Why choose Chalco Aluminum 6101 electrical busbar
Chalco 6101 EC grade aluminum busbar conforms to IEC 60105, ISO 209-1, 2, DIN EN 755-2, DIN EN 755-5 standards. The 6101 aluminum busbar has excellent conductivity, high strength, good corrosion resistance, and lightweight design.
Chalco Aluminum supplies 1050, 1060, 1070, 1100, 1350, 6060, 6082, 6101 etc. conductive aluminum busbar product. The products have been widely exported to Hitachi, ABB, Siemens, Legrand, Toshiba etc. companies, and enjoy good reputation from them.
Specification of Chalco Aluminum 6101 electrical aluminum busbar
Tempers: T6, T61, T63, T64, T65
Equivalent Names: UNS A96101, AA6101-T61, Al6101-T61, AA6101-T65, Al6101-T65
Specification compliance: ASTM B317/B317M, ASTM B236, ASTM B241, ASTM B429, IEC 60105, ISO 209-1/2, DIN EN 755-2, DIN EN 755-5:2008-06
Testing & quality control: Conductivity Test/Temperature Rise Test/Bending Test
Surface Treatment & Processing
- Surface Requirements: Smooth, burr-free, clean, oil-free, with a dense, uniform oxide layer for superior corrosion resistance.
- Anodizing – Enhances oxidation resistance and durability.
- Tin Plating & Electroplating – Improves conductivity and corrosion resistance (available in silver, tin, nickel).
- Insulation Coating & Sleeves – Powder coating, epoxy resin coating, insulation paint, PVC, heat shrink tubing, silicone rubber for electrical insulation and enhanced safety.
- Protective spraying – Additional surface protection for extended service life.
- Edge processing: Right angle, rounded corner, R-rounded corner – tailored for different structural and assembly needs.
- Machining & Fabrication: Cutting, Drilling, Bending, Stamping
For detailed production and processing capacity, check the [Capacity Part].
Stock Sizes
- Thickness: 0.08"-9.8" (2-250mm)
- Width: 0.2"-11.8" (5-300mm)
- Length: Customizable up to project specifications.
Dimensions and tolerance | |||
Length | Maximum 6m [Click for size table] | ||
Width | 10mm - 200mm | ||
Width tolerance [mm] | b≤35.50 | ±0.40 | |
35.50 | ±0.80 | ||
6>100.00 | ±1.20 | ||
Thickness | 0.15mm - 40mm | ||
Thickness tolerance [mm] | a≤6.30 | ±0.15 | |
6.30 | ±0.20 | ||
a>12.50 | ±0.30 | ||
Minimum Bend Radius [mm] | 1x thickness (up to 12mm) 2x thickness (>12mm) |
Note: In the above table,
a=thickness, i.e. narrow edge size;
b=width refers to the size of the wide edge.
Product types of Chalco 6101 electrical aluminum busbar
-
6101 EC Grade Flat Busbar
A key choice for power transmission, switchgear, and enclosures, with excellent conductivity, lightweight design, and corrosion resistance for high-current use.
-
Extruded 6101 Aluminum Busbar
Produced with high-precision extrusion for uniform dimensions, enhanced strength, and superior finish, ideal for demanding structural and electrical applications.
-
6101 busbar coil strip
Provide high conductivity, flexibility, and corrosion resistance, ideal for compact power distribution and flexible connections.
-
6101 busbar by plate sawing
Precision-cut for accurate dimensions, perfect for precision equipment and applications requiring exact specifications.
-
Flexible 6101 Aluminum Busbar
Composed of multiple thin layers of 6101 aluminum, laminated or braided together to provide high flexibility, reduced stress fatigue, and improved vibration resistance.
-
Laminated 6101 Aluminum Busbar
Consist of multiple conductive layers separated by insulating materials, significantly reducing electromagnetic interference (EMI) and improving power efficiency.
-
Round Edge 6101 Aluminum Busbar
Feature smooth, rounded corners to minimize stress concentration, reducing the risk of electrical discharge and improving safety in high-voltage applications.
-
Insulated 6101 Aluminum Busbar
Feature protective coatings or insulating sleeves to enhance dielectric strength, safety, and corrosion resistance. Ideal for high-voltage systems where electrical isolation is necessary.
Properties of Chalco Aluminum 6101 electrical aluminum busbar
Chalco 6101 aluminum busbar has outstanding performance advantages in terms of conductivity and current carrying capacity. According to different busbar sizes, Chalco conductive aluminum bus bars can handle currents up to 4000A.
For specific requirements, please clickQuick Quoteto contact our customer service personnel. The following table is a reference table for the performance parameters of Chalco 6101 conductive aluminum busbar.
Temper | Yield Strength Rp0.2(Mpa) | Ultimate tensile strength Rm(Mpa) | Elongation | Conductivity %IACS |
6101-T6 | ≥172 | ≥200 | 15 | - |
6101-T61 | ≥55 | ≥103 | - | ≥59% |
6101-T63 | ≥150 | ≥185 | - | ≥56 |
6101-T64 | ≥55 | ≥105 | - | ≥59.5 |
6101-T65 | - | - | - | ≥58% |
Manufacturing Processing and Customization capabilities
Chalco Aluminum is a leading manufacturer of high-performance aluminum busbars, offering comprehensive processing, customization, and manufacturing capabilities to meet diverse industrial and electrical applications. Our state-of-the-art facilities ensure precision machining, advanced material cladding, and high-quality surface treatments to enhance performance, durability, and reliability.
Surface treatment for enhanced performance
To improve the durability, conductivity, and corrosion resistance of our aluminum busbars, we offer the following surface treatments:
- Anodizing – Forms a dense oxide layer for enhanced corrosion resistance.
- Electroplating – Silver, tin, or nickel plating to increase electrical conductivity and oxidation resistance.
- Protective Spraying – Ensures long-term performance in harsh environments.
Customization & quality assurance
We support custom orders based on specific electrical and mechanical requirements, including:
- Custom dimensions – Thickness 0.15mm - 40mm, Width 10mm - 200mm, Length up to 6m.
- Special bending and forming – Tailored to fit unique electrical layouts.
- Stringent testing procedures – Including conductivity tests, temperature rise tests, and bending tests to guarantee optimal performance.
Precision machining & fabrication
We provide advanced machining services to achieve precise dimensions and structural integrity for various applications:
- Cutting – Custom length adjustments for different installations.
- Drilling – Precision hole placement for electrical connections.
- Bending – Tailored shaping to fit complex assembly requirements.
- Stamping – High-efficiency mass production for uniform busbar components.
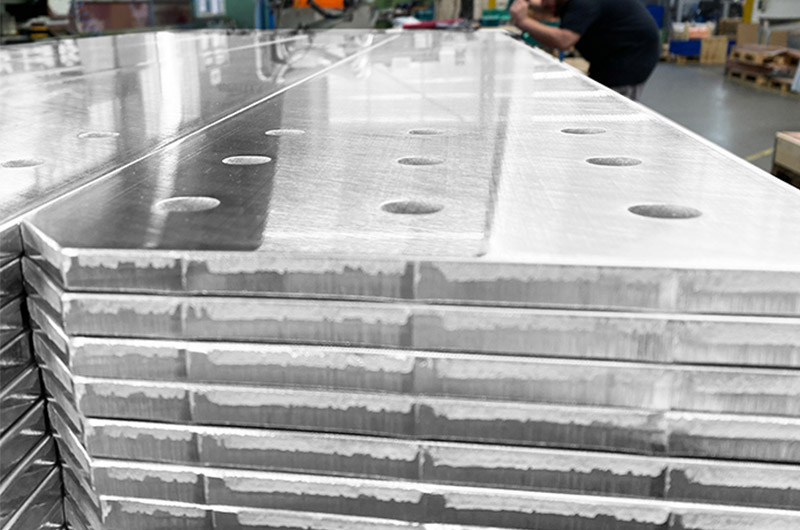
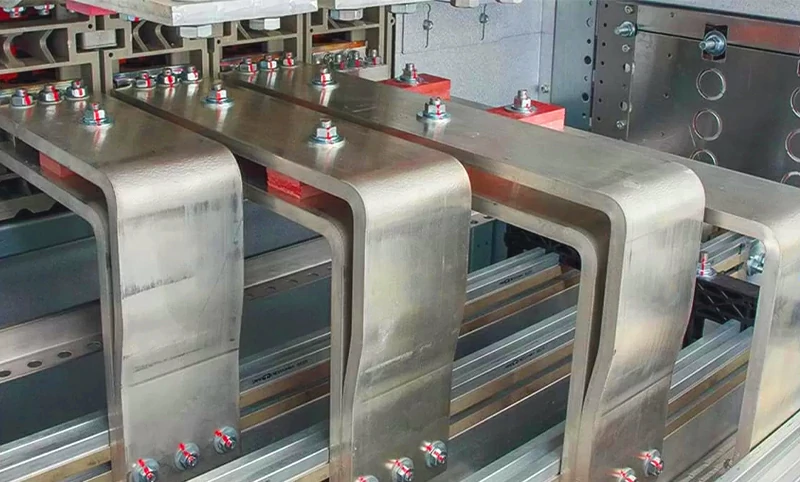
Copper cladding & insulation coating
Our specialized cladding and insulation techniques enhance conductivity, corrosion resistance, and electrical safety:
- Copper-Clad Aluminum (CCA) Processing – Utilizing explosive welding, rolling cladding, and hot-dip cladding to form a high-strength copper-aluminum composite layer, improving conductivity and mechanical performance.
- Insulation Coatings – Powder coating, epoxy resin coating to prevent electrical leakage and corrosion.
- Insulation Sleeves – Options include PVC, heat shrink tubing, and silicone rubber, ensuring additional protection in high-voltage applications.
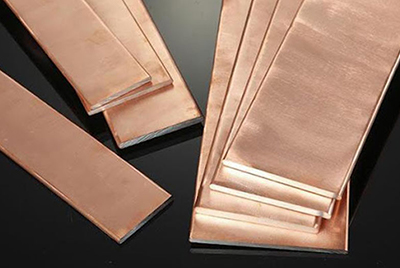
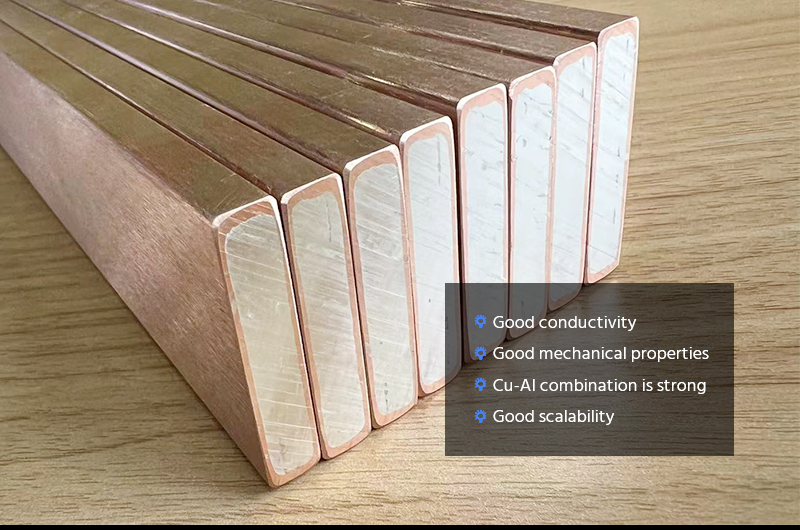
At Chalco Aluminum, we combine high-precision manufacturing with advanced processing technologies, ensuring reliable, high-quality aluminum and copper-clad busbars for global industrial and electrical applications.
For further inquiries or customized solutions, contact us today for a quick quote!Quick Quote
Advantage of Chalco Aluminum 6101 electrical aluminum busbar
Chalco can provide complete design, including machining, forming, and brazing. Cutting, stamping, bending, drilling and other processing can be completed according to the specific requirements of customers for current capacity and bending degree.
Chalco can provide surface coating and insulation processing for conductive aluminum busbars according to customer requirements to improve product corrosion resistance, aesthetics, and avoid short circuits and other issues.
High conductivity: the 6101 conductive aluminum busbar is lighter than ordinary copper wires, but its conductivity is equivalent to that of copper.
Lightweight: due to its lightweight, it is often used in weight sensitive applications such as aerospace and automotive to achieve lightweight design.
Good thermal stability: 6101 conductive aluminum busbar is able to work for long periods of time in high temperature environments and not easily melt or deform.
Processability: it can perform machining operations such as cutting, punching, and bending to meet the needs of different applications.
Good corrosion resistance: 6101 conductive aluminum busbar can resist moisture, acid, alkali, and most corrosive media.
Application of Chalco Aluminum 6101 electrical aluminum busbar
Power transmission and distribution system: power substations, power transmission lines, switchgear, distribution cabinets, etc.
Industrial equipment and machinery: such as machine control cabinets, electrical panels, generators, transformers, and other equipment.
Transportation: power transmission and control systems such as electric vehicles, rail transit systems (such as subways, high-speed trains), and ships and aircraft.
Metallurgy and mining: such as electrolytic cells, electric furnaces, electrolytic aluminum production, and other high current applications.
Other fields: power transmission, electrical connection and distribution in areas such as renewable energy, electronic equipment, communication equipment, electrical systems of buildings and buildings, lighting systems, etc.
6101 aluminum busbar or copper aluminum busbar
6101 aluminum busbar is the most commonly used aluminum busbar, frequently compared with or used as a substitute for copper busbars. Due to its lightweight and cost-effectiveness, 6101 aluminum is a popular choice in many applications. Below is a comparison of the current-carrying capacity between 6101 aluminum busbars and copper busbars.Converting Copper to Aluminum using an Ampacity Chart | ||||||||||||
Ampacity Conversion Chart | Copper C110 | 30° C Rise | 50° C Rise | 65° C Rise | Aluminum 6101 | 30° C Rise | 50° C Rise | 65° C Rise | ||||
Flat Bar Size in Inches | Sq. In | Circ Mils Thousands | Weight Per Ft in Lb. | DC Resistance at 20° C, Microhms/Ft | 60 Hz Ampacity Amp* | Weight Per Ft in Lb. | DC Resistance at 20° C, Microhms/Ft | 60 Hz Ampacity Amp** | ||||
1/2*1 | 0.5 | 637 | 1.93 | 16.5 | 620 | 820 | 940 | 0.585 | 31 | 347 | 459 | 526 |
1/2*1 1/2 | 0.75 | 955 | 2.9 | 11 | 830 | 1100 | 1250 | 0.878 | 21 | 465 | 616 | 700 |
1/2*2 | 1 | 1270 | 3.86 | 8.23 | 1000 | 1350 | 1550 | 1.17 | 15 | 560 | 756 | 868 |
1/2*2 1/2 | 1.25 | 1590 | 4.83 | 6.58 | 1200 | 1600 | 1850 | 1.463 | 12 | 672 | 896 | 1036 |
1/2*3 | 1.5 | 1910 | 5.8 | 5.49 | 1400 | 1850 | 2150 | 1.755 | 10 | 784 | 1036 | 1204 |
1/2*3 1/2 | 1.75 | 2230 | 6.76 | 4.7 | 1550 | 2100 | 2400 | 2.048 | 9 | 868 | 1176 | 1344 |
1/2*4 | 2 | 2550 | 7.73 | 4.11 | 1700 | 2300 | 2650 | 2.34 | 8 | 952 | 1288 | 1484 |
1/2*5 | 2.5 | 3180 | 9.66 | 3.29 | 2050 | 2750 | 3150 | 2.925 | 6 | 1148 | 1540 | 1764 |
1/2*6 | 3 | 3820 | 11.6 | 2.74 | 2400 | 3150 | 3650 | 3.51 | 5 | 1344 | 1764 | 2044 |
1/2*8 | 4 | 5090 | 15.5 | 2.06 | 3000 | 4000 | 4600 | 4.68 | 4 | 1680 | 2240 | 2576 |
1/4*1/2 | 0.125 | 159 | 0.483 | 65.8 | 240 | 315 | 360 | 0.146 | 123 | 134 | 176 | 202 |
1/4*3/4 | 0.188 | 239 | 0.726 | 43.8 | 320 | 425 | 490 | 0.220 | 82 | 179 | 238 | 274 |
1/4*1 | 0.25 | 318 | 0.966 | 32.9 | 400 | 530 | 620 | 0.293 | 62 | 224 | 297 | 347 |
1/4*1 1/2 | 0.375 | 477 | 1.450 | 21.9 | 560 | 740 | 880 | 0.439 | 41 | 314 | 414 | 482 |
1/4*2 | 0.5 | 637 | 1.930 | 16.5 | 710 | 940 | 1100 | 0.585 | 31 | 398 | 526 | 616 |
1/4*2 1/2 | 0.625 | 796 | 2.410 | 13.2 | 850 | 1150 | 1300 | 0.731 | 25 | 476 | 644 | 728 |
1/4*3 | 0.75 | 955 | 2.900 | 11 | 990 | 1300 | 1550 | 0.878 | 21 | 554 | 728 | 868 |
1/4*3 1/2 | 0.875 | 1110 | 3.380 | 9.4 | 1150 | 1500 | 1750 | 1.024 | 18 | 644 | 840 | 980 |
1/4*4 | 1 | 1270 | 3.860 | 8.23 | 1250 | 1700 | 1950 | 1.170 | 15 | 700 | 952 | 1092 |
1/4*5 | 1.25 | 1590 | 4.830 | 6.58 | 1500 | 2000 | 2350 | 1.463 | 12 | 840 | 1120 | 1316 |
1/4*6 | 1.5 | 1910 | 5.800 | 5.49 | 1750 | 2350 | 2700 | 1.755 | 10 | 980 | 1316 | 1512 |
1/8*1/2 | 0.0625 | 79.6 | 0.241 | 132 | 153 | 205 | 235 | 0.073 | 247 | 86 | 115 | 132 |
1/8*3/4 | 0.0938 | 119 | 0.362 | 87.7 | 215 | 285 | 325 | 0.110 | 164 | 120 | 160 | 182 |
1/8*1 | 0.125 | 159 | 0.483 | 65.8 | 270 | 360 | 415 | 0.146 | 123 | 151 | 202 | 232 |
1/8*1 1/2 | 0.188 | 239 | 0.726 | 43.8 | 385 | 510 | 590 | 0.220 | 82 | 216 | 286 | 330 |
1/8*2 | 0.25 | 318 | 0.966 | 32.9 | 495 | 660 | 760 | 0.293 | 62 | 277 | 370 | 426 |
1/8*2 1/2 | 0.312 | 397 | 1.210 | 26.4 | 600 | 800 | 920 | 0.365 | 49 | 336 | 448 | 515 |
1/8*3 | 0.375 | 477 | 1.450 | 21.9 | 710 | 940 | 1100 | 0.439 | 41 | 398 | 526 | 616 |
1/8*3 1/2 | 0.438 | 558 | 1.690 | 18.8 | 810 | 1100 | 1250 | 0.512 | 35 | 454 | 616 | 700 |
1/8*4 | 0.5 | 636 | 1.930 | 16.5 | 900 | 1200 | 1400 | 0.585 | 31 | 504 | 672 | 784 |
1/16*1/2 | 0.0312 | 39.7 | 0.121 | 264 | 103 | 136 | 157 | 0.037 | 494 | 58 | 76 | 88 |
1/16*3/4 | 0.0469 | 59.7 | 0.181 | 175 | 145 | 193 | 225 | 0.055 | 327 | 81 | 108 | 126 |
1/16*1 | 0.0625 | 79.6 | 0.242 | 132 | 187 | 250 | 285 | 0.073 | 247 | 105 | 140 | 160 |
1/16*1 1/2 | 0.0938 | 119 | 0.362 | 87.7 | 270 | 355 | 410 | 0.110 | 164 | 151 | 199 | 230 |
1/16*2 | 0.125 | 159 | 0.483 | 65.8 | 345 | 460 | 530 | 0.146 | 123 | 193 | 258 | 297 |
Source: Copper Development Organization; Aluminum Association | ||||||||||||
Note: Ratings depend upon configuration, air flow, ambient temp, etc. The values depicted are an approximation. Controlled testing is always required to validate. | ||||||||||||
Other considerations Forming the busbar (aluminum has a tendency to crack with very tight radius) Electroplating the busbar (white rust on aluminum, oxidation is an issue with aluminum) Configuration of the busbar (vertical or horizontal configuration) |
In practical applications, there are two common methods to convert copper busbar dimensions to aluminum busbar dimensions to achieve the same temperature rise:
1. Increase the width of the aluminum bar by 27%. For example, to achieve the same temperature rise, a 5-inch x 1/4-inch aluminum bar is equivalent to a 4-inch x 1/4-inch copper bar.
2. Increase the thickness of the aluminum bar by about 50%. For example, to achieve the same temperature rise, a 4-inch x 3/8-inch aluminum bar is equivalent to a 4-inch x 1/4-inch copper bar.
Increasing the width of the aluminum busbar to enlarge the cross-sectional area not only reduces resistive heating but also significantly increases the surface area for heat dissipation. Changes in the thickness of rectangular bars do not notably affect the exposed surface area.
For instance, increasing the width from 4 inches to 8 inches for a 1/4-inch bar increases the capacity by about 87%, whereas increasing the thickness of a 4-inch bar from 1/4 inch to 1/2 inch only increases the capacity by about 45%. While both examples double the cross-sectional area, the current-carrying capacity difference between these two examples is 42%.
If you have electrical project needs or require technical support, feel free to contact Chalco. We will provide you with comprehensive solutions and professional services. Quick Quote
More electrical aluminum busbar products in Chalco
-
1060 EC aluminum busbar T3, T4, T5, T6, T8
It is usually formed by extrusion or rolling, and has good processing performance.
High conductivity Corrosion resistance -
1350 EC aluminum busbar H14, H16, H19
The minimum weight percentage is 99.5%, which is the material used for battery busbars.
Conductivity Thermal conductivity -
6060 EC aluminum busbar T4, T5, T6
It can effectively transmit and distribute electricity, reducing energy loss and line power loss.
Lightweight Processability -
6082 EC aluminum busbar T3, T4, T5, T6
It has high strength and hardness, while maintaining good conductivity.
Machinability High strength and rigidity -
6061 aluminum busbar has strong conductivity and is a universal material for most processing technologies.
Smooth surface Strong moisture resistance -
6063 EC aluminum busbar T4, T5, T6, T52, T66
In high-power applications, it can help effectively dissipate heat, and reduce the risk of equipment overheating.
Strong plasticity Excellent heat dissipation -
CCA bus or bimetallic conductive bus, it is the third generation of "new energy-saving conductor materials".
Conductivity Scalability Reliability
More electrical aluminum products in Chalco
- Conductive aluminum busbar
- EC Grade aluminum wire rod
- Electrical aluminum tubular bus pipe
- Aluminum plate strip foil for capacitor
- Aluminum wire for electrical application
Common sizes of Chalco aluminum electrical aluminum busbar
Square angle aluminum bar | ||||||||||
2mm | 2*30 | 2*40 | 2*67 | 2*70 | 2.5* 25 | |||||
3mm | 3*10 | 3*15 | 3*20 | 3*25 | 3*30 | 3*40 | 3*50 | 3*60 | 3*67 | 3*75 |
3*110 | ||||||||||
4mm | 4*10 | 4*15 | 4*20 | 4*25 | 4*30 | 4*40 | 4*45 | 4*50 | 4*60 | 4.6*60 |
4.8*9.8 | ||||||||||
5mm | 5*15 | 5*20 | 5*25 | 5*30 | 5*35 | 5*40 | 5*50 | 5*60 | 5*80 | 5*100 |
6mm | 6*20 | 6*25 | 6*30 | 6*40 | 6*50 | 6*54 | 6*55 | 6*60 | 6*65 | 6*70 |
6*75 | 6*80 | 6*100 | 6*120 | 6*150 | 6*160 | |||||
6.3mm | 6.3*50 | 6.3*63 | 6.3*63.5 | 6.3*80 | 6.35*50.8 | 6.35*76.2 | ||||
7mm | 7.6*80 | 7*150 | 7*4*20*4 | |||||||
8mm | 8*11 | 8*30 | 8*40 | 8*50 | 8*51 | 8*60 | 8*63 | 8*63.5 | 8*65 | 8*70 |
8*80 | 8*90 | 8*100 | 8*120 | 8*125 | 8.8*28.6 | |||||
9mm | 9*170 | 9*125 | 9. 2*64 | |||||||
10mm | 10*20 | 10*25 | 10*30 | 10*40 | 10*45 | 10*50 | 10*60 | 10*63 | 10*65 | 10*70 |
10*80 | 10*90 | 10*100 | 10*110 | 10*114 | 10*120 | 10*125 | 10*140 | 10*150 | 10*160 | |
12mm | 12*30 | 12*40 | 12*45 | 12*50 | 12*60 | 12*70 | 12*76 | 12*80 | 12*100 | 12*120 |
12*125 | 12*130 | 12*140 | 12*150 | 12*160 | ||||||
12.5mm | 12.5*90 | 12.5*100 | 12.5*125 | 12.5*127 | 12.7*101.6 | 12.7*160 | ||||
13mm | 13*125 | 13*130 | 13*160 | |||||||
14mm | 14*100 | 14*120 | 14.5*80 | |||||||
15mm | 15*30 | 15*35 | 15*50 | 15*60 | 15*80 | 15*100 | 15*120 | 15*125 | 15*150 | |
16mm | 16*30 | 16*90 | 16*100 | 16*110 | 16*125 | 16*130 | 16*140 | 16*150 | 16*160 | |
20mm | 20*76 | 20*100 | 20*120 | 20*130 | ||||||
Square bar | 19*19 | 30*45 | 15*15 | |||||||
Round bar | Φ6 | Φ8 | Φ10 | Φ11 | Φ12 | Φ14 | Φ15 | Φ15.6 | Φ16 | Φ18 |
Φ20 | Φ21 | Φ22 | Φ23 | Φ25 | Φ27 | Φ28 | Φ30 | Φ32 | Φ35 | |
Φ38 | Φ40 | Φ45 | Φ50 | Φ55 | Φ60 |
Round angle aluminum bar | |||||||||
2mm | R2*20 | R2.5* 50 | |||||||
3mm | R3*30 | R3*40 | R3*50 | R3*60 | R3*80 | R3*100 | R3*120 | R3*160 | |
4mm | R4*25 | R4*30 | R4*35 | R4*40 | R4*50 | R4*60 | R4.1*44.1 | R4.7*151 | |
5mm | R5*30 | R5*35 | R5*40 | R5*45 | R5*50 | R5*60 | R5*70 | R5*75 | R5*80 |
R5*90 | R5*100 | R5*120 | |||||||
6mm | R6*40 | R6*50 | R6*60 | R6*70 | R6*80 | R6*100 | R6*120 | R6*140 | R6*160 |
R6.3*63 | R6.35*76.5 | ||||||||
7mm | R7*70 | ||||||||
8mm | R8*40 | R8*50 | R8*60 | R8*80 | R8*100 | RS*120 | |||
10mm | R10*20 | R10*40 | R10*50 | R10*60 | R10*75 | R10*80 | R10*100 | R10*120 | R10*125 |
R10*150 | R10*160 | R10*170 | R10.4*25 | ||||||
12mm | R12*80 | R12*100 | R12*110 | R12*120 | R12*125 | R12*150 | R12*160 | ||
12.5mm | R12.5*80 | R12.5*125 | R12.7*90 | R12.7*127 | |||||
13mm | R13*120 | R13*125 | |||||||
14mm | R14*100 | R14*120 | R14*150 | ||||||
15mm | R15*100 | R15*120 | R15*130 | R15*150 | |||||
16mm | R16*150 | R16*160 | |||||||
19mm | R19.05*101.6 | R19.05*127 | |||||||
20mm | R20*80 | R20*120 | R20*130 | ||||||
Special-shaped hypotenuse | *4*50 | *5*50 | *5*60 | *6*40 | *6*50 | *6*60 | *6*80 | *8*60 | *8*80 |
*8*100 | *8*120 | *10*40 | *10*80 | *10*100 | *10*120 | *12*80 | *12*100 | *12*120 | |
*15*120 | *20*130 | *28*60 |