Aluminum, known for its excellent machinability and strength-to-weight ratio, has become a favorite material across industries. At Chalco, we leverage advanced CNC router for aluminum and a professional engineering team to provide comprehensive aluminum CNC machining services. From prototype validation to mass production, we customize custom aluminum machining parts to meet your design needs, helping you accelerate time-to-market and reduce overall costs.Welcome to Contact
In this comprehensive guide, we'll delve into aluminum's properties, the CNC aluminum milling machine process, common challenges, and effective strategies. Let's explore how to unlock the potential of the best aluminum for machining to create lighter, stronger, and more competitive products.
- What is CNC aluminum machining?
- CNC aluminum machining services
- Most common aluminum products for CNC machining
- Best aluminum alloys for CNC machining
- Surface finishing options for CNC machining
- Top applications of CNC aluminum machining
- Case studies in CNC aluminum machining
- Why choose us as your CNC aluminum machining partner
What is CNC aluminum machining?
CNC aluminum machining is an advanced subtractive manufacturing process that utilizes computer numerical control (CNC) machines and pre-programmed codes (such as G-codes) to remove excess material from solid aluminum blocks. This precise process produces high-quality aluminum alloy parts with strict tolerance requirements.
At Chalco, we specialize in custom CNC aluminum machining, leveraging cutting-edge equipment like CNC aluminum milling machines and CNC routers for aluminum. Our expertise ensures every machined aluminum part meets the highest standards of precision and quality.
Why aluminum for CNC machining?
Compared to other lightweight metals such as magnesium alloys and titanium alloys, aluminum is the most popular material for CNC machining due to its unique combination of properties:
- Lightweight yet Strong: Ideal for weight-sensitive applications without compromising durability.
- Highly Formable: Offers excellent machinability, enabling complex and intricate designs.
- Easy to Cut: Reduces machining time and enhances cost-efficiency.
CNC aluminum machining services
In CNC aluminum machining, selecting the appropriate machining process is critical for achieving high precision and efficiency. Below are the primary CNC machining processes and their key characteristics:
CNC milling
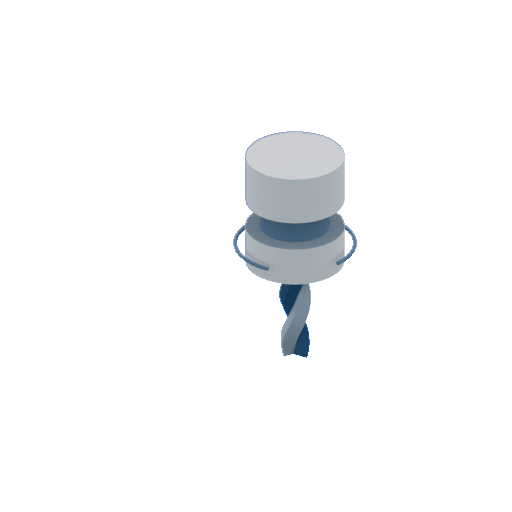
CNC milling utilizes a rotating multi-point cutting tool to remove material in multiple directions, while the workpiece remains stationary along its axis. This method is ideal for rapidly machining flat surfaces, cavities, curves, and complex geometries for prototypes and production parts. At Chalco, our high-precision CNC milling achieves accuracies of up to 0.008 mm, with milling components ready in as little as one day.Custom aluminum parts
Milling Equipment
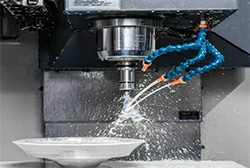
3-Axis CNC Milling
The most common type of CNC milling machine.Capable of processing the majority of parts with high precision at a low cost.
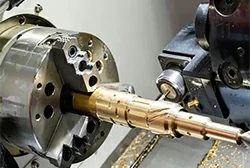
4-Axis CNC Milling
Ideal for multi-surface machining or parts requiring curved surface processing.Offers greater flexibility but at a slightly higher cost.
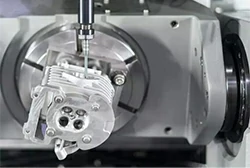
5-Axis CNC Milling
Ideal for complex shapes, curved surfaces, and precision parts with multi-directional processing. Higher cost, but unmatched versatility.
CNC Milling Functional Parameters
Alloy material | 6061, 7075, 2024, 5083, 5052, 6082, etc. |
Maximum size | 4000x1500x800mm |
Minimum part size | 5x5x5mm |
Minimum wall thickness | ≤0.5mm |
Tolerance | The thicker the wall, the better the structural integrity. |
Radius | +/- 0.01mm or 0.0004” |
Hole | The inner radius should be at least 1/3 of the cavity depth. Use a larger radius as much as possible. |
Threaded and tapped holes | Minimum hole diameter ≥0.8mm, hole depth should not exceed 4 times the hole diameter in principle. |
Delivery time | Diameter: 1.5-5mm, depth: diameter*3; |
CNC turning
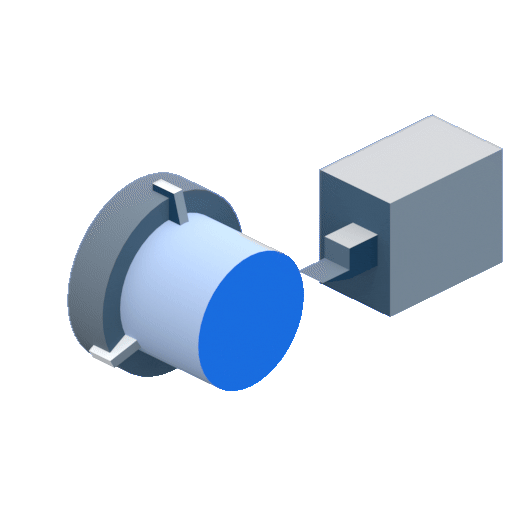
CNC Turning removes material from a workpiece by rotating it at high speeds while a single-point cutting tool moves along its axis. This process is ideal for creating cylindrical, conical, and threaded shapes. Known for its high precision and efficiency, CNC turning is widely used for producing complex rotational aluminum components.Custom aluminum parts
Types of CNC Turning Processes
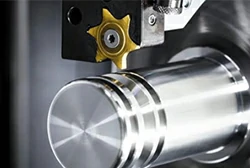
Grooving
Involves pressing a specially shaped tool into the workpiece to form narrow cavities.Commonly used for precision slots and grooves.
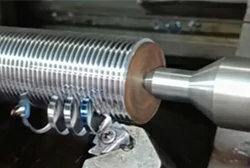
Threading
A specialized CNC turning technique for producing threads, enabling components to be screwed into other objects.Essential for manufacturing bolts, screws, and fasteners.
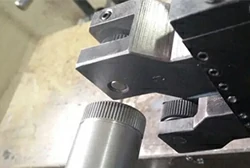
Knurling
Creates a serrated pattern on the workpiece surface to enhance grip, particularly for tools or handles requiring added traction.
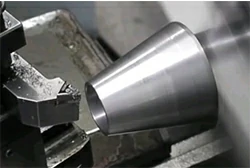
Taper Turning
Shapes cylindrical components with gradually reducing diameters, forming a tapered or conical profile. Ideal for shafts, spindles, and similar components.
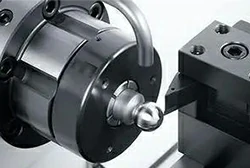
Spherical Generation
Produces a perfect spherical shape by systematically reducing the diameter around a fixed axis.Often used for ball joints or precision bearings.
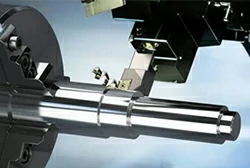
Cylindrical Turning
A process to uniformly reduce the diameter of the workpiece, maintaining a consistent cut throughout.Prevents variations and ensures high precision.
CNC Turning Functional Parameters
Alloy material | 6061, 7075, 2024, 5083, 5052, 6082, etc. |
Maximum part size | Diameter: 500mm (19.7”), length 1500mm (59”); |
Minimum part size | Diameter: 1mm |
Minimum wall thickness | ≤0.5mm or 0.02 |
Minimum hole diameter | ≥0.5mm |
Radius | Hole depth should maintain a 1:10 diameter-to-depth ratio to avoid tool deflection |
Tolerance | Minimum internal radius is 0.5mm, ≥3mm radius can improve tool contact and reduce part stress concentration. |
Threaded and tapped holes | +/- 0.01mm or 0.0004” |
Text | External and internal threads can be accurately cut. Standard thread sizes are from M1.6 and above. Ensure that the minimum thread length is 1.5 times the diameter to ensure stability. |
Delivery time | The height of the engraved characters should be at least 2mm and the depth should be at least 0.5mm to ensure clear and easy to read after processing. |
Other auxiliary or special CNC aluminum processes
In addition to traditional turning and milling, CNC aluminum machining incorporates several specialized processes to meet diverse manufacturing needs:
- Drilling: Vertical drill bits precisely cut along straight paths to create holes and threads in the workpiece. Ideal for applications requiring CNC drilling services, such as products designed to house screws and bolts.Drilling service
- Pocketing: Also known as pocket milling, this process involves creating recessed areas inside a part to form internal cavities or complex structures.
- Facing: End milling techniques are used to create flat cross-sectional areas on the surface of the workpiece, ensuring surface flatness and dimensional accuracy.
For rapid cutting or 2D shaping tasks, such as waterjet cutting, laser cutting, and plasma cutting, visit our Cutting Processes page to explore more options.Cutting service
By leveraging these multi-axis CNC milling techniques and CNC precision capabilities, CNC aluminum machining enables the production of high-precision aluminum parts, effectively meeting the varied demands for high-performance aluminum components across industries.
Are You Looking for an Aluminum Supplier?
If you need a professional aluminum supplier to provide you with high-quality, cost-effective aluminum, we will be your best choice.
Most common aluminum products for CNC machining
Different shapes and types of aluminum are widely used in CNC machining based on their unique properties and application requirements. Below are some of the most common CNC aluminum workpiece materials we handle:
CNC aluminum alloy selection for machining
-
Aluminum EN-AW 6061 | 3.3211| AlMg1SiCu
Known as a universal alloy, 6061 aluminum offers excellent machinability and corrosion resistance, making it ideal for electrical components, brake pistons, and bicycle frames. As one of the most popular alloys in CNC aluminum machining, 6061-T6 grade is a top choice in the aerospace and automotive industries due to its high strength and heat treatability.
EN 485 EN 570 ASTM B209 AMS 4025 AMS 4026 AMS 4027 AMS-QQ-A-250/11 -
Aluminum EN-AW 7075 | 3.4365 | AlZn5, 5MgCu
A high-strength alloy, 7075 aluminum is renowned for its superior fatigue resistance, often used in aerospace and military applications such as aircraft parts and missile components. Despite lower corrosion resistance, its exceptional strength-to-weight ratio makes it ideal for high-stress environments. 7075-T6 grade is widely utilized in high-performance machinery and sports equipment, where extreme strength and precision are required.
EN 485 ASTM B209 AMS 4044 AMS 4045 AMS 4078 AMS-QQ-A-250/12 -
Aluminum EN-AW 6082 | 3.2315 | AlSi1MgMn
The strongest alloy in the 6000 series, 6082 aluminum offers excellent corrosion resistance and machinability. With high tensile strength and good toughness, this alloy is widely used in CNC aluminum machining, particularly for high-load structures and applications in corrosive environments.
EN 485 EN 570 -
Aluminum EN-AW 2024| 3.1355 | AlCu4Mg1
Known for its outstanding fatigue resistance and high strength-to-weight ratio, 2024-T3 aluminum is extensively applied in the aerospace and automotive sectors. While its corrosion resistance is relatively poor, performance can be enhanced through heat treatment and surface coatings. This alloy excels in high-stress applications, meeting the demands of reliability and strength.
EN 485 ASTM B209 AMS 4035 AMS 4037 AMS 4193 AMS 4297 AMS-QQ-A-250/4 -
Aluminum EN-AW 3003| 3.0517 | AlMn1Cu
As a nearly pure aluminum alloy with added manganese for enhanced strength, 3003 aluminum offers excellent formability and corrosion resistance. Its non-heat-treatable nature makes it ideal for radiators, HVAC systems, and chemical equipment. This versatile alloy is a favorite in aluminum machining for applications requiring superior formability.
EN 485 EN 570 ASTM B209 AMS 4006 AMS 4008 AMS-QQ-A-250/2 -
Aluminum EN-AW 5052 | 3.3523 | AlMg2, 5
Renowned for its high corrosion resistance and good formability, 5052 aluminum is the preferred material for fuel tanks, sheet metal parts, and fuel lines. Though non-heat-treatable, its high fatigue strength makes it ideal for marine and saltwater environments.
EN 485 ASTM B209 AMS 4015 AMS 4016 AMS 4017 AMS-QQ-A-250/8 -
Aluminum EN-AW 5083| 3.3547 | AlMg4.5Mn0.7
Known as a marine-grade alloy, 5083 aluminum provides exceptional corrosion resistance and high strength, excelling in low-temperature environments. Often used in shipbuilding, offshore structures, and storage tanks, this alloy ensures outstanding performance under harsh conditions.
EN 485 ASTM B209 AMS 4056 AMS-QQ-A-250/6 -
MIC-6
A non-heat-treatable alloy designed for high-precision parts, MIC-6 aluminum offers excellent stress-relief properties and superior machinability. Its precision and stability make it a top choice for electronics and laser technologies, ensuring high tolerance and mechanical performance in CNC aluminum machining.
In addition to the commonly used aluminum alloys, Chalco offers a variety of additional options to meet specific industry requirements.Choose materials
-
Aluminum 1100
Pure aluminum with excellent corrosion resistance and machinability, ideal for complex forming tasks.
-
Aluminum 2007
High-strength copper-aluminum alloy, excellent for fasteners and precision parts.
-
Aluminum 2011
Easy-to-machine alloy with good conductivity, commonly used in appliance components and automotive trims.
-
Aluminum 2014
High strength and machinability, suitable for aircraft parts and high-stress components.
-
Aluminum 2017
A heat-treatable alloy with superior ductility, widely applied in aerospace and military equipment.
-
Aluminum 5754
A durable aluminum-magnesium alloy for marine and automotive applications.
-
Aluminum 6060
Known for its formability and corrosion resistance, often used in construction and medical equipment.
-
Aluminum 6063
Exceptional machinability and corrosion resistance, preferred for pipes, railings, and architectural designs.
-
Aluminum 7050
High-strength alloy with superior fatigue resistance, used in aerospace and defense applications.
Find the Perfect Aluminum Alloy
With these diverse options, CNC aluminum machining can deliver high-quality, precision parts tailored to any industry's needs. To save time, refer to our comprehensive aluminum alloy chart for quick selection of the ideal material. Quick Quote
Alloy | Cost | Strength | Machinability | Corrosion Resistance | Fatigue Resistance | Endurance |
1100 | $ | Low | Excellent | Excellent | Low | Low |
2007 | $$ | High | Excellent | Poor | Moderate | High |
2011 | $ | High | Excellent | Moderate | Moderate | Limited |
2024 | $$$ | Highest | Good | Poor | Excellent | High |
3003 | $ | Moderate | Limited | Good | Limited | Limited |
5052 | $ | Moderate | Moderate | Good | Moderate | Limited |
5083 | $$ | High | Limited | Excellent | Moderate | Limited |
5754 | $$ | High | Moderate | Excellent | Moderate | Moderate |
6060 | $$ | Moderate | Excellent | Good | Moderate | Moderate |
6061 | $$ | High | Excellent | Excellent | Good | Moderate |
6063 | $ | Moderate | Excellent | Excellent | Moderate | Limited |
6082 | $$ | High | Excellent | Moderate | Good | Moderate |
7050 | $$$ | Highest | Limited | Good | Excellent | High |
7075 | $$$ | Highest | Limited | Good | Excellent | High |
MIC-6 | $$ | Moderate | Excellent | Good | High | Moderate |
CNC machining surface finishes
Surface finishing technologies enhance the corrosion resistance, hardness, and aesthetic appeal of CNC aluminum parts. Here are the most common surface finishing methods and their key characteristics:
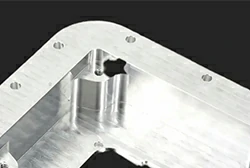
As-Machined
The surface directly from the CNC machine retains tool marks without further treatment, making it a cost-effective option.
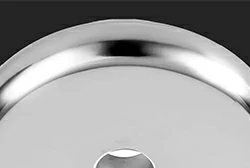
Polishing
Uses mechanical force to improve surface smoothness, ideal for aluminum parts requiring high surface quality.
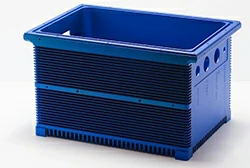
Anodizing
An electrochemical process that creates an oxide layer on the aluminum surface, improving corrosion resistance and hardness. It can also be dyed in various colors.
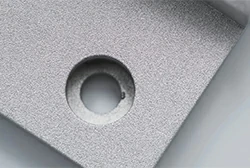
Sandblasting
Shoots fine media particles at high speeds onto the part surface to remove burrs and defects, leaving a satin finish.
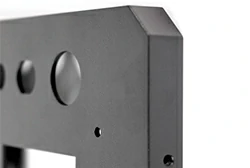
Powder Coating
Uses electrostatically applied polymer powder to form a durable and uniform protective layer, available in a variety of colors.
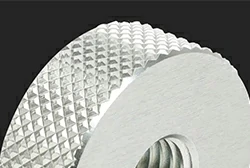
Electroplating
Applies a thin metal layer to the surface, improving wear resistance, corrosion resistance, and surface conductivity.
By integrating these surface finishing techniques, CNC aluminum machining can produce components that combine outstanding performance with attractive aesthetics, meeting the rigorous demands of diverse industries.Customize
Benefits of choosing aluminum for CNC machining
High Strength-to-Weight Ratio
Aluminum alloys are lightweight yet strong, making them ideal for industries like aerospace and automotive, where lightweight structures are critical.
Recyclability
Aluminum is highly recyclable, supporting sustainability and reducing material waste during manufacturing.
Corrosion Resistance
Aluminum naturally forms an oxide layer that offers excellent corrosion protection. Anodizing further enhances this property, making it suitable for harsh environments.
Machinability
Aluminum's excellent machinability, with low cutting forces and high-speed processing, makes aluminum CNC machining highly efficient, reducing production costs.
Quick Turnaround Time
Modern CNC systems and CAM software enable fast production cycles, often delivering finished parts within a week, meeting urgent customer requirements.
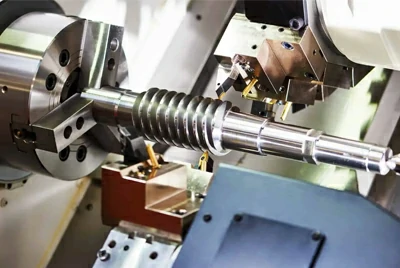
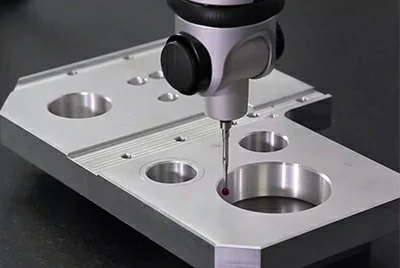
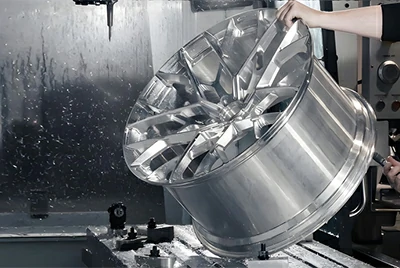

Best application areas for CNC aluminum machining
CNC aluminum machining caters to a wide range of industries, fulfilling diverse demands for high-performance and precision-engineered aluminum components. Below are the key application areas where CNC aluminum machining plays a pivotal role:
Aerospace
The aerospace industry relies heavily on CNC aluminum machining to produce aircraft structural components and turbine parts. The high strength-to-weight ratio and exceptional fatigue resistance of aluminum alloys ensure lightweight and reliable designs, meeting the strict precision requirements of aerospace applications.
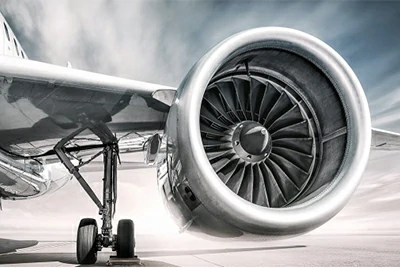
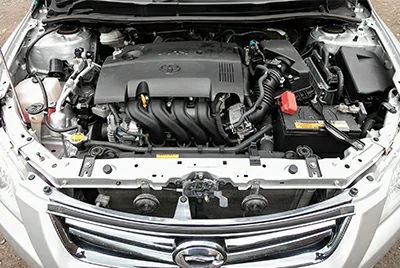
Automotive and Transportation
CNC aluminum machining is widely used in automotive and transportation for engine parts, suspension systems, and railway components. Aluminum lightweight properties enhance fuel efficiency and reduce vehicle weight, while its fatigue resistance ensures component durability and performance.
Consumer Electronics
CNC aluminum machining is common in consumer electronics, producing laptop casings, audio equipment housings, and camera components. Aluminum provides excellent thermal conductivity and a premium look, offering functional and stylish products that meet consumer expectations.
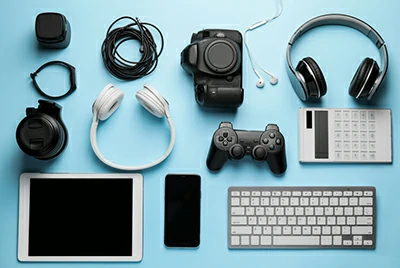
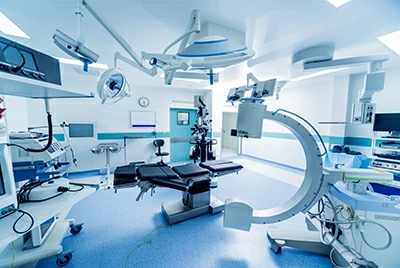
Medical and Food Industry
CNC aluminum machining is common in consumer electronics, producing laptop casings, audio housings, and camera components. Aluminum’s thermal conductivity and premium appearance make products both functional and visually appealing.
Sporting Goods
CNC aluminum machining is used in sporting equipment like bicycle frames, baseball bats, and mountaineering gear. Aluminum alloys’ high strength-to-weight ratio and fatigue resistance make them ideal for lightweight, durable sports gear.
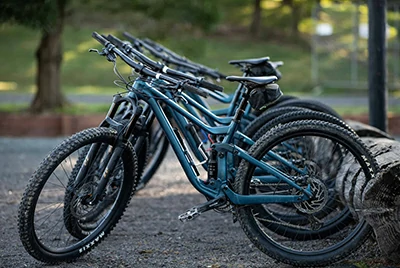
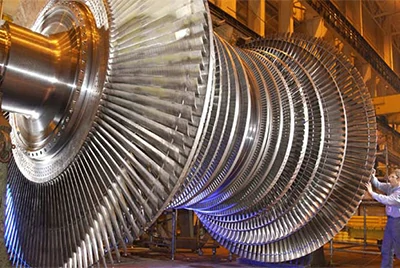
Energy
In the energy sector, CNC aluminum machining is key to producing precision turbine blades and chambers for turbines and reactors. Aluminum’s accuracy and corrosion resistance ensure efficient, reliable energy system operation.
CNC aluminum machining case studies
CNC aluminum machining serves as a cornerstone across industries, delivering custom-engineered aluminum parts that exceed expectations in performance, precision, and durability. Below are examples of CNC aluminum components we have successfully manufactured:
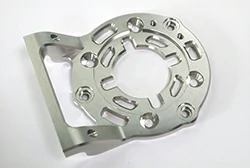
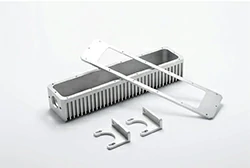
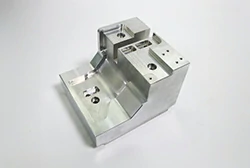
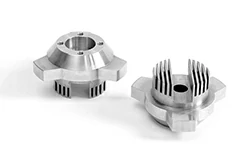
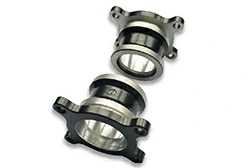
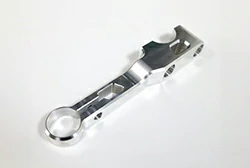
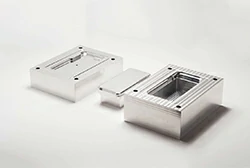
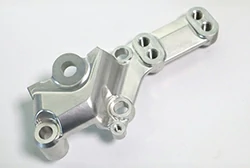
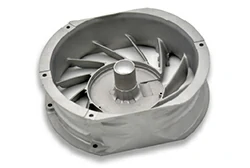
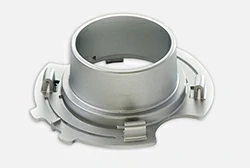
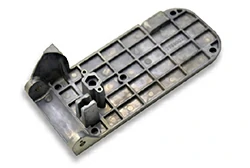
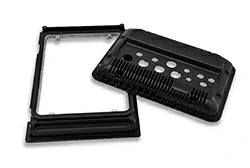
Choose us as your CNC aluminum machining partner
Selecting the right CNC aluminum machining partner is critical to the success of your project. Here's why Chalco should be your top choice:
1. Advanced equipment and expert technical team
- State-of-the-Art Machinery: We operate multiple 5-axis CNC machines and high-precision measuring instruments, including Carl Zeiss coordinate measuring machines (CMM).
- Skilled Engineers: Our experienced engineering team ensures every project meets the highest technical standards and precision requirements.
- In-House Aluminum Stock: We maintain a consistent supply of aluminum materials, ensuring quality control and seamless production.
2. Strict quality control and international certifications
- Certified Quality Management: We are ISO9001 and IATF16949 certified, with a robust quality management system in place.
- Comprehensive Inspection: From raw material checks to final product testing, each stage undergoes rigorous monitoring.
- Precision Lab: Our high-accuracy measurement lab and thorough inspection processes guarantee consistent product quality, meeting and exceeding customer expectations.
3. Extensive industry experience and trusted reputation
- Diverse Expertise: With extensive experience in aerospace, automotive, and consumer electronics, we bring a deep understanding of industry requirements to every project.
- Trusted by Clients: Our commitment to high-quality CNC aluminum machining services has earned us strong customer loyalty and an impeccable reputation.
4. Fast delivery and flexible production capacity
- Rapid Prototyping and High-Volume Production: We excel at handling urgent orders and custom production needs, delivering on time without compromising quality.
- Streamlined Production: Our end-to-end manufacturing service simplifies workflows and boosts efficiency, making us the perfect choice for bulk orders.
5. Comprehensive after-sales support
- Quick Response: Our dedicated support team ensures any issues during use are promptly addressed.
- Warranty and Return Policy: We offer a warranty and hassle-free return options to guarantee long-term product reliability.
- Competitive Pricing: With our in-house aluminum stock and efficient production processes, we provide cost-effective solutions ideal for bulk purchase customers.
Why chalco?
By choosing Chalco as your CNC aluminum machining partner, you gain access to cutting-edge technology, unparalleled expertise, and industry-leading quality standards. From prototyping to large-scale production, we deliver precision-crafted aluminum components tailored to your specific requirements.
Contact us today to discuss your project needs and experience the Chalco difference!
Chalco can provide you the most comprehensive inventory of aluminum products and can also supply you customized products. Precise quotation will be provided within 24 hours.
Get a quote