Pressure vessel aluminum plate with foil aluminum tube certification
- EU CERTIFICATE OF QUALITY SYSTEM APPROVAL , In accordance with the requirements of the Pressure Equipment, Directive 2014/68/EU .
- In accordance with the requirements of AD 2000-Merkblatt W0.
- DOT/TC certified and manufactured in accordance with DOT-3AL and TC-3ALM specifications.
Chalco Aluminum can provide 6061, 6351 seamless aluminum tubes, 6061, 6351, 7032, 7060 aluminum round bar, 5052, 5154, 5083, 6061 aluminum coil plate, and 5052, 5154, 5083, 6082, 6061 O aluminium circular plate, which are suitable for various aluminum alloy gas cylinders, fire extinguishers.
Commonly used alloy specifications for aluminum alloy gas cylinders, fire extinguishers
6061, 6351, 7032, 7060 aluminum alloy round bar
Seamless aluminum alloy gas cylinders, fire extinguishers are generally obtained by extrusion and spinning methods. Extrusion method bottle materials are commonly used 6061, 6351, 7032, 7060 aluminum alloy round bars, heated and extruded into seamless aluminum tubes, and then closed. Then heat treatment to reach T6 temper.
When 7032 and 7060 aluminum alloys are used, the diameter of the gas cylinder should not exceed 203mm, and the volume should not exceed 20L. 7032 and 7060 aluminum alloys have significantly better performance indicators than 6xxx aluminum alloys. But due to the high content of alloy elements in the matrix and higher working pressure, the fracture resistance of 7xxx aluminum alloys is poor, which manifested on the cylinder is the poor fatigue life.
However, through the three-stage overaging process of 115°C /6 ~ 9h → 180°C /8 ~ 13h → 115°C /6 ~ 10h, the fatigue performance specified in the product standard can be met, and the performance is optimal and can meet the demand for mass production.Quick Quote
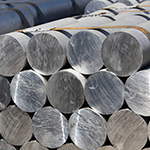
6061-aluminum-round-bar
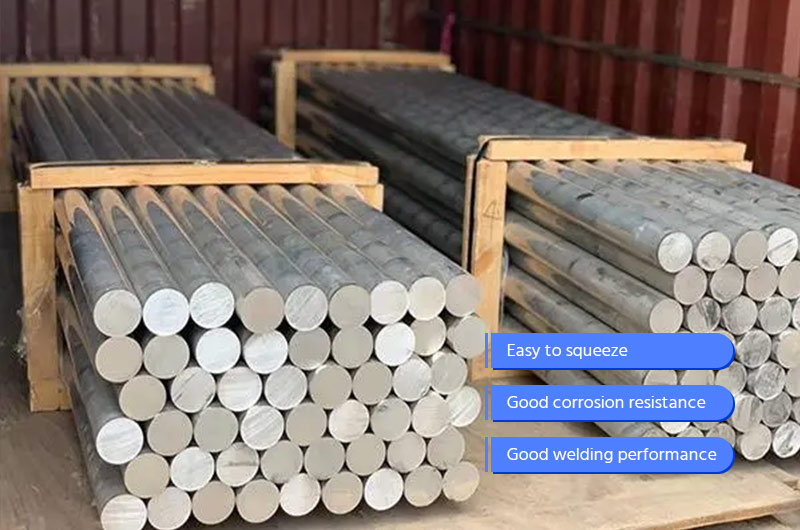
6005-aluminum-bar
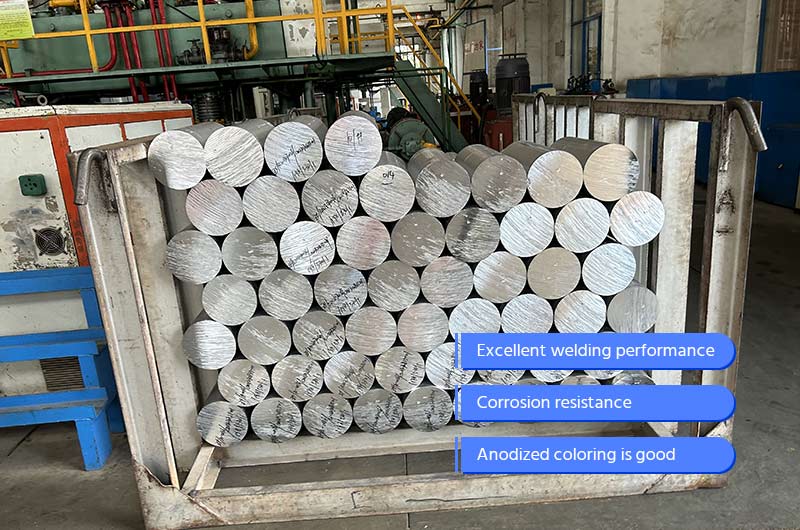
6063-aluminum-rod
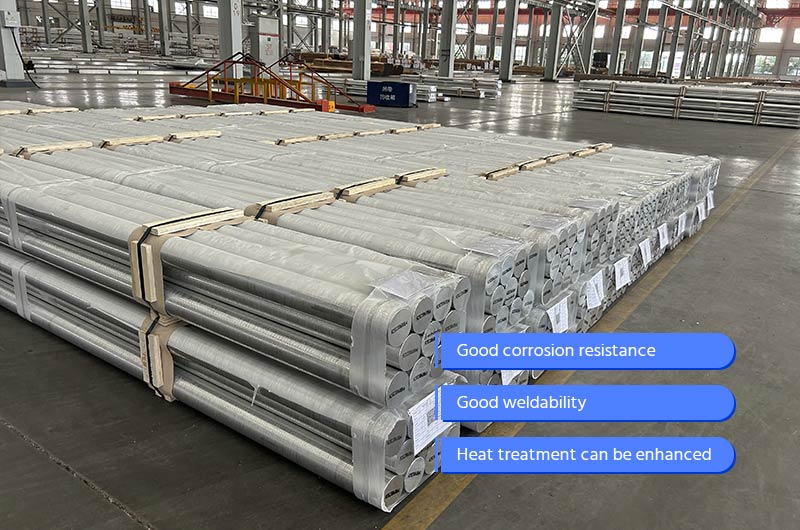
6082-aluminum-round-bar
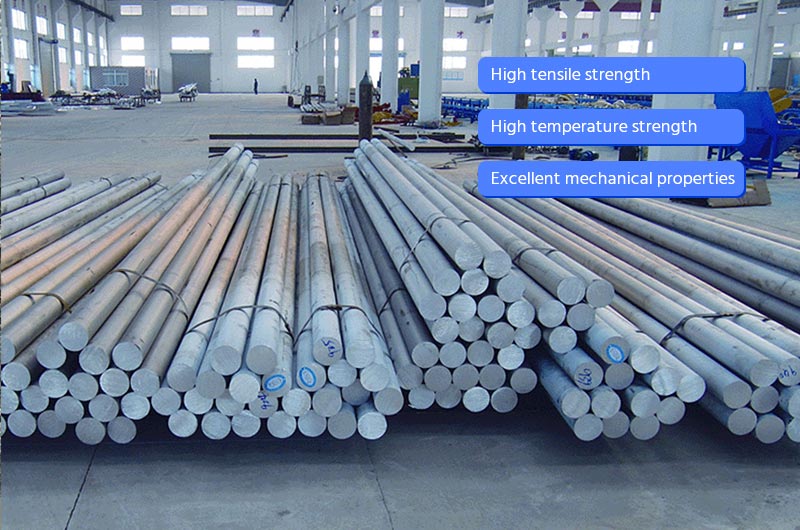
7050-aluminum-rod-bar

7075-aluminium-rod
5052 5154 5083 6082 6061 O aluminum circle plate
Seamless aluminum alloy cylinders can also be formed by spinning and stretching, which is suitable for the production of small batches of aluminum cylinders. The common specifications are as follows:
Alloy | 5052, 5154, 5083, 6082, 6061 |
Product name | 5052, 5154, 5083, 6082, 6061 O aluminum circle plate |
Temper | O |
Thickness | 4mm-6mm |
Surface quality | Bright and smooth, free of rolling mark, oil stain oxidation defect. Bright and smooth with lightly scratch and defect not affect the usage, after deep drawing or spinning process not have orange peel. |
Application | aluminum seamless LPG cylinders |
6061 6351 aluminum alloy seamless tube
The seamless aluminum alloy gas cylinder can also be obtained by closing both ends of the seamless aluminum tube. Utilizing the good plasticity of the seamless aluminum tube at high temperature, under repeated rolling in the radial and longitudinal directions of the rotary wheel, the diameter shrinks and thickens continuously, and finally the seal is fused together to form a variable wall thickness cylinder head.Quick Quote
The process route is:
- Pipe spinning
- Strong spinning straight wall part
- Heat closing (400 ~ 450 ℃) general spinning to form the shoulder and neck of the bottle
6061 and 6351 aluminum alloy seamless aluminum tubes are often used.
5052 5154 5083 6061 aluminum alloy coil plate
Ordinary aluminum alloy gas cylinders, fire extinguishers are usually stretched and welded from 5mm-6mm 5052, 5154, 5083, 6061 aluminum coils plates. The welding seam is in the middle of the bottle body, which is welded with 5356 aluminum alloy welding wire.
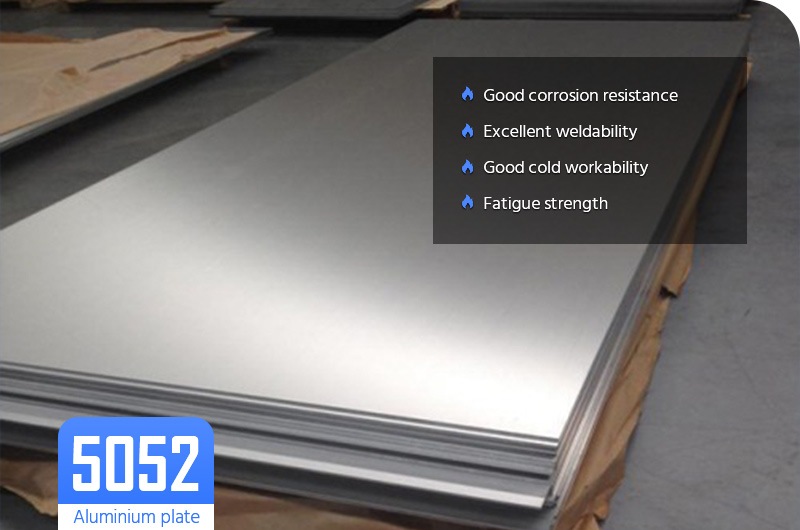
5052-aluminum-sheet-plate
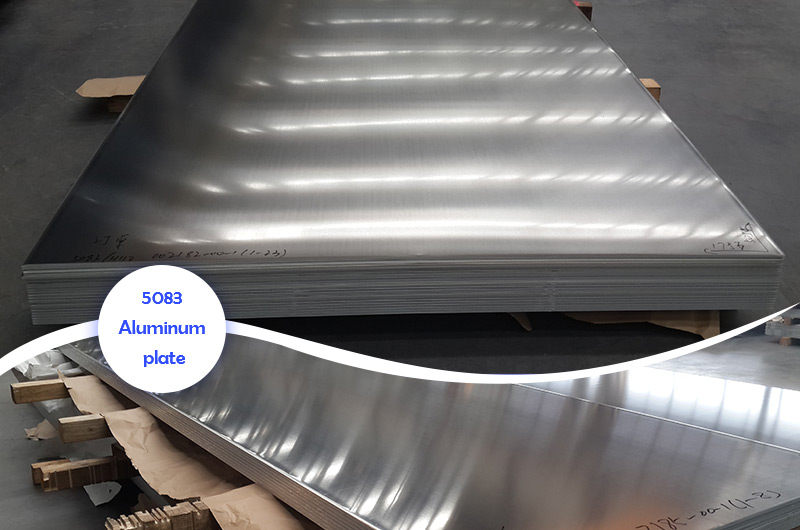
5083-aluminum-plate
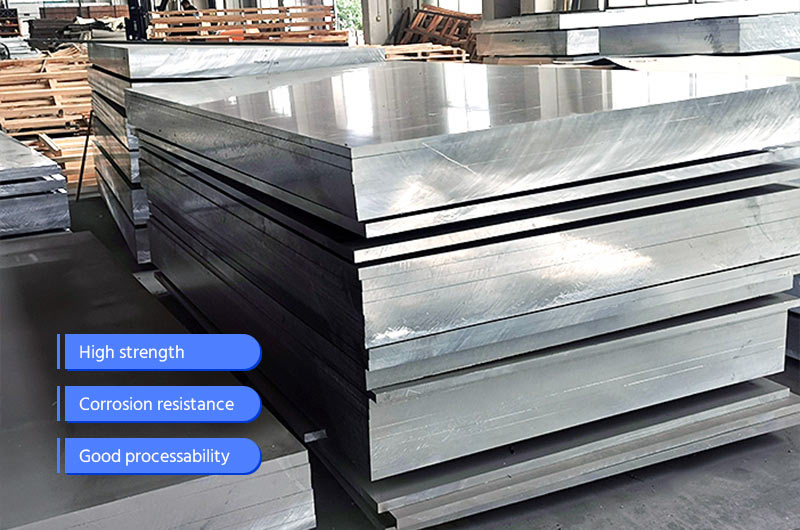
5454-plate
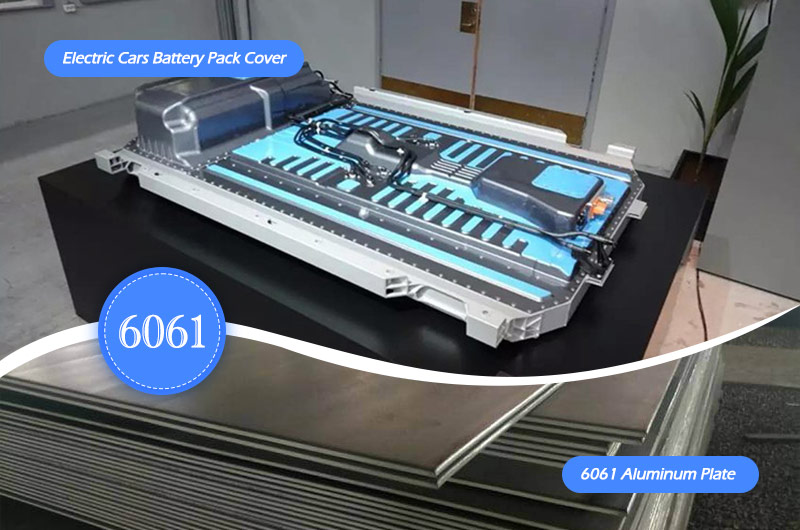
6061-aluminum-plate
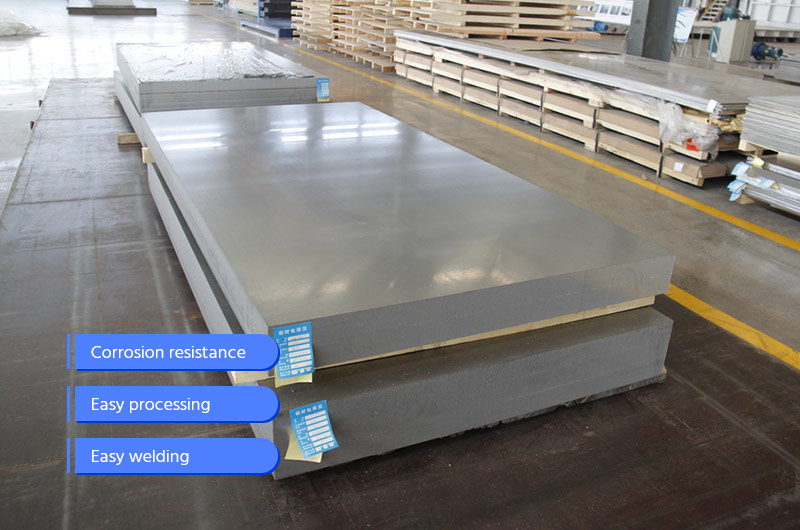
6063-aluminum-sheet
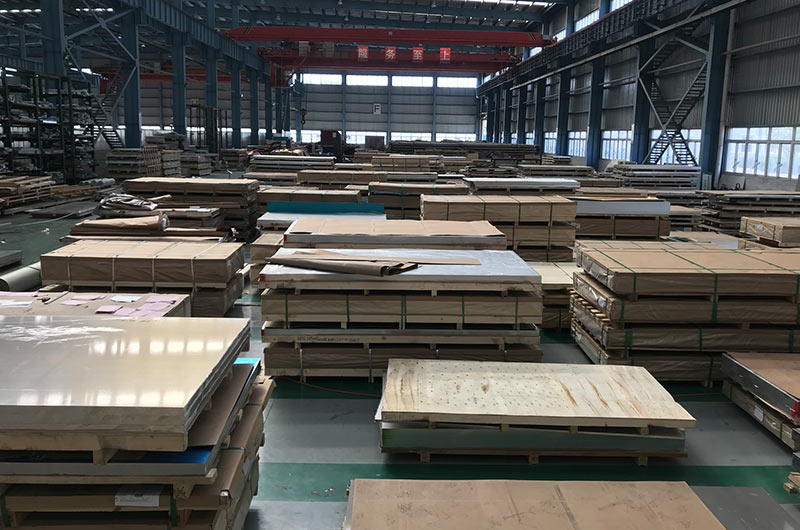
6013-aluminum-sheet-plate
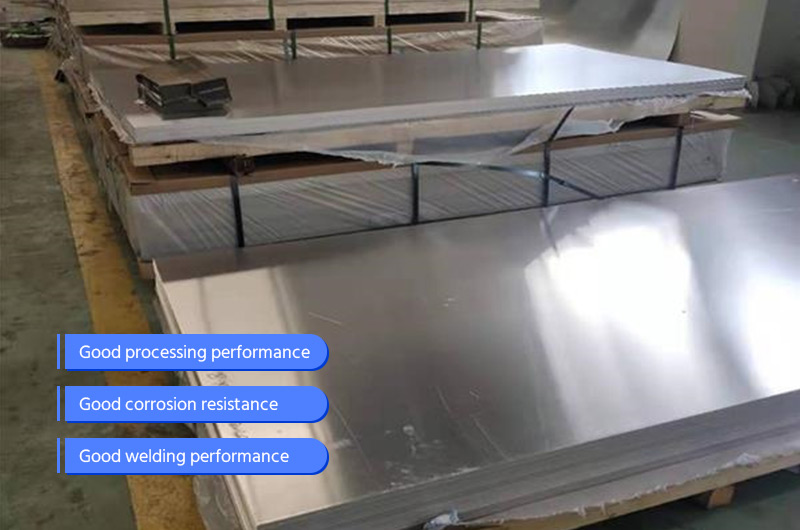
6082-aluminum-sheet
The advantages of aluminum alloy application on gas cylinders, fire extinguishers
Compared with steel commonly used in gas cylinders, fire extinguishers, aluminum alloys can be used in gas cylinders and have the following advantages.
Good corrosion resistance
Corrosion resistance is one of the most important uses of non-ferrous metal gas cylinders, fire extinguishers. Due to the different chemical properties of aluminum alloys, the range and degree of corrosion resistance media are also different.
Good heat transfer
The thermal conductivity of aluminum alloy is several times that of steel. In terms of thermal conductivity, aluminum alloy is an excellent thermal conductivity material second only to copper.
High specific strength
Among the commonly used structural materials, aluminum has a lower density and a higher specific strength (ratio of tensile strength to density) than steel. For mobile gas cylinders, fire extinguishers, higher specific strength of materials means lighter weight of equipment, which can reduce energy consumption and save costs during transportation.
Good low temperature resistance
The crystal structure of the aluminum alloy is a face-centered cubic structure. Since the face-centered cubic crystal structure has a particularly good coordination ability in all aspects, when the aluminum alloy gas cylinder is used under a very low temperature condition, brittle fracture will not occur. Not only that, the light and toughness of aluminum alloy will not be reduced, but will have good mechanical properties. The low temperature resistance of aluminum alloy can reach -269℃ without any additional requirements.Quick Quote
Are You Looking for an Aluminum Supplier?
If you need a professional aluminum supplier to provide you with high-quality, cost-effective aluminum, we will be your best choice.
How to choose the raw material of aluminum alloy gas cylinder, fire extinguishers?
In the selection of aluminum alloy seamless gas cylinder body material, the first consideration is its safety. In order to prevent accidents caused by failure and damage, the bottle body material must have sufficient strength, certain plasticity, toughness, and good durability, corrosion ability and good low temperature performance.
Because the fatigue strength of aluminum alloy is low, it is necessary to choose a material with better fatigue resistance.
Third, consider its processing performance, supply and price.
According to the requirements of GB 11640-2011 Aluminum Alloy Seamless Gas Cylinders, the body material of aluminum alloy seamless gas cylinders should generally be 6061 aluminum alloy, which has the performance of good cold and hot processing, corrosion resistance, low temperature, fatigue, etc. GB 11640-2011 Aluminum Alloy Seamless Gas Cylinders allows the cylinder to use other aluminum alloy materials with good intergranular corrosion resistance and process performance, but it should pass the corrosion test and the constant load crack resistance test.
Chalco Aluminum can communicate and provide alloys required for various aluminum alloy cylinders, such as 5052, 5154, 5083, 6082, 6061, 6061, 6351, 7032, 7060.
Manufacturing process of aluminum alloy gas cylinder, fire extinguishers
Punching and drawing method
This method refers to the aluminum alloy seamless gas cylinder, fire extinguishers, fire extinguishers formed by heating and punching the aluminum alloy billet into a short and thick cup, and then drawing and closing it. It is the main method for the manufacture of aluminum alloy seamless gas cylinders, fire extinguishers.
Cold extrusion
Cold extrusion refers to the aluminum alloy seamless gas bottle formed by cold extrusion of aluminum alloy billet and then closed. This processing method has simple procedures and low cost, but requires a press with a larger tonnage.
Punching and Stretching Method
It refers to the process of deep-drawing the aluminum alloy plate into a long cup-shaped part, and then closing the open end. The wall thickness of this processing method is relatively uniform, but the material utilization rate is low, the process is complicated, and the cost is high, so there are fewer manufacturers using this processing method.
Spinning method
Spinning method refers to the gas bottle manufactured by spinning the aluminum alloy plate. For materials such as aluminum alloy, spinning can maximize the plastic potential of the material, so that the deformation can reach more than 70%, and one-time clamping and spinning can achieve the effect that requires multiple stretching and annealing. Therefore, stretch spinning is also one of the processes for manufacturing aluminum bottles, and it is especially suitable for the production of small batches of products.Quick Quote
The barrel billet after stretching and spinning can be spun again (generally needs to be heated) to form a small mouth gas cylinder, fire extinguishers. This kind of gas cylinder, fire extinguishers, which is all processed and manufactured by spinning process, is called "full spinning gas cylinder”, which generally has high precision, uniform wall thickness, good quality, and high bursting pressure (need to cooperate with appropriate heat treatment process).
Welding method
The welding gas bottle is generally stretched and formed by 5mm-6mm 6061 plate, the weld seam is in the middle of the bottle body, and the weld joint is opened with a 60° bevel in the butt joint method, leaving a 2 mm excess height, and welded with 5356 aluminum alloy welding wire.
Application of aluminum alloy cylinders
With the emergence of cold back extrusion technology, large-scale production of aluminum alloy gas cylinders, fire extinguishers began in Europe. The first batch of gas cylinders, fire extinguishers are made of 6xxx series aluminum alloys. Lightweight, corrosion-resistant aluminum gas cylinders are becoming more and more popular in the beverage industry and are mainly used to store CO2. While 6 xxx gas cylinders are still widely used today, the use of aluminum cylinders has become more widespread and technically demanding in recent years. In many markets, such as healthcare, life support, and new energy vehicle applications, users require lighter-weight solutions for improved portability and storage efficiency.
Generally, aluminum alloy cylinders are used to hold petroleum gas, natural gas, hydrogen, standard gas, ultra-pure gas, medical oxygen, carbon monoxide, carbon dioxide, diving, beverage preparation and other gases.
According to the use, it is divided into the following categories:
Aluminum cylinder
- Seamless aluminum alloy gas cylinders, fire extinguishers
- Aluminum alloy oxygen cylinder
- Aluminum alloy seamless gas cylinder, fire extinguishers for sea diving
- Aluminum liquefied petroleum gas (LPG) cylinders
- Aluminum alloy vehicle LNG cylinder
- Vehicle-mounted aluminum alloy CNG cylinder
- Aluminum argon tank
- Aluminum helium cylinder
- Aluminium co2 cylinder
- Aluminum propane tank
- Aluminum alloy HCNG cylinder
- Hydrogen/natural gas (HCNG) is a hydrogen-mixed natural gas.
Composite material aluminum liner gas cylinder, fire extinguishers
Aluminum alloy liner carbon fiber winding structure is composed of aluminum alloy seamless liner, carbon fiber, resin, etc. It has low density of aluminum alloy material, excellent sealing performance, processability, ductility, enhanced crack resistance, good performance and other characteristics. It is also combined with the advantages of light weight, high specific strength, good safety, high specific modulus and strong designability of carbon fiber composite materials, to achieve high pressure bearing capacity, high fatigue life, light weight, corrosion resistance and other excellent performance combination.Quick Quote
Composite aluminum alloy gas cylinders, fire extinguishers have been widely used in the aerospace field, and have become key components of satellites, missile weapon power systems, launch vehicle auxiliary power systems and space vehicle propulsion systems, Such as HS2702 satellite platform, Centaur carrier rocket, space shuttle, Tianzhou cargo spaceship, Tiangong Laboratory, Chang'e V and Tianwen I, etc.
Lincoln Company has developed a spherical 5086 aluminum alloy lined T40 carbon fiber wound composite gas cylinder, fire extinguishers for the deep space program, with a working pressure of 34. 47 MPa; Brunswick company developed a spherical 6061 aluminum alloy lined T40 carbon fiber wound composite gas cylinder for the FS-1300 satellite platform, working pressure 27. 58 MPa.Quick Quote
Aluminum alloys are widely used in storage aluminum tanks and gas cylinders, fire extinguishers. In recent years, aluminum-lithium alloy materials represented by 2195 and aluminum-scandium alloy materials represented by 5B70 have been industrialized. The alloy formed by adding lithium to aluminum can effectively reduce the density of the alloy and increase the stiffness, while still maintaining high strength, good corrosion resistance and fatigue resistance, and suitable ductility. The alloy is used in aerospace fields. It is mainly used in the external storage tanks of some space shuttles and the large storage tank structure of the carrier.
Composite gas cylinders, fire extinguishers are also used in the field of natural gas fuel cylinders for vehicles and portable oxygen cylinders for medical diving.
Why choose Chalco Aluminum as the supplier of aluminum alloy cylinder raw materials?
Chalco Aluminum has rich experience in the field of raw materials for aluminum alloy cylinders, providing 6061, 6351, 7032, 7060 aluminum rods for aluminum alloy extrusion, 5052, 5154, 5083 6082, 6061 O aluminum circle, 6061, 6351 aluminum seamless tube, 5052, 5154, 5083 aluminum coil. They are widely used in various areas such as aluminum alloy gas cylinders, fire extinguishers, petroleum and petrochemical, gas, automobile transportation, diving, aerospace and other fields and has achieved outstanding results.