Carbon-coated aluminum foil is an advanced negative electrode current collector designed for high-performance battery systems. By applying a uniform conductive carbon layer on high-purity aluminum foil, it effectively prevents corrosion and enhances adhesion between the electrode material and the current collector, ensuring battery stability and reliability.
Compared to traditional aluminum foil, carbon-coated aluminum foil offers superior electrical conductivity and reduced internal resistance, effectively lowering interface contact resistance and inhibiting lithium dendrite growth, which significantly reduces the risk of short circuits and improves battery safety.
Our carbon-coated aluminum foil employs advanced coating processes and precise quality control procedures, meeting IATF 16949 and ISO 9001 quality standards. We strictly adhere to the GB/T 36147 national standard, with precise control over coating thickness, electrical conductivity, and adhesion. All products undergo ASTM D3359 adhesion testing to guarantee long-term stability. Chalco's carbon-coated aluminum foil is the ideal choice for improving battery output power and optimizing durability.Welcome to Contact
Specifications of carbon coated aluminum foil
Aluminum Foil Substrate | 1060, 1070, 1080, 1100, 1235t, 1235t3 |
Aluminum Foil Substrate Thickness | 16µm |
Coating | Carbon Black, Graphite Flakes, Graphene |
Coating Thickness | 1 Μm On One Side/2*1 Μm On Both Sides |
Total Thickness | 18µm |
Aluminum Foil Width | 260mm |
Coating Width | 230mm |
Coating Type | Aqueous Solvent |
Coated Surface | One Side Or Both Sides |
Density | 0.5-2.0g/M2 |
Surface Conductivity | <30ω/25µm2 |
Length | 80-90m |
Weight | 1kg/Roll |
Advantages of carbon coated aluminum foil
The advantages of carbon-coated aluminum foil include enhancing battery energy density, suppressing battery polarization, reducing internal resistance, and increasing battery cycle life. Currently, it is particularly prominent in the field of lithium iron phosphate batteries. With the increasing demand for battery energy density, the market for carbon-coated aluminum foil continues to grow and has been widely applied in most power lithium batteries.Quick Quote
- Suppression of Battery Polarization and Improved Rate Performance: Carbon-coated aluminum foil effectively reduces battery polarization, lowers heat effects, and enhances the rate performance of the battery.
- Reduction of Internal Resistance: By minimizing the dynamic internal resistance amplification during the cycling process, carbon-coated aluminum foil decreases the internal resistance of the battery.
- Prolonged Cycle Life: Carbon-coated aluminum foil contributes to improved battery consistency, extending the cycle life of the battery.
- Increased Adhesion: Enhanced adhesion between active materials and the current collector reduces the manufacturing cost of electrode sheets and diminishes the amount of binder used.
- Protection Against Corrosion of the Current Collector: Carbon-coated aluminum foil efficiently prevents the corrosion of the current collector in the electrolyte, thereby extending the battery's lifespan.
- Improved Material Processing Performance: For materials like lithium iron phosphate and lithium titanate, carbon-coated aluminum foil helps improve their processing performance.
Carbon Coating Material Selection
The choice of carbon coating materials is crucial for the conductivity and adhesion of aluminum foil. Common carbon coating materials include carbon black, graphite, carbon nanotubes, graphene, and reduced graphene oxide.
By combining various types of carbon materials, the conductive performance of the coating can be significantly enhanced, reducing the internal resistance of the battery and improving charge/discharge efficiency.
Carbon black and graphite are widely used in industrial production due to their good processability, while carbon nanotubes and graphene further enhance the coating's electrical conductivity, flexibility, and scratch resistance.
Aluminum Foil Types | Peel strength(N/cm) | Rs(Ω) | Rct(Ω) |
Aluminum Foil | 4.9 | 4.37 | 156.2 |
Carbon Black Coated Aluminum Foil | 6.5 | 2.96 | 121.4 |
Graphite Coated Aluminum Foil | 14.5 | 2.66 | 90.3 |
Name | Coating Material | Coating Thickness/Μm | Areal Density | Lifepo4 Peel Strength/(Mn·Mm-1) | Internal Resistance/Mω |
Aluminum Foil | - | - | /(G·M-2) | 290 | 2.5-4.1 |
Carbon Coated Aluminum Foil | Carbon Black, Graphene | 1.5-3.0 | - | 315 | 1.1 |
Carbon Coated Aluminum Foil | Carbon Black, Graphene | 1.7-2.6 | 0.9 | 313 | 1.4 |
Carbon Coated Aluminum Foil | Carbon Black, Graphene | 1.6-2.5 | 1.1 | 316 | 1.3 |
Carbon Coated Aluminum Foil | Carbon Black, Graphene | 1.5-2.5 | 1.3 | 311 | 1.5 |
Recommendations products for carbon coated aluminum foil related
Production process of carbon coated aluminum foil
The manufacturing process of carbon-coated aluminum foil typically involves two main stages: bare foil manufacturing and coating application.
Bare Foil Manufacturing
Firstly, the aluminum foil is produced using the cast rolling-cold rolling process, where raw aluminum ingots and billets are cast into rolled aluminum coils, which are then processed through cold rolling, intermediate annealing, and foil rolling to produce battery-grade aluminum foil.
During this process, parameters such as rolling force, rolling speed, and annealing temperature play a significant role in ensuring the consistency and yield of the aluminum foil. To meet the market's demand for higher lithium battery energy density, the trend towards thinner aluminum foil is increasingly evident.
Coating Application
After bare foil manufacturing, the coating application begins. The carbon coating is applied by evenly covering the aluminum foil surface with conductive carbon slurry. This slurry typically includes conductive materials such as carbon black, graphite flakes, and graphene, which are mixed with film-forming agents, solvents, and additives to create a dense carbon-coated layer. This coating improves the adhesion between the aluminum foil and electrode materials while also reducing internal resistance.
The conductive carbon slurry can be applied using surface coating technology or CVD (Chemical Vapor Deposition) technology. Surface coating is suitable for larger carbon particles like carbon black and graphite and is characterized by its simplicity and controllability. On the other hand, CVD technology involves generating the carbon coating through a gas-phase reaction, making it particularly suitable for fine materials like graphene and carbon nanotubes, thus achieving superior coating uniformity and performance.
By applying surface treatment and carbon coating to bare aluminum foil, not only is the conductivity and adhesion strength of the aluminum foil significantly enhanced, but the internal polarization effect of the battery is also effectively reduced, improving high-rate charge and discharge performance. Additionally, the conductive carbon coating reduces the amount of binder required, thus lowering production costs and improving the overall performance of the battery.
Applications of Carbon Coated Aluminum Foil
Lithium-Ion Batteries and Lithium-Sulfur Batteries: Carbon coated aluminum foil is used as the current collector in lithium-ion and lithium-sulfur batteries. It enhances the adhesion between the electrode material and the current collector, reduces internal resistance, and improves both charge/discharge efficiency and cycle life. This makes it highly suitable for high-energy-density batteries.
Electric Vehicle Power Batteries (EV, HEV): In the power batteries of electric vehicles, carbon coated aluminum foil effectively reduces the internal resistance, suppresses the growth of lithium dendrites, minimizes the risk of short circuits, extends battery life, increases driving range, making it ideal for high-rate charge and discharge requirements.
Functional Solid Polymer Capacitors: Carbon coated aluminum foil is used as an electrode material in solid polymer capacitors, improving capacity and current handling capabilities, ensuring the stability of the capacitor's performance.
Aluminum Electrolytic Capacitors: In aluminum electrolytic capacitors, carbon coated aluminum foil enhances conductivity and corrosion resistance, ensuring excellent performance under high-frequency and high-temperature conditions.
High-Efficiency Energy Storage Systems: By reducing internal resistance and polarization effects, carbon coated aluminum foil improves the efficiency of charge and discharge processes and the energy output in energy storage systems, making it suitable for both residential and industrial energy storage scenarios.
High Power Industrial Applications: In high power applications such as industrial energy storage and base station power supply, carbon coated aluminum foil ensures efficient energy transmission under high current conditions and exhibits excellent corrosion resistance and stability, even in harsh environments.
Chalco Complete Solution for New Energy Power Batteries
Power Battery Aluminum Material
Power battery shell:1050 3003 3005
Power battery tray:6061
Power battery cover plate:3003, 5182
Contact us now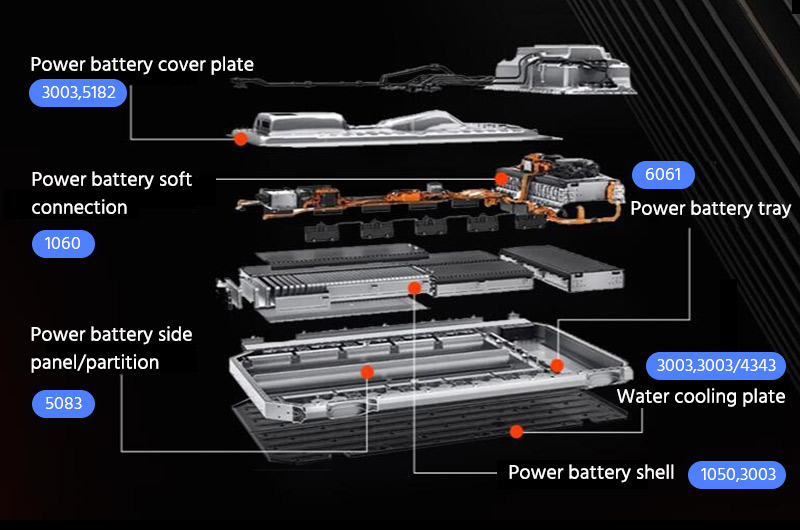
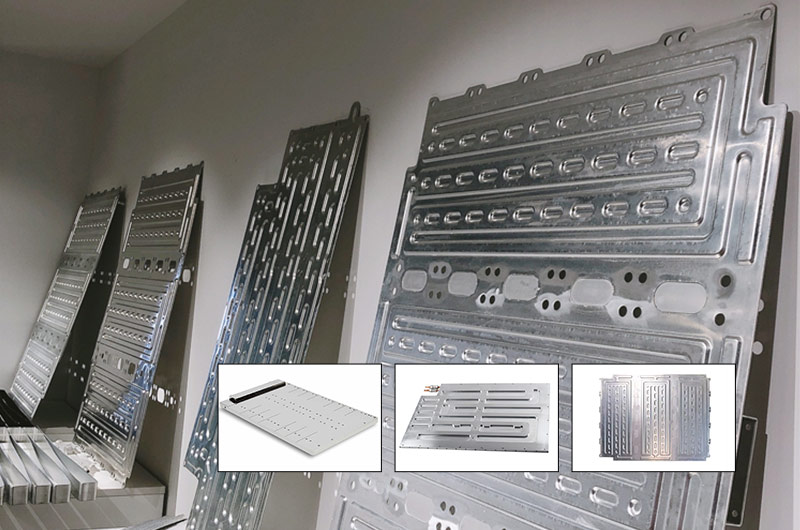
Power Battery Liquid Cold Board
3003/4045 brazing aluminum plate
3003/4343 brazing aluminum plate
3003mod/4343 brazing aluminum plate
3003/4004 brazing aluminum plate
Contact us now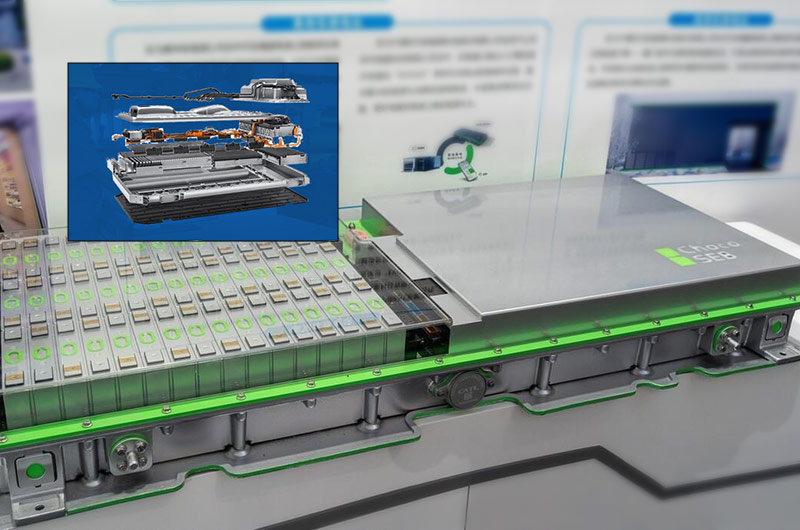
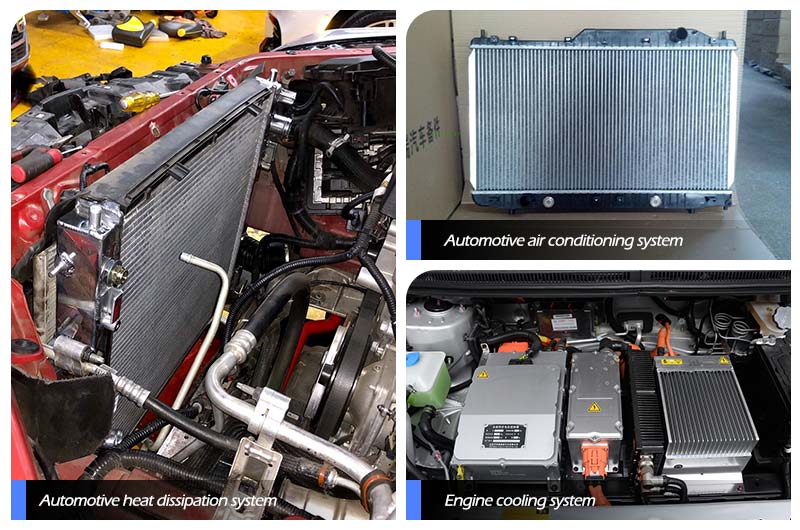
Substrate:3003
Brazing layer:4004, 4045, 4104, 4343
Application:Radiator, cooling, Air-conditioning system
Contact us nowWhy choose Chalco's carbon-coated aluminum foil?
- Ultra-thin Coating Technology: Utilizing ultra-thin coating technology to ensure high performance while controlling coating thickness between 0.3µm to 2µm.
- High Thermal Conductivity: Uniformly applying nanocarbon materials to enhance thermal conduction, converting it into infrared RF to boost heat dissipation efficiency.
- Strong Stability: Possessing extremely high chemical stability, resistant to NMP, ensuring battery safety performance.
- Good Nocturnal Stability: Protecting the current collector from electrolyte corrosion, with excellent wetting properties.
- High Coating Adhesion: Enhancing energy density, durable over time, with no foil exposure after 200 wipes.
- Excellent Barrier Performance: Uniform coating to prevent corrosion and oxidation of the current collector, extending battery lifespan.
- Quality Assurance: Vertical integration strategy and a quality control system monitor each production step.
- Diverse Customization Support: Available for continuous/interrupted, single/double-sided coating, providing differentiated customization to meet various needs.
Properties of carbon coated aluminum foil substrate
Alloy | 1235 T | 1235 T3 | 1100 | 1060 |
Tensile Strength Mpa | ≥200 | ≥240 | ≥240 | ≥200 |
Elongation % | ≥2.0 | ≥2.5 | ≥3.0 | ≥3.0 |
Surface Tension Mn/M | ≥31 | ≥31 | ≥31 | ≥31 |
Thickness And Deviation Μm | 9-25;±4% | |||
Width And Deviation Mm | 200-1400;±1 | |||
Pinholes/M2 | Diameter 0.1-0.3mm; <3 | |||
Plate Shape | With a flat sheet | |||
Surface Quality | No oil, no roller marks, no oxidation, no foreign matter pressed in and other defects that affect use | |||
End Surface Quality | No staggered layers, tower type, burrs ≤50µm, gaps ≤50µm | |||
Weight Per Roll Kg | 50-500kg | |||
Roll Diameter Mm | 76.2±1/152±1 | |||
Environmental Requirements | Comply with ROHS standards |
Mechanical properties of carbon coated aluminum foil substrate
Alloy | Temper | Thickness/mm | Room temperature tensile testing results | ||||
Tensile strength (Rm) MPa | elongation after break (A100) % | elongation after break (A50) % | |||||
Single side light aluminum foil | Double side light aluminum foil | Single side light aluminum foil | Double side light aluminum foil | ||||
1050 | H18 | >0.013-0.015 | - | - | - | - | - |
1050 | H18 | >0.015-0.020 | ≥185 | ≥2.0 | - | - | - |
1050/1060 | H18 | ≤0.010 | - | - | - | - | - |
1050/1060 | H18 | ≤0.010 | - | - | - | - | - |
1050/1060 | H18 | >0.010-0.013 | ≥190 | - | ≥2.5 | - | ≥3.0 |
1050/1060 | H18 | >0.013-0.015 | - | - | - | - | - |
1070 | H18 | ≤0.010 | ≥185 | - | ≥2.0 | - | - |
1070 | H18 | >0.010-0.013 | - | - | - | - | - |
1070 | H18 | >0.013-0.015 | ≥180 | - | - | - | - |
1070 | H18 | >0.015-0.020 | ≥175 | - | - | - | - |
1100 | H18 | ≤0.010 | ≥230 | ≥1.0 | ≥2.0 | - | ≥3.0 |
1100 | H18 | >0.010-0.013 | - | - | - | - | - |
1100 | H18 | >0.013-0.015 | ≥220 | - | - | - | - |
1100 | H18 | >0.015-0.020 | - | - | ≥2.0 | - | - |
1235 | H18 | ≤0.010 | - | - | - | - | - |
1235 | H18 | >0.010-0.013 | ≥180 | - | - | ≥2.0 | - |
1235 | H18 | >0.013-0.015 | ≥185 | - | - | - | - |
1235 | H18 | >0.015-0.020 | ≥175 | - | - | - | - |
Carbon-Coated Aluminum Foil FAQ
Question: What is Carbon Coated Aluminum Foil, and why is it important in batteries?
Answer: Carbon coated aluminum foil is a current collector with a conductive carbon layer evenly coated on the surface of aluminum foil. It is widely used in lithium-ion and lithium-sulfur batteries. It significantly reduces interfacial resistance, and enhances adhesion between the electrode material and the current collector, thus improving charge/discharge efficiency and cycle life of the battery.
Question: How is the conductivity of carbon coated aluminum foil, and how does it impact battery performance?
Answer: Carbon coated aluminum foil has excellent conductivity, and the carbon layer significantly reduces the internal resistance of the battery current collector. Better conductivity leads to higher charge/discharge efficiency, effectively reducing the growth of lithium dendrites and minimizing the risk of short circuits.
Question:Does the coating thickness of carbon coated aluminum foil affect its performance?
Answer:Yes, the coating thickness directly affects conductivity and adhesion. Typically, the coating thickness is between 1.5 to 3.0 microns, ensuring uniformity and conductivity while also enhancing bonding strength with electrode materials.
Question:How is the corrosion resistance of carbon coated aluminum foil?
Answer:The application environment for carbon coated aluminum foil in batteries is often harsh, especially under high temperature and high humidity conditions. The carbon coating effectively protects the aluminum foil, preventing electrolyte corrosion, thus improving battery reliability and lifespan.
Question:What are the advantages of carbon coated aluminum foil compared to traditional bare aluminum foil?
Answer:Compared to traditional bare aluminum foil, carbon coated aluminum foil has lower interfacial resistance and higher conductivity, leading to better charge/discharge performance. Additionally, the carbon coating reduces the use of binders, lowers production costs, and suppresses the growth of lithium dendrites, thereby enhancing battery safety.
Question:What is the production process for carbon coated aluminum foil?
Answer: The production of carbon coated aluminum foil involves two main steps: base foil production and coating. First, bare aluminum foil is produced using a casting and rolling process, then a conductive carbon slurry is uniformly coated onto the aluminum surface, and dried to form a dense carbon layer.
Question: What challenges may be encountered in the production process of carbon-coated aluminum foil?
Answer: Challenges in the processing of water-based slurries include issues such as bubbles, shrinkage holes, and sagging, which may constrain the production process of carbon-coated aluminum foil.
Question: What are the important factors to consider when purchasing carbon coated aluminum foil?
Answer: When purchasing, focus on coating thickness, conductivity, peel strength, corrosion resistance, and quality certifications. The coating thickness affects both conductivity and adhesion, and higher peel strength ensures better stability during charge and discharge cycles. It is also crucial to select products certified by industry standards such as IATF 16949 and ISO 9001.
Chalco can provide you the most comprehensive inventory of aluminum products and can also supply you customized products. Precise quotation will be provided within 24 hours.
Get a quote