The 5056 H38 aluminum wire offers exceptional stiffness, elasticity, lightweight design, and strong corrosion resistance, making it perfect for high-strength applications with repeated loads.
We can customize the 5056 H38 aluminum wire in various diameters and specifications to meet your precise application needs.
- Excellent winding capability, reducing the risk of breakage, and suitable for machine winding.
- Available in multiple diameter sizes, with customized production upon request.
- Strict quality control, with tight tolerances ensuring consistent diameter.
- Smooth, burr-free surface for a clean finish.
Specifications for 5056 H38 aluminum wire for springs
Standards: ASTM B211, EN 573-3, QQ-A-225/7, MIL-DTL-3992
Certifications: Lloyd's Register, IATF 16949, SAE J452, ISO 9001, ISO 14001, ISO 45001
Inventory sizes for 5056 H38 aluminum wire for springs
The 5056 aluminum alloy features high strength, excellent fatigue resistance, and good formability. It is lightweight, corrosion-resistant, and widely used in industries such as aerospace and marine, where corrosion protection is essential.
Size Range: 1-15 mm
Tolerance Range: ± 0.02 mm
- 1.0 mm Diameter: Suitable for lightweight electronic devices or small mechanical components.
- 1.5 mm Diameter: Ideal for medium-load household appliances or small machinery.
- 2.0 mm Diameter: Used for higher strength in medium-sized machinery.
- 3.0 mm - 4.0 mm Diameter: High load capacity, suitable for high-strength, large equipment.
Complete size table for aluminum wire for springs
Alloy | Temper | Diameter (mm) | Tolerance |
1050, 1070, 1100, 1350 | H18 | 1-15 | ±0.02 |
2011, 2017, 2024, 2117 | O, T2 | 3-10 | ±0.02 |
3003, 3004, 3A21 | H14 | 3-10 | ±0.02 |
5052, 5051, 5083, 5154, 5183, 5754, 5050 | O, H14, H18, H32 | 1-15 | ±0.02 |
6005, 6056, 6060, 6061, 6063, 6065, 6082, 6101, 6463 | O, T2, T4, H14, H18, H32 | 3-30 | ±0.02 |
7075, 7050, 7003, 7004 | O, H13, T73 | 1.6-15 | ±0.02 |
7A01, 7A02, 7A03, 7A04, 7A09 | O, H13, T73 | 1.6-10 | ±0.02 |
Chemical elements of 5056 H38 aluminum wire for springs
Chemical Element | % Present |
Si | 0.30 max |
Fe | 0.40 max |
Cu | 0.1 max |
Mn | 0.05 - 0.20 |
Mg | 4.50 - 5.60 |
Cr | 0.05 - 0.20 |
Zn | 0.10 max |
Other (Each) | 0.05 max |
Others (Total) | 0.15 max |
Aluminium (Al) | Balance |
Properties of 5056 H38 aluminum wire for springs
Physical Property | Value |
Brinell Hardness | 100 |
Modulus of Elasticity | 67 GPa |
Shear Modulus | 25 GPa |
Fatigue Strength | 150 GPa |
Yield Strength | 350 GPa |
Tensile Strength | 420 GPa |
Thermal Conductivity | 130 W/m.K |
Electrical Resistivity | 29 % IACS |
Elongation at Fracture | 14% |
Applications of 5056 H38 aluminum wire for springs
Compression Springs
Compression springs shorten or compress when a force is applied, storing mechanical energy in the process. They are commonly used in applications such as shock absorbers and engine suspensions.
Contact us now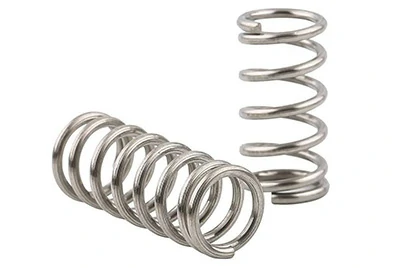
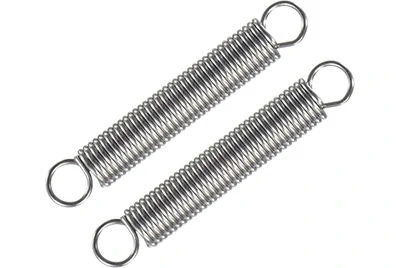
Tension Springs
When a tension spring is stretched, it attempts to return to its original shape. They are suitable for applications such as door locks and brake systems.
Contact us nowTorsion Springs
A torsion spring is a spiral-wound spring used for torque applications, commonly found in rotating door hinges or automotive seat adjustment mechanisms.
Contact us now
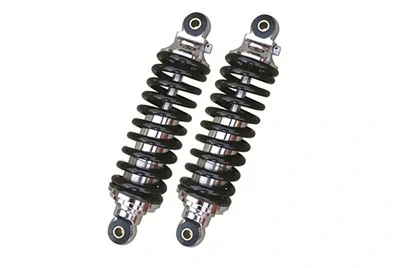
Spiral Springs
A spiral spring is a spiral-shaped metal spring suitable for use in consumer electronics (such as computer keyboards) and precision instruments.
Contact us nowAluminum springs are widely used in various industries such as aerospace, electronics, and automotive due to their lightweight, corrosion resistance, and excellent elasticity.
They are suitable for applications in shock absorption, tension maintenance, and lightweight design in complex mechanical structures.
Advantages of 5056 H38 aluminum wire for springs
- High Strength: Offers good mechanical strength, capable of withstanding significant loads.
- Strong Fatigue Resistance: Effectively resists fatigue cracking after cold working and treatment, making it suitable for springs subjected to repeated loads.
- Good Elasticity: Demonstrates excellent elasticity and recovery in spring applications.
- Outstanding Corrosion Resistance: Particularly suitable for use in marine or humid environments.
- Excellent Ductility: Easily processed into various shapes while maintaining good mechanical properties.
- Good Thermal Conductivity: Suitable for applications requiring heat dissipation.
- Cost-Effective: Aluminum offers a high cost-performance ratio.
Surface treatments for 5056 H38 aluminum wire for springs
- Anodizing: Anodizing significantly enhances the corrosion resistance of 5056 aluminum wire and increases surface hardness, preventing scratches or wear during use.
- Electroplating: Primarily used to improve the wear resistance and oxidation resistance of aluminum springs, especially effective in high-friction or high-temperature environments.
- Chemical Coating: Enhances the corrosion resistance of the aluminum wire surface, particularly in springs used in marine environments. Additionally, chemical coatings can increase the lubricity of the spring surface.
- Shot Peening: Improves the surface hardness and fatigue resistance of the aluminum wire.
How Chalco implements quality control
- Each batch of aluminum wire undergoes composition testing to ensure that chemical composition and mechanical properties meet expected standards.
- We use advanced hot continuous rolling processes to produce aluminum wire, ensuring excellent surface quality and stable performance, while achieving high strength and good ductility to meet stringent customer requirements.
- Throughout the production process, we perform multiple quality checks, including dimensional tolerances, mechanical properties, and corrosion resistance testing.
- We provide customized quality control solutions based on specific customer needs, ensuring that products meet their application requirements.
- Through these rigorous quality control measures, we ensure that each aluminum wire has high reliability and durability, making it suitable for various complex and demanding applications.
Packaging and transportation of 5056 H38 aluminum wire for springs
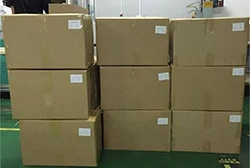
Carton Packaging
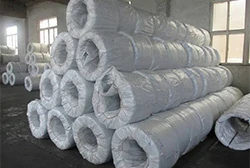
Woven Bag Packaging
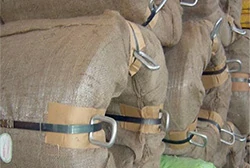
Burlap Packaging
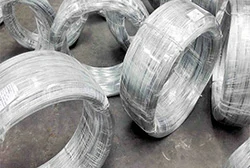
Plastic Film Packaging
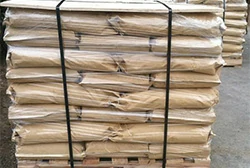
Kraft Paper Packaging
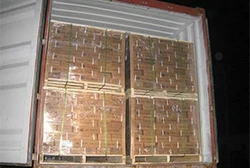
Container Transport
Advantages of aluminum springs compared to steel springs
- Lower Cold Processing Costs: Aluminum is easier to shape during cold processing, resulting in lower production costs for aluminum springs.
- Enhanced Corrosion Resistance and Surface Hardness: Anodizing treatment enhances aluminum's corrosion resistance and surface hardness while providing a variety of color options, improving both aesthetics and functionality.
- Corrosion Resistance: Aluminum springs perform better in humid or highly corrosive environments.
- Higher Fatigue Strength: Aluminum has advantages in fatigue strength, while steel is more prone to fatigue failure under cyclic stress.
- Lightweight: Aluminum springs weigh only one-third as much as steel, which is especially important in aerospace and automotive applications.
- Complex Shapes: The plasticity and formability of aluminum allow for the manufacturing of complex spring geometries.
Popular related products from Chalco
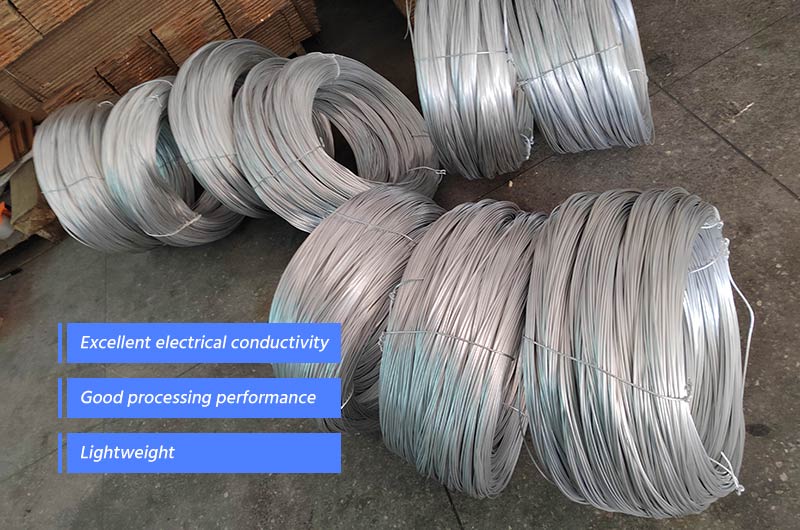
Aluminum Wire for Rivets
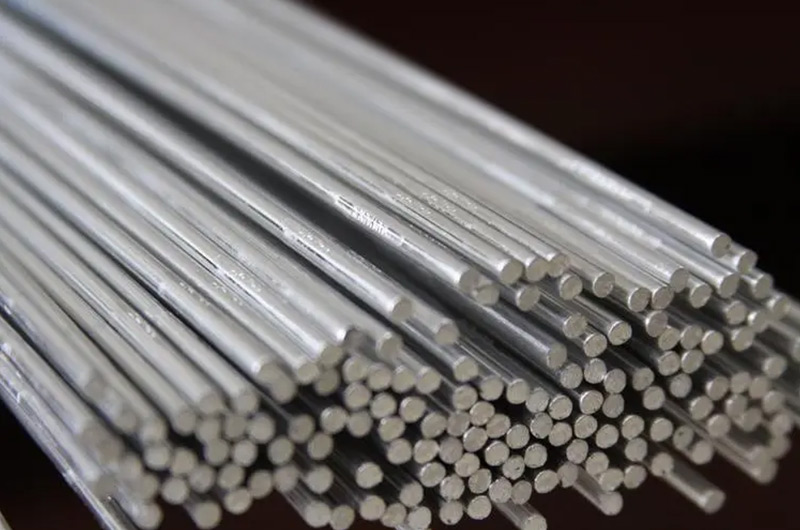
Aluminum Welding Wire
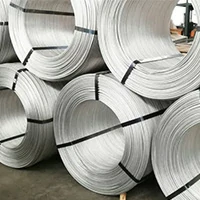
Bare Aluminum Wire for Electrical Use