8079 Color Coated Aluminum Foil is a high-performance aluminum foil with a specialized coating treatment that offers excellent weather resistance, corrosion resistance, and thermal insulation properties. It is widely used in building insulation, roof waterproofing, and indoor thermal insulation applications, providing customers with durable and efficient solutions.
As one of the biggest aluminum manufacturers in China, we supply color lacquered aluminium coil for manufacture of roofing.The surface of our aluminium foil has no stains, no marks, no fissure, no hole, no perforations, no lines without lacquers and breaks, exports to Germany, Poland, United Kingdom, Algeria, Brazil, etc.
Hot selling products of 8079 coated aluminum foil
PE color coated aluminum foil
Coating Thickness: 15-25 microns
PE Color Coated Aluminum Foil is coated with a layer of polyester (PE) on the surface of the aluminum foil, which is then baked at high temperatures to form a strong protective film. This coating has excellent flexibility and decorative properties, with a rich range of colors and high gloss.
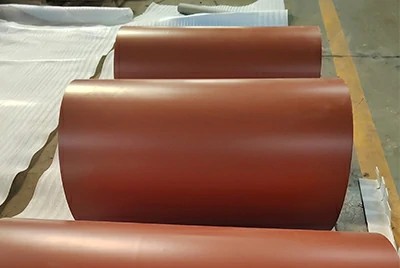
Features
- Excellent UV Resistance: Effectively resists ultraviolet radiation and prevents the coating from fading.
- Rich Color Options: A wide range of colors available to meet different decorative styles.
- Excellent Processability: Good ductility and flexibility, suitable for various bending, stamping, and forming processes.
- Cost-Effective: Compared to PVDF coatings, PE coatings offer a more affordable and cost-effective solution.
PVDF color coated aluminum foil
Coating Types: Traditional PVDF Coating, Nano PVDF Coating
Two-Layer Thickness:25-28 microns
Three-Layer Thickness:35-45 microns
Contact us now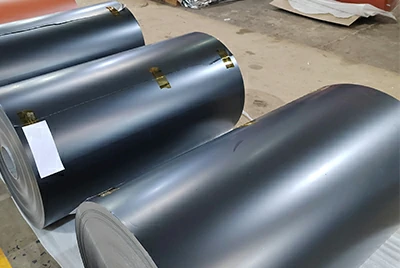
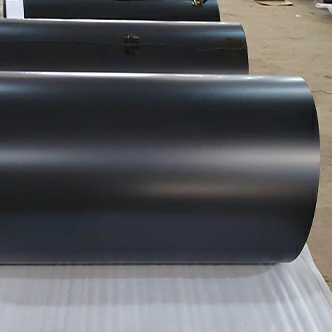
Traditional PVDF Coating
Traditional PVDF coating uses polyvinylidene fluoride (PVDF) resin as the primary component, which is baked at high temperatures to form a tough coating film. This coating offers exceptional weather resistance and UV resistance, ensuring it does not fade over extended periods of use.
- Outstanding Weather Resistance: Maintains stable performance in harsh environments, with a service life of over 20 years.
- Strong Corrosion Resistance: Resists damage from acid rain, salt spray, and various airborne pollutants.
- Self-Cleaning Performance: The surface is less likely to attract dirt, and rainwater can easily wash it clean.
Performance parameters of PVDF color coated aluminum foil
Description | Test Standard | PVDF Result |
Thickness of coating | PVDF paint≥25 um | 26um to 28um |
Coating Flexibility(T-bend) | PVDF paint ≤2T | 2T |
Color difference | ΔE≤2.0(follow color sample) | ΔE<2.0 |
Pencil Hardness | ≥HB | ≥HB |
Chemical Resistance | 5%HCl or 5%NaOH test in 24hours; ASTM D1308 | No change |
Coating Adhesion | ≥1 grade for 10*10mm² gridding test | 1 grade |
Resist Solvent | No change for 200 times (MEK) | No change |
Boiling Water Resistance | coating no tear off for 2 hours boiling | no tear off |
Peeling Strength/Stripping Strength | Average≥7 N/mm of 180°C peel off for panel with 0.5mm alu.skin | 7N/mm |
Impact Test for paint | 50Kg.cm impact - paint no split for panel | no split |
Abrasion Resistance(L/Mil) | ASTM D968 | 44 |
Temperature resistance | -40°C to +80°C temperature without change of color tolerance, paint peel off, peeling strength average drop rate ≤10% | change of gloss only. No paint peel off |
Coefficient of Linear Thermal Expansion | 100°C temperature difference | 2.4mm/m |
Detergent Resistance(3%) | ASTM D2248 | No change |
Humidity Resistance (3000hrs, 100%RH, 100°F) | ASTM D2247 | No change |
Salt Spray Resistance (3000hrs, 5% salt) | ASTM B117 | No change |
Resistance to Staining | 4000h radiate in 800W/m² in humidity condition, glossiness deviation less grade 2, color difference ≤4.0 | No change |
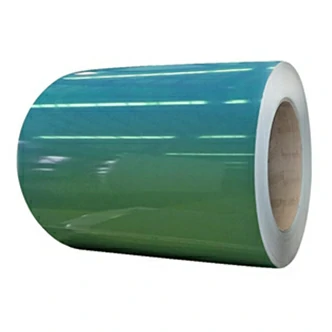
Nano PVDF Coating
Nano PVDF Coating is based on the traditional PVDF coating, with an additional layer of transparent nano-level materials to form a high-performance, self-cleaning coating. The nano-coating enhances the product's performance and extends its lifespan.
- Superb Self-Cleaning Ability: The nano structure makes the surface smoother, making it difficult for dust and pollutants to adhere, thus making it easier to clean.
- Higher Weather Resistance: Enhanced UV resistance and aging resistance, ideal for extreme climatic conditions.
- Antibacterial and Anti-Mold: Effectively suppresses the growth of bacteria and mold, keeping the surface clean and hygienic.
Performance parameters of NANO-PVDF color coated aluminum foil
Description | Test Standard | NANO-PVDF Result |
Thickness of coating | NANO PVDF paint≥34um | 35um to 37um |
Coating Flexibility(T-bend) | NANO PVDF paint ≤2T | 2T |
Color difference | ΔE≤2.0(follow color sample) | ΔE<2.0 |
Pencil Hardness | ISO 15184:1998 Section 10 | 5H |
Chemical Resistance | 5%HCl or 5%NaOH test in 240hours | No change |
Coating Adhesion | ISO 2409:2007 Section 6 | The edges of the cuts are completely smooth, none of the squares of the lattice is detached. |
Resist Solvent | No change for 200 times (MEK) | No change |
Boiling Water Resistance | EN438-2:2005 Section 12 | Rating 5, no visible change. Average change of mass: 0.08%; Average change of thickness: 1.36% |
Peeling Strength/Stripping Strength | BS EN319:1993 | 2.4 N/mm² |
Impact Test for paint | ISO6272-1:2002 Section 8 | The coating not crack or peel after 2kg weight ball dropped from 1.5m height |
Abrasion Resistance(L/Mil) | ISO7784-2:1997 Section 8 | The abrasive rubber wheel: Taber H-22; the cycles number: 100; the mean loss mass: 91mg |
Temperature resistance | EN438-2:2005 Section 19 | Rating 4, change of gloss only |
Coefficient of Linear Thermal Expansion | ISO11359-2:1999 Section 7 | 1.3 x 10-4 K |
Detergent Resistance(3%) | ASTM D2248 | No change |
Humidity Resistance (3000hrs, 100%RH, 100°F) | ASTM D2247 | No change |
Salt Spray Resistance (3000hrs, 5% salt) | ASTM B117 | No change |
Resistance to Staining | EN438-2:2005 Section 26 | Rating 5, no visible change |
Introduction to 8079 coated aluminum foil
Alloy: 8079
Temper: O, H22, H24
Thickness: 0.04mm - 0.15mm (commonly 0.05mm, 0.06mm, 0.07mm, 0.08mm, 0.1mm, 0.11mm, 0.12mm, 0.15mm)
Width: 200mm - 1400mm (commonly 150mm, 914mm, or custom)
Lacquered: One side or both sides
Color: Terracotta, White, Black, Blue, Green (colors can be customized based on client requirements)
Coating Thickness: ≤26μm (customized according to client needs)
Inner Diameter: 76.2mm, 152mm
Outer Diameter: <580mm
Standards: ASTM B209, EN 546-2, EN 485-2, EN 573-3
8079 color coated aluminum foil product photos
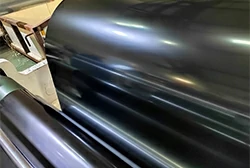
Production
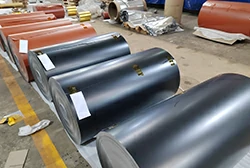
Finished Products
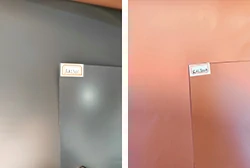
Color Comparison
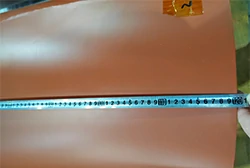
Width Measurement
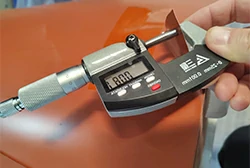
Thickness Measurement
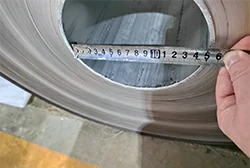
Core Measurement
Applications of 8079 coated aluminum foil in building insulation
Roof waterproofing projects
8079 color-coated aluminum foil, combined with asphalt, creates waterproof membranes ideal for roof and skylight waterproofing. It offers excellent waterproofing and superior weather resistance, making it essential for skylight projects.
Contact us now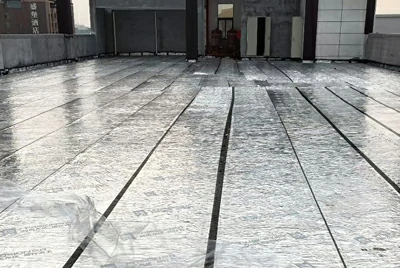
Specific applications of roof waterproofing
- Roof Waterproofing: Color coated aluminum foil can be laminated with asphalt materials to create waterproof membranes, suitable for new construction and roof repairs, especially for flat and pitched roofs.
- Basement Waterproofing: In addition to roofing, color coated aluminum foil asphalt waterproof membranes are also used in underground structures like basements and subways, ensuring moisture and waterproofing protection.
- Skylight Waterproofing: Combining color coated aluminum foil with waterproof membranes enhances water resistance and UV protection, offering additional waterproofing for skylights.
- Bridges and Tunnels: In special projects, color coated aluminum foil asphalt waterproof membranes are also used in bridges, tunnels, and other structures, particularly in high-moisture and high-water-pressure environments.
Advantages
- Superior Waterproofing: The composite material of asphalt and color coated aluminum foil provides excellent waterproofing, preventing moisture penetration around roofs and skylights.
- Strong Weather Resistance: The surface coating of color coated aluminum foil resists UV rays, acid rain, and harsh weather, maintaining stability and corrosion resistance over time.
- Thermal Reflectivity: The aluminum foil's excellent reflective properties help reduce heat absorption in the roof, lowering indoor temperatures and saving energy.
- High Tensile Strength: The material structure enhances tensile strength, resisting temperature fluctuations and external impacts to avoid cracking in the waterproof layer.
- Easy Installation: Flexible material that is easy to lay and cut, ideal for complex roof structures, reducing construction time and cost.
Roof waterproofing construction considerations
1. Substrate Treatment: Ensure that the roof substrate is clean, dry, and flat before installation, free from dust, oil, or debris, to ensure proper bonding and long-term stability of the waterproof membrane.
2. Installation Temperature: The ambient temperature should be above 5°C during installation. In cold environments, proper insulation measures should be taken to ensure the effective installation of the waterproof membrane.
3. Overlap Width: When laying the membrane, ensure the overlap meets design requirements, typically about 10 cm, to ensure tightness and waterproofing, preventing leaks.
4. Regular Inspections: While color coated aluminum foil asphalt waterproof membranes have a long lifespan, regular inspections and maintenance are necessary to detect potential issues like tears, aging, or water accumulation, ensuring the membrane's longevity.
Roof insulation system
Roofs are key areas for heat loss and gain. 8079 color-coated aluminum foil improves insulation with excellent thermal resistance, making it ideal for roof insulation and thermal barrier applications.
Contact us now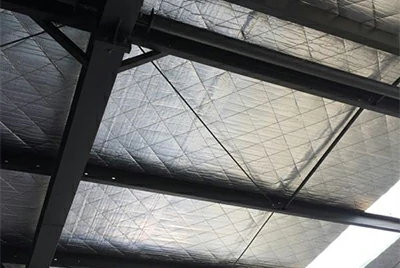
Advantages
Long-lasting Insulation: Prevents heat buildup on the roof, ensuring comfortable indoor temperatures, especially during summer, and reducing air conditioning usage.
Waterproofing: When used with other roofing materials, it enhances waterproofing, preventing moisture penetration and roof damage.
External wall insulation structures
Installing aluminum foil composite insulation on exterior walls provides excellent thermal insulation, reducing energy loss. 8079 color-coated aluminum foil is ideal for wall insulation due to its superior thermal performance and weather resistance.
Contact us now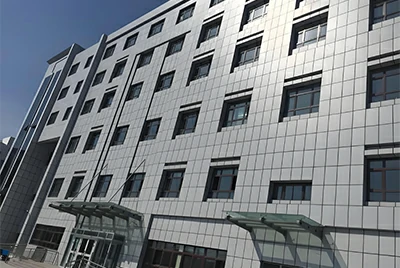
Advantages
High Weather Resistance: PVDF coating has exceptional UV and corrosion resistance, suitable for various climates, maintaining color and performance stability.
Improved Building Energy Efficiency: By reflecting heat and maintaining indoor temperatures, it reduces the load on air conditioning and heating systems, leading to lower energy consumption and reduced carbon emissions.
Indoor thermal insulation and soundproofing
In indoor environments, 8079 color coated aluminum foil not only offers excellent thermal insulation but also provides soundproofing benefits, making it ideal for spaces with specific temperature and noise requirements.
Contact us now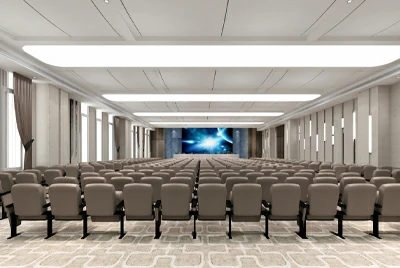
Specific Applications
Thermal Insulation and Soundproof Panels: Combine color coated aluminum foil with sound-absorbing materials (such as rock wool or fiberglass) to create insulation and soundproof panels for walls or ceilings, achieving both thermal insulation and soundproofing effects.
Interior Space Renovation: In environments requiring better indoor temperature control (such as meeting rooms, AV rooms, laboratories), use color coated aluminum foil to enhance the thermal and acoustic properties of walls and ceilings.
Advantages
Improved Living Comfort: Reduces heat and noise intrusion from the outside, improving indoor comfort.
Effective Energy Savings: By providing both thermal insulation and soundproofing, it reduces energy consumption from air conditioning and heating, saving on energy costs.
Kitchen fireproof and heat insulation
Kitchens, particularly in residential and commercial settings, are high-temperature and fire-prone areas, requiring strict fireproofing and heat insulation. 8079 color coated aluminum foil serves as a fireproof and heat-insulating protective material in kitchens, enhancing safety.
Contact us now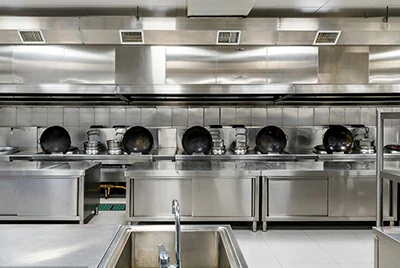
Advantages
Fireproof Heat Insulation: Aluminum foil has excellent high-temperature resistance, effectively blocking heat and preventing fires.
Corrosion Resistance: Kitchen environments are prone to grease and humidity, which can cause corrosion. The surface coating of color coated aluminum foil provides moisture and corrosion resistance, ensuring long-term use in humid environments.
Advantages of 8079 coated aluminum foil
Outstanding heat resistance and corrosion resistance
8079 aluminum foil, with low tensile strength and excellent ductility, is ideal for high heat and corrosion resistance applications. Coating improves weather and UV resistance, making it perfect for roof insulation and building facades, extending product lifespan.
Excellent thermal insulation and heat preservation performance
8079 color coated aluminum foil stands out in terms of thermal insulation and heat preservation performance. Whether used for building facades, roofs, or insulation systems, its efficient heat separation effect can effectively reduce energy loss and improve the energy efficiency of buildings. It is especially suitable for construction projects in regions with extreme temperatures, both hot and cold.
Customized coating options
8079 color-coated aluminum foil can be customized with various coatings, including PE (Polyester) and PVDF (Fluorocarbon). PE coatings offer UV protection and aesthetic appeal, ideal for indoor decoration and advertising. PVDF coatings provide stronger UV and pollution resistance, making them perfect for exterior walls and public buildings.
Moisture and corrosion resistance
Due to its protective coating, 8079 color coated aluminum foil demonstrates excellent moisture resistance and corrosion resistance, making it ideal for use in humid environments such as kitchens and industrial areas. It not only prevents moisture from penetrating but also effectively resists acidic, alkaline, and salty substances in the air.
Why choose Chalco: a guarantee of quality, technology, and service
1. Advanced Production Equipment and Technology
CHALCO uses imported equipment from Germany and internationally advanced technology to ensure that aluminum foil products meet European standards. Our production lines cover everything from ingot material to rolled products, with a maximum width of up to 1800mm and a minimum thickness of 0.006mm, catering to various application needs.
2. Strict Quality Control and Certifications
CHALCO is certified with ISO 9001 and ISO 14001, ensuring that product quality and environmental protection meet international standards. Our products are also certified by ROHS, REACH, FDA, and meet export packaging requirements, ensuring safe transportation.
3. Strong Production Capacity
The company operates four coating production lines with an annual production capacity of 50, 000 tons. We also possess the most advanced aluminum composite panel spraying line in China, with an annual output of 1 million square meters. Supporting equipment such as slitting machines, flying shear machines, and embossing machines enhances production efficiency.
4. Customized Services and Solutions
CHALCO offers customized aluminum products based on customer requirements, covering different coatings, sizes, and packaging needs to meet the demands of various industries. Additionally, the entire production process is traceable, ensuring reliable quality.
5. Technological Innovation and Research & Development
CHALCO continually invests in technology research and development to optimize product quality and performance. We provide market-leading aluminum foil solutions that help customers maintain a competitive edge.
6. Environmental Protection and Sustainability
The company strictly adheres to environmental standards, having obtained ISO 14001 certification, promotes green production, reduces environmental impact, and actively encourages resource recycling.
Are You Looking for an Aluminum Supplier?
If you need a professional aluminum supplier to provide you with high-quality, cost-effective aluminum, we will be your best choice.
Production process of 8079 color coated aluminum foil
1. Aluminum Foil Base Material Selection
First, high-quality aluminum alloys (such as 8079 aluminum foil) are selected and rolled into thin sheets to achieve the required thickness. The focus during this stage is on the flatness, thickness uniformity, and surface quality of the aluminum foil.
2. Surface Pre-Treatment
To ensure that the coating adheres well to the aluminum foil, the surface must be pre-treated. Common surface treatment methods include:
- Cleaning: Removing oils, dust, and other impurities from the aluminum foil surface.
- Chemical Etching: Using chemical reactions to roughen the surface of the aluminum foil, increasing its surface roughness and improving coating adhesion.
- Phosphating: Forming a phosphate film on the surface of the aluminum foil, further enhancing the adhesion of the coating.
3. Coating Application
Applying the coating to the aluminum foil surface is the core step in the production of color coated aluminum foil. The coating material is chosen according to the specific application requirements, with common coatings including PE (Polyester) and PVDF (Fluorocarbon) coatings. The coating methods generally include:
- Roll Coating: Applying the coating evenly across the surface of the aluminum foil, suitable for mass production.
- Spray Coating: Using a spray gun to apply the coating to the surface of the aluminum foil, suitable for fine craftsmanship and complex shapes.
4. Baking and Curing
After the coating is applied, the aluminum foil needs to be baked in an oven at high temperatures. Under these high temperatures, a chemical reaction occurs between the coating and the aluminum foil surface, forming a strong protective film. The baking temperature and time vary depending on the coating material.
- PE Coating: Typically baked at around 150°C for 10-15 minutes.
- PVDF Coating: Requires higher temperatures, usually around 200°C, with a baking time of 20 minutes.
5. Cooling and Cutting
After baking, the color-coated aluminum foil must cool naturally. Once the temperature lowers, it is slit into narrower widths as required. We can cut the aluminum foil into different widths and coil weights according to customer needs.
Purchasing guide for 8079 color coated aluminum foil
1. Alloy Selection
Common alloys used for building insulation and roof waterproofing include 8011, 8079, 1050, and 1200. Different alloys have distinct characteristics and should be chosen based on the specific application needs. For example, 8079 alloy is suitable for applications requiring higher strength and moisture resistance.
2. Coating Types
Color-coated aluminum foil coatings are divided into PE and PVDF types. PE is suitable for indoor use, offering good weatherability and decorative effects. On the other hand, PVDF is ideal for outdoor environments, with stronger UV resistance, acid-base resistance, and corrosion resistance. Choosing the right coating ensures long-term performance of the aluminum foil.
3. Key Indicators to Consider When Purchasing
- Coating Thickness: Choose the appropriate coating thickness according to specific needs. The front side generally requires a thicker coating to improve weatherability.
- Surface Gloss: Different gloss levels can be selected according to requirements. The standard gloss is 25±1-5, suitable for various decorative needs.
- Weather Resistance and UV Performance: Choose materials that adapt to environmental conditions to ensure that the aluminum foil will not fade, mold, or degrade during outdoor use.
- Mechanical Properties: This includes tensile strength, impact resistance, and scratch resistance. These properties determine the durability of the aluminum foil in practical use.
- Moisture and Heat Resistance: Ensure that the aluminum foil does not peel, bubble, or discolor in humid environments.
4. Environmental Adaptability
- Temperature and Humidity: Different coatings of color-coated aluminum foil have varying adaptability to temperature and humidity. Choose the appropriate coating based on the application environment.
- UV Exposure: Applications exposed to sunlight for extended periods require materials with strong UV resistance, such as PVDF coating.
- Acid-Base Environments: For applications like food packaging and chemical packaging, consider the material's acid-base resistance to ensure that it will not degrade due to chemical exposure.
5. Quality Control and Packaging
To ensure safety during transportation, 8079 color coated aluminum foil is typically packaged according to export standards. Packaging methods include packing with wooden pallets or in roll form. The packaging material needs to be moisture-resistant, impact-resistant, and ensure that the surface of the aluminum foil remains undamaged. Packaging sizes and methods can be customized according to customer requirements.
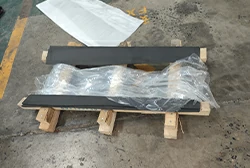
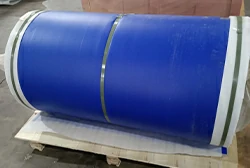
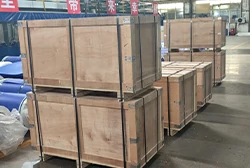