Chalco brazed aluminum honeycomb panel introduction
Brazed aluminum honeycomb panel is a honeycomb panel material prepared by brazing process, which uses brazing material to metallurgically connect the aluminum honeycomb core with the panel to form a stable joint structure. This connection method allows the product to be welded and processed later, so that the brazed aluminum honeycomb panel has good mechanical operability in the application.
This material is not only light in weight, high in strength and rigid, but also has excellent stability, heat insulation and sound insulation properties, and is pollution-free. In addition, brazing technology overcomes the shortcomings of adhesive connection methods and is not limited by the performance of the adhesive. Therefore, the mechanical properties are greatly improved, significantly higher than traditional adhesive honeycomb materials, and are very suitable for industrial production.
Why we recommend aluminum alloy brazed honeycomb panels to you
Aluminum honeycomb panels have the advantages of light weight, high strength, large size, and low cost. They have been widely used in various industries for many years. However, in addition to the above advantages, traditional honeycomb panels are bonded with epoxy glue, which still has major hidden dangers in fire safety issues.
Brazed aluminum alloy honeycomb panels are superior to traditional honeycomb aluminum panels in terms of structural strength, sound insulation, fire resistance and environmental protection. Unlike ordinary honeycomb aluminum panels that are glued together, brazed honeycomb panels use a brazing process to firmly connect the honeycomb core to the panel, and have higher peel strength, compressive strength and impact resistance, making them very suitable for high-strength and special demand occasions, such as aerospace, sound insulation and fireproof buildings.
Property | Adhesive honeycomb panel | Brazed honeycomb panels |
Connection | Use adhesive to bond honeycomb core and panels | Use brazing process to metallurgically connect the honeycomb core to the panel |
Adhesion strength | Aluminum honeycomb panels are sandwich structures formed by gluing aluminum alloy skins and honeycomb cores. However, the gluing process can easily lead to interface failure during engineering operations, resulting in defects such as hollowing and bulging. At the same time, the mechanical properties are also limited by the performance of the adhesive. | Using brazed aluminum honeycomb panels instead of glued aluminum honeycombs is a way to better utilize the advantages of honeycomb structures. Metallurgical connection, high connection strength, excellent reliability, suitable for occasions with high strength requirements . |
Peel strength | Low, limited by adhesive performance | High (>200N mm/mm), meeting high strength requirements |
Fire resistance | Not highly fire resistant, limited fire performance | Temperature resistance above 600℃, in line with fire resistance standards |
Environmental protection | Contains adhesive, which may cause pollution | Non-combustible, non-toxic, 100% recyclable |
Sound insulation performance | Sound insulation effect is average | The sound insulation can reach more than 26dB, and the highest can reach 33dB |
Impact resistance | generally | Excellent impact resistance, meeting high impact strength requirements |
Service life | medium | The service life is more than three times that of adhesive board |
Application Areas | Building decoration, interior wall panels, etc. | Rail transportation, aerospace, shipbuilding, building exterior walls, etc. |
Performance parameters of Chalco brazed aluminum honeycomb panels
Item | Experimental Standard | Performance |
Weight | GB/T 1455-2005 | 9.5 kg/m² |
Bending Strength | GB/T 1453-2005 | 155 MPa |
Compressive Strength | GB/T 1452-2005 | 5.09 MPa |
Tensile Strength | GB/T 1457-2005 | 8.29 MPa |
Peel Strength | GB/T 1457-2005 | 231 (N·mm)/mm |
Fatigue Resistance | Load: 0.3-3.6 KN, Frequency: 10 Hz, Span: 236 mm, 3 million cycles | No damage |
Sound Insulation Performance | ISO 10140-2: 2010 | 28 dB |
Thermal Conductivity | GB/T 13475-2008 | 4.8 W/(m²·K) |
Falling Ball Impact Performance | - | A steel ball (50 mm diameter, 500 g) falls from 2 meters; depth of depression after half an hour is less than 0.5 mm |
Fire Resistance | BS EN 1363-1: 2012 | After 46 minutes of combustion, no cracks, collapse, breakage, flames, etc.; sample remained intact |
Simulated High-Heeled Shoes Bearing Strength | - | Applied force of 1000 N on a 25 mm² area for 1 minute; no obvious indentation |
Salt Spray Resistance | ISO 9227: 1990 | 168 hours; no significant corrosion |
- The roller peel strength is high, generally greater than 200N·mm/mm, and the honeycomb core is in a torn state.
- The compressive strength ranges from 4 to 20 MPa.
- The tensile strength exceeds 10MPa.
- The impact resistance is superior to similar products. After being tested with a 500g cement ball and a speed of 350Km/h, the performance of the welded aluminum honeycomb panel fully meets the design requirements.
- The sound insulation effect of standard products is ≥26dB. By changing the specifications and structure, the sound insulation can reach more than 33dB.
- It complies with the fire resistance test requirements of EN 1363-1:2012 and can withstand temperatures above 600°C.
- The surface density of 20mm thickness is 810Kg/㎡ and the volume density is 0.40.8*10³Kg/m³.
- The material is non-flammable, does not produce toxic or hazardous substances, is 100% recyclable and has no pollution.
Chalco brazed honeycomb composite panel product recommendation
Aluminum brazed honeycomb panel
Standard size: 4*8
Custom sizes available through salesperson communication. We offer brazed honeycomb panel technology, with fully welded aluminum panels, making it 100% non-combustible, recyclable, and environmentally friendly.
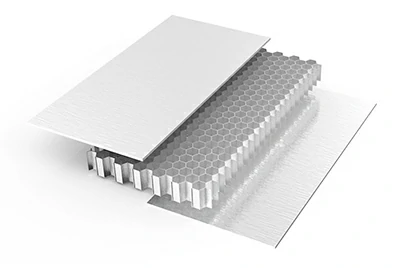
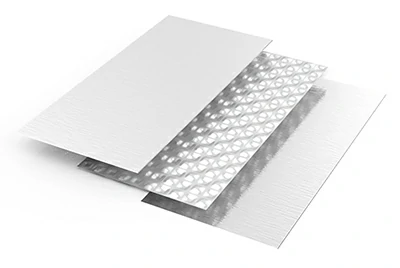
Brazed aluminum honeycomb panel/ACM Panel
Conventional ACM panels use adhesives to bond aluminum skins to a polyethylene core, posing a fire risk. In contrast, Chalco's new generation ACM panels feature a metal core welded to the aluminum skin using brazing technology, making them 100% non-combustible.
Brazed backing stone honeycomb panel
Our lightweight 5mm stone veneer panels are ideal for exterior cladding in extreme weather conditions. With a large 1500*3000mm size, they are easy to install. Our experienced team ensures high-quality, complex, and custom-shaped panels through comprehensive testing.
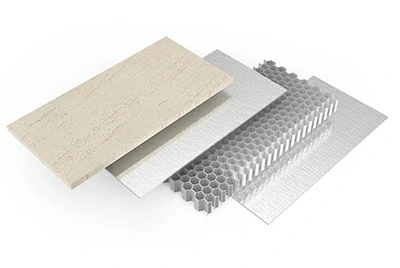
Chalco brazed honeycomb aluminum plate application areas
Aircraft Manufacturing
Brazed honeycomb panels are widely used in aircraft for their strength, light weight, and high temperature resistance. They excel in high-stress, high-vibration environments, making them ideal for cockpits, partitions, and floors, while enhancing strength, comfort, and energy efficiency.
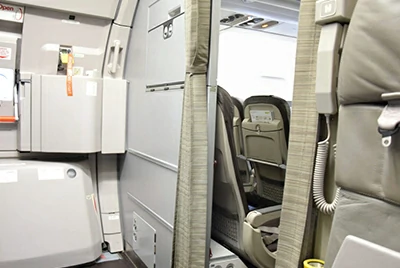
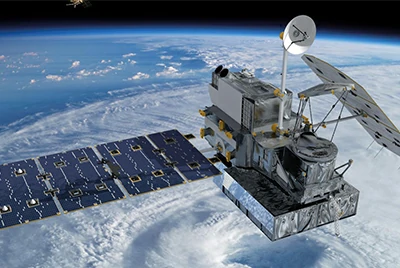
Aerospace
In aerospace, brazed honeycomb panels are used in rockets and satellites for their high temperature, fire, and impact resistance. They ensure structural stability in extreme conditions and vibrations, while their corrosion resistance and environmental properties meet strict material standards, enhancing the lifespan and safety of aircraft.
Space equipment
Brazed honeycomb panels are used in space telescopes for their high light-to-strength ratio and low thermal expansion, ensuring shape stability in extreme cold. These properties help maintain optical accuracy during temperature changes, resulting in clearer imaging.
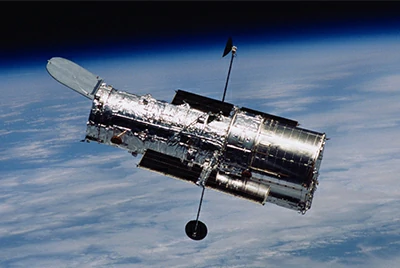
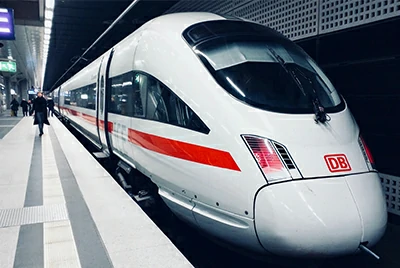
Rail Transit
Brazed honeycomb panels are lightweight and strong, reducing vehicle weight to improve fuel efficiency and lower energy consumption. Their sound and heat insulation enhance passenger comfort, while their fire and impact resistance make them ideal for high-speed rail and subway interiors and exteriors.
Military
In the military, brazed honeycomb panels are used in vehicles and equipment for their strength, fire resistance, and impact resistance. They are ideal for lightweight protective panels in fighter jets and armored vehicles, enhancing durability and protection against vibrations and impacts in combat environments.
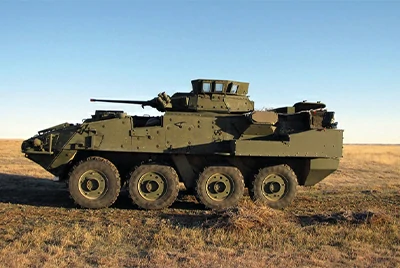
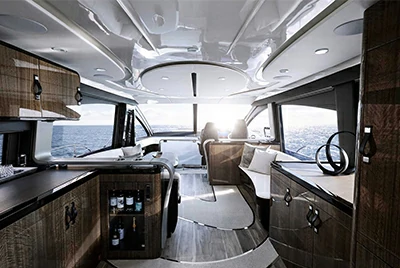
Marine vessels
In marine vessels, brazed honeycomb panels are used in hull structures and interiors. Made from corrosion-resistant aluminum alloys, they reduce weight and enhance sound and heat insulation. These panels improve hull strength and extend the ship's service life.
Architecture
Brazed honeycomb panels are used in construction for curtain walls and interior decoration, offering flatness, light weight, and strength. Their fire resistance, environmental benefits, and wind pressure resistance make them ideal for high-rise facades, while the brazing process enhances both safety and aesthetic flexibility.
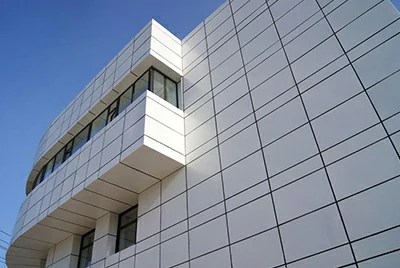
Aluminum brazed honeycomb panel production process revealed
Brazing is the process of joining two metals together through the melting and flow of a filler metal. The filler metal itself has a lower melting point, so the base metal does not melt during the process.
Chalco applies this technology to transform adhesive honeycomb panels and aluminum alloy honeycomb composite panels into completely adhesive-free products. By applying a temperature of 580-600 degrees Celsius and nitrogen oxide protection, the two aluminum skins are completely welded together with the honeycomb core/metal core , achieving stronger mechanical properties and self-verified fire safety.
Surface treatment of materials before brazing:
The honeycomb core and face sheet are cleaned and treated to remove the oxide layer to ensure the bonding quality during brazing. Surface treatment often includes degreasing, pickling, etc. to improve the brazing wettability between materials.
Component assembly:
- Precise alignment of honeycomb core and face sheet: Before brazing, the honeycomb core is sandwiched between two face sheets to ensure that all components are positioned precisely so that the brazing material during the brazing process evenly fills the joint surface.
- Brazing material coating: Brazing material is evenly applied between the honeycomb core and the face sheet. This step ensures that the brazing material can fully flow when heated, fill the interface and be evenly distributed.
Vacuum brazing process:
- Principle: Vacuum brazing is to heat the brazing material (usually an aluminum-based alloy) to its melting point in a vacuum environment, so that it melts and fills the joint between the honeycomb core and the aluminum face plate. Due to the vacuum conditions, no oxidation occurs during the brazing process, ensuring a clean and strong joint.
- Purpose: The purpose of vacuum brazing is to achieve molecular-level metallurgical bonding of the brazing material through high temperature, and firmly weld the honeycomb core and the aluminum panel together. The bond formed in this way is stronger than that of the adhesive process and can withstand higher mechanical stress.
- Temperature control: Brazing temperature (usually around 600°C) needs to be strictly controlled. Too high a temperature may damage the aluminum structure, while too low a temperature may not completely melt the brazing material, resulting in uneven welding and affecting bonding strength.
Cooling and removal:
After brazing, slow cooling is required to avoid residual stress or deformation caused by sudden temperature drop and ensure the stability and structural integrity of the honeycomb panel.
Quality Inspection:
After cooling, the honeycomb panels are strictly tested, including peel strength, compressive strength, flatness, fire resistance, sound insulation and other indicators. Only products that meet the design standards and industry specifications will enter the next step.
Subsequent processing and surface treatment:
According to customer needs, the brazed honeycomb panels can be surface treated (such as spraying, anodizing) and further processed (cutting, punching, etc.) to ensure that their appearance and size meet the use requirements.
Chalco's ongoing R&D in the field of brazed composite aluminum panels
Based on the successful development of welded aluminum honeycomb sandwich panels, Chalco has successfully developed a variety of welded light metal structural materials: pure metal foam aluminum sandwich panels, corrugated sandwich panels, ultra-thin sandwich panels, honeycomb energy-absorbing materials, etc. This material can be widely used in train energy absorption, automobile energy absorption and passive protection of important facilities.
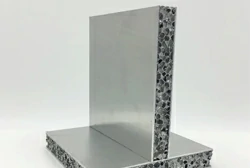
Foam aluminum sandwich board panel plate
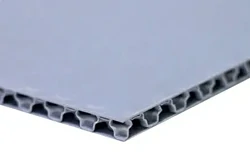
Corrugated sandwich board panel plate
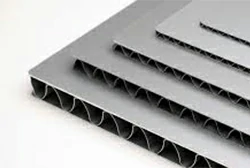
Ultra-thin sandwich board panel plate