Chalco offers a full line of aluminum wire products engineered for high-performance rivet and fastener manufacturing. From precision cold heading to corrosion-resistant and conductive applications, our materials support a wide range of mechanical and structural joining solutions in industries such as automotive, aerospace, construction, and electronics.
Whether you are producing lightweight structural rivets or high-strength bolts and screws, Chalco provides the alloys, dimensions, and finishes to meet your technical needs with consistency and efficiency.
Product introduction for Chalco rivet & fastener aluminum wire
Chalco supplies a comprehensive range of aluminum wires tailored for rivet and fastener production:
- Aluminum Wire for Rivets: Cold Heading Quality Aluminum Wire (CHQ), Anti-Corrosion Aluminum Wire...
- Aluminum Wire for Fasteners: Semi-Hard Aluminum Wire (HB), High-Strength Aluminum Wire, Conductive Aluminum Wire, High Temperature Resistant Aluminum Wire...
- Other Metal & Bimetallic Wires: Copper Wire, Steel Wire, Aluminum-Copper Composite Wire...
Alloy: 2000, 3000, 5000, 6000, 7000 series common aluminum alloys; steel wire, titanium alloy wire, copper wire, bimetallic composite aluminum wire
Diameter: Aluminum thin wire (0.127-0.8mm), aluminum wire (0.8-9.5mm), aluminum wire rod (9.5-25mm)
Production method: cold drawing, hot rolling [Click to view production details]
Specification: ASTM B211, ASTM B221, ASTM B316, ASTM B314, ASTM B324, CSA C60889, ASTM B800, GOST 13843-78, IS 5487: 1997
Certifications: ISO 9001:2015, AS9100, DFARS, REACH, RoHS
Surface: anodizing, galvanizing, nickel plating, phosphating, coating, electrochemical polishing …
Aluminum wire for rivets
Chalco supplies precision aluminum wire specifically engineered for the cold heading of solid rivets, blind rivets, and semi-tubular rivets. These wires offer excellent ductility, stable deformation, and corrosion resistance—ideal for lightweight structural joining in aerospace, automotive, construction, and HVAC systems.
-
Cold Heading Quality Aluminum Wire (CHQ)
For solid, blind, and semi-tubular rivets, offering ductility and stability for smooth cold heading.
Typical Alloys 1100, 2117, 5056, 6061-O, 2024
Applications Aircraft rivets, HVAC blind rivets, lightweight structural connections
-
Anti-Corrosion Aluminum Wire
Formulated with special alloying or surface treatments to resist salt spray, moisture, and chemical exposure.
Typical Alloys: 5A02, 5056
Applications Marine rivets, HVAC duct fasteners, outdoor architectural joints
-
6061 O aluminum wire
High strength, good corrosion resistance and formability. Ideal for solid and blind rivets in aerospace, automotive, and industrial assemblies.
-
1050/1060/1100
Soft, conductive, and highly formable—ideal for HVAC, light-duty sheet metal, and electrical rivet applications.
-
2024 aluminum wire
High strength and good fatigue resistance. Used for aerospace-grade solid rivets requiring excellent load-bearing and durability.
-
2117 aluminum wire
Medium strength and excellent forming properties. Common for general-purpose rivets in shipbuilding, offshore platforms, and HVAC systems.
-
2219 aluminum wire
High strength and thermal stability with good corrosion resistance. Suitable for high-temperature rivet applications in aerospace and engines.
-
3003 aluminum wire
Corrosion-resistant and easily formable. Used in HVAC, construction, and building panels for light-load rivets.
-
5056 aluminum wire
High strength and excellent corrosion resistance. Ideal for structural rivets in marine, chemical, and salt-prone environments.
-
5052 aluminum wire
Combines good strength with excellent corrosion resistance. Commonly used in marine and architectural rivets.
-
5A02 corrosion resistant aluminum wire
Moderate strength and strong corrosion resistance. Suitable for rivets in marine equipment, chemical tanks, and external enclosures.
-
5A06 corrosion resistant aluminum wire
High strength with good corrosion resistance. Designed for medium-load rivets in outdoor structures and shipboard applications.
-
5154 aluminum wire
Medium strength with good corrosion resistance and weldability. Suitable for marine-grade rivets and chemical-resistant assemblies.
-
3A21 aluminum wire
High plasticity and excellent fatigue resistance. Commonly used for structural rivets in shipbuilding and pressure equipment.
Looking for rivet wire with reliable formability and consistent performance? Contact our technical team for alloy selection support or request a quote for your specific rivet application.Quick Quote
Chalco hot selling aluminum wire products for fastener
Designed for bolts, screws, and nuts, Chalco's aluminum wire solutions combine high strength, excellent machinability, and corrosion resistance. Whether you need electrical conductivity, structural performance, or high-temperature durability, we offer alloys and tempers tailored to demanding fastening applications.
-
Semi-Hard Aluminum Wire (HB)
Partially hardened aluminum wire offering a balance of strength and formability.
Typical Alloys: 3004, 5052
Applications: Structural screws, precision bolts, construction fixings
-
High-Strength Aluminum Wire
Strengthened through alloying and heat treatment to meet demanding mechanical performance.
Typical Alloys: 6061, 6082, 2014, 7075
Applications: Aerospace bolts, automotive screws, high-load fasteners
-
Conductive Aluminum Wire
Made from high-purity aluminum for electrical fasteners that require both mechanical connection and low resistance.
Typical Alloys: 1050, 1060, 1100
Applications: Electrical fasteners, cable lugs, power system screws
-
High Temperature Resistant Aluminum Wire
Designed for fasteners used in high-temperature and high-stress environments.
Typical Alloys: 2219, 2618
Applications: Aerospace bolts, engine fasteners, high-temperature screw joints
-
6061 aluminum wire
High strength, corrosion-resistant, and easy to form. Ideal for high-strength bolts, nuts, and threaded fasteners in industrial and aerospace use.
-
6063 aluminum wire
Moderate strength with good corrosion resistance. Commonly used in construction bolts and low-load structural fasteners.
-
6082 aluminum wire
Excellent strength and corrosion resistance. Suitable for high-load bolts and nuts in transportation and aerospace applications.
-
6151 aluminum wire
High strength and good toughness. Used for automotive and industrial bolts, nuts, and structural fasteners.
-
6056 aluminum wire
High strength aluminum alloy for critical fasteners. Used in aerospace and defense-grade bolts and structural screws.
-
1050/1060 aluminum wire
Good conductivity and ductility. Ideal for electrical fasteners like cable clamp bolts and conductive screws.
-
1100 aluminum wire
Low strength but highly formable. Used in precision screws and non-load-bearing aluminum fasteners.
-
2014 aluminum wire
High strength and heat resistance. Ideal for aerospace bolts and nuts under high-load, high-temperature conditions.
-
2024 aluminum wire
Excellent strength and fatigue resistance. Used in high-performance fasteners for aerospace and structural assemblies.
-
2011 aluminum wire
Superior machinability with low strength. Best suited for precision-machined screws and commercial aluminum bolts.
-
2117 aluminum wire
Medium strength with good formability. Used for general-purpose industrial and marine bolts and nuts.
-
2017 aluminum wire
High strength and good formability. Suitable for heavy-duty aerospace bolts and high-load threaded fasteners.
-
2618 aluminum wire
High strength and thermal stability. Designed for fasteners in engines and high-temperature aerospace systems.
-
3004 aluminum wire
Corrosion-resistant and strong. Applied in structural bolts and nuts for construction, HVAC, and transportation.
-
5056 aluminum wire
High strength and excellent corrosion resistance. Ideal for structural fasteners in marine, chemical, and outdoor settings.
-
7050 aluminum wire
Ultra-high strength with stress corrosion resistance. Used for aerospace bolts and military-grade threaded fasteners.
-
7075 aluminum wire
Exceptional strength and fatigue resistance. Preferred for high-load aerospace and defense bolts and screws.
-
7A03 aluminum wire
Very high strength for extreme load demands. Used in critical fasteners for aircraft structures and defense systems.
Need a fastener wire solution that balances strength, corrosion resistance, and formability? Get in touch to find the right alloy and wire specification for your application.Quick Quote
Other metal & bimetallic wires for rivets and fasteners
Beyond aluminum, Chalco also provides specialty fastener wire in copper, steel, titanium alloy, and advanced bimetallic composites. These materials are used in high-performance fastening applications requiring conductivity, enhanced strength, temperature resistance, or multi-functional design.
Steel wire for fasteners
Steel wire for fasteners is usually made of high carbon steel, stainless steel or alloy steel. It has high strength and wear resistance and is suitable for fasteners that bear larger loads.
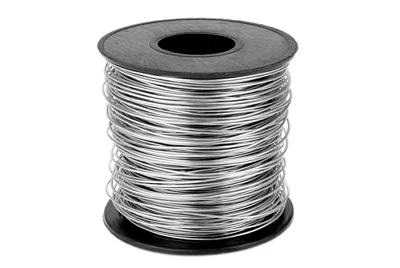
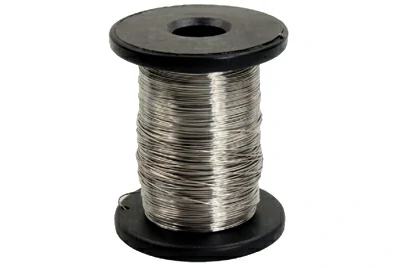
Titanium alloy wire for fasteners
Titanium alloy wire for fasteners is composed of titanium and its alloys, which have excellent strength, corrosion resistance and high temperature performance. Titanium alloy wire is suitable for fasteners that require extremely high performance.
Copper alloy wire for fasteners
Copper wire for fasteners is made of pure copper or copper alloy, with excellent electrical conductivity, thermal conductivity and corrosion resistance. Copper wire is suitable for fasteners that require electrical conductivity or good thermal conductivity.
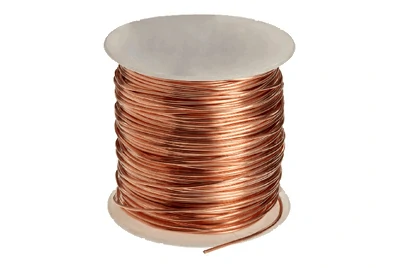
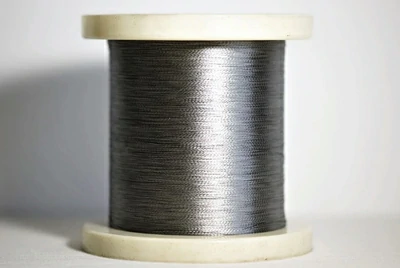
Bimetallic composite wire for fasteners
Made of two different metal materials, usually aluminum and copper, aluminum and steel, etc. Bimetallic composite wire can combine the advantages of two metals while improving strength, corrosion resistance and conductivity.
-
Aluminum-copper composite wire
Combining the lightness of aluminum with the excellent conductivity of copper, it is suitable for fasteners that require conductivity and light weight, such as electrical grounding screws and connectors.
-
Aluminum-steel composite wire
Aluminum offers lightness and steel's enhanced strength and wear resistance, making it suitable for construction and mechanical fasteners with high strength and corrosion resistance requirements, such as high-load bolts and nuts.
-
Aluminum-nickel composite wire
Aluminum provides lightweight properties, and nickel improves corrosion resistance and high temperature resistance, making it suitable for fasteners in aerospace and high-temperature environments, such as high-temperature bolts and rivets.
-
Copper-steel composite wire
Copper provides conductivity and steel provides strength, making it suitable for fasteners that require high strength and conductivity, such as electrical connectors and high-strength bolts.
Looking for alternative materials or composite wire solutions for extreme or hybrid applications? Talk to us for customized metal wire supply and fastener-specific recommendations.Quick Quote
Chalco aluminum wire for fasteners services and cooperation areas
Chalco's aluminum wire products for rivets and fasteners are widely trusted across industries for their exceptional strength, formability, and corrosion resistance. From lightweight solid rivets to structural-grade bolts, our wires are engineered to meet the performance needs of demanding applications. We have established long-term partnerships with clients in automotive, aerospace, marine, construction, electronics, and energy sectors—delivering both high-volume standard materials and customized alloy solutions.
To better serve varied application scenarios, our product range is divided into two major categories:
- Aircraft skin and structural panel riveting
- HVAC duct and system connections
- Marine and shipbuilding panel joints
- Construction panel and frame assembly
- Consumer electronics assembly (e.g. battery cases)
- Electrical panel and terminal connections
- Automotive blind rivets and trim attachments
- Solar module frames and brackets
- Aerospace bolts and screws
- Automotive bolts, nuts, and studs
- High-strength industrial fasteners
- Building structure anchoring bolts
- Precision screws and connectors for devices
- Conductive fasteners for power transmission
- Engine system and high-temp fasteners
- Structural components in rail and heavy equipment
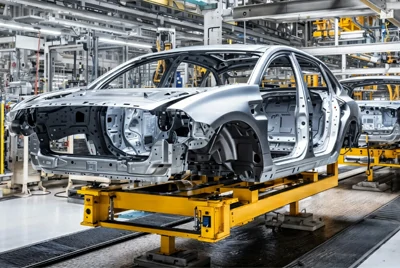
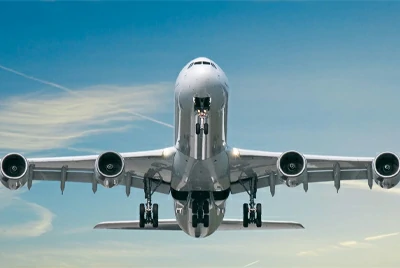
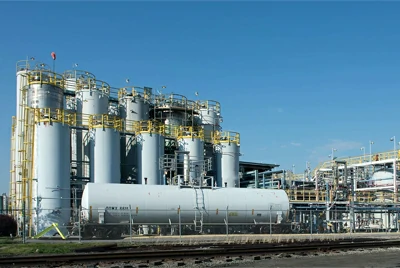
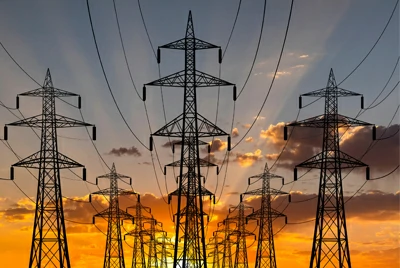
To meet the demanding requirements of rivet and fastener applications—ranging from strength and formability to corrosion resistance—Chalco leverages advanced production technologies and alloy expertise to deliver high-performance aluminum wire solutions. Whether for aerospace, automotive, marine, or industrial use, we offer tailored specifications and consistent quality to support your manufacturing goals.Quick Quote
Chalco manufacturing capabilities for rivet & fastener aluminum wire
In order to meet the stringent requirements of the fastener industry for high strength, precision and corrosion resistance, Chalco adopts a variety of advanced production methods to ensure the superior performance of aluminum wire in various fastener applications. Through sophisticated production processes and combined with different production technologies, we can efficiently provide aluminum wires of various specifications and shapes to meet customers' diverse needs in terms of strength, hardness, corrosion resistance, etc.Quick Quote
Hot rolled and continuous casting and rolling
Hot rolling and continuous casting and rolling is an efficient way to produce aluminum wire. First, the aluminum liquid is cast into aluminum bars through a casting mold, and then the aluminum bars are rolled into aluminum wire through hot rolling and continuous rolling processes.
- High production efficiency: Hot rolling and continuous casting and rolling can greatly increase production speed, reduce production cycle, and are more efficient than traditional casting and rolling methods.
- No joints and uniform structure: The hot-rolled aluminum wire has no joints in the whole coil, and the surface of the aluminum wire is smooth without coarse grain rings, which is suitable for cold heading fasteners in the fields of aerospace, high-speed railway, automobile, etc.
- Superior material properties: The aluminum wire produced by this process has a more uniform organizational structure and stable mechanical properties, making it suitable for the production of high-strength fasteners.
- Energy saving: This process can effectively reduce energy consumption and improve the energy efficiency of the production process.
Drawing process
Wire drawing is the most common method of producing aluminum wire, which is to stretch aluminum into wire by passing it through a die. This process can produce aluminum wires of different diameters and is usually used to produce cold-headed aluminum wire, conductive aluminum wire, etc.
- High Precision: The wire drawing process can precisely control the diameter and surface smoothness of the aluminum wire to meet the dimensional accuracy requirements of fastener applications.
- Strong flexibility: Aluminum wires of different specifications and shapes (such as round wires, flat wires, etc.) can be produced according to customer needs.
- Cost-effectiveness: The wire drawing process requires less investment in equipment, is suitable for mass production, and can effectively reduce production costs.
Extrusion process
Extrusion is the process of heating an aluminum rod to a certain temperature and then extruding aluminum wires of different shapes through a die. The extrusion process is often used to produce large-diameter aluminum wires or aluminum wires of complex shapes.
- Diversified shapes: The extrusion process can produce aluminum wires with complex shapes, such as flat wires, special-shaped wires, etc., to meet the needs of special fasteners.
- High Precision: The extrusion process can precisely control the size and shape of the aluminum wire, making it suitable for high-demand fastener production.
- Efficient production: suitable for mass production and can improve production efficiency.
Chalco Rivet & Fastener wire custom processing capabilities
- Customized Cutting Service: Chalco provides precision aluminum wire cutting services, which can be customized according to customer needs. Cut the length to ensure that the dimensional accuracy of the aluminum wire meets the specific requirements of the fastener. Our cutting equipment can quickly and accurately complete large-volume orders.
- Customized surface treatment: We provide a variety of surface treatment technologies, including anodizing, spraying, etc., to ensure that the aluminum wire has excellent corrosion resistance and wear resistance during use. Especially in harsh environments such as ocean and chemical, surface treatment can greatly extend the service life of the aluminum wire.
- Customized industry solutions: According to the special needs of customers, we also provide customized processing services, including the mixing of different alloys, the adjustment of different strengths and corrosion resistance. Our processing team can provide professional technical support and solutions according to different fastener application fields (such as automobiles, cables, aerospace, etc.).
- Customized wire shape: In addition to conventional round aluminum wire, we also provide a variety of wire shape processing services, including flat wire, square wire, oval wire, etc.
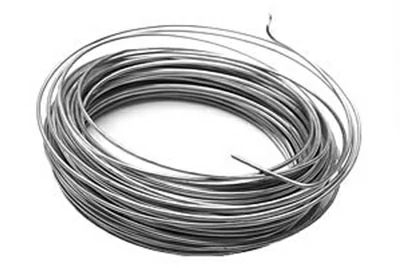
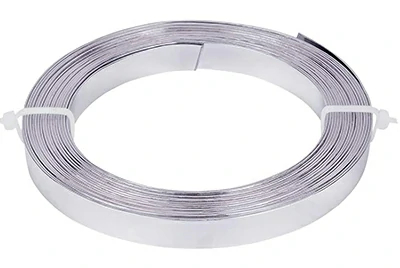
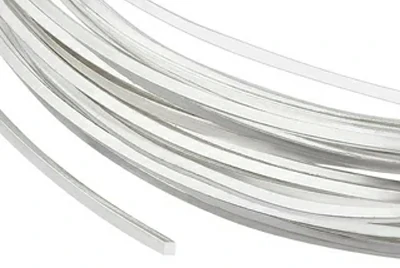
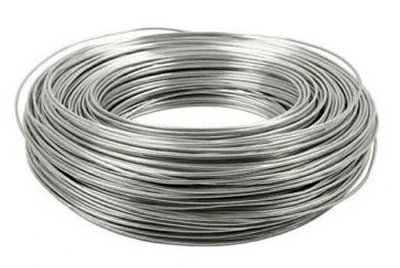
Why choose Chalco aluminum wire for Rivet & Fastener
- Efficient production line: Chalco has advanced production equipment and automated control systems, which can efficiently produce aluminum wires of various specifications. Our production line includes efficient production technologies such as precision drawing and continuous casting and rolling to ensure the diameter accuracy, smoothness and surface quality of the aluminum wire, meeting the strict requirements of the fastener field for aluminum wire.
- Multi-alloy series production: We can provide aluminum wires produced from different aluminum alloys (such as 3003, 5052, 6061, 7075, etc.) according to customer needs, covering a variety of performance requirements such as corrosion resistance, high temperature resistance, high strength, etc. Each alloy can be customized according to different fastener application requirements.
- Cold headed aluminum wire hardening and heat treatment: Chalco's cold headed aluminum wire will be hardened to H state (such as H14 or H18), which improves the strength and hardness of the aluminum wire to meet the high requirements of the fastener field. Before shipment, we will randomly select finished wires for heat treatment and convert them to T4 state to ensure that the mechanical properties of the aluminum wire are optimal and suitable for high-load and high-strength fastener applications.
- Flexible production scale: Chalco has the ability to produce from small batches to large-scale production, and can flexibly adjust according to customer order requirements. Whether it is long-term supply of a single specification or customized production of multiple specifications in small batches, we can complete it efficiently.
- Precision testing and quality control: Chalco conducts a number of key tests during the production process, including dimensional measurement, mechanical property testing, surface quality inspection, and shear strength and non-riveting testing after heat treatment. These tests ensure that the aluminum wire can withstand the expected shear force in actual applications, provide stable connections, and improve safety and service life.
Aluminum Rivet & Fastener Wire buying guide
1. Choose the right type of aluminum wire
Choose the right type of aluminum wire based on application requirements. For example, aerospace and military fields require high-strength aluminum wire (such as 7075, 7050), while chemical and marine environments require corrosion-resistant aluminum wire (such as 5052, 5A02).
2. Confirm the strength and hardness of the aluminum wire
Different aluminum wire types have different strengths and hardnesses. Cold-forged aluminum wire is usually hardened to the H state (such as H14, H18) and is suitable for fasteners with high strength requirements, while semi-hard aluminum wire is suitable for medium-load applications. When purchasing, you need to ensure that the strength of the aluminum wire meets the working load requirements of the fastener.
3. Consider the surface treatment of the aluminum wire
Surface treatment has an important impact on the corrosion resistance and service life of aluminum wire. Treatment methods such as anodizing and electrophoretic coating can significantly improve the corrosion resistance of aluminum wire, especially suitable for fasteners in marine and chemical environments.
4. Choose the appropriate aluminum wire specifications
Select the appropriate aluminum wire specifications according to the size requirements of the fasteners. The diameter, length and shape of the aluminum wire (such as round wire, flat wire) need to match the design and manufacturing process of the fastener.
5. Understand the supplier's production capacity and quality control
It is very important to choose a reliable aluminum wire supplier. Understanding the supplier's production capabilities, quality control processes and certifications can ensure that the purchased aluminum wire meets the quality requirements and is delivered on time.
6. Price and delivery time
In addition to price, delivery cycle and after-sales service are also important purchasing considerations. Make sure the supplier can provide a stable supply of products and provide timely support in emergency situations.
7. Check certification and compliance
Make sure the aluminum wire you purchase complies with relevant quality certifications, such as ISO 9001:2015, RoHS, REACH, etc. These certifications ensure that the aluminum wire meets international quality standards and does not produce harmful substances during use.
8. Consider environmental adaptability
Choose the appropriate aluminum wire according to the use environment of the fastener (such as high temperature, low temperature, humidity, corrosive environment, etc.). For example, high temperature resistant aluminum wire (such as 2219, 2618) is suitable for high temperature environment, while corrosion resistant aluminum wire (such as 5052, 5A02) is suitable for marine and chemical environment.
9. Things to note when purchasing
Durability and Reliability: Choose aluminum wire for long-term durability to ensure it can withstand the challenges of high loads and harsh environments during application.
Customized needs: If standard specifications do not meet your requirements, you can consider working with suppliers to customize aluminum wire to meet specific application needs.
Inventory and delivery time: Ensure that suppliers have sufficient inventory and can provide timely delivery services to avoid project delays due to out-of-stock.
Fastener purchasing FAQs
Q1: What are the common types of aluminum wire for fasteners?
A1: Aluminum wire for fasteners can be divided into cold heading aluminum wire, semi-hard aluminum wire, high-strength aluminum wire, corrosion-resistant aluminum wire, conductive aluminum wire and high-temperature resistant aluminum wire according to application requirements. Each type of aluminum wire has different strength, hardness and corrosion resistance, and is suitable for fasteners in different fields.
Q2: How to choose the appropriate aluminum wire specifications?
A2: The specifications of the aluminum wire (such as diameter, length, etc.) should be selected according to the specific fastener design requirements. Common aluminum wire diameters range from 0.5mm to 10mm. When selecting, make sure that the size of the aluminum wire matches the size of the fastener.
Q3: What are the options for surface treatment of aluminum wire?
A3: Common surface treatment methods include anodizing, electrophoretic coating, chemical plating and spraying, etc. When choosing a surface treatment method, it should be determined based on the use environment and corrosion resistance requirements of the fastener.
Q4: What are the quality standards and certifications for fastener aluminum wire?
A4: Common quality standards include ASTM, ISO 9001, AS9100, etc. Ensuring that the aluminum wire meets relevant standards and certifications can ensure its stable quality and meet specific application requirements.
Chalco can provide you the most comprehensive inventory of aluminum products and can also supply you customized products. Precise quotation will be provided within 24 hours.
Get a quote