemical surface ceramic aluminum alloy products have more than 20 colors, and the biggest feature is that they can be colored like printed fabric according to needs. The surface is brightly colored and the decorative effect is excellent.
What makes Chalco stand out in aluminum surface treatment?
- Essential coating pretreatment;
- Anodic oxidation tests to control current, voltage, temperature, and bath composition;
- Compatibility with alloy components;
- Corrosion testing of painted aluminum products;
- Development of process parameters;
- Measurement of current waveform, voltage, and temperature;
- Quality testing and characterization of anodic oxide film;
- Surface and chemical analysis;
- Surface morphology;
- Wear test;
- Customer satisfaction.
Six key indicators make Chalco your first choice
1. Appearance quality of aluminum surface treatment
The surface of aluminum alloy anodizing shall not have defects such as electric burning or oxide film peeling.
The paint film after electrophoresis, pulverization, and fluorocarbon contour should be uniform, clean, and flat, without wrinkles, cracks, bubbles, flow marks, inclusions, peeling and other defects in the paint film effect.
The surface of the product must be coated to avoid surface scratches, collisions, and corrosion during transportation and stacking.
2. Wall thickness
Wall thickness is one of the main factors affecting the strength of the workpiece and is a key part of the project. For example, the minimum nominal wall thickness of the main profile of the Chalco outer window is not less than 1.4mm.
3. Aluminum surface treatment film thickness
The film thickness of industrial anodized aluminum is generally 12um;
The thickness of electrophoretic coating aluminum film is divided into abs;
The minimum local surface thickness of powder sprayed aluminum decorative coating is above 40um.
4. Chemical composition and mechanical properties
The chemical composition and mechanical properties of aluminum alloy products can be produced according to customer needs.
5. Color difference
When selecting the quantity and supply status of alloy plates, the impact of color difference on the building structure and some other aspects should be considered.
6. Resistance to salt spray corrosion, wear, waiting, and mortar, etc.
This is an important technical parameter of aluminum alloy products, which reflects the performance of the product and directly affects its use.