Among the 6000 series alloys, 6061, 6063 and 6082 alloys are the most popular, and 6951 aluminum has unique performance characteristics. Due to the addition of special alloy components and trace elements, 6951 alloy has superior formability, structural properties and superior brazing performance. Filled with other specific demands for 6000 series alloys, it is the intermediate choice material for certain specialized industries.
6951 aluminum -a special 6000 series aluminum alloy
The name of the main alloying elements of the 6000 series brass alloy is that it has universally moderate strength, good corrosion resistance, excellent burnability and processing The 6000 series aluminum alloys are renowned for their primary alloying elements, magnesium and silicon. They generally exhibit medium strength, good corrosion resistance, excellent weldability, and machinability.
Typically heat-treatable, these alloys offer good surface finish capabilities while maintaining high thermal and electrical conductivity. They are widely used in construction, transportation, and general engineering applications. In comparison, the 6951 aluminum alloy, while retaining the fundamental characteristics, demonstrates unique performance advantages and specialized application areas.
- Brazing performance: the 6951 alloy excels in brazing performance, making it suitable for heat exchangers and other brazing applications.
- Formability and structural stability: the 6951 alloy offers excellent formability and structural stability, particularly suited for manufacturing honeycomb core materials.
- Application areas: the 6951 alloy is suitable for brazing applications, aerospace honeycomb panels, automotive radiators, and other high-demand fields. other 6000 series alloys are used for construction profiles and decorative materials, structural components, marine parts, and mechanical applications.
Specification of Chalco 6951 aluminum
Grade: 6951; ENAW-AlMgSi0.3Cu; ENAW-6951
Classification: Aluminum - 6000 series (Magnesium Mg and Silicon Si are major alloying elements)
Density: 2.7 g/cm³
Product type: 6951 composite brazing sheet coil; 6951 sheet, coil, strip, and foil brazing fin material; 6951 brazing core material; 6951 honeycomb core material; 6951 welding rod
Standard: EN 573-3: 2009 Aluminum and aluminum alloys. Chemical composition and form of wrought products. Chemical composition and form of products
6951 composite brazing sheet coil
The 6951 composite brazing sheet, made of 6951 aluminum alloy and a brazing layer, is ideal for efficient heat transfer due to its high thermal conductivity, excellent corrosion resistance, and brazing performance. It is primarily used in heat exchangers, condensers, and radiators, particularly in automotive and air conditioning systems.
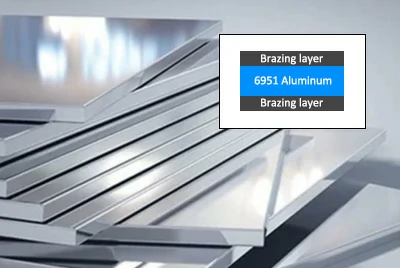
-
6951 + 4343/4045/4047 Brazing Layer
6951 core with 4343 or 4045 brazing layer, ideal for radiators and condensers due to good heat and mechanical properties.
-
6951 + 7072 + 4343/4045 Brazing Layer
7072 corrosion layer between 6951 core and 4343/4045 brazing layer, perfect for humid environments like automotive cooling systems.
-
6951 + 3003 Alloy Core + 4343 Brazing Layer
3003 core boosts corrosion resistance, ideal for long-term high-temperature applications like heat exchangers
-
6951 + 4004 Brazing Layer
4004 brazing layer provides low melting point and good bonding, used in high-temperature heat exchangers.
-
6951 Multi-layer Composite
Combines brazing, corrosion, and reinforcement layers, used in aerospace for strength and heat conductivity.
-
6951 Composite Tubes
Lightweight, durable tubes for heat exchangers, combining 6951 alloy and brazing layers for thermal efficiency.
6951 sheet, coil, strip, and foil brazing fin material
The 6951 sheet, coil, strip, and foil brazing fin material is crafted from 6951 aluminum alloy, which is renowned for its excellent thermal conductivity, corrosion resistance, and brazing performance. This material is specifically designed for efficient heat transfer applications.
Hot selling thicknesses: 0.08, 0.1, 0.15, 0.32, etc.…
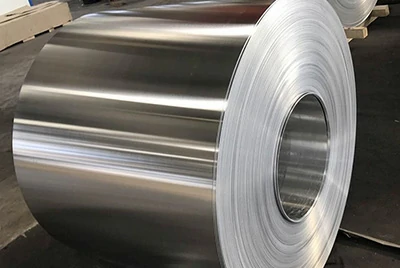
6951 brazing core material
The 6951 brazing core material is used as a core component in brazing, typically combined with other alloys. It offers high strength and corrosion resistance, maintaining stability during high-temperature brazing processes. It is widely used in manufacturing core components for heat exchangers and condensers.
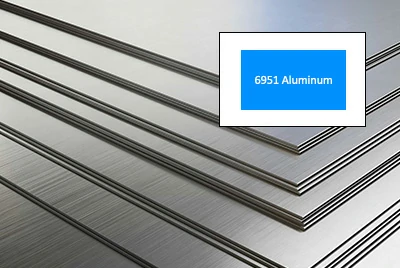
6951 honeycomb core material
Lightweight, high strength, and excellent corrosion resistance make it excel in demanding aerospace applications. It is widely used in the aerospace sector for manufacturing aircraft structural components such as wings, tail fins, and interior panels.
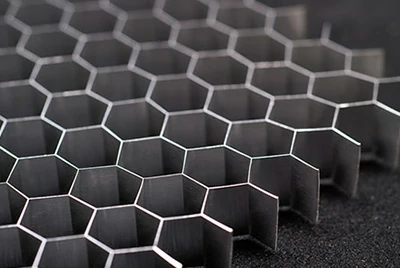
6951 welding rod
The 6951 welding rod is used in aluminum alloy welding and brazing, ensuring strong and durable joints. It offers high strength, stability at high temperatures, and excellent weld quality, making it ideal for aerospace and automotive manufacturing.
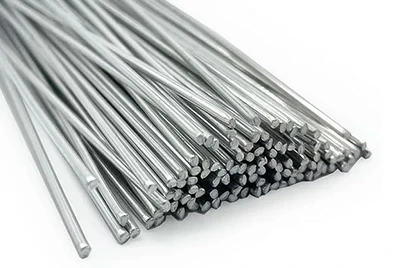
6951 aluminum chemical composition
6951 aluminum belongs to the 6000 series alloys, meaning its primary alloying elements are magnesium and silicon. Its improved version contains 97.2% aluminum, with primary alloying elements including magnesium, silicon, and iron, and additions of copper, manganese, and zinc. This alloy increases strength to enhance sag resistance and is heat-treatable (the metal becomes stronger through heating and cooling).
Chemical composition % of grade ENAW-AlMgSi0.3Cu (ENAW-6951 )
Chemical composition % of grade ENAW-AlMgSi0.3Cu (ENAW-6951 ) | |
Fe | max 0.8 |
S | 0.2 - 0.5 |
Mn | max 0.1 |
Cu | 0.15 - 0.4 |
Mg | 0.4 - 0.8 |
Zinc | max 0.2 |
Others | each 0.05; total 0.15 |
Al | remainder |
6951 aluminum mechanical property
Mechanical Properties | 6951-O | 6951-T6 | ||
Metric | English | Metric | English | |
Hardness, Brinell | 28 | 28 | 82 | 82 |
Tensile Strength, Ultimate | 110 MPa | 16000 psi | 270 MPa | 39200 psi |
Tensile Strength, Yield | 40.0 MPa | 5800 psi | 230 MPa | 33, 400 psi |
Elongation at Break | 30% | 30% | 13% | 13% |
Modulus of Elasticity | 69.0 GPa | 10000 ksi | 69.0 GPa | 10000 ksi |
Poissons Ratio | 0.33 | 0.33 | 0.33 | 0.33 |
Shear Modulus | 26.0 GPa | 3770 ksi | 26.0 GPa | 3770 ksi |
Shear Strength | 75.0 MPa | 10900 psi | 180 MPa | 26100 psi |
Thermal Properties | 6951-O | 6951-T6 | 6951-O | 6951-T6 |
Metric | English | Metric | English | |
CTE, linear | 23.4-25 µm/m-°C | 13.0-13.9 µin/in-°F | 23.4-25 µm/m-°C | 13.0-13.9 µin/in-°F |
Specific Heat Capacity | 0.890 J/g-°C | 0.213 BTU/lb-°F | 0.890 J/g-°C | 0.213 BTU/lb-°F |
Thermal Conductivity | 213 W/mK | 1480 BTU-in/hr-ft²-°F | 197 W/mK | 1370 BTU-in/hr-ft²-°F |
Melting Point | 616 - 654 °C | 1140 - 1210 °F | 616 - 654 °C | 1140 - 1210 °F |
Solidus | 616 °C | 1140°F | 616 °C | 1140°F |
Liquidus | 654 °C | 1210°F | 654 °C | 1210°F |
Application filed of Chalco 6951 aluminum products
- Brazing applications: the 6951 aluminum alloy is widely used in various brazing processes due to its excellent welding performance. It is particularly used in the aerospace, automotive, and air conditioning systems, as well as in heat exchangers, condensers, and radiators. In the electrical and electronics industry, it is commonly used to manufacture components with reliable welding connections and good conductivity.
- Honeycomb panel manufacturing: the 6951 aluminum alloy is often used to produce lightweight honeycomb structure panels. In the aerospace and automotive industries, honeycomb panels are widely used for structural support, insulation, and energy absorption structures. The lightweight, high strength, and good weldability of 6951 aluminum alloy make it a preferred material.
- Shipbuilding: it is used in the construction of hull structures and marine equipment due to its excellent seawater corrosion resistance and structural strength.
- Construction: it is used to manufacture building exterior panels, roofing materials, and decorative elements because of its weather resistance and aesthetic appeal.
- Consumer electronics: it is used in the housings of mobile phones, laptops, and other electronic products due to its lightweight, durability, and design advantages.