Chalco aluminum filler rod product introduction
Alloy: 4043, 4047, 5356, 5556, 4643, 4943, 6061, 1050, 1100, etc. Click to view [Alloy Details]
Product categories: Aluminum TIG rod; Aluminum MIG solid wire; A RC Welding Rods; Other special filler material; Meet AWS A5.10, ISO standards and other standards
Welding Position: Flat; Horizontal; Overhead; Vertical-Down; Vertical-Up
Finish/Coating: Grey, Silver, White
Hot selling diameter: 0.035 inch; 0.045 inch (1.1 mm); 0.093 inch; 1/16 inch (1.6 mm); 1/8 inch (3.2 mm); 3/16 inch; 3/32 inch (2.4 mm); 3/64 inch; 5/32 inch
Click to view [Product size and performance reference table]
Packaging specifications: 1kg/roll, 2kg/2.5kg/5kg/box, 10 pieces/bundle, 1lb/10lb per tube, etc. (large or small packages of different specifications can be provided according to customer needs)
Chalco aluminum TIG rod
Common alloys: 1100, 4045, 4047, 5356, 5556, 4043
TIG welding rods are mainly used for tungsten inert gas welding (Tungsten Inert Gas Welding), and are often used for high-precision welding of aluminum and aluminum alloys.
Contact us now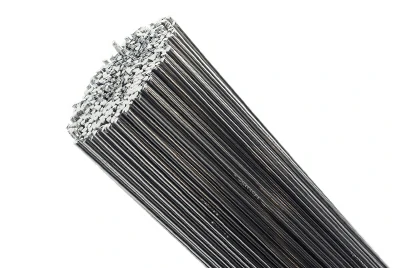
Chalco aluminum TIG rod product features:
- Pure aluminum welding rod (such as ER1100): used for welding pure aluminum substrates, with high corrosion resistance.
- Aluminum-silicon alloy welding rods (such as ER4045, ER4047): suitable for welding aluminum castings or scenes requiring low crack sensitivity.
- Aluminum-magnesium alloy welding rod (such as ER5356): used for welding aluminum alloy parts that require high strength or crack resistance.
Chalco aluminum TIG rod product advantages
- High Quality Welds: Aluminum TIG welding wire provides high quality, good penetration welds. This is important for applications where a strong, durable weld is required.
- Good Corrosion Resistance: Aluminum is known for its good corrosion resistance. This makes aluminum TIG welding rods ideal for applications where the weld is exposed to corrosive environments.
- Light Weight: Aluminum is a lightweight metal. This makes aluminum TIG welding rods ideal for applications where weight is critical.
Chalco aluminum TIG rod application areas
- Aerospace: welding aluminum structural parts or thin-walled tubes.
- Automobile industry: welding of radiators, fuel tanks and other components.
- Shipbuilding and rail transportation: welding of corrosion-resistant aluminum alloy parts.
Chalco aluminum MIG solid wire
Common alloys: 4043, 5356, 5183, 2319
Aluminium alloy solid wire for MIG welding (Metal Inert Gas Welding). MIG welding is a high speed and efficient aluminium welding method, often using this solid wire as a filler.
Contact us now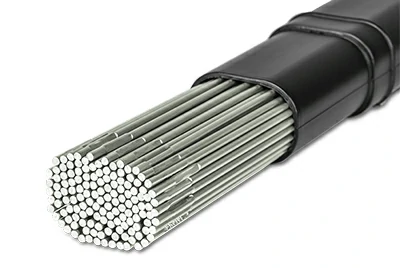
Chalco aluminum MIG rod product features:
- ER4043 (aluminum silicon alloy): widely used in welding 6XXX series aluminum alloys, with good crack resistance.
- ER5356 (aluminum-magnesium alloy): used for welding 5XXX series aluminum alloys, suitable for scenarios requiring higher strength and corrosion resistance.
Chalco aluminum MIG rod product advantages:
- High welding efficiency, suitable for large-scale production.
- Stable arc and weld quality.
Chalco aluminum MIG rod application areas:
- Construction industry: welding of aluminum alloy door and window frames.
- Shipbuilding: Welding of aluminum alloy components used in marine environments.
- Industrial Fabrication: Welding of aluminum tanks, pipes, and large structures.
Chalco aluminum arc welding rods
Common alloys: 4043, 5356, 4045, 4047
The welding rods specially designed for arc welding of aluminum and aluminum alloys have excellent crack resistance, corrosion resistance and welding stability, and can provide high-quality joint performance in a variety of welding environments.
Contact us now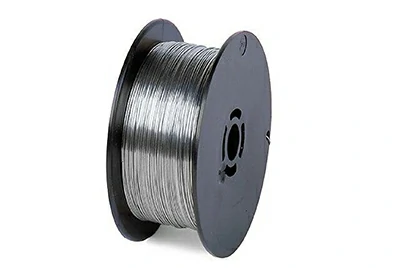
Chalco aluminum arc welding rod product features:
- ER4045: Suitable for welding cast aluminum and some aluminum alloys.
- ER5356: High strength, suitable for welding 5 series aluminum alloys.
- ER4043: Low melting point, good fluidity, suitable for welding 6 series aluminum alloys and some cast aluminum.
Chalco aluminum arc welding rod product advantages:
- Excellent melting performance: The electrode melts stably, the arc is easy to ignite and maintain, and is suitable for a variety of welding environments.
- Versatility: Suitable for different processes and welding conditions, can be used for welding in all positions (flat welding, vertical welding, overhead welding).
- Self-protection characteristics: The coating layer generates protective gas during the welding process to prevent weld oxidation and contamination, thereby ensuring welding quality.
- Superior mechanical properties: The weld has high strength and good ductility to meet the requirements of high stress structures.
- Corrosion resistance: The welds made with some special coated welding rods or alloy welding rods have excellent corrosion resistance and are suitable for harsh environments.
- Strong adaptability: Suitable for DC or AC power supply to meet the needs of different equipment and environments.
Chalco aluminum arc welding rod application areas:
- Construction engineering: welding steel structures, bridges and building frames, etc.
- Energy field: suitable for welding of oil and gas pipelines, power station boilers and pressure vessels.
- Shipbuilding and marine engineering: used for welding of hull structures, offshore platforms and marine equipment.
- Automotive industry: welding chassis, frames and key connecting parts.
- Nuclear industry: Special electrodes are used for welding nuclear reactor components, which require high strength, corrosion resistance and radiation resistance.
Other special filler material
Aluminum brazing rod
Common alloys: 4045, 4343
Made of 4045 and 4343 alloys, it offers low-temperature welding, high corrosion resistance, and is ideal for high thermal conductivity applications like air conditioners, radiators, and automotive pipelines.
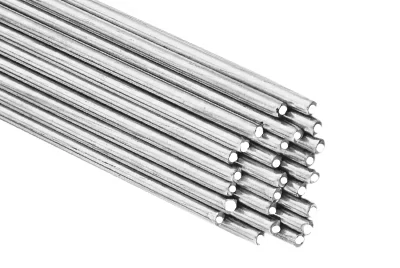
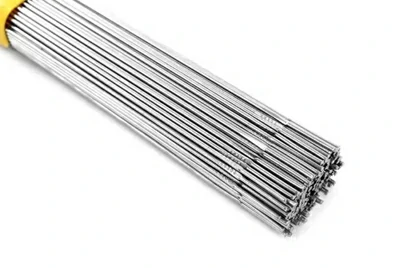
Low temperature welding rod
Ideal for low-temperature aluminum welding, it’s easy to use, requires minimal equipment, and is perfect for home repairs and light industrial applications.
Zirconiated tungsten for aluminum
Containing zirconia, it can provide arc stability and precision welding performance, and is suitable for TIG welding of aluminum and aluminum alloys in aerospace, electronic equipment and precision manufacturing applications.
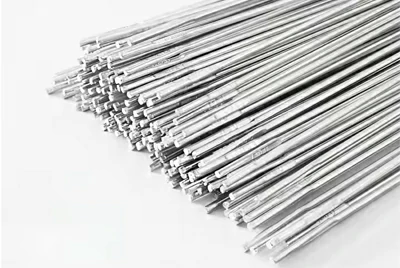
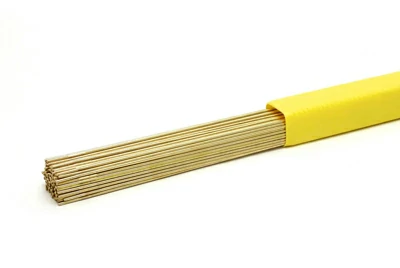
Aluminum gas welding rod
Common alloys: 1100, 4045
Gas welding aluminum rods are ideal for thin-walled plates, pipes, and simple structures, offering excellent plasticity and ductility for maintenance and high-toughness applications.
Oxyacetylene welding filler rod
Common alloys: 1100, 4045, 4047
Designed for oxyacetylene welding, it suits industrial applications. The 1100 alloy offers excellent corrosion resistance, while 4045 and 4047 alloys are favored for casting and repair due to their low melting point and good filling properties.
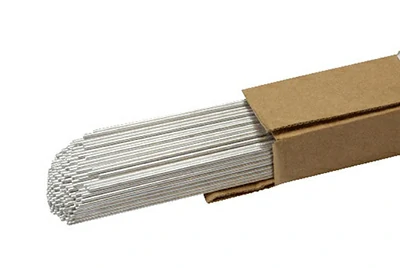
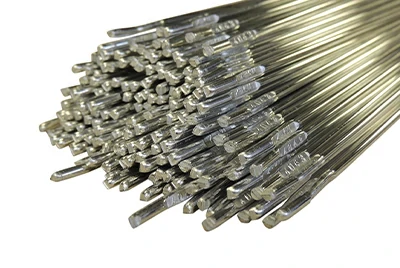
Flux-Cored Wire
Commonly alloys:5356, 5183, 4043
Flux-cored aluminum welding wire requires no shielding gas, reducing spatter and improving efficiency. It is widely used in shipbuilding, construction, and storage tank manufacturing.
Aluminum bronze tig rod
It has high strength, wear resistance and corrosion resistance, and is suitable for welding copper and aluminum dissimilar metal joints, repair and processing of marine equipment and heavy machinery parts.
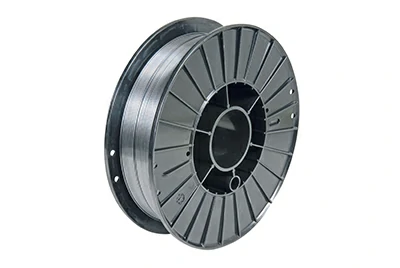
Other materials welding rod
In order to meet the needs of different materials and application scenarios, we provide a wide variety of welding materials, which can be customized according to the parent material properties, welding process and joint requirements to ensure the strength, ductility and corrosion resistance of the welded joint. In addition to aluminum alloy welding rods, if you need other alloy welding materials such as copper and steel, please feel free to contact our sales staff. Quick Quote
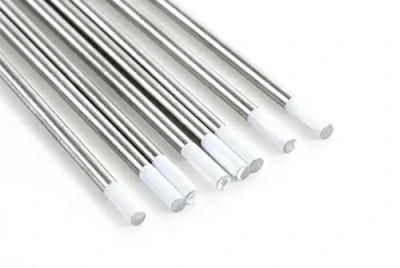
Stainless Steel TIG Welding Rods
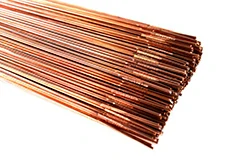
Mild Steel TIG Welding Rods
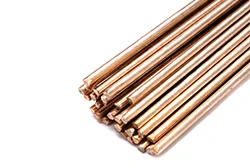
Bronze TIG Welding Rods
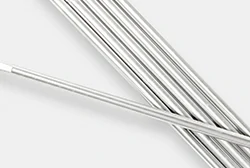
Nickel Alloy TIG Welding Rods
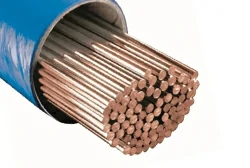
Copper TIG Welding Rods
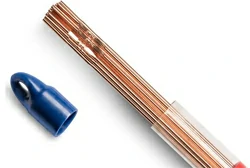
Alloy Steel TIG Welding Rods
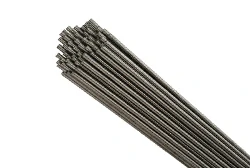
Titanium TIG Welding Rods
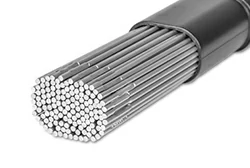
Cast Iron TIG Welding Rods
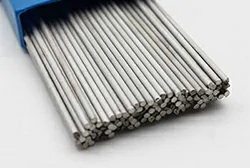
Magnesium TIG welding rods
Choose aluminum filler rod by aluminum alloy grade
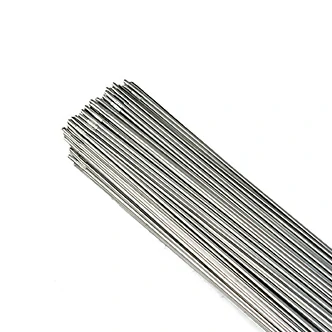
ER4043/ R4043 aluminum filler rod
ER4043 is a general-purpose aluminum TIG wire with silicon additives, offering good fluidity, crack resistance, and bright welds. It suits 6000 series alloys, supports heat treatment, and has higher tensile strength than ER5356.
Applicable welding positions: flat welding; horizontal welding; overhead welding; vertical welding downward; vertical welding upward
Tensile Strength (minimum requirement): 29 ksi
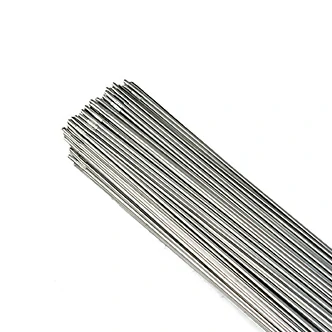
ER 5356 aluminum filler rod
ER5356 electrodes are popular aluminum TIG electrodes for general welding, ideal for 5000 series alloys and not heat treatable.
Applicable welding positions: flat welding; horizontal welding; overhead welding; vertical welding downward; vertical welding upward
Tensile Strength (minimum requirement): 38 ksi
-
4047 aluminum filler rod
High silicon content, good fluidity, suitable for reducing thermal cracking.
-
4145 aluminum filler rod
High strength and corrosion resistance, suitable for aviation and automotive industries.
-
4943 aluminum filler rod
High strength and good toughness, suitable for structural welding.
-
5183 aluminum filler rod
Excellent corrosion resistance for marine and tank applications.
-
5554 aluminum filler rod
It has strong crack resistance and is specially used for welding chemical storage tanks and pipelines.
-
5556 aluminum filler rod
High strength and wear resistance, suitable for highly loaded structures.
-
6061 aluminum filler rod
Easy to weld, widely used in general engineering fields.
-
6063 aluminum filler rod
It has excellent processing properties and is suitable for decorative and structural purposes.
-
1100 aluminum filler rod
Pure aluminum, soft and corrosion-resistant, suitable for low-strength welding.
-
1050 aluminum filler rod
High purity, good conductivity and corrosion resistance, suitable for welding with low strength requirements.
-
4009 aluminum filler rod
Suitable for special welding needs in high temperature environments.
-
4008 aluminum filler rod
High strength, corrosion resistance, for special applications.
-
5654 aluminum filler rod
Specially designed for hydrogen storage tanks, with excellent corrosion resistance.
-
2319 aluminum filler rod
High-strength alloy specially used in aerospace and military fields.
-
4643 aluminum filler rod
High toughness and crack resistance, suitable for welding requiring high reliability.
Reference table: sizes and properties of Chalco aluminum filler rods
The following table lists the performance and parameters of the two most commonly used aluminum welding wires, ER4043 and ER5356, including typical welding current, voltage, welding speed, gas flow and other detailed information. If you need to know the performance parameters of other welding wires or have special requirements, please feel free to contact us!
4043 Aluminum filler material is a 5% silicon aluminum filler recommended for welding of 3003, 3004, 5052, 6061, 6063, and cast alloy such as 443, 355, 356 and 214.
Rod Diameter | Rod Length | Welding Current Designation | Tensile Strength (As Welded) | Series |
1/16 in | 36 in | DCEP | - | Super Glaze 4043 TIG |
1/16 in | 36 in | AC | 29 ksi | ER4043 |
3/32 in | 36 in | AC | 29 ksi | ER4043 |
3/32 in | 36 in | DCEP | - | Super Glaze 4043 TIG |
3/32 in | 36 in | AC | 29 ksi | ER4043 |
1/8 in | 36 in | AC | 29 ksi | ER4043 |
1/8 in | 36 in | DCEP | - | Super Glaze 4043 TIG |
1/8 in | 36 in | AC | 29 ksi | ER4043 |
5356 aluminum filler material is a 5% magnesium aluminum filler recommended for welding of 5050, 5052, 5083, 5356, 5454 and 5456.
Rod Diameter | Rod Length | Welding Current Designation | Tensile Strength (As Welded) | Yield Strength (As Welded) | Series |
1/16 in | 36 in | DCEP | 240 to 296 N/mm2 | 110 to 120 N/mm2 | Super Glaze 5356 TIG |
1/16 in | 36 in | AC | 38 ksi | Not Specified | ER5356 |
3/32 in | 36 in | DCEP | 240 to 296 N/mm2 | 110 to 120 N/mm2 | Super Glaze 5356 TIG |
3/32 in | 36 in | AC | 38 ksi | Not Specified | ER5356 |
1/8 in | 36 in | DCEP | 240 to 296 N/mm2 | 110 to 120 N/mm2 | Super Glaze 5356 TIG |
1/8 in | 36 in | AC | 38 ksi | Not Specified | ER5356 |
Knowledge center of welding and brazing
1. Chalco aluminum filler rod welding position
2. How to choose 4043 and 5356 filling rods
When welding 6XXX series aluminum or 5XXX series aluminum with less than 3% magnesium, 4043 and 5356 aluminum filler rods are both common choices. They both meet high shear strength requirements and provide excellent performance in most aluminum alloy welding applications. However, depending on the specific application requirements, they each have unique advantages in different scenarios.
4043 Aluminum Filler Rod is suitable for the following applications:
- It has excellent high temperature crack resistance when exposed to high temperature environment for a long time (above 150°F).
- Applications that wish to reduce the risk of termination and shrinkage cracking, provide more stable welds and reduce welding defects.
- Welding tasks that require high weld aesthetics can produce bright and clean weld appearance.
- Workpieces that are particularly sensitive to welding deformation can minimize the deformation problems caused by welding.
5356 Aluminum Filler Rod is suitable for the following applications:
- When welding 5XXX or 6XXX series aluminum, higher tensile strengths can be achieved for high strength requirements.
- The base material after anodizing treatment needs to have a good color match, and the weld should have excellent color consistency with the base material.
- In application scenarios that withstand dynamic loads, it provides higher ductility and toughness to ensure the reliability of the welded structure.
- In connection situations where higher shear strength is required, only one welding is required to achieve higher shear strength.
Classification | 4043 Aluminum Filler Rod | 5356 Aluminum Filler Rod | General scenarios |
Applicable Materials | 6XXX aluminum, 5XXX aluminum with less than 3% magnesium | 5XXX Aluminum, 6XXX Aluminum | 6XXX aluminum, 5XXX aluminum with less than 3% magnesium |
High temperature resistance | Suitable for high temperature environments (>150°F) | Not suitable for long-term high temperature environment | - |
Crack resistance | Reduced risk of termination and shrinkage cracking | - | - |
Weld seam aesthetics | Bright and clean welds | Good anodizing color matching | - |
Deformation resistance | Minimize welding deformation problems | - | - |
tensile strength | - | High tensile strength, suitable for high strength requirements | - |
Ductility and toughness | - | High ductility and toughness, suitable for structures subjected to dynamic loads | - |
Shear Strength | Multi-layer welding for high shear strength | High shear strength can be achieved with single-layer welding | For high shear strength requirements, both can be selected, but 5356 is more efficient |
Welding efficiency | Multi-layer welding to achieve high-strength connection | A single layer of welding can meet most strength requirements | - |
3. How to choose welding materials correctly
Material | Typical properties | Recommended application scenarios | Applicable process | Soldering temperature range (°C) |
Steel | High strength, low cost, good wear resistance; suitable for processing rusty or oxidized materials; wide range of applications. | Structural manufacturing: general machinery manufacturing and repair. | TIG welding, oxyacetylene welding | 1300–1500 |
Building: Steel frame structure. | ||||
Vehicles: welding of automotive parts. | ||||
Copper | It has excellent thermal conductivity and good corrosion resistance, and is suitable for connecting different metals (such as copper and copper, copper and brass). | Plumbing system: such as hot water pipes or cold-water pipe connections. | Silver brazing (15% or 2% silver copper brazing filler metal), oxyacetylene welding | 645–820 (Silver Brazing) |
Electrical equipment: used for the connection of electrical components. | ~1083 (copper melting point, close to welding) | |||
Silver | Low melting point, high fluidity, strong corrosion resistance; suitable for parts requiring high strength, precise fit, and beautiful weld appearance. | Precision manufacturing: HVAC, refrigeration equipment, marine equipment and other parts that require high sealing performance. | Silver brazing (45% silver brazing filler metal) | 640–680 |
Craft decoration: welding of metal products. | ||||
Aluminum | It is light in weight and has good electrical and thermal conductivity, but it requires high welding technology; high thermal conductivity means that heat input needs to be strictly controlled to avoid overheating or insufficient fusion. | Aerospace: aircraft parts and structural parts. | TIG welding (such as 5356 electrode), oxyacetylene welding (rare), argon arc welding | 600–660 (close to the melting point of aluminum alloy) |
Shipbuilding: welding of lightweight components. | ||||
Daily necessities: aluminum product repair. |
4. How to properly store and handle aluminum filler metal?
Proper storage and handling of aluminum filler metal is critical to ensure optimal welding results. Filler metal should be kept in a dry, clean area with an ambient temperature similar to that of the welding room. Avoid moving it directly from a cold area to a warm area, which can cause condensation on the surface and affect the quality of the weld. If the aluminum wire reel is not in use, it should be wrapped in a plastic bag or other protective cover to avoid the ingress of dust and debris. It is best to store TIG cut lengths of wire in the original box for safekeeping.
5. How to get the best welding results?
When welding aluminum or other metals, speed and weld integrity are equally important. To achieve the best welding performance, you should first understand the basic characteristics and selection criteria of filler metals. Especially for beginners, you can become familiar with the handling characteristics of aluminum filler metals by practicing and using welding scraps. If you need more help or professional advice, it is very useful to seek technical support from your local welding dealer or filler metal manufacturer.
6. When welding, what equipment should be paid attention to?
To ensure a smooth welding process, in addition to the correct selection and storage of aluminum filler metal, suitable welding equipment is also required, including:
- Spool Gun or Push-Pull Gun: Suitable for MIG welding process to ensure steady feed of aluminum filler metal.
- U-groove drive roller: prevents wire from being pinched or compressed, ensuring smooth wire feeding.
- Nylon Inlet Tube and Liner: Reduces friction and reduces debris accumulation.
- Aluminum Wire Contact Tip: Specially designed contact tip with slightly larger aperture to accommodate aluminum filler metal, ensuring smooth wire feeding and maintaining a stable arc.
These equipment can greatly improve welding efficiency and ensure good welding quality.