Aluminum finned tubes are efficient heat exchanger components made up of a base tube and extended aluminum fins. Their design aims to enhance heat dissipation or absorption efficiency by increasing the outer surface area.Welcome to contact
Aluminum finned tubes are commonly manufactured using processes such as extrusion, rolling, or winding. The choice of production method determines the performance and specific applications of the finned tubes. Overall, these tubes are suitable for applications requiring efficient heat conduction and weight reduction, such as evaporators, condensers, and heat exchangers.
Jump to >>> | Extruded aluminum fins | Mono-aluminum finned tubes | HFW finned tubes | Longitudinal finned tubes | Tension wound finned tubes | Aluminum embedded fin tube | Tension wound finned tubes |
You might be interested:
Chalco's most popular aluminum finned tubes
Extruded aluminum fins
Extruded finned tubes, also known as bimetallic finned tubes, are produced by applying high pressure to extrude aluminum around the outer surface of the base tube to form fins that tightly adhere to the tube. The fins are manufactured through cold processing, ensuring strength.
Spec: EN 10204
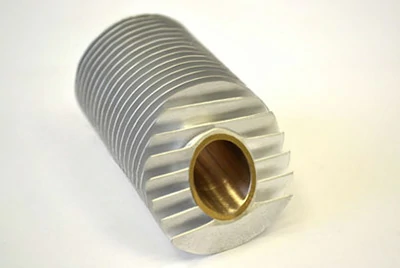
Introduction of extruded aluminum fin tubes
Base tube | Base tube material | Stainless steel, carbon steel, alloy steel, titanium, copper, duplex stainless steel |
Base tube outer diameter | 1/2”-1-1/2” (12.7-38.1mm) | |
Base tube thickness | ≥1.5mm | |
Base tube length | 500-15000mm | |
Fin | Fin material | Aluminum, copper |
Fin height | 9.8-16mm | |
Fin thickness | 0.3-0.65mm (normally 0.3, 0.35, 0.4, 02.55, 0.6, 0.65mm) | |
Fin density | 5 FPI-11 FPI (197FPM-433FPM) | |
Fin tube | Fin tube outer diameter | ≤50.8mm (2”) |
Fin tube length | 500-15000mm + exposed length | |
Exposed end | Customized according to customer requirements |
Characteristics of extruded aluminum fin tubes
Features | Description |
Manufacturing process | Cold extrusion (screw extrusion) |
Fin and tube bonding | Excellent |
Heat transfer efficiency | Excellent |
Mechanical resistance | Excellent (can be frequently cleaned with high pressure jetting, reducing downtime and extending overall life) |
Corrosion resistance | Fins completely cover the base tube (except exposed ends) and provide excellent corrosion protection |
Temperature range | ≤300℃ |
Standard dimensions of extruded aluminum fin tubes
Tubes Diameter | Fins Diameter | Fins Spacing(Fin/inch) |
3/8″ (9.52 mm) | 1.1″ (28 mm) | 4 fpi (157 fin/m) |
5/8″ (15.9 mm) | 1 3/8″ (35 mm) | 5 fpi (197 fin/m) |
3/4″ (19 mm) | 1 1/2″ (38.1 mm) | 7 fpi (276 fin/m) |
7/8″ (22.2 mm) | 1 3/4″ (44.5 mm) | 8 fpi (315 fin/m) |
1″ (25.4 mm) | 1 7/8″ (47.6 mm) | 9 fpi (354 fin/m) |
1.05″ (26.7 mm) | 2″ (50.8 mm) | 10 fpi (393 fin/m) |
1.315″ (33.4 mm) | 2 1/4″ (57.2 mm) | 11 fpi (433 fin/m) |
1 1/2″ (38.1 mm) | 2.315″ (58.8 mm) | 14 fpi (551 fin/m) |
2"(50.8mm) | 2 1/2″ (63.5 mm) | 16 fpi (630 fin/m) |
Why use aluminum extruded finned tubes?
Aluminum extruded finned tubes offer excellent heat transfer performance and corrosion resistance, making them widely used in industrial applications. The manufacturing process securely bonds the fins to the inner tube, preventing loosening or breaking, and avoiding galvanic corrosion. The fins completely cover the tube, ensuring no accumulation of contaminants, and they can be easily cleaned at high pressure without deformation. Additionally, the fins have good vibration resistance and stable performance, making them suitable for weight-sensitive and demanding environments, offering great cost-effectiveness.Free samples
Best applications for aluminum extruded finned tubes
Extruded finned tubes are widely used in various industrial fields that require efficient heat transfer and corrosion resistance, particularly excelling in harsh environments. These tubes play a crucial role in refrigeration, heating, and chemical industries, including:
- Cooling Units: Used in cooling and air handling systems to enhance heat dissipation.
- Heating Devices: Ensure efficient heat transfer in heating equipment.
- Air/Wind-Cooled Radiators: Suitable for air fin coolers, air-cooled radiators, and heat exchangers, especially in harsh environments.
- Corrosive Environments: Widely applied in chemical plants, refineries, and natural gas processing facilities where corrosion is a concern.


Mono-aluminum finned tubes(Low Fin Tube)
Mono-aluminum finned tubes, also known as Low Fin Tubes, are a type of integral extruded finned tube without any inner tube. They are made from an aluminum tube that is entirely rolled. These tubes are suitable for ultra-lightweight heat exchangers that require a full aluminum structure with high weight requirements.
Spec: ASTM B404/B404M
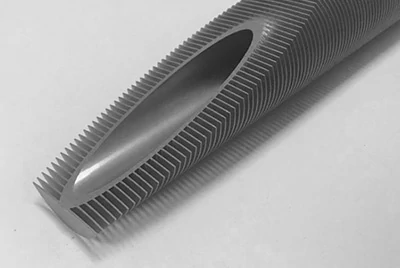
Introduction of Mono-aluminum finned tubes (Low Fin Tube)
Fin Tube | Material | Pure aluminum |
Alloy Grade | 1060, 3003, 5052, 5454, 6061 | |
Alcald Alloy Grade | Alcald3003, Alcald7072 | |
Fin Tube OD | ≤50.8mm(2”) | |
Fin Tube ID | 1/2”-1-1/2”(12.7-38.1mm) | |
Fin Tube Wall Thickness | 1.2-3.2mm | |
Fin Tube Length | ≤10m | |
Fin | Fin Height | ≤9.5mm |
Fin Thickness | 0.4mm | |
Fin Density | 5 FPI-11 FPI(197FPM-433FPM) |
The above provides an overview of our mono-aluminum finned tubes' specifications. Specific parameters can be customized according to your needs. Quick Quote
Applications of Mono-Aluminum Finned Tubes (Low Fin Tube)
- Viscous Fluid Cooling: Suitable for handling fluids with high viscosity, ensuring efficient heat dissipation.
- Heat Pipe Heat Recovery: Used in heat recovery systems to transfer and recover heat through heat pipes.
- Weight-Sensitive Applications: Ideal for applications where weight is a concern, such as in lightweight heat exchangers. The all-aluminum structure ensures the equipment remains lightweight.
High frequency welded finned tubes
High Frequency Welded Finned Tubes, abbreviated as HFW Finned Tubes, utilize specialized high-frequency welding technology for helical winding, typically divided into two types: HFW Solid Finned Tubes and HFW Serrated Finned Tubes.
Contact us now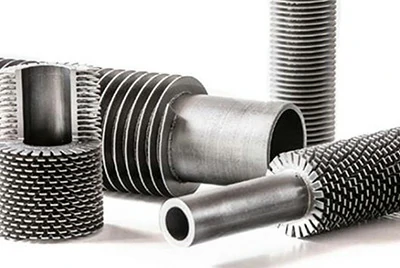
Introduction of High Frequency Welded Finned Tubes
HFW Solid Finned Tubes | HFW Serrated Finned Tubes | |
Welding process | GMAW | GMAW |
Pipe size | 1”-12.75” | 1”-12.75” |
Fin height | 1”-1 1/4” | 3/8”-1 1/4” |
Fin thickness | 0.035”-0.105” | 0.035”-0.06” |
Fin width | - | 5/32″- 5/16″ |
Fin spacing | 1FPI-7FPI | 1FPI-7FPI |
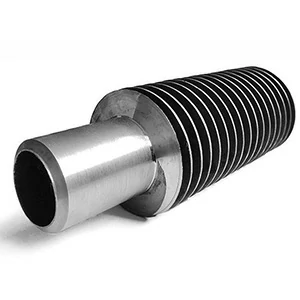
HFW Solid Finned Tubes
Welded helical solid finned tubes are created by helically winding fin strips and continuously welding them onto the tube surface, ensuring tight contact. This process uses gas-shielded metal arc welding for a strong connection and superior heat transfer performance. Even when using specialized tubing, the physical properties are almost unaffected. Solid finned tubes are suitable for any heat transfer application, especially in high-temperature and high-pressure environments. Their fin thickness is greater than that of serrated fins, making them the preferred choice in harsh conditions or when frequent cleaning is required due to potential oil fouling.
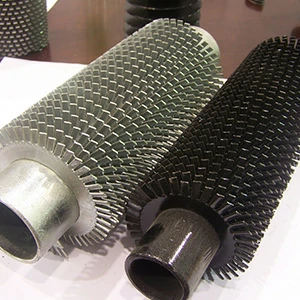
HFW Serrated Finned Tubes
Welded helical serrated finned tubes are produced similarly to solid finned tubes, with the key difference being that the fin strips are pre-cut into a serrated shape before being wound around the pipe to ensure tight contact. The outer edges of the fin strips spread out like petals and are continuously welded to the pipe using gas metal arc welding. The serrated fin structure offers higher heat transfer efficiency than solid fins, allowing fluid to flow transversely (cross-fins) along the pipe axis, which helps increase turbulence, disrupt the thermal boundary layer, and enhance heat transfer efficiency.
Longitudinal finned tubes
Longitudinal finned tubes are heat exchange pipes where the fins are fixed along the length of the tube through resistance welding, making them suitable for high-temperature and high-pressure environments. The fins are typically U-shaped, with a number that is a multiple of four, welded in pairs to increase the heat exchange area.
Contact us now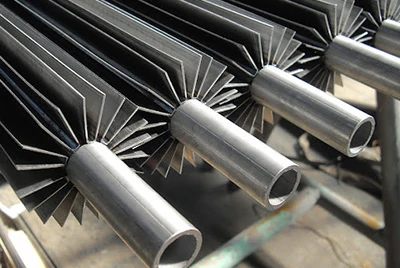
Introduction of longitudinal finned tube
Base tube | Base tube material | Stainless steel, carbon steel, alloy steel |
Base tube outer diameter | 3/4”-3” (19.05-76mm) | |
Base tube thickness | 2.0-6.0mm | |
Base tube length | ≤15000mm | |
Fin | Fin material | Aluminum (1100), stainless steel, carbon steel |
Fin height | 1/4”-1 1/4” (6.35-32mm) | |
Fin thickness | 0.8-1.2mm | |
Number of fins | 4-48 (common 4/8/16/24/32/48) |
Advantages of Longitudinal Finned Tubes
- Significantly Increased Heat Exchange Area: Compared to bare pipes, longitudinal finned tubes provide 8 to 12 times the heat transfer area, greatly enhancing heat exchange efficiency.
- Improved Thermal Conductivity: By increasing the fin area and fluid turbulence, longitudinal finned tubes are more efficient than bare pipes, especially in high-temperature and high-pressure environments.
- Space and Cost Savings: With improved heat transfer performance, heat exchangers can be designed smaller, making them a more economical choice.
- Customizable Design: Fins can be tailored with "cut and twist" treatments to enhance the turbulence of the shell-side fluid, further optimizing heat transfer.Solutions
Applications of Longitudinal Finned Tubes
Due to their outstanding heat exchange performance, longitudinal finned tubes are widely used in various industries. They are particularly suited for equipment that requires efficient heat transfer, such as heat exchangers, heaters, and coolers, meeting the needs of the petroleum, power, chemical, and petrochemical industries.
- Double-tube and multi-tube heat exchangers
- Flame heaters
- Gas coolers and heaters
- Tank heaters
- Petroleum, power, chemical, and petrochemical industries


Tension wound finned tubes
Tension wound finned tubes are formed by wrapping strips made of aluminum or copper around a tube under tension. This strip winding technology provides different types of fins: L-shaped fins, LL-shaped fins, and KL-shaped fins.
Contact us now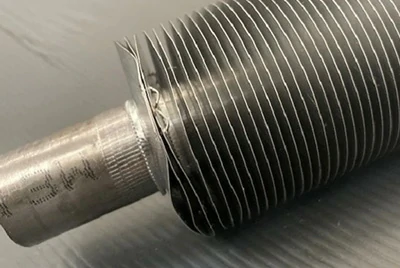
Tension wound finned tubes are widely accepted in applications where the heat transfer temperature is relatively low and cost control is necessary. Compared to "G”-type finned tubes and extruded finned tubes, this type of finned tube is relatively cost-effective.
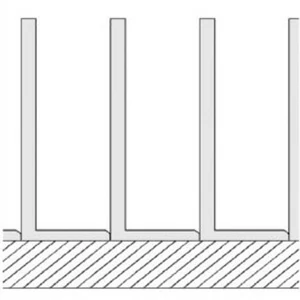
L Fin Tube(wrapped fin)
L-shaped fin tubes are an economical type of finned tube suitable for medium-temperature applications. They ensure maximum heat transfer efficiency and moderate corrosion protection by tightly spiraling the fin strips around the base tube. Commonly used in medium-temperature cooling applications.
Maximum Working Temperature: 150°C
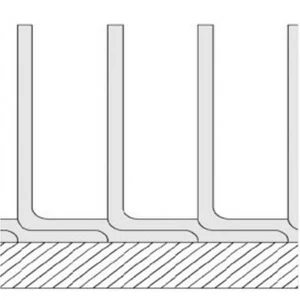
LL Fin Tube(Overlapped Fin)
LL-shaped fin tubes are a type of overlapped finned tube where the fin feet overlap during the winding process, completely wrapping the base tube and providing excellent corrosion resistance. Particularly suitable for applications requiring additional corrosion protection. It serves as a cost-effective alternative to extruded fins.
Maximum Working Temperature: 180°C
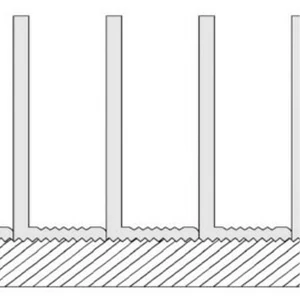
KL Fin Tube( Knurled L Fin)
KL-shaped fin tubes enhance the bond between the fins and the tube through a pre-knurled treatment on the base tube, improving heat transfer performance. Similar to L-shaped fin tubes, but due to the knurling treatment, they have better heat resistance, suitable for medium-temperature and moderate corrosion requirement applications.
Maximum Working Temperature: 260°C
Among the aforementioned types of wound-finned tubes, the fins are fixed through spiral tension, and the ends must be securely fastened together using mechanical bonding, brazing, or other methods. This design also allows for the use of a much thinner base tube, significantly reducing costs.Quick Quote
They are widely used in air-finned coolers, and radiators, and are the preferred choice in industries such as power generation, chemical industry, oil refineries, chemical processing plants, and rubber factories.
Aluminum embedded fin tube
Aluminum Embedded Fin Tubes, also known as 'G' Fin Tubes, are created by mechanically embedding aluminum fin strips into grooves on the tube wall, forming a strong mechanical bond capable of withstanding vibrations and high temperatures. They are ideal for high-temperature applications.
Spec:AEN 10204
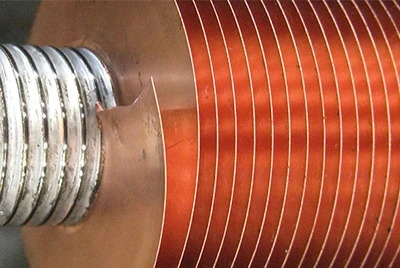
Introduce of Aluminum Embedded Fin Tube('G' Fin Tube)
Base tube | Base tube material | Stainless steel, carbon steel, alloy steel, titanium, copper, duplex stainless steel |
Base tube outer diameter | 1/2”-1-1/2” (12.7-38.1mm) | |
Base tube thickness | ≥2.11mm | |
Base tube length | 500-15000mm | |
Fin | Fin material | Aluminum (1100), copper, stainless steel |
Fin height | 9.8-16mm | |
Fin thickness | 0.3-0.65mm (normally 0.3, 0.35, 0.4, 02.55, 0.6, 0.65mm) | |
Fin density | 6 FPI-11 FPI (236 FPM-433 FPM) | |
Fin tube | Fin tube outer diameter | ≤50.8mm (2”) |
Fin tube length | 500-15000mm + exposed end length | |
Exposed end | Customized according to customer requirements |
Characteristics of Aluminum Embedded Fin Tube('G' Fin Tube)
Features | Description |
Manufacturing process | Slots are cut into the base tube and the fin stock is embedded |
Fin and tube bonding | Very good |
Heat transfer efficiency | Excellent |
Mechanical resistance | Very good |
Corrosion resistance | Medium |
Temperature range | ≤415℃ (withstands temperatures much higher than aluminum L-fin tubes) |
Best Applications for Aluminum Embedded Fin Tubes
Aluminum-embedded fin tubes ('G' Fin Tubes) excel in high-temperature applications, particularly in environments where temperatures may exceed 415°C. By embedding aluminum fin strips into the tube wall, they achieve excellent thermal transfer efficiency and mechanical strength, allowing them to withstand vibrations and thermal cycling. As a result, they are widely used in many industrial sectors.Fin tube experts
- Oil/Chemical Industry: Used to enhance thermal efficiency in chemical reaction processes, ensuring stable equipment operation at high temperatures.
- Natural Gas Processing: Ensures effective cooling and processing of natural gas in gas compression and cooling systems.
- Steel Industry: Suitable for blast furnaces and converter systems, improving thermal management during metal smelting processes.
- Power Plants: Utilized in fossil fuel and nuclear power plants for steam turbine exhaust condensation, enhancing energy recovery rates.
- Air Conditioning Systems: Suitable for cooling refrigerants like Freon, ammonia, and propane, ensuring efficient equipment operation.
- Municipal Waste Incineration Systems: Used to handle high-temperature flue gases, enhancing thermal efficiency during the incineration process.
- Compressor Coolers: Ensures that gases do not overheat during compression, extending equipment lifespan.


The high-temperature resistance and excellent thermal conduction properties of aluminum-embedded fin tubes ('G' Fin Tubes) make them an indispensable heat exchange solution across various industries.
Tension wound finned tubes
Tension wound finned tubes utilize a tension winding process to tightly wrap fins around the base tube, increasing contact area and enhancing heat transfer efficiency. The fin surface treatment promotes airflow turbulence, improving cooling performance, while the fin ends are welded to ensure stability.
Contact us now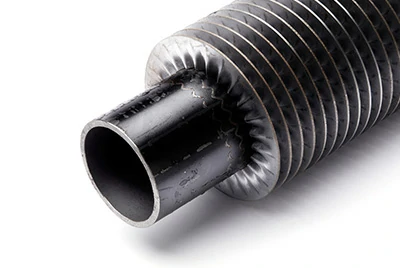
Introduction of tension wound finned tubes
Base tube | Base tube material | Stainless steel, carbon steel, alloy steel, titanium, copper, duplex stainless steel |
Base tube outer diameter | 1”-4” (25.4-101.6mm) | |
Base tube thickness | ≥2.11mm | |
Base tube length | 500-15000mm | |
Fin | Fin material | Aluminum (1100), stainless steel, carbon steel |
Fin height | 1/4”-1” (6.35-25.4mm) | |
Fin thickness | 0.15-2mm | |
Fin density | 3 FPI-11 FPI (118 FPM-433 FPM) | |
Fin tube | Fin tube outer diameter | ≤50.8mm (2”) |
Fin tube length | 500-15000mm + exposed end length | |
Exposed end | Customized according to customer requirements |
Characteristic of Tension wound finned tubes
Features | Description |
Manufacturing process | Spiral Stretch Wrap (Curled Fin Tube) |
Fin and tube bonding | Medium |
Heat transfer efficiency | Good |
Mechanical resistance | Very Good |
Corrosion resistance | Medium-Very Good |
Temperature range | ≤270℃ |
Applications of Tension Wound Finned Tubes
Tension wound finned tubes are widely used in various cooling systems, primarily for heat dissipation and extending equipment lifespan. They are commonly found in inverter coolers, custom radiators, air compressors, and hydraulic power systems, effectively dissipating heat and ensuring stable fluid temperature control and equipment operation.
- Inverter Coolers: Used to dissipate heat from engine water and thermal oil.
- Custom Radiators: Installed in tanks to cool closed-loop systems.
- Air Compressors: Provide cooling surfaces for the air in the compressor.
- Hydraulic Power Supply: Cool hydraulic oil to extend the lifespan of power sources.
Chalco's featured finned tubes
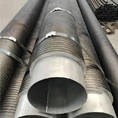
Large Diameter Finned Pipe
Large-diameter finned pipes are typically made from large-diameter steel tubes, although some specialized industries may use large-diameter aluminum finned pipes. They are widely used in industrial workshops, agricultural greenhouses, and food drying plants, offering excellent heat dissipation performance. Common diameters range from 2” to 6”, including solid and serrated high-frequency welded finned tubes.
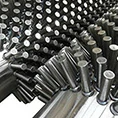
Nailhead Tube
Nailhead tubes, also known as stud tubes, are primarily used in heat exchangers within the petrochemical industry, suitable for environments resistant to gas and steam corrosion. The studs are fixed to the surface of the tube using resistance welding technology, and the arrangement of the studs can be adjusted according to specific requirements. Compared to finned tubes, nailhead tubes have higher mechanical strength, making them suitable for applications that require resistance to mechanical stress.
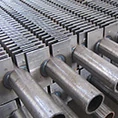
Rectangular H Fin Tube
Rectangular finned tubes, also known as H-type finned tubes, are commonly used in utility boilers, industrial boilers, and waste heat recovery systems. Their unique rectangular fin design effectively increases the heat transfer area, making them particularly suitable for dusty flue gas environments, such as economizers in coal, oil combustion equipment, or waste incinerators.
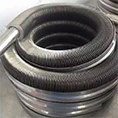
Finned Tube Coil
Finned tube coils increase the air contact area through fins, improving heat transfer efficiency, and can be bent into various shapes based on demand. They offer energy-saving, durability, and corrosion resistance, making them widely used in heat exchangers for direct cooling and heating applications.
Chalco finned tubes: efficient and reliable heat exchange systems
Chalco offers comprehensive finned tube solutions to meet the thermal exchange needs of various industries. Our finned tubes can be customized according to customer requirements, ensuring maximum efficiency for applications in industrial boilers, petrochemical equipment, and large heating systems. The lightweight aluminum alloy structure provides excellent durability and corrosion resistance, ensuring a long product lifespan. Our professional team supports the entire process, ensuring projects are delivered on time and meet customer needs.Solutions
- High-Efficiency Heat Transfer: Our finned tube designs not only provide a larger heat dissipation area but also optimize structural design to maximize heat transfer efficiency, making them suitable for long-term operation under high-intensity and complex conditions.
- Advanced Manufacturing Process: Chalco boasts innovative manufacturing processes and research capabilities, particularly our unique extruded fin technology, which maintains stable heat transfer performance in high-temperature and high-pressure environments.
- Flexibility and Customization: Based on your needs, we offer various materials, sizes, fin thicknesses, and shapes to ensure compatibility with any complex working conditions. Additionally, we support special processes such as U-bending, leak detectors, and the addition of flow disruptors.
- International Quality Standards: All finned tube products are certified by international standards such as SGS, ABS, LLOYDS, and MOODY, guaranteeing exceptional quality and reliability.
- Fast Delivery: With ample inventory and multiple high-performance fin machines, we can quickly respond to large-scale customization demands, ensuring production and delivery are completed in a short timeframe.
Chalco complete heat exchanger solutions: meeting your diverse heat exchange needs
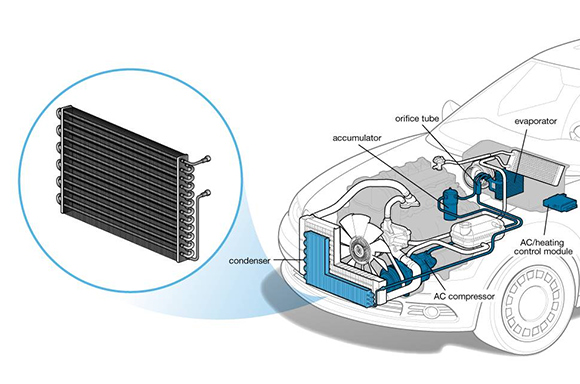
Aluminum Fin Stock
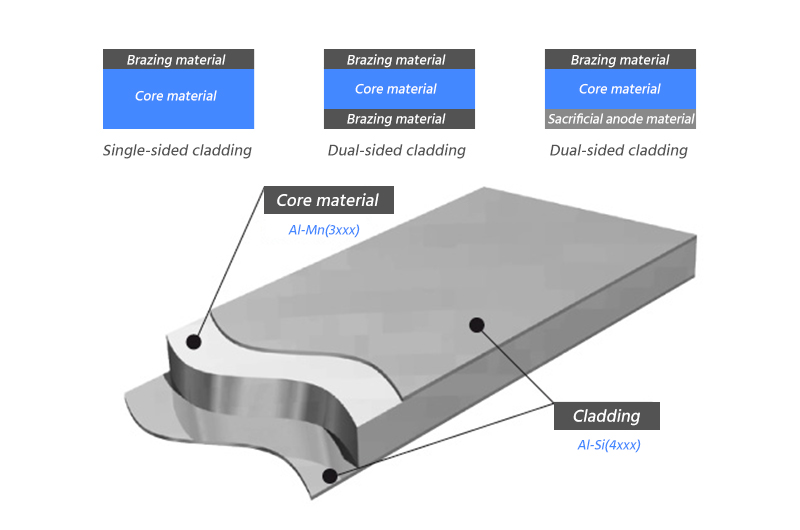
Aluminum Brazing Sheet
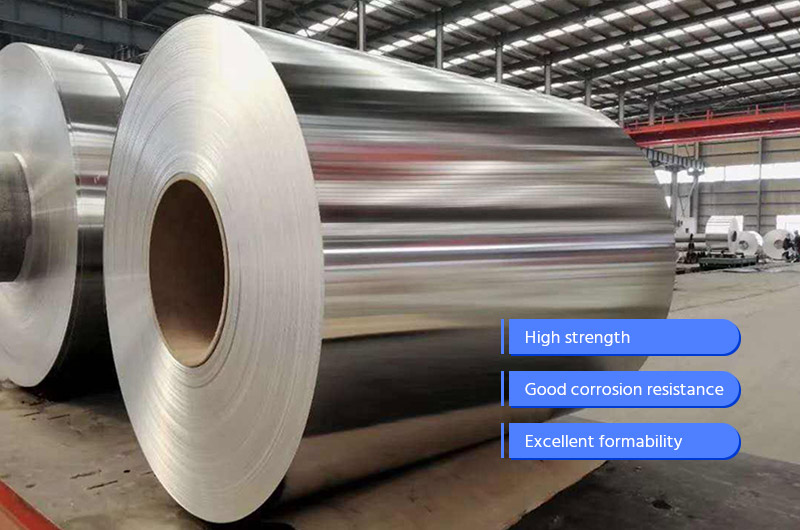
Aluminum Brazing Clad Coil
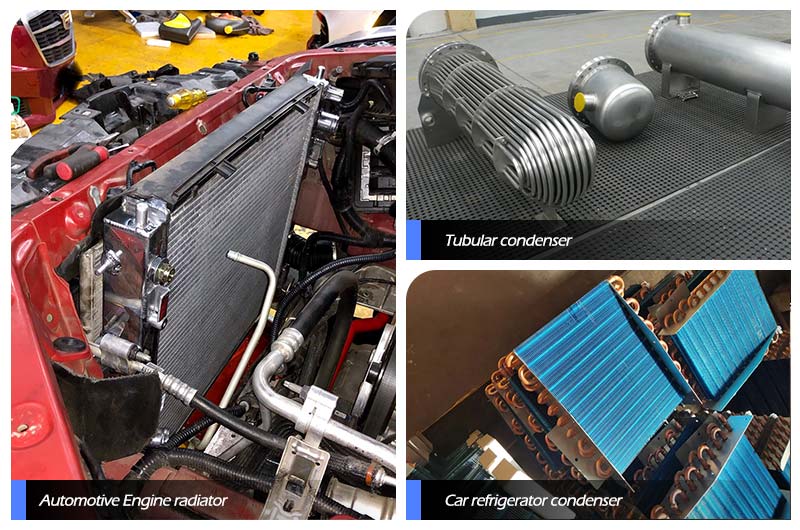
HF Welded Tubes
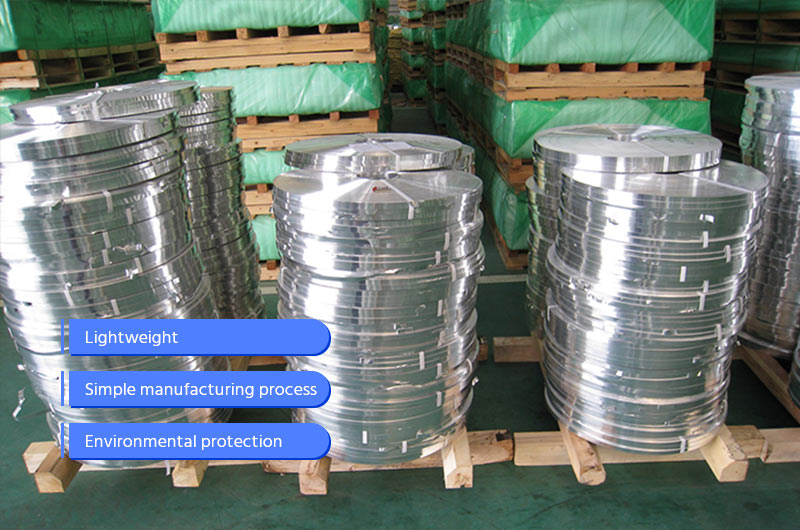
Non-clad Brazing Aluminum Strip
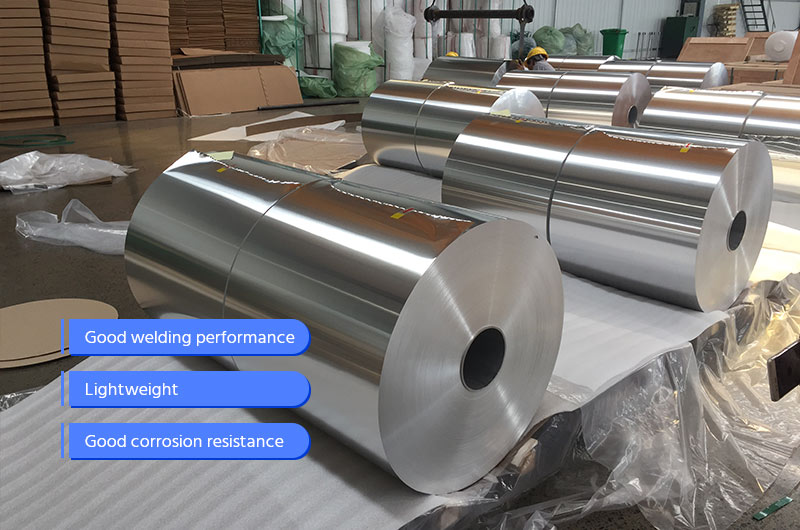
Aluminum Brazing Clad Foil
What information is needed to order chalco finned tubes?
Fluid Type:
- The fluid flowing inside the finned tube (e.g., air, water, glycol, heat-sensitive liquids).
- Pressure and Temperature.Quick Quote
- Maximum pressure and temperature inside the tube.
- Highest temperature outside the finned tube.
Environmental Conditions:
- The medium flowing around the finned tube (e.g., ambient air, fan cooling, combustion exhaust).
- Tube Specifications:
- Base tube dimensions: outer diameter (OD), wall thickness (WT), and length.
- Base tube materials: such as 316 stainless steel, 304 stainless steel, aluminum, carbon steel, copper, etc.
Fin Specifications:
- Fin materials (e.g., 316 stainless steel, 304 stainless steel, aluminum, carbon steel, copper, etc.).
- Fin types (e.g., solid fins, serrated fins).
- Fin height and thickness.
- Number of fins per inch or per meter (or fin spacing).
Length of Unfinned Sections:
Length of the unfinned portions at both ends of the base tube.
Quantity:
The number of finned tubes required.
Chalco can provide you the most comprehensive inventory of aluminum products and can also supply you customized products. Precise quotation will be provided within 24 hours.
Get a quote