In industrial manufacturing and pipeline engineering, flanges are key components that connect pipes, valves, pumps and various equipment, and are directly related to the sealing, safety and operating efficiency of the system. High-quality flanges not only ensure the stability of fluid transportation, but also facilitate the installation, maintenance and replacement of equipment.
Generally speaking, flanges can be divided into pipe flanges and structural flanges, which are used in fluid conveying systems and building and mechanical support structures respectively. In addition, Chalco's independently developed large-diameter flanges break through the traditional size limitations and can reach a diameter of 5-7 meters. They are suitable for large industrial equipment, marine engineering and wind power industries, providing safer and more efficient connection solutions and helping various industries to develop with high quality.
Chalco aluminum flange product parameters
Aluminum alloy: 7075, 6061, 5086, 5083, 3003, 1100
Other alloy materials: nickel alloy flanges, stainless steel flanges, stainless steel and super duplex steel flanges, chrome alloy flanges, titanium alloy flanges ... Please contact us for consultationContact
Nominal pipe sizes: NPS 1/2 ” to NPS 48 ” (DN15 to DN1200)
Flange face types: Flat Face (FF), Raised Face (RF), Ring Type Joint (RTJ), Concentric Serrated Face, Spiral Serrated Face
Flange surface treatment: stock finish, smooth surface, spiral serration, concentric serration, anodized [View details]
Specification:
- ASME standards: ASME B16.5, ASME B16.47 Type A, ASME B16.47 Type B, ANSI/ASME B16.1
- European standards: EN 1092-1, DIN 2633, UNI
- Japanese standard: JIS B2220
- Russian Standard: GOST 12820 / 12821-80
- Korean Standard: KS 1503
- South African Standards: SANS/SABS
Chalco aluminum flange patented product display
-
Large diameter aluminum flange
Chalco's large diameter flanges can reach 5-7 meters, and we continue to independently develop new technologies. We use forging, casting, cutting, rolling and other processes, equipped with large forging equipment, CNC machining centers and automatic welding systems to ensure high precision and excellent performance.
Chalco aluminum pipe flange hot selling products
Pipe flanges are used to connect pipes, valves and equipment to ensure sealing and pressure bearing capacity. Chalco uses a variety of processing technologies to ensure that the flanges have high strength, corrosion resistance and stable connection performance, providing safety protection.
Contact us now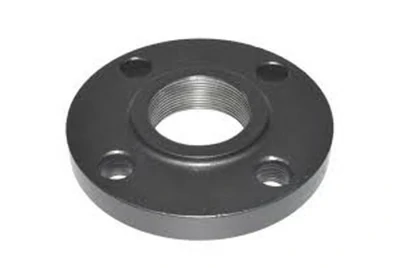
-
Ductwork flange
It is mainly used to connect ventilation, air conditioning, smoke exhaust and other air duct systems to ensure the sealing and stability of the air duct. It is usually used in combination with bolts or flange clamps to make the air duct connection more stable, while reducing air leakage and improving system efficiency.
-
Loose plate flanges
The flange is not directly welded to the pipe, but connected by flanging or welding ring. The flange can be rotated for easy installation and alignment. Click to view detailed[Size Parameters]
-
Slip-on flanges
The flange is placed on the outside of the pipe and welded on the inside and outside. It is suitable for low pressure and low temperature occasions and is easy to install. Applicable to: air, oil, water. Pressure level: 125; Click to view detailed[Size Parameters]
-
Butt weld flanges
Butt welding with pipeline, high connection strength, suitable for high pressure and high temperature occasions. Applicable to: air, oil, water ; pressure level: 125. Click to view detailed[Size Parameters]
-
Welding neck flanges
With high neck, it is butt-welded to the pipe and is suitable for high pressure and high temperature applications to reduce stress concentration.
-
Socket weld flange
The pipe is inserted into the inner hole of the flange and then welded. It is suitable for small diameter and high pressure pipes.
-
Blind flanges
A blind flange is essentially a solid plate or disc-shaped fitting used in vacuum systems. It can be machined to create custom fittings or to close off unused pipe sections or ports in a vacuum chamber. Click to view detailed[Size Parameters]
-
Threaded flanges
The inner hole is threaded and can be connected to the pipe with external thread without welding. It is suitable for low pressure and small diameter occasions. Click to view detailed[Size Parameters]
-
Collar flange
Used in conjunction with loose flanges, the pipe ends are flanging or welded with flanging rings, and the flanges are sleeved on them. Suitable for corrosive media.
Chalco aluminum structural flange hot selling products
Structural flanges are mainly used in buildings, mechanical supports and railing systems to fix and enhance stability. Chalco relies on precision manufacturing technology to provide high-strength, easy-to-install structural flanges to meet different engineering needs and ensure long-term stable use.
Contact us now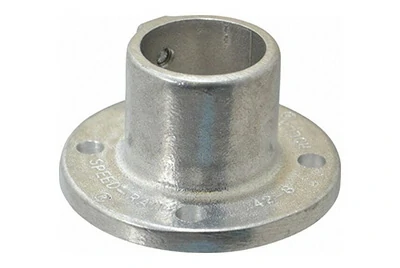
Wall flanges
Used to fix handrails or railings to the wall to ensure the stability and safety of the structure.
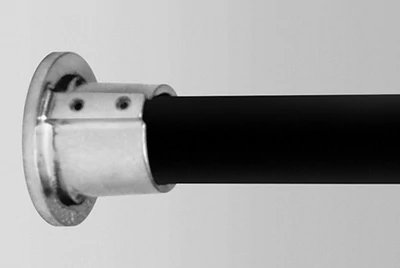
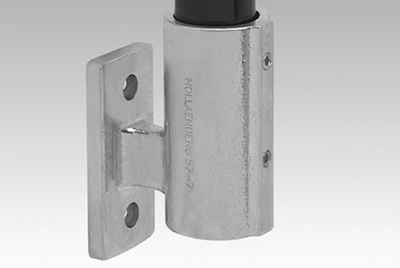
Floor flanges
Used to fix railing posts to the ground to provide vertical support. Commonly used in balconies, stairs and other areas.
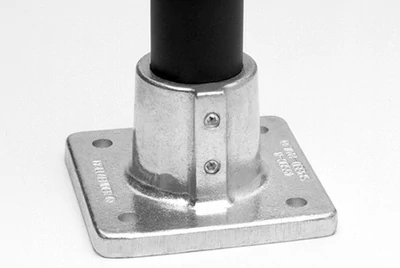
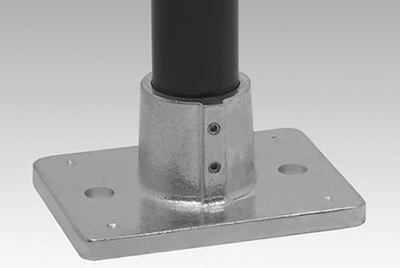
Angle flanges
Used to connect railings or handrails at a specific angle, often used at corners or slopes to ensure structural continuity and aesthetics.
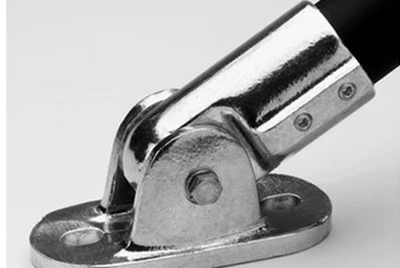
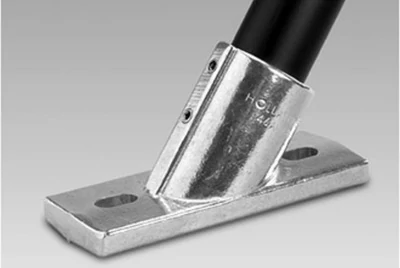
Railing flanges
Used to insert railings or handrails into flanges, providing a stable connection and ensuring the stability of the structure.
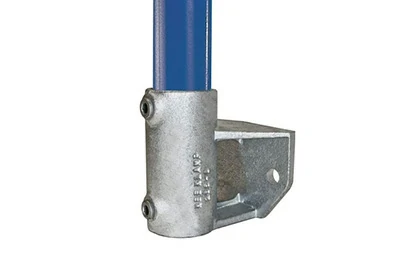
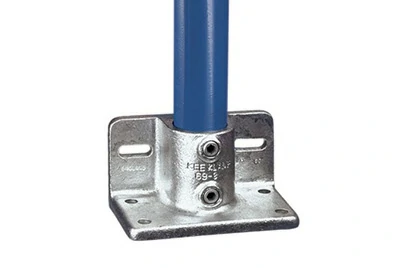
Cover flanges
Used to cover the connection parts, improve the overall aesthetics and provide protection.
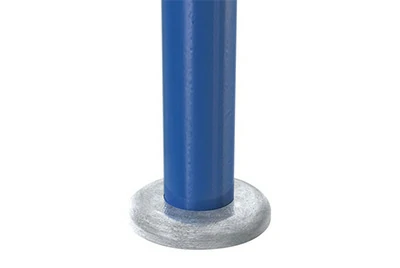
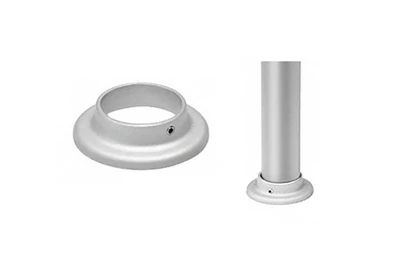
Hole flanges
Classified according to the number of bolt holes to meet different installation needs and load-bearing requirements.
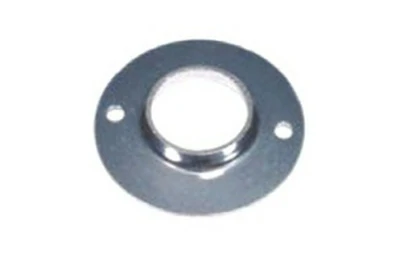
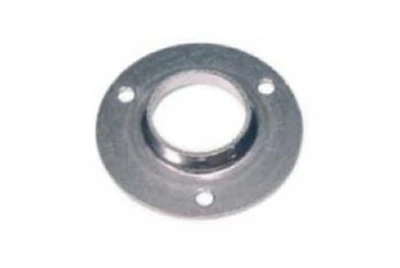
Chalco flange production and processing capabilities
Forged flange
Forged flanges are produced by applying high temperature and high pressure to metal blanks to cause them to undergo plastic deformation, thereby obtaining flange products with excellent mechanical properties. The flanges produced by this process have high strength and good impact resistance, and are suitable for high pressure and high temperature environments .
- Advanced forging equipment: Chalco has several large forging equipment that can produce forged flanges of various specifications to ensure the high strength and reliability of the products .
- Precision heat treatment process: The company is equipped with modern heat treatment facilities, which can perform precise heat treatment on forged flanges to optimize their mechanical properties.
Casting flange
Cast flanges are made by pouring molten metal into a prefabricated mold and forming it after cooling. This process is suitable for the production of flanges with complex shapes and has relatively low costs, but its mechanical properties are slightly inferior to forged flanges .
- High-precision casting technology: Chalco uses advanced casting technology to produce casting flanges with precise dimensions and smooth surface to meet the diverse needs of customers .
- Strict quality control: The company implements a comprehensive quality management system to ensure that the internal and external quality of the cast flanges meet international standards.
Milling or cutting flanges
Milling or cutting flanges are flange blanks that are cut directly from medium and thick plates and then machined. This process is suitable for the production of small and medium-sized flanges, with short production cycles and high flexibility .
- Precision CNC cutting equipment: The company has multiple CNC cutting machines that can efficiently and accurately cut flange blanks to ensure dimensional accuracy.
- Efficient processing capabilities: Chalco has strong machining capabilities, which can quickly complete the subsequent processing of cut flanges and shorten the delivery cycle.
Rolled flange
Rolled flanges are made by rolling a plate into a ring shape, then welding and processing it. This process is mostly used in the production of large flanges to meet the needs of special sizes and shapes.
More flange products
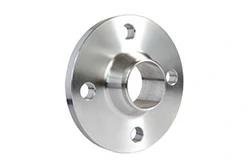
Weld neck flange
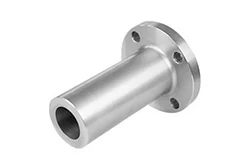
Long weld neck flange
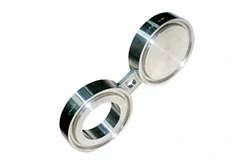
Spectacle blind flanges
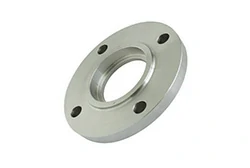
Socket weld flanges
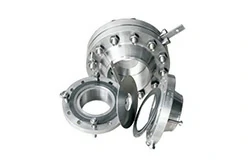
Orifice flanges
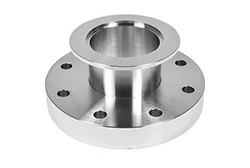
Lap joint flanges
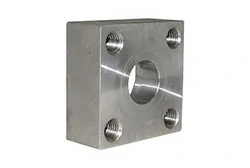
Square flanges
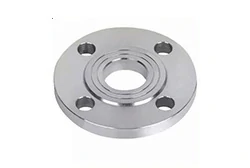
Ring type joint flanges
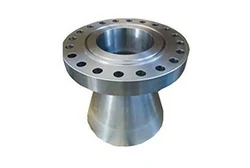
Expander flanges

Reducing flanges
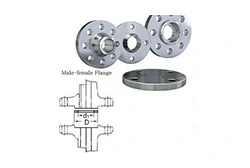
Male & female flanges
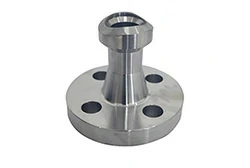
Weldolet flange
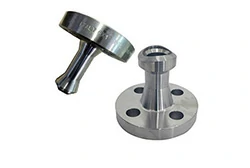
Nipolet flange
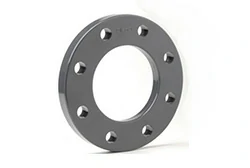
Backing ring flanges
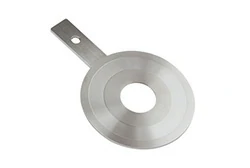
Ring spacer flanges
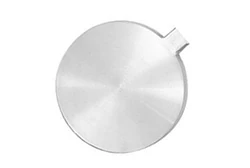
Paddle blind flanges
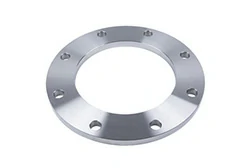
Plate flange
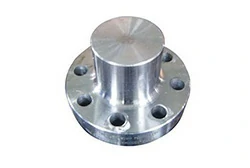
High hub blind flange
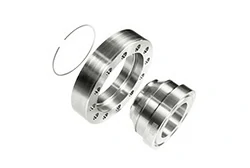
Swivel ring flange
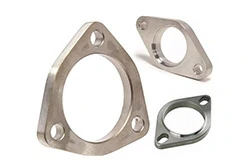
Exhaust flanges
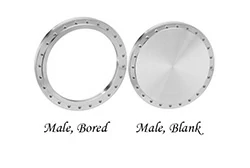
Wire seal flange
Chalco flange face types explained
Raised face flange (RF)
Raised face flanges (RF) are easily identifiable because the gasket surface area is above the flange bolt line. Raised face flanges are compatible with a wide range of flange gaskets, from flat face to semi-metallic and metallic types (e.g., jacketed and spiral wound gaskets), whether annular or full flat face.
Flat flange (FF)
The contact surface of a flat face flange (FF) is at the same height as the bolt line of the flange. A full-face gasket, usually a soft gasket, is used between two flat face flanges. According to ASME B31.3, a flat face flange should never be mated with a raised face flange because the resulting flange joint is certain to leak.
Ring joint flange (RTJ)
Ring Joint Flanges (RTJ) are used when a metal-to-metal seal between mating flanges is required (conditions for high pressure and high temperature applications, i.e. above 700/800 C°). Ring Joint Flanges have a circular groove that accommodates a Ring Joint Gasket (oval or rectangular ). RTJ flanges can be sealed by RTJ gaskets of different styles (R, RX, BX) and profiles (e.g. R style is octagonal/oval).
Lap flange
Lap joint flanges have flat faces that are not used to seal the flange joint, but simply carry the back side of the stub end. The sealing surface is actually on the stub end itself and can be either flat or convex.
Tongue and groove flange (T and G)
The two tongue-and-groove flanges (T&G faces) fit perfectly into each other: one flange has a raised ring, the other has a groove, and they fit together easily ( the tongue goes into the groove and seals the joint).
Inner and outer flanges (M and F)
Similar to tongue and groove flanges, the male and female flanges (M&F face type) also match each other. One flange has an area that extends beyond its face area, the male flange, and the other flange has a matching depression machined into the facing surface, the female flange. The female face is 3/16 inch deep, while the male face is 1/4 inch high, and both are smoothed. The outer diameter of the female face retains the gasket.
Chalco flange surface processing
Inventory complete
It is the most widely used of all flange finishes because it is suitable for virtually all common service conditions. Under compression, the soft face of the gasket will dig into this finish, which helps to form a seal and creates a high level of friction between the mating surfaces. The finish on these flanges is produced by a 1.6 mm radius round head tool at a feed rate of 0.8 mm per revolution up to size 12". For sizes 14 inches and larger, the finish is completed by a 3.2 mm round head tool at a feed rate of 1.2 mm per revolution .
Spiral sawtooth
This is also a continuous or phonograph spiral groove, but it differs from the original finish in that the groove is usually produced using a 90° tool, creating a "V" shaped geometry with 45° angle teeth.
Concentric sawtooth
As the name implies, this surface consists of concentric grooves. With a 90° tool, the teeth are evenly spaced across the surface.
Smooth surface
This surface finish has no visible tool marks. These finishes are commonly used on gaskets with metal surfaces such as double jackets, flat steel and corrugated metal. Smooth surfaces mate to form a seal and rely on the flatness of the opposing surfaces to achieve the seal. This is usually achieved by having the gasket contact surface formed by a continuous spiral groove formed by a rounded tool with a radius of 0.8 mm at a feed rate of 0.3 mm per revolution and a depth of 0.05 mm. This will result in a roughness between Ra 3.2 and 6.3 microns (125 – 250 micro inches).
Chalco flange product partial stock size reference table
![]() |
Loose plate flange aluminum | ||||||
DN | d1 | Typ | b | O | kg | Price | |
10 | 17, 2 | C | 12 | blank | 0, 196 | request | |
15 | 21, 3 | C | 12 | blank | 0, 180 | request | |
15 | 21, 3 | C | 12 | coated | 0, 180 | request | |
20 | 26, 9 | C | 12 | blank | 0, 235 | request | |
20 | 26, 9 | C | 12 | coated | 0, 240 | request | |
25 | 29, 0 | A | 12 | blank | 0, 260 | request | |
25 | 29, 0 | A | 12 | coated | 0, 280 | request | |
25 | 33, 7 | C | 12 | blank | 0, 240 | request | |
25 | 33, 7 | C | 12 | coated | 0, 260 | request | |
32 | 35, 0 | A | 16 | blank | 0, 500 | request | |
32 | 35, 0 | A | 16 | coated | 0, 560 | request | |
32 | 42, 4 | C | 16 | blank | 0, 520 | request | |
32 | 42, 4 | C | 16 | coated | 0, 524 | request | |
40 | 44, 0 | A | 16 | blank | 0, 593 | request | |
40 | 44, 0 | A | 16 | coated | 0, 600 | request | |
40 | 48, 3 | C | 16 | blank | 0, 580 | request | |
40 | 48, 3 | C | 16 | coated | 0, 580 | request | |
50 | 54, 0 | A | 16 | blank | 0, 780 | request | |
50 | 54, 0 | A | 16 | coated | 0, 760 | request | |
50 | 57, 0 | B | 16 | blank | 0, 770 | request | |
50 | 57, 0 | B | 16 | coated | 0 | request | |
50 | 60, 3 | C | 16 | blank | 0, 700 | request | |
50 | 60, 3 | C | 16 | coated | 0, 690 | request | |
50 | 60, 3 | D | 18 | blank | 0, 640 | request | |
65 | 70, 0 | A | 16 | blank | 0, 860 | request | |
65 | 70, 0 | A | 16 | coated | 0, 920 | request | |
65 | 76, 1 | C | 16 | blank | 0, 850 | request | |
65 | 76, 1 | C | 16 | coated | 0, 860 | request | |
65 | 76, 1 | D | 18 | blank | 0, 797 | request | |
80 | 84, 0 | A | 18 | blank | 1, 099 | request | |
80 | 84, 0 | A | 18 | coated | 1, 100 | request | |
80 | 88, 9 | C | 18 | blank | 1, 038 | request | |
80 | 88, 9 | C | 18 | coated | 1, 060 | request | |
80 | 88, 9 | D | 20 | blank | 0, 951 | request | |
100 | 104, 0 | A | 18 | blank | 1, 247 | request | |
100 | 104, 0 | A | 18 | coated | 1, 240 | request | |
100 | 108, 0 | B | 18 | blank | 1, 240 | request | |
100 | 108, 0 | B | 18 | coated | 0 | request | |
100 | 114, 3 | C | 18 | blank | 1, 180 | request | |
100 | 114, 3 | C | 18 | coated | 1, 120 | request | |
100 | 114, 3 | D | 20 | blank | 1, 014 | request | |
125 | 129, 0 | A | 18 | blank | 1, 475 | request | |
125 | 129, 0 | A | 18 | coated | 1, 540 | request | |
125 | 133, 0 | B | 18 | blank | 1, 650 | request | |
125 | 133, 0 | B | 18 | coated | 0 | request | |
125 | 139, 7 | C | 18 | blank | 1, 430 | request | |
125 | 139, 7 | C | 18 | coated | 1, 439 | request | |
125 | 139, 7 | D | 22 | blank | 1, 538 | request | |
150 | 154, 0 | A | 18 | blank | 1, 874 | request | |
150 | 154, 0 | A | 18 | coated | 1, 920 | request | |
150 | 159, 0 | B | 18 | blank | 1, 870 | request | |
150 | 159, 0 | B | 18 | coated | 0 | request | |
150 | 168, 3 | C | 18 | blank | 1, 700 | request | |
150 | 168, 3 | C | 18 | coated | 1, 680 | request | |
150 | 168, 3 | D | 22 | blank | 2, 054 | request | |
200 | 204, 0 | A | 20 | blank | 2, 660 | request | |
200 | 204, 0 | A | 20 | coated | 2, 680 | request | |
200 | 219, 1 | C | 20 | blank | 2, 486 | request | |
200 | 219, 1 | C | 20 | coated | 2, 420 | request | |
200 | 219, 1 | D | 24 | blank | 2, 216 | request | |
250 | 254, 0 | A | 22 | blank | 3, 570 | request | |
250 | 254, 0 | A | 22 | coated | 3, 298 | request | |
250 | 267, 0 | B | 22 | blank | 3, 300 | request | |
250 | 267, 0 | B | 22 | coated | 0 | request | |
250 | 273, 0 | C | 22 | blank | 3, 240 | request | |
250 | 273, 0 | C | 22 | coated | 3, 220 | request | |
250 | 273, 0 | D | 26 | blank | 3, 480 | request | |
300 | 304, 0 | A | 22 | blank | 4, 240 | request | |
300 | 304, 0 | A | 22 | coated | 3, 700 | request | |
300 | 323, 9 | C | 22 | blank | 3, 720 | request | |
300 | 323.9 | C | 22 | coated | 3, 680 | request | |
300 | 323.9 | D | 26 | blank | 3, 380 | request | |
350 | 355.6 | A/C | 22 | blank | 5, 100 | request | |
350 | 355.6 | A/C | 22 | coated | 5, 200 | request | |
350 | 368, 0 | B | 22 | blank | 4, 200 | request | |
350 | 368, 0 | B | 22 | coated | 0 | request | |
400 | 406, 4 | A/C | 25 | blank | 6, 940 | request | |
400 | 406, 4 | A/C | 25 | coated | 7, 020 | request | |
450 | 457, 2 | A/C | 25 | coated | 0 | request | |
450 | 457.2 | A/C | 25 | blank | 7, 300 | request | |
500 | 508.0 | A/C | 28 | blank | 9, 320 | request | |
500 | 508.0 | A/C | 28 | coated | 0 | request | |
600 | 609.6 | A/C | 30 | blank | 12, 130 | request | |
600 | 609.6 | A/C | 30 | coated | 14, 500 | request | |
700 | 711.2 | A/C | 40 | blank | 21, 000 | request | |
700 | 711.2 | A/C | 40 | coated | 0 | request | |
800 | 812.8 | A/C | 44 | blank | 29, 200 | request | |
800 | 812.8 | A/C | 44 | coated | 30, 000 | request | |
900 | 914.4 | A/C | 44 | blank | 37, 000 | request | |
900 | 914.4 | A/C | 44 | coated | 0 | request | |
1000 | 1016.0 | Air conditioning | 44 | blank | 43, 000 | request | |
1000 | 1016.0 | A/C | 44 | coated | 0 | request | |
1200 | 1232.0 | Air conditioning | 60 | blank | 75, 000 | request |
![]() |
Slip-on weld flanges | ||||||
Pipe size | Flange OD | For Bolt Dia | Dia | No. of | Bolt Circle Dia. | Max. Pressure | |
1/2 | 3 1/2" | 1/2" | 5/8" | 4 | 2 3/8" | 150 psi @ 72° F | |
3/4 | 3 7/8" | 1/2" | 5/8" | 4 | 2 3/4" | 150 psi @ 72° F | |
1 | 4 1/4" | 1/2" | 5/8" | 4 | 3 1/8" | 150 psi @ 72° F | |
1 1/4 | 4 5/8" | 1/2" | 5/8" | 4 | 3 1/2" | 150 psi @ 72° F | |
1 1/2 | 5" | 1/2" | 5/8" | 4 | 3 7/8" | 150 psi @ 72° F | |
2 | 6" | 5/8" | 3/4" | 4 | 4 3/4" | 150 psi @ 72° F | |
2 1/2 | 7" | 5/8" | 3/4" | 4 | 5 1/2" | 150 psi @ 72° F | |
3 | 7 1/2" | 5/8" | 3/4" | 4 | 6" | 150 psi @ 72° F | |
4 | 9" | 5/8" | 3/4" | 8 | 7 1/2" | 150 psi @ 72° F | |
6 | 11" | 3/4" | 7/8" | 8 | 9 1/2" | 150 psi @ 72° F | |
8 | 13 1/2" | 3/4" | 7/8" | 8 | 11 3/4" | 150 psi @ 72° F |
![]() |
Butt-weld flanges | ||||||
Pipe size | Flange OD | For Bolt Dia | Dia | No. of | Bolt Circle Dia. | Max. Pressure | |
1/2 | 3 1/2" | 1/2" | 5/8" | 4 | 2 3/8" | 150 psi @ 72° F | |
3/4 | 3 7/8" | 1/2" | 5/8" | 4 | 2 3/4" | 150 psi @ 72° F | |
1 | 4 1/4" | 1/2" | 5/8" | 4 | 3 1/8" | 150 psi @ 72° F | |
1 1/2 | 5" | 1/2" | 5/8" | 4 | 3 7/8" | 150 psi @ 72° F | |
2 1/2 | 7" | 5/8" | 3/4" | 4 | 5 1/2" | 150 psi @ 72° F | |
3 | 7 1/2" | 5/8" | 3/4" | 4 | 6" | 150 psi @ 72° F | |
4 | 9" | 5/8" | 3/4" | 8 | 7 1/2" | 150 psi @ 72° F | |
6 | 11" | 3/4" | 7/8" | 8 | 9 1/2" | 150 psi @ 72° F |
![]() |
Aluminum blind flange | ||||
Size (in) | Bolt Circle Diameter (in) | Bolt Hole Diameter (in) | Flange Diameter (in) | Flange Thickness (in) | Number of Bolt Holes |
1/2 | 2.38 | 0.63 | 3.5 | 0.44 | 4 |
3/4 | 2.75 | 0.63 | 3.88 | 0.5 | 4 |
1 | 3.13 | 0.63 | 4.25 | 0.56 | 4 |
1-1/4 | 3.5 | 0.63 | 4.63 | 0.63 | 4 |
1-1/2 | 3.88 | 0.63 | 5 | 0.69 | 4 |
2 | 4.75 | 0.75 | 6 | 0.75 | 4 |
2-1/2 | 5.5 | 0.75 | 7 | 0.88 | 4 |
3 | 6 | 0.75 | 7.5 | 0.94 | 4 |
3-1/2 | 7 | 0.75 | 8.5 | 0.94 | 8 |
4 | 7.5 | 0.75 | 9 | 0.94 | 8 |
5 | 8.5 | 0.88 | 10 | 0.94 | 8 |
6 | 9.5 | 0.88 | 11 | 1 | 8 |
8 | 11.75 | 0.88 | 13.5 | 1.13 | 8 |
10 | 14.25 | 1 | 16 | 1.19 | 12 |
![]() |
Aluminum threaded pipe flange | ||||||
Pipe size | Flange OD | For Bolt Dia | Dia | No. of | Bolt Circle Dia. | Max. Pressure | |
1/2 | 3 1/2" | 1/2" | 5/8" | 4 | 2 3/8" | 150 psi @ 72° F | |
3/4 | 3 7/8" | 1/2" | 5/8" | 4 | 2 3/4" | 150 psi @ 72° F | |
1 | 4 1/4" | 1/2" | 5/8" | 4 | 3 1/8" | 150 psi @ 72° F | |
1 1/4 | 4 5/8" | 1/2" | 5/8" | 4 | 3 1/2" | 150 psi @ 72° F | |
1 1/2 | 5" | 1/2" | 5/8" | 4 | 3 7/8" | 150 psi @ 72° F | |
2 | 6" | 5/8" | 3/4" | 4 | 4 3/4" | 150 psi @ 72° F | |
2 1/2 | 7" | 5/8" | 3/4" | 4 | 5 1/2" | 150 psi @ 72° F | |
3 | 7 1/2" | 5/8" | 3/4" | 4 | 6" | 150 psi @ 72° F | |
4 | 9" | 5/8" | 3/4" | 8 | 7 1/2" | 150 psi @ 72° F | |
6 | 11" | 3/4" | 7/8" | 8 | 9 1/2" | 150 psi @ 72° F | |
8 | 13 1/2" | 3/4" | 7/8" | 8 | 11 3/4" | 150 psi @ 72° F |
Frequently Asked Questions about flange product purchase
How to choose the right flange type?
There are various types of flanges, such as welding neck flanges, flat welding flanges, slip-on flanges , socket welding flanges, threaded flanges, blind flanges, etc. The selection should be based on the pressure, temperature, medium characteristics and installation and maintenance requirements of the pipeline system.
How to choose the material of flange?
The flange material should match the pipe material. Common materials include carbon steel, stainless steel, alloy steel, etc. For corrosive media or high temperature and high pressure environments, it is recommended to use stainless steel or alloy steel flanges.
How to determine the standard and size of flange?
There are many flange standards, such as the national standard ( GB), the American standard (ANSI/ASME), the German standard (DIN), etc. When purchasing, you need to confirm the standard that the required flange meets, and select the appropriate flange size according to the nominal diameter (DN) and pressure level (PN) of the pipeline .
How to ensure the quality of flanges?
Choose manufacturers that meet international standards and ensure that the products have ISO, ASME, CE and other certifications.
When purchasing, documents such as material certification and test reports are required to confirm that the product meets the requirements.
Focus on checking the flange's dimensional accuracy, surface treatment, and weld quality to ensure there are no defects such as cracks, pores, and burrs.
What are the advantages of aluminum flanges over steel flanges?
Aluminum flanges are lightweight, corrosion-resistant, have good thermal conductivity, and are non-magnetic. They are suitable for special environments such as food processing, medicine, aerospace, and marine engineering, and are superior to carbon steel flanges in situations where weight reduction and corrosion resistance need to be improved.
What is the lead time when ordering flanges?
The production cycle of flanges depends on specifications, materials and processing methods:
- Flanges of standard specifications are usually available from stock with a delivery time of 1-3 days.
- Non-standard customized flanges require mold opening or special processing, and the delivery time is generally 10-30 days, depending on the order quantity and process complexity.
What are some common questions when buying flanges?
- Does the flange bolt hole spacing meet the existing pipeline standards? (Avoid installation errors)
- Does the flange sealing surface match the matching gasket? (Affects sealing performance)
- Is additional anti-corrosion treatment required, such as anodizing or painting? (To improve durability)
What value-added services does Chalco provide?
- Customized service: Non-standard flanges, large diameter flanges, etc. can be processed according to customer needs.
- Surface treatment: Provide smooth, serrated, oxidized and other different surface processes.
- Technical support: A professional team provides selection suggestions to ensure that the product is suitable for your engineering needs.