As a leading large-scale aerospace parts manufacturer, Chalco continues to provide high-quality, high-precision key components to the global aerospace industry with its rich experience and excellent technology.
Among Chalco's products, not only aluminum products are used in aerospace, but other alloys such as titanium alloys and nickel alloys are also widely used in aerospace.
Chalco's certificate
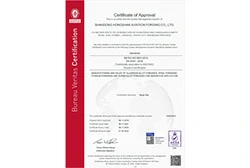
AS9100D quality management certification
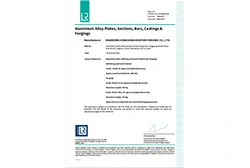
Lloyd's register certificate
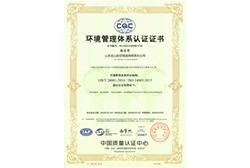
Environmental management system certification
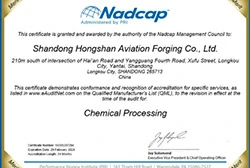
NADCAP chemical etching certificate
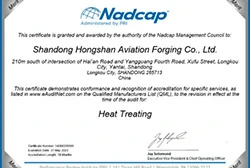
NADCAP heat treatment certification

NADCAP non-destructive testing certificate
Our main products
Chalco popular aviation aluminum forgings
Forged titanium alloy body frame
Alloy material: TA15, TA15-M
Maximum size: 2539×1571×148mm
Net projection area: 3㎡
Application: Helicopter fuselage frame.
Production process: Die forging
Contact us now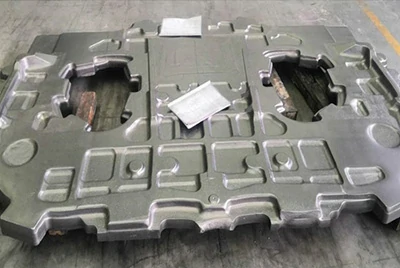
Wing support beam
Alloy material: TA15
Maximum size: 3702×451×310mm
Application: It is the main load-bearing component of the wing. A good wing spar can extend the service life of the wing.
Contact us now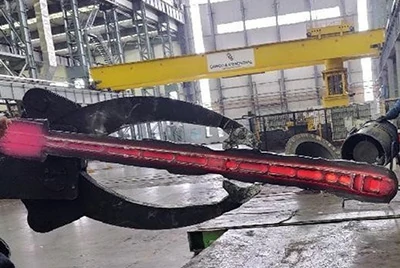
Fixed wing folding ribs
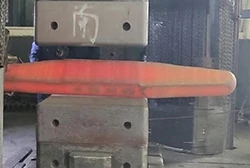
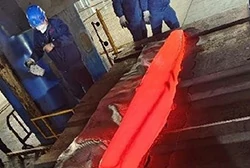
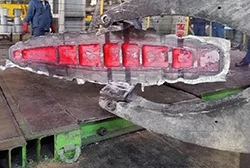
Wing folding ribs are foldable support structures inside the wing, mainly used to save space by folding the wings when the aircraft is parked or stored, and are commonly found in carrier-based aircraft.
Alloy material: TA15
Maximum size: 2986×450×265mm
Production process: Forging
Landing gear outer cylinder
The outer tube and inner tube (or piston) of the landing gear cooperate with each other and are extended and retracted through a hydraulic or pneumatic system to absorb and disperse the impact force when the aircraft lands, ensuring the smooth operation and structural integrity of the landing gear.
Material: A-100 steel, 300M steel
Maximum size: 2079×630×413mm
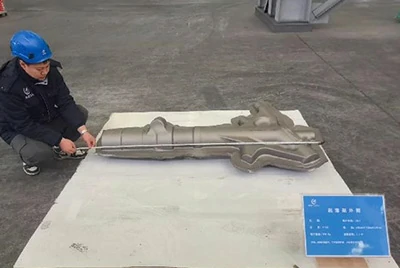
Aircraft landing gear wheel
The aircraft landing gear wheel hub is a key component made of 7075 or 2024 high-strength aluminum alloy through forging, CNC precision machining and heat treatment processes. It is used to support aircraft tires and withstand high-load operation.
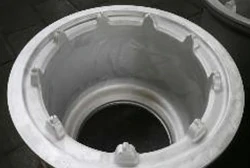
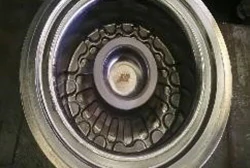
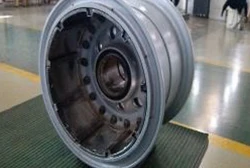
Aircraft landing gear side brace
The side struts of an aircraft are usually divided into two parts, upper and lower, connected by a hinge, called the upper side strut and the lower side strut. They are connected by a hinge point and jointly support the structure when the landing gear is deployed.
Alloy material: 7075 aluminum alloy
Boeing aircraft components
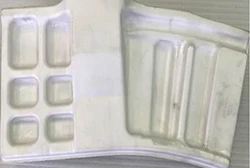
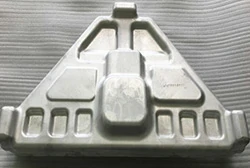
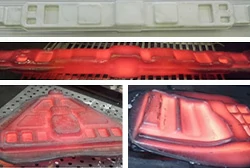
These aviation parts have passed Boeing's process verification and are Boeing's designated suppliers.
Product | Aluminum Alloy | Titanium Alloy | Aluminum Alloy Weight (kg) | Titanium Alloy Weight (kg) |
B01 | 7050-T74, T7452, T7454 | Ti6Al4V | 116 | 185 |
B03 | 7050-T74, T7452, T7454 | Ti6Al4V | 165 | 265 |
B05 | 7050-T74, T7452, T7454 | Ti6Al4V | 127 | 205 |
Inlet inner and outer panels
Product | Material | Dimensions (mm) |
Inner wall panel of air intake duct | 5A06-O Aluminum | 1450×892×396 |
Inner wall panel of air intake duct | 7050-T7452 Aluminum | 2006×1030×445 |
Outer wall panel of air intake duct | 7050-T7452 Aluminum | 2029×1025×408 |
The 5A06 aluminum alloy used for the inner and outer panels of the air intake provides good corrosion resistance and medium strength, while the 7050 aluminum alloy provides extremely high strength and excellent fatigue resistance.
Aircraft propeller blades and propeller hub
Propeller blades
Aircraft propeller blades are key components that convert engine rotational kinetic energy into thrust, and propel the aircraft forward through its aerodynamic design.
Aluminum alloy: 2A11
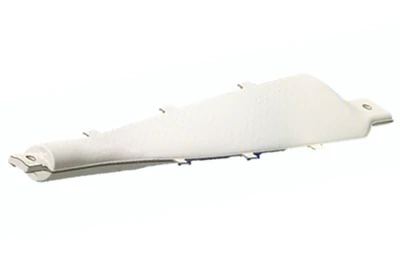
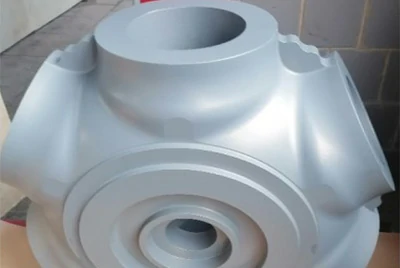
Propeller hub
The central component that connects the propeller blades and the engine, transferring the engine's power to the propeller blades.
Aluminum alloy: 2618
Contact us nowLow-pressure turbine rotor cone
The low-pressure turbine rotor cone is a key structural part of the low-pressure turbine rotor in a turbine engine, responsible for guiding the airflow and converting it into rotational kinetic energy.
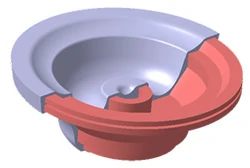
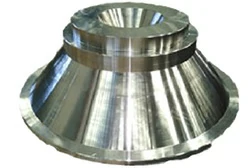
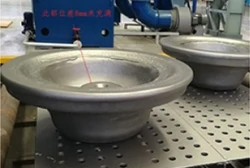
7050 head window frame and joint
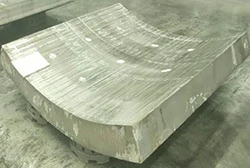
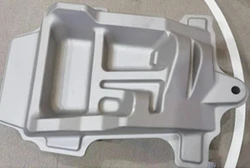
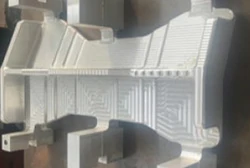
The specific alloy data are as follows:
Product | Material | Weight (kg) |
7050 nose side window frame | 7050-T7452 | 1764 |
7050 nose main window frame | 7050-T7452 | 1700 |
Main landing gear joint | 7050-T7452 | 90 |
Rear three-way joint | 7050-O | 191 |
Gas turbine disc
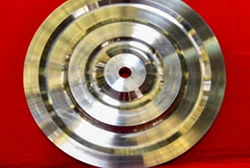
High pressure compressor first stage
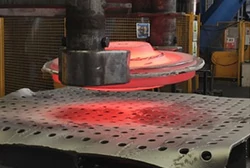
High pressure compressor spacer
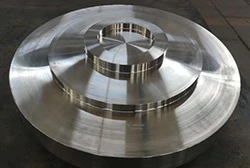
High pressure compressor three-stage plate
Discs (or rotor discs) are one of the key components in aircraft gas turbines. They are mainly used to support and fix turbine blades or compressor blades and transmit rotational motion to other components. Chalco is the only supplier of key disc shaft components to Rolls-Royce.
Product | Material | Dimensions (mm) | Weight (kg) |
High-Pressure Compressor Stage 1 Disc | In718 | Φ685*86 | 200 |
High-Pressure Compressor Spacer Disc | In718 | Φ669*111 | 128 |
High-Pressure Compressor Stage 3 Disc | In718 | Φ680*120 | 212 |
In aircraft gas turbines, Stage 1 Disc, Stage 2 Disc and Stage 4 Disc usually refer to different levels of compressor or turbine discs, and these discs play a specific role in different stages of the compressor or turbine.
- First-stage disc: Its function is to compress air or convert the energy of combustion gas, and its characteristic is to handle large air flow or high-temperature and high-pressure gas.
- Second-stage disc: Its function is to further compress air or convert energy, and its characteristic is to withstand medium pressure and load.
- Fourth-stage disc: Its function is to perform the final stage of compression or energy extraction, and its characteristic is to withstand the highest pressure and temperature.
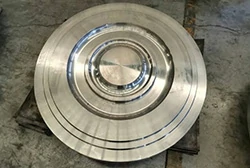
Stage 1 Disc
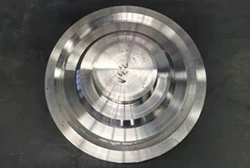
Stage 2 Disc
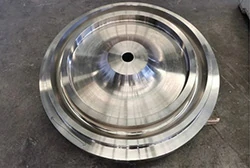
Stage 4 Disc
Disc product details
Product | Material | Dimensions (mm) | Weight (kg) |
Stage 1 Disc | IN718 | Φ1140×211 | 1452 |
Stage 2 Disc | IN718 | Φ1090×209 | 1395 |
Stage 4 Disc | IN718 | Φ1016×240.5 | 1220 |
Large titanium alloy impeller
Large titanium alloy impellers have excellent strength-to-weight ratio and corrosion resistance and are widely used in turbine engines and compressors in the aerospace field to provide efficient air compression and flow..
Product | Material | Dimensions (mm) | Weight (kg) |
Impeller | TC4 | Φ1860×635 | 8000 |
Other forging products
Chalco standard forging products
Chalco standard forging products such as forged aluminum bars, forged aluminum plates, forged aluminum rings, forged aluminum tubes and more.
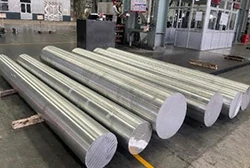
Forged aluminum bars
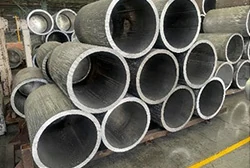
Forged aluminum tube
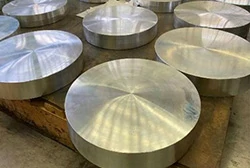
Forged aluminum cake
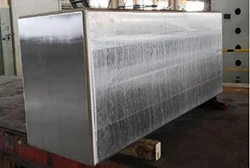
Forged aluminum block
Chalco irregular forging products
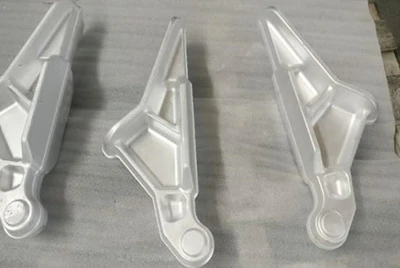
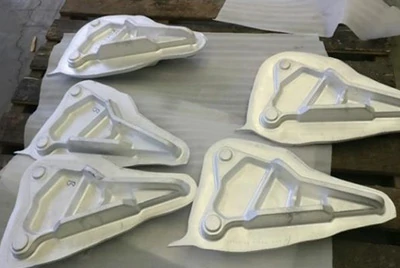
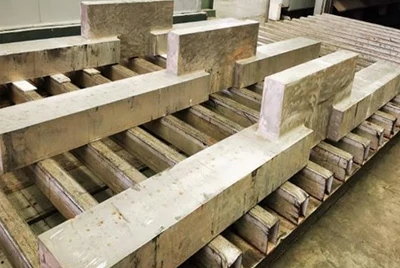
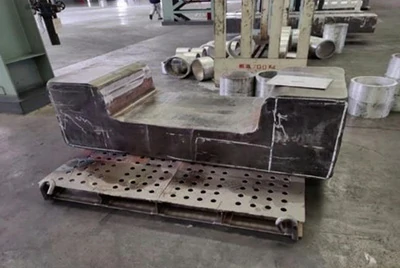
Advanced production equipment
We are able to produce large and high-quality forging products, mainly relying on our powerful production equipment, and the products we provide always surprise and satisfy our customers.
Large forging equipment
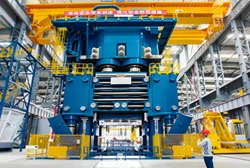
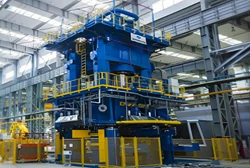
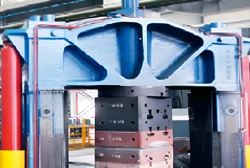
Our main forging equipment is imported from Germany. The key process parameters such as forging force, forging speed, and pressing position have achieved information-based, digital, controllable, and traceable intelligent management and control. The following are the specific parameters.
Nominal pressure (T) | 50000 | 12500 | 6000 | 2500 |
Stroke of moving beam (mm) | 2000 | 2000 | 3000 | 2000 |
Working table size (mm) | 4000×7000 | 2300×4000 | 2600×7000 | 1800×3500 |
Pressing speed (mm/s) | 0.05-50 | 0.05-50 | 0-50 | 0-50 |
Pressing speed control accuracy | ±5% | ±5% | ±5% | ±5% |
Forging supporting equipment
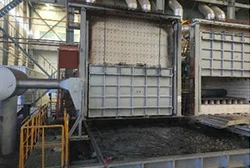
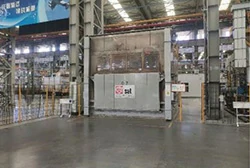
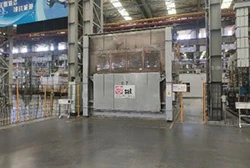
The forging supporting equipment are imported from Italy (2 sets), France (15 sets) and Belgium (11 sets), and there are also forging manipulators from Germany. The operating tonnage is 5-40T, the movements are sensitive and stable, and they have functions such as digital positioning and controllable moving speed. The implementation standards are GJB 904 and AMS 2750.
Manufacturer | Maximum qualified area per unit (m) | Maximum loading capacity per unit (tons) | Temperature control accuracy (°C) |
Italy | 7×3×1 | 80 | ±7 |
France | 5×3.5×1 | 40 | ±5 |
Belgium | 7×3×1.5 | 60 | ±5 |
Heat treatment equipment
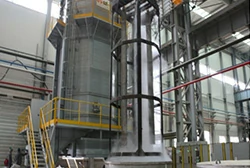
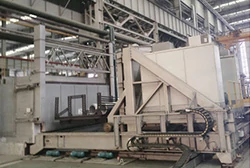
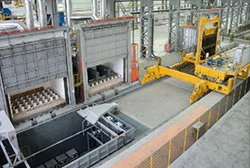
Chalco's heat treatment furnace has a maximum loading capacity of 40 tons and a temperature control accuracy of ±3°C.
Heat Treatment Furnace | Manufacturer | Quantity | Maximum Qualified Area (m) | Maximum Loading Capacity per Unit (tons) | Temperature Control Accuracy (°C) | Transfer Time (s) | Standard |
Titanium alloy/steel | Belgium | 2 | 3×3×1 | 5 | ±6 | / | GJB 904, AMS 2750 |
Titanium alloy/steel | Belgium | 3 | 3×5×1.5 | 40 | Two units: ±6, one unit: ±8 | / | GJB 904, AMS 2750 |
Aluminum alloy | France | 1 | Φ3×7 | 7.5 | ±3 | ≤9 | GJB 904, AMS 2750 |
Aluminum alloy | France | 2 | 5×3×1.2 | 5 | ±3 | ≤13 | GJB 904, AMS 2750 |
Metal cutting equipment
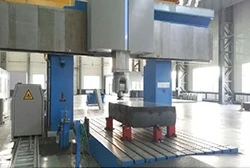
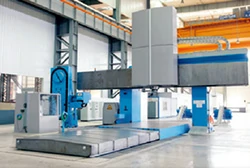
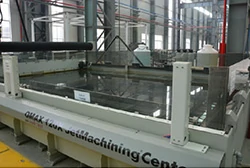
Chalco's metal cutting equipment can be up to 5 meters wide, 6 meters long, and has a maximum load capacity of 400 tons.
Equipment Name | Processing Capacity | Load Capacity |
3×6 Five-axis | 3 m X 6 m | 180 tons, 10 tons/m² |
5×8 Five-axis | 5 m X 8 m | 400 tons, 10 tons/m² |
Water cutting | 4 m X 6 m X 1 m | 1 ton/m² |
Special process equipment-flaw detection equipment
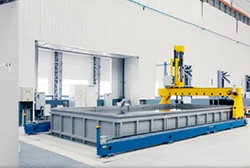
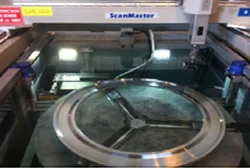
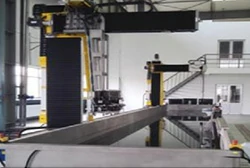
Chalco's water immersion ultrasonic flaw detection for disc shaft parts has been certified by Rolls-Royce and Shangfa.
Type | Measurement Size (mm) |
Water Immersion Testing (Structural Parts) | 7000 X 2500 X 1000 |
Water Immersion Testing (Discs and Rings) | Φ1500 |
Water Immersion Testing (Bars) | Φ100-Φ1050 X 6000 |
Special process equipment - etching, flaw detection, and testing equipment
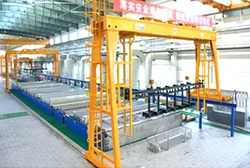
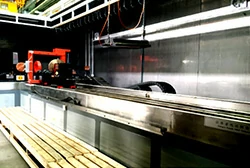
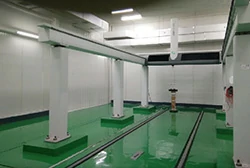
4 surface etching and cleaning lines can meet the surface treatment of aluminum alloy, titanium alloy, high-temperature alloy, high-strength steel and other materials, with the longest length up to 30m.
Equipment Name | Main Parameters (m) |
Chemical etching line | Maximum 30 |
Magnetic particle testing | Φ0.8×5.5 |
Coordinate measuring machine | 7×2.5×1.5 |
How can Chalco help you?
Customized machining services: Chalco provides precision machining services including forging, extrusion, heat treatment and surface treatment according to customer needs, ensuring that accessories precisely meet design requirements.
Technical support and material selection advice: Chalco's team of experts can provide customers with material selection, design optimization and manufacturing process advice to help customers improve product performance and reduce production costs.
High-quality aviation material supply: Chalco provides a wide range of aviation-grade aluminum alloys, titanium alloys and other high-performance metal materials to ensure that its products meet international aviation standards such as AMS and ASTM.
Quality testing and certification: Through advanced testing equipment and strict quality control system, Chalco provides a full range of product quality testing services to ensure that accessories meet the high standards of the aviation industry and can provide relevant certifications.
A wide variety of molds: There are many types of molds. If your product can match our existing molds, you can save mold opening costs.