With the continuous innovation of forging technology, we have made breakthroughs in the performance, specifications and application of aluminum alloy forgings to meet the needs of high precision, light weight and high strength.
The research and development of high-end forgings has enhanced our forging capabilities and demonstrated our strength in aerospace, rail transportation and other fields. In the future, we will continue to promote technological innovation and provide stronger, larger and more precise forging solutions.
Chalco high-end aluminum forging product introduction
Product alloys: 6061, 7075, 7050, 2024, 2219, 2618, 6063, 6082, etc. [Choose by alloy grade]
Forging methods: free forging, die forging, ring forging, cold forging, hot forging, precision forging (drop hammer forging) [Technical interpretation]
Forging product customization: size customization, shape customization, surface treatment customization, precision customization, etc.
Additional services: heat treatment/hardening, shot peening/sand blasting, vibration cleaning, machining, anodizing, etc.
Chalco forging product size range reference:
Product name | Alloy series | Size (mm) | Specification | |
Free Forgings | Forging Block | 1XXX series-8XXX series | (50~5000)*(50~2000)*(50~1000) | AMS4127; AMS4133; AMS4143; AMS4144 And other customer requirements |
Forging cake | 1XXX series-8XXX series | ∅100~ ∅2500*20~1000 | ||
Forged Rods | 1XXX series-8XXX series | ∅25~ ∅1200*100~4000 | ||
Forged Ring | 1XXX series-8XXX series | ∅500~ ∅2500*50~1200 | ||
Forged back extrusion tube | Anti-squeeze tube | 1XXX series-8XXX series | ∅150~ ∅735*300~2400 | |
Forged pipe | 1XXX series-8XXX series | ∅500~ ∅1200*800~1500 | ||
Die forgings | Die forgings | 1XXX series-8XXX series | Customized according to customer needs |
Chalco high-end aluminum forging product display
Our company has significant advantages in the production of conventional aluminum alloy forgings, with many years of production experience, mature processes and advanced equipment, ensuring short delivery cycles and stable product quality.
At the same time, we continue to optimize production technology, promote equipment innovation, and gradually expand the R&D and production capabilities of high-end aluminum alloy forgings, committed to providing customers with more precise and higher-performance customized products.
Aluminum forged ring products
Chalco aluminum alloy forging rings are developing towards higher strength, larger specifications and more complex shapes to meet the needs of high-end fields such as aerospace, automobile and industrial manufacturing.
Contact us now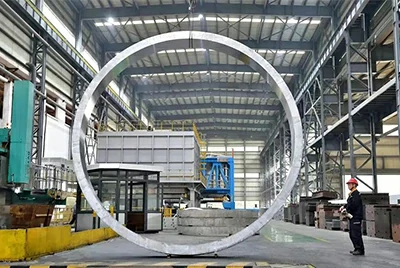
- Lightweight and high strength
- Development and application of high-performance alloys
- Customized precision machining
-
Thick wall aluminum forging ring
Alloy: 7075 T6
Size: ∅1900* ∅1200*85mm
Tensile strength: ≥530MPa
Yield strength: ≥450MPa
-
Conical aluminum alloy forging ring
Alloy: 6061 T6
Size: ∅2080* ∅1829* ∅1020mm
Tensile strength: ≥320MPa
Application: A certain type of naval project
-
Large diameter forging ring
Alloy: 7050 T6
Size: ∅2257*∅2012*90mm
Specification: YS/T479-2005
-
Oversized forged rings
Alloy:2024/2A12 T4
Size: ∅3380*∅3300*90mm
Specification: GBn223-84
-
Special-shaped aluminum alloy forging ring
Alloy: 6061 T6
Size: ∅1090*∅374*330mm
Specification: YS/T479-2005
Aluminum forged pipe products
With the continuous optimization of manufacturing processes, Chalco aluminum alloy forged pipes have achieved significant breakthroughs in dimensional accuracy, high temperature resistance and strength, and are widely used in aviation, automotive, petrochemical and other fields.
Contact us now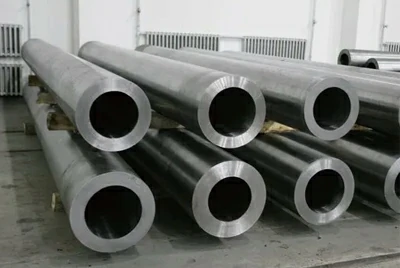
- High precision and complex structure
- High temperature resistant, high strength alloy pipe
- Intelligent manufacturing and automated production
-
Standard aluminum forged pipe
6061 T6: ∅334*∅284*690mm
5A06 O: ∅388*∅356*470mm
5083 H112: ∅524*∅481*1988mm
-
Large diameter aluminum forged pipe
7A19 T6: ∅556* ∅438*1680mm
6061 T6: ∅710* ∅630*2420mm
6061 T6: ∅834*778*1665mm
Specification: YS/T479-2005
-
Large size forged rectangular tube
Alloy: 5A06 O
Size: 300*120*6.0mm
Application: Missile bracket for a certain aircraft carrier
-
T-shaped aluminum forged tube
Alloy: 6061 T6
Size: ∅960* ∅780*2150mm
Specification: ASTM B247-2015
-
Variable diameter aluminum forged pipe
Alloy: 6061 7050 2024
Size: Customized
Application: aerospace, industrial equipment, marine engineering
-
Pillar forging pipe
Alloy: 2024/2A12 T352
Size: Customized
Specification: GBn223-84
-
Hydrogen cylinder forging pipe
Alloy: ∅491*∅490*840mm
Specification: YS/T479-2005
Inner diameter tolerance: -0.5mm~+2.5mm
Straightness: ≤1mm/m
-
High precision forged reverse extrusion tube
Alloy: 5083 H112
∅424mm*∅366mm*2220mm (WT 29mm)
∅478mm*∅428mm*1850mm (WT 25mm)
Eccentricity: 1.0mm, straightness 1mm/m
Other high end forging products
Aluminum forged rod
Developed towards higher strength, longer length and more complex structure.
Large diameter aluminum alloy short rod
High strength extra long aluminum alloy forged rod
Composite forging rod
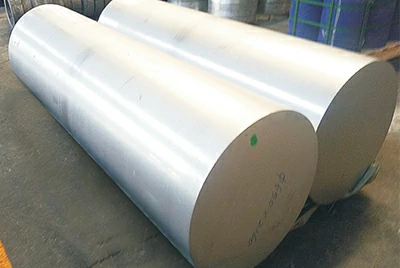
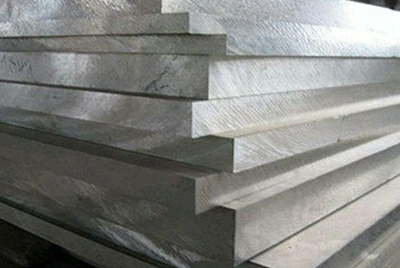
Aluminum forging plate
Advances in precision forging have improved the dimensional accuracy and mechanical properties of aluminum forging plates.
Extra wide aluminum alloy forging plate
High precision aluminum alloy forging plate
High temperature resistant aviation forging plate
Aluminum forging block
Larger sizes, higher density, excellent mechanical properties, and uniform structure through advanced technology.
Oversized aluminum alloy forgings
High density aluminum alloy forging
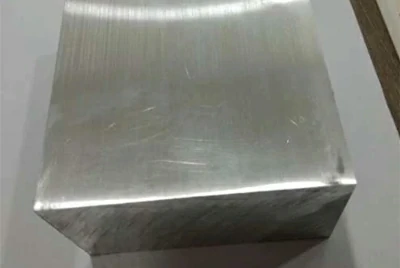
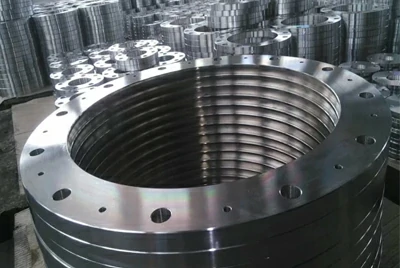
Aluminum forged flange
High pressure, large diameter, lightweight, and corrosion resistance, offering excellent stability in pipeline and fluid systems.
High pressure large diameter flange
Corrosion resistant composite flange
Aluminum forging disc
Aluminum forging disc is advancing in diameter and homogeneity, with optimized processes enhancing strength, stability, and precision.
Extra large diameter forging disc
Highly homogeneous forging disc
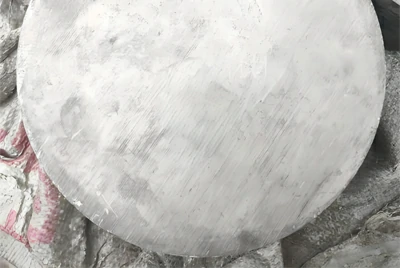
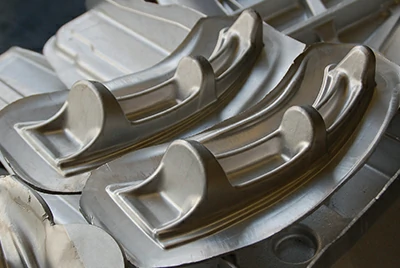
Customized aluminum forgings
As demand for high-precision, complex shapes grows, customized production of special-shaped aluminum alloy forgings has advanced. This breakthrough is driven by precision die forging, CAD/CAM, multi-axis CNC machining, and advanced heat treatment, ensuring excellent mechanical properties, material efficiency, and accuracy.
Chalco aluminum forgings products alloy inventory
Alloy series | 2000 Series Forging Alloy | 5000 series forging alloy | 6000 series forging alloy | 70000 series forging alloy |
Alloy | 2011 2014 2017 2024 2124 2219 2618 | 5052 5083 5251 5754 | 6005 6026 6061 6063 6082 6262 | 7010 7050 7068 7075 7175 |
Features | High strength Lower corrosion resistance Good processability | Excellent corrosion resistance Good weldability High toughness | Excellent overall performance Heat treatment performance Lightweight and durable | Ultra-high strength Good fatigue performance Strong processability |
Application | Aircraft structural parts High performance auto parts Aircraft engine parts Military equipment parts Missile structural parts Heavy Duty Truck Parts | Ship structure parts Chemical equipment parts Protective Armor Building structural parts Refrigerated transport equipment Pipe flange | Automobile chassis High-speed train structural parts Industrial machinery parts Building door and window frames Aviation pipe fittings Mountaineering and sports equipment | Aircraft landing gear Aerospace load-bearing components High performance bicycle parts Military armor plate High-end motorcycle frames Wind power equipment components |
Reference table of mechanical properties of main forging alloys | |||||
Desired Properties | Material | Mechanical Properties | |||
Former Sumitomo Designation | Temper | Tensile Strength (N/mm)² | Proof Stress (N/mm)² | Elongation (%) | |
High Strength | 6061 | T6 | 315 | 275 | 19 |
2011 | T8 | 410 | 315 | 15 | |
2014 | T6 | 480 | 275 | 22 | |
2017 | T4 | 440 | 275 | 22 | |
Abrasion Resistance | 4032 | T6 | 380 | 315 | 9 |
High-Temperature Strength | 2618 | T6 | 440 | 370 | 10 |
Although our main product of Chalco Aluminum is aluminum, the group company is also involved in other metal fields and can provide a variety of metal products. If you have needs for other metal alloy forgings, please feel free to communicate with our sales staff. We will do our best to allocate resources and provide you with the best solution.Quick Quote
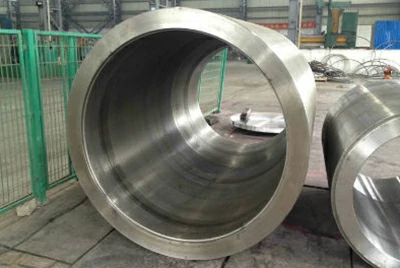
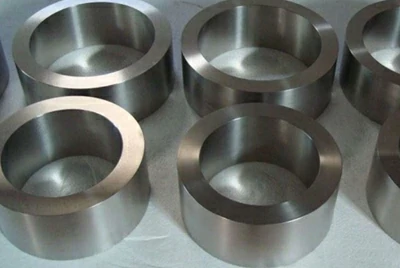
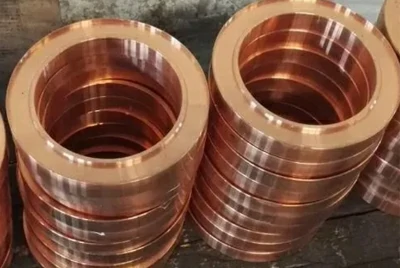
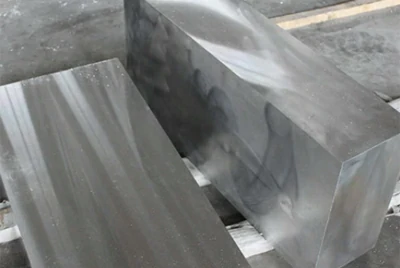
Chalco aluminum forging product technology innovation
- Technological innovation: processes such as thermomechanical processing, microstructure control and heat treatment optimize the aluminum alloy forging process to ensure excellent mechanical properties.
- Advanced Equipment: Continue to invest in advanced forging equipment to improve production accuracy and efficiency and meet the production needs of high-specification complex structures.
- Precision quality control: metallurgical review, non-destructive testing and destructive testing, etc., to ensure high standards of product size, strength and stability.
- High-end industry applications: Combining advanced technologies and equipment to meet customized needs in aerospace, national defense, rail transportation and other fields.
- Improved production efficiency and quality: Chalco has a wide range of press equipment to achieve flexibility in delivery time and multiple capacities.
Forging Press | Screw press | 5, 500 tons, 4, 100 tons, 2, 100 tons |
Mechanical press | 1600 tons, 1300 tons 1000 ton mechanical press (CNC direct drive) 300 tons, 200 tons, 150 tons, 125 tons | |
Production smelting | Induction heating furnace Electric furnace | |
C-Frame Trimmers | 75 tons, 30 tons, 20 tons, 10 tons |
Chalco aluminum forging products cover industrial fields
Aerospace forgings
With the innovation of forging technology, the application of Chalco aluminum forgings in the aerospace field has significantly improved. Advanced technology allows the product to not only meet the requirements of high strength, lightweight and corrosion resistance, but also achieve breakthroughs in dimensional accuracy and material utilization. From complex accessories to critical structural parts, our aluminum forgings demonstrate greater stability and reliability.
- Rocket Structures: Adapter Structures, Bulkheads, Payload Adapters, Separator Rings, Barrels, Cones, ESPA Rings, Y-Rings, Rideshare Structures, 5.5 Meter Rings, 8.4 Meter Ring Segments
- Rockets, thrusters: closures, combustion chamber forgings, bushings, domes, nozzles, thrust cones, oil pans
- Space capsule/ISS: bulkheads, tunnels, LIDS adapters, deck forgings, docking adapters
- Commercial spacecraft: flanges, valves, ejector plates, case forgings, interfaces, bushings, thrust cones
- Missiles: cylinders, shell forgings, frustums, interstage forgings, nozzles, shells, shrouds, cones, tubes
- Fixed-wing aircraft: air inlet connecting ring, engine connecting ring, adapter, bell adapter, brake caliper, turbine box, column structure, hanger, air inlet box assembly, propeller hub, air inlet adapter, landing gear shaft, landing gear cylinder, landing gear resistance bracket, transmission ring gear
- Aircraft, rotorcraft: planetary gear forgings, swash plates, transmission forgings, transmission ring gears


Aluminum forgings for defense projects
With the innovation of forging technology, the performance of aluminum forgings in the defense industry has been continuously improved. The combination of new processes and heat treatment technology has made breakthroughs in strength, lightness and resistance to extreme environments, meeting the requirements of weapon systems, armored vehicles and aircraft for high reliability and high performance, and providing technical support for more efficient and accurate defense equipment.
- Armored vehicle related parts: armored vehicle chassis, track components, armored protective plates, wheels and hubs
- Ship-related parts: ship structural parts, steering gear and propeller parts, shipborne weapon system parts, ship power system parts
- Fighter aircraft and aircraft related parts: fighter fuselage structural parts, engine parts, flight control system parts, wing brackets and connectors
- Missile system related components: missile shell, propulsion system components, control components, guidance system components
- Weapon system related parts: gun barrels and cannons, weapon launcher parts, ammunition magazine components, aiming and control system parts


Aluminum forgings for nuclear power projects
Our company focuses on the research and development of high-end aluminum alloy forgings, providing high-performance products that meet the needs of the nuclear energy field. Through advanced forging technology, our products have excellent performance in strength, corrosion resistance, radiation protection and thermal conductivity, and are widely used in nuclear energy-related equipment, providing reliable material solutions for the industry.
- Nuclear reactor components: cooling system components, pressure vessels and their accessories. Product types include large-diameter aluminum alloy forging rings, high-precision aluminum alloy forging tubes, etc.
- Nuclear power plant cooling system: cooling pipes and structural parts. Product types include high-precision aluminum alloy forged pipes, large-diameter aluminum alloy forged pipes, etc.
- Nuclear waste disposal equipment: storage and transport containers, etc. Product types include thick-walled aluminum alloy forged rings, aluminum alloy forged rings, etc.
- Radiation protection components: used for radiation protection shielding. Product types include customized aluminum alloy forgings, etc.


Vehicle forgings
With the innovation of forging technology, the performance of aluminum forgings in vehicle manufacturing continues to improve. Advanced processes increase the strength, precision and lightweight of aluminum parts, significantly improving fuel efficiency, durability and handling performance. Applications extend from traditional suspension and engine components to electric vehicle battery housings, high-performance braking systems and lightweight body structures.
- Automotive forgings: forged wheels, rear support frames, control arms, joints, brake calipers, gear levers, pistons
- Bicycle Forgings: Triple Clamps, Seat Posts, Steerers, Suspension Tubes, Suspension Parts, Cranks, Brake Calipers, Ratchets
- Motorcycle forgings: triple clamps, gear hubs, axle brackets, upper and lower clamps, pedal shifters, pedals


Forging industrial hardware
With the development of forging technology, the aluminum forging process has achieved precise control, and aluminum is shaped under high pressure to produce stronger, durable and lightweight components. This high-performance hardware is widely used in factories, warehouses and other industrial facilities to provide reliable support.
- Articulated and moving parts: hinges, joints, pulleys, casters
- Fastening and connecting parts: latches, brackets, connectors
- Control and adjustment parts: handles, knobs
- Transmission and power components: gears


Forging knowledge
Aluminum forging type
Free Forging
The pressure is directly applied by a forging hammer or hydraulic press to allow the metal material to deform freely outside the die, which is suitable for most forgings with complex shapes.
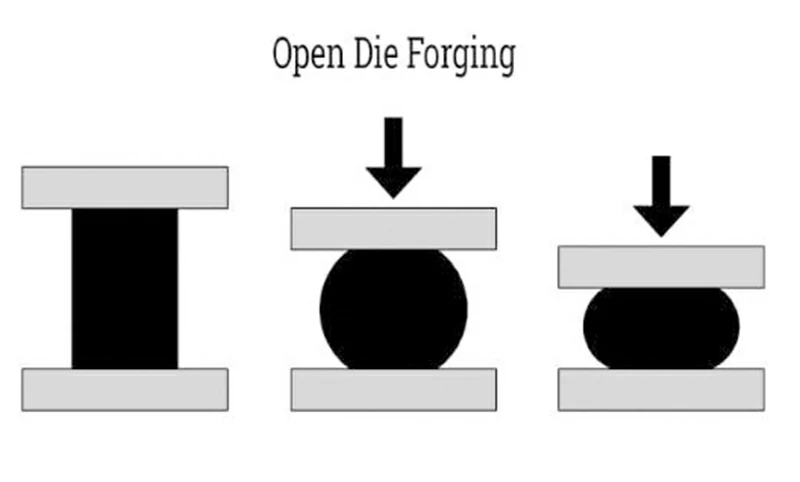
Die Forging
The metal material is placed in the mold and the metal is formed in the mold through external force. It is suitable for forgings with high precision requirements and simpler shapes.
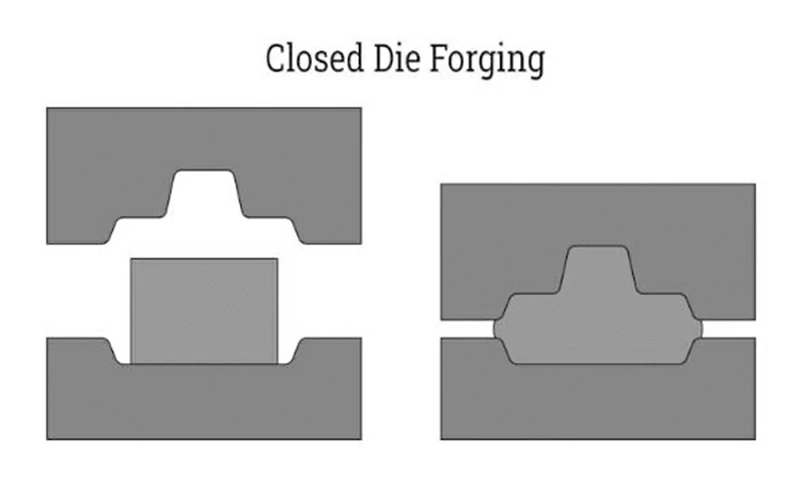
Ring Forging
Specially used for producing ring-shaped products, manufactured by a combination of rolling and forging, commonly used in the aviation, automotive and petroleum industries.
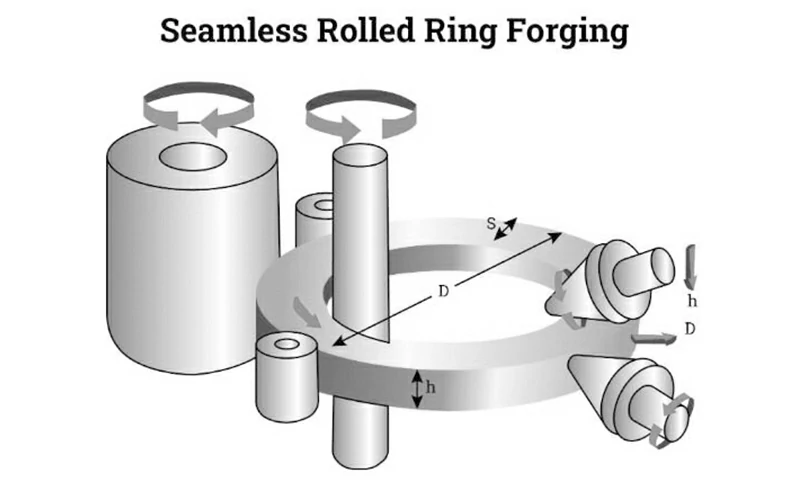
Cold Forging
Forging is carried out at room temperature or slightly above room temperature. It is suitable for the manufacture of small-sized, high-precision parts and is mainly used to improve the mechanical properties of parts.
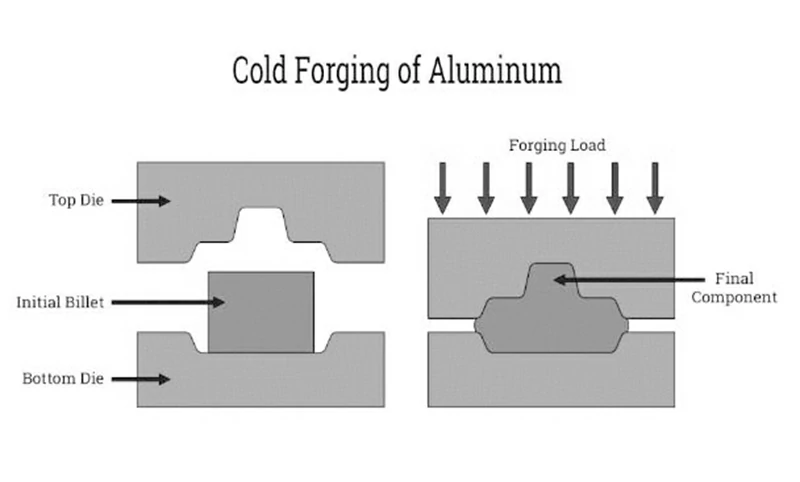
Hot Forging
Forging at high temperature can greatly improve the deformation capacity of metal materials. It is suitable for the production of large-size forgings and is commonly seen in the production of structural parts and tools.
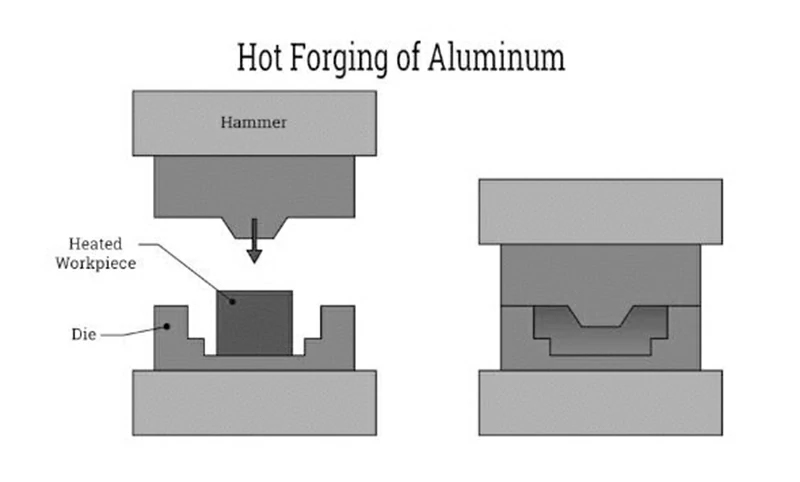
Precision forging (drop hammer forging)
Forging is performed by applying precise pressure through a drop hammer or hydraulic press, which is suitable for high-precision, small-batch production of aluminum alloy forgings.
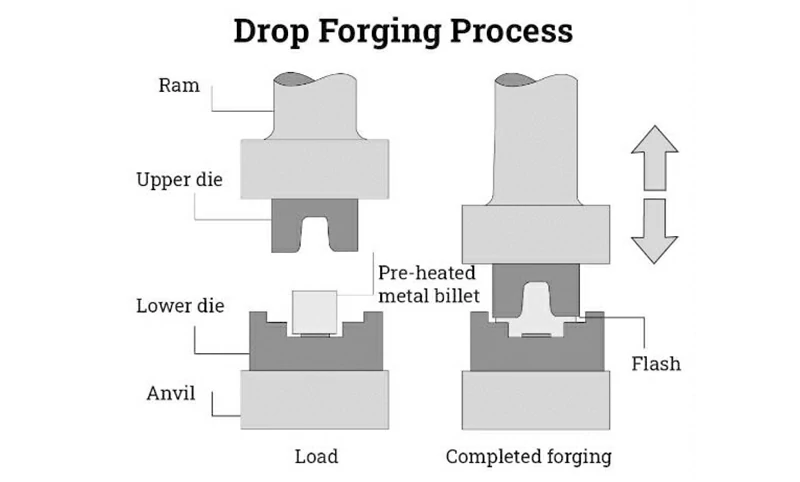
How to choose between free forging and die forging
- Part shape and complexity: Free forging is suitable for simple parts, while die forging is suitable for complex parts.
- Production batch: Free forging is suitable for small batches, and die forging is suitable for large batch production.
- Dimensional accuracy: Free forging has lower accuracy, while die forging has higher accuracy.
- Cost: Free forging has low initial investment, while die forging is suitable for long-term large-scale production with lower cost.
- Material utilization rate: The material utilization rate of free forging is high, while the material utilization rate of die forging is low.
Forging and Casting
Forging: Through the plastic deformation of metal, it has high strength and good mechanical properties. It is suitable for parts with high strength, fatigue resistance, and impact resistance, and has high dimensional accuracy. It is suitable for aerospace, automobile, military and other fields, but compared with casting, forging has a longer production cycle and higher cost.
Casting: Suitable for the production of complex shapes and large-sized parts, and can achieve large-scale production, but the strength and surface quality of castings are usually lower than forgings. Casting costs are lower and it is suitable for large-scale production and parts with complex shapes, such as large engine housings, pipes, molds, etc.
Selection suggestion: If there are high requirements for strength, durability and precision, forging process should be selected. If the parts are complex in shape, large in size and require low-cost, large-scale production, casting is a more appropriate choice.
Characteristic | Forging | Casting |
Process principle | Heating the metal and applying external force to deform it plastically to obtain the desired shape | The metal is melted and poured into a mold and then cooled to form |
strength | High strength, because the metal's grain structure is refined by plastic deformation | Low, there may be defects such as pores and cracks during the casting process |
Mechanical properties | Superior, especially in fatigue resistance and impact resistance | Generally, it depends on the casting process and material selection |
Surface quality | Generally good, but the surface needs further treatment to meet higher requirements | There may be surface defects such as sand holes and pores |
Dimensional accuracy | High, capable of achieving high dimensional accuracy and consistency | Generally, the accuracy is poor and secondary processing is required |
Production efficiency | Suitable for mass production, but the production cycle for each part is long | Suitable for complex shapes and mass production, but more time-consuming |
Material utilization | Higher, almost no metal waste | Low, waste may be generated during casting |
cost | Higher, especially in small batch production, the cost is higher | Low, suitable for mass production and can save costs |
Application Areas | High-strength parts (such as aviation, automotive parts, tools, etc.) | Suitable for complex shapes and large parts (such as pipes, engine casings, etc.) |
Adaptability | Suitable for parts with high strength requirements and regular shapes | Suitable for parts with complex shapes and large sizes |
Defect Rate | Fewer defects unless process control is inadequate | There are many defects, such as pores and cracks, which may affect the quality |
Post-processing requirements | Heat treatment or machining may be required to achieve final results | Requires a lot of post-processing, such as removing sand holes, polishing, etc. |
Production cycle | Longer, especially for complex parts requiring more processing time | Shorter, suitable for rapid mass production |
Advantages of aluminum alloy forging products
- Lightweight: Aluminum alloy itself has a low density, which is very suitable for use in areas where weight reduction is required, such as aerospace, automotive and other industries.
- Excellent mechanical properties: Forging process can optimize the internal structure of aluminum alloy, improve the tensile strength, fatigue resistance and corrosion resistance of the material.
- Precision: Through precision forging technology, aluminum alloy forgings can achieve higher dimensional accuracy and adapt to applications with high precision requirements.
- High temperature resistance: Aluminum alloy forgings after heat treatment have good high temperature resistance and are suitable for use in high temperature environments.
Comparison of various metal forging products
characteristic | Aluminum alloy forging | Steel forging | Titanium alloy forging | Magnesium alloy forging |
density | Light (2.6–2.8 g/cm³) | Heavier (7.85 g/cm³) | Heavier (4.4–4.5 g/cm³) | Lightest (1.7 g/cm³) |
strength | Medium, suitable for low to medium load applications | High, suitable for applications with high load requirements | Very high, suitable for high strength and high temperature environments | Lower, suitable for light load requirements |
Fatigue resistance | Good, suitable for repeated stress situations | Very good, suitable for high frequency use | Excellent, especially suitable for aerospace and military fields | Poor, suitable for low load and short time use |
Corrosion resistance | Excellent, especially in marine or harsh environments | Poor, especially prone to rust in humid environment | Excellent, titanium alloy itself has strong resistance to most corrosive media | Good for use in air, but sensitive to some chemicals |
High temperature resistance | Medium, heat treatment can enhance high temperature resistance | Good, suitable for applications in high temperature environments | Excellent, suitable for high temperature, high load environment | Generally, suitable for normal to medium temperature environments |
Processing difficulty | Easy to process, suitable for large-scale production | Difficult to process, especially in high-strength materials | High difficulty, complex process and high cost | Easier, but less intense |
cost | Low, especially cost-effective in mass production | Higher, especially in special alloys or large quantities | Very high, due to the difficulty of raw materials and processing | Low, cheap materials, suitable for lightweight requirements |
Application Areas | Aerospace, automobile, military, electronics, construction, etc. | Aerospace, military industry, heavy machinery, transportation vehicles, etc. | Aerospace, military, medical equipment, etc. | Aerospace, electric vehicles, lightweight structures, etc. |
Weight advantage | The advantages are obvious, especially suitable for industries with lightweight requirements | No clear advantage, suitable for weight-insensitive applications | Heavy, not suitable for occasions requiring lightweight | Extremely lightweight, suitable for applications requiring ultra-light materials |