Aluminum square and rectangular tubes, also known as aluminum box sections, are square (equal-sided) or rectangular (unequal-sided) tubes made of aluminum alloy. Due to limitations in extrusion press tonnage and mold development, the common size range for aluminum square tubes is 10x10mm-200x200mm (1/2"x1/2"-8"x8").
Chalco's extra-large aluminum square and rectangular tubes are produced using a 500MN vertical extrusion press, which first extrudes a round tube and then gradually bends it into a square or rectangular shape using a roller forming machine. This process significantly exceeds the size limitations of traditional square aluminum tubes.Click to order
- Extra large square tube size: 300 x 300mm-1200 x 1200mm
- Extra large rectangular tube size: 300 x 400mm-1000 x 1200mm
- Wall thickness: 6-120mm
Chalco's seamless extruded aluminum square and rectangular tubes offer high production efficiency, excellent forming capabilities, superior quality, and a wide range of sizes and wall thicknesses. The one-step forming process ensures optimal mechanical and physical properties. These tubes find extensive applications in construction, machinery, marine engineering, cranes, and more.
Introduction of super large diameter aluminum square tube/rectangular tube
Aluminum alloy | 2000 series: 2024 |
6000 series: 6060, 6061, 6063, 6082 | |
7000 series: 7075 | |
Square tube size | 300*300-1200*1200mm |
Rectangular tube size | 300*400-1000*1200mm |
Wall thickness | 6-120mm |
Length | 4-12m |
Heat treatment | Well-type heat treatment system |
Testing | Surface inspection, dimension inspection, nondestructive inspection, metallographic inspection, hardness inspection |
Surface protection | Rust-proof treatment on the outer surface, drying treatment on the inner surface, protective cover on the port |
Standard | ASTM B221, ASTM B429, EN 755-9, JIS H4100 |
The most popular large diameter aluminum square tube / rectangular tube
-
6061 large diameter alu square tube
Medium to high strength
Excellent corrosion resistance
High dimensional accuracy
-
6063 large diameter alu square tube
Excellent extrusion properties
Smooth surface finish
Easy to machine
-
6082 large diameter alu square tube
High strength
Good weldability
Excellent fatigue resistance
-
6060 large diameter alu square tube
Moderate strength
Good corrosion resistance
Good machinability
-
2024 large diameter alu square tube
High strength
Excellent fatigue resistance
Good machinability
-
7075 large diameter alu square tube
Very high strength
Excellent mechanical properties
Resistance to stress corrosion cracking
Chalco's advanced manufacturing process for extra large aluminum square and rectangular tubes
Chalco and its strategic partners possess the world's largest 500MN vertical extrusion press, equipped with high-efficiency descaling machines, proprietary lubricant spraying technology, rapid mold changeover technology, and precision straightening equipment for large-diameter seamless tubes.
This extrusion press offers exceptional pressure, a wide range of product specifications, high production efficiency, and high material utilization, resulting in high-quality tubes suitable for high-strength and advanced materials, including aluminum and steel. It can produce extra large aluminum square tubes up to 1200x1200mm and rectangular tubes up to 1000x1200mm in a single extrusion process. Moreover, it can produce thick-walled tubes with a maximum wall thickness of 120mm and a maximum length of 12 meters.Quick Quote
500MN vertical extrusion technology: crafting excellence
Chalco employs world-leading 500MN vertical extrusion technology, similar to that used by renowned international companies such as Woman-Gordon (USA), Allure (Germany), and Symptoms (Japan).
Core Process Advantages:
Single-pass extrusion: Utilizing a 500MN extrusion press, the billet is pierced and then vertically extruded in a single pass, taking only 10 minutes.
Round-to-square conversion: A roller forming machine is employed to convert the round tube into a square one through multiple passes in a single operation, ensuring dimensional accuracy and consistent wall thickness.
Heat treatment: A pit-type electric furnace is used for heat treatment, with a professional temperature control system maintaining heating rate deviation within ±5°C and holding temperature deviation within ±5°C.
Precision machining: External boring and internal turning are performed to ensure concentricity deviation of less than 0.5mm, surface roughness less than 12.5μm, and straightness better than 1:1000.
Leveraging our robust production capacity and technological advantages, we provide customers with high-quality, high-performance extra-large aluminum square tubes. Our finished products feature large dimensions, a dense grain structure, superior strength and toughness, high dimensional accuracy, and excellent surface quality.
Equipment parameters for the 500MN vertical extrusion:
Nominal pressure | 500MN |
Main pump pressure | 31.5MPA |
Ultra-high pressure system pressure | 100 MPA |
Return force | 30MN |
Maximum opening height of press | 8500 MM |
Slider stroke | 2500 MM |
Effective table surface | 3800 *6800 MM |
Main power | 4500KW |
Press dimensions | 10.1(L)*9.1(W)* 30M(H) |
Total weight of equipment | 10, 000 tons |
In addition to extra-large diameter aluminum square tubes, the equipment can also produce various large-sized cylindrical, pancake-shaped, and columnar extrusions to replace die forgings.
Round-to-Square conversion using roller forming
Traditionally, it is challenging for conventional extrusion presses to handle such large square sections (1200*1200mm) due to the extremely high pressure required and the demanding requirements for molds and other equipment.Quick Quote
While our 500MN vertical extrusion press can easily handle the required pressure, the special nature of square molds subjects them to immense stress during extrusion, especially at the corners of the square section, which can easily lead to damage and uneven wall thickness. Considering both cost and quality, we have adopted the following process:
- Initial round tube extrusion: The material is first extruded into a round tube using our 500MN vertical extrusion press.
- Subsequent round-to-square conversion: The round tube is then formed into a square tube in a single pass using a roller forming machine.
Compared to traditional methods, the roller forming process involves multiple shaping steps, allowing for a more even distribution of stress and resulting in higher quality large aluminum square tubes.
Our roller forming process is a multi-stage, single-pass operation. The round tube passes through multiple sets of rollers, each precisely designed to gradually transform it into a square cross-section. This continuous process completes the transformation from round to square in a single operation. The precision of each deformation ensures dimensional accuracy and consistent wall thickness throughout the forming process.
Rigorous testing, guaranteed quality
Chalco boasts a world-class physical and chemical testing center, equipped with advanced testing equipment such as NHO gas analyzers for metal material chemical analysis, Zeiss metallographic microscopes for metallographic testing, and high-temperature creep and rupture testing machines for mechanical property testing. Our testing capabilities are certified by ISO/IEC and CNAS, ensuring the accuracy and reliability of our test results.
Every finished tube undergoes rigorous testing, including:
- Surface inspection: Ensuring a smooth surface, free from scratches and visible defects, and a clean interior.
- Dimensional inspection: Precisely controlling the inner and outer diameters, length, and other dimensions within the customer's specified tolerances.
- Geometrical tolerance inspection: Ensuring dimensional accuracy, consistent wall thickness, and straightness.
- Non-destructive testing: Employing advanced eddy current and ultrasonic testing techniques for comprehensive internal quality inspection.
- Metallographic examination: Strictly controlling grain size to ensure a uniform material structure.
- Hardness testing: Ensuring that the product meets the required hardness.
Multiple protection for safe transportation
To ensure our products arrive at their destination in perfect condition, we implement multiple layers of protection during transportation and storage:
- Rust prevention: The outer surface of the tubes undergoes specialized rust prevention treatment to effectively prevent oxidation and corrosion.
- Wrapping protection: Multiple layers of straw ropes are used to cushion the tubes during transportation, preventing bumps and scratches.
- Drying treatment: The inner surface of the tubes is dried to prevent moisture ingress and subsequent rust formation.
- End cap protection: The tube ends are sealed with protective caps to prevent foreign object entry and protect the ends from damage.
Why choose extra large aluminum square tubes produced by vertical extrusion and round-to-square conversion?
The perfect combination of vertical extrusion and round-to-square conversion leads to significantly higher production efficiency and superior product quality for extra-large aluminum square tubes. Vertical extrusion ensures optimal material utilization, resulting in a seamless structure, dense microstructure, and high dimensional accuracy. Meanwhile, the round-to-square conversion process effectively reduces stress concentration, enhancing product performance. This combined process not only produces aluminum square tubes with high strength, toughness, and corrosion resistance but also accommodates diverse customer customization needs.
- High material utilization and low cost: Maximizes material utilization, minimizes waste and can utilize existing round tube molds, reducing production costs.
- Superior product quality: High extrusion pressure results in a dense microstructure, fine grain size, excellent ductility, high strength, and corrosion resistance.
- High production efficiency: The high degree of automation in both vertical extrusion and round-to-square conversion processes significantly improves production efficiency.
- High dimensional accuracy: Products exhibit precise dimensions and a smooth surface finish.
Advantages of extra large square tubes over round tubes
- Higher bending stiffness: The four right-angled sides of square tubes provide greater bending stiffness, making them ideal for applications requiring high rigidity.
- Improved torsional resistance: The cross-sectional shape of square tubes offers superior torsional resistance, making them suitable for structural frameworks.
- Better bending performance: The symmetrical structure and uniform stress distribution of square tubes allow for more even stress distribution during bending, reducing the risk of deformation and enhancing stability.
- Higher space utilization: The square cross-section of square tubes enables better space utilization during transportation and structural design, improving material efficiency.
- Easier connection and installation: The flat surfaces of square tubes make welding, joining, and installation more convenient, making them particularly suitable for construction and engineering applications.
Application areas for extra large aluminum square/rectangular tubes
Construction industry
Common alloys: 6061, 6063, 6082
With their high strength, structural rigidity, and corrosion resistance, extra large aluminum square/rectangular tubes are ideal for critical structures in large-scale buildings, bridges, and long-span roofs.
Contact us now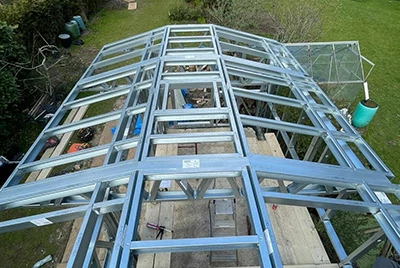
- Frame structures: Extra large thick-walled aluminum square/rectangular tubes are commonly used for frame structures in large buildings such as airports, stadiums, and exhibition centers. Their lightweight and high-strength properties help reduce building weight and improve seismic performance. Common alloys: 6061, 6082.
- Curtain wall frames: In some modern buildings, aluminum tube structures are directly used for facades to reduce weight. Large-diameter aluminum square tubes offer excellent structural support and weather resistance, making them ideal for curtain wall frame support. Common alloys: 6061, 6082.
- Long-span roofs: In long-span roofs, these tubes serve as beams, providing both lightness and sufficient strength and rigidity. Common alloy: 6082.
- Bridge structures: Extra large aluminum square tubes can be used as load-bearing components in bridges, reducing the bridge's self-weight and increasing its durability. Common alloys: 6005A, 6082.
Crane industry
Common alloys: 2014, 6061, 6082, 7075
Due to their excellent mechanical properties, corrosion resistance, and machinability, large-diameter square tubes play a crucial role in crane manufacturing. They can significantly extend service life and reduce maintenance costs.
Contact us now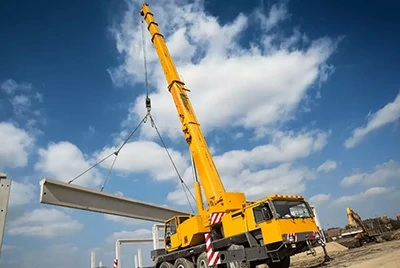
- Boom: Large-diameter thick-walled aluminum square tubes can be used for crane booms. Their high strength and lightweight properties allow for a larger load capacity and lower self-weight, thereby increasing the lifting height and working range of the crane. Common alloys: 2014, 7075.
- End beams: End beams connect the main beam and legs, bearing the loads transmitted from the main beam. The corrosion resistance of large-diameter thick-walled aluminum square tubes can extend the service life of end beams and reduce maintenance costs. Common alloys: 6082, 7075.
- Traveling mechanisms: Large-diameter thick-walled aluminum square tubes can be used to manufacture the frames of traveling mechanisms. The lightweight material makes them more flexible and ensures smooth and reliable crane movement. Common alloys: 6061, 6082, 7075.
Shipbuilding industry
Common alloys: 5083, 5086, 5059, 6061, 6082
Considering the long-term exposure of ships to seawater, corrosion resistance is a primary consideration for their structural materials. Large-diameter aluminum square tubes are widely used in ship hulls, decks, and other parts due to their excellent seawater corrosion resistance and high strength-to-weight ratio.
Contact us now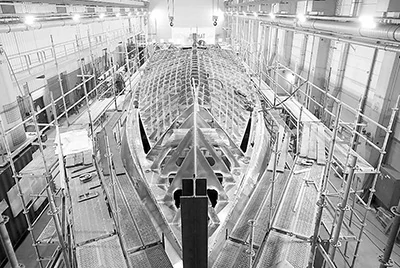
- Hull structure: Due to their lightweight, high strength, and corrosion resistance, large-diameter aluminum square/rectangular tubes are suitable for ship hull frames and support structures, reducing ship weight and improving fuel efficiency. Common alloys: 5083, 5059.
- Cabin and interior: Aluminum rectangular tubes can be used to manufacture frames, partitions, and decorative elements in cabins, providing strength while maintaining a lightweight structure. Common alloys: 5083, 6061.
- Large equipment supports: Large-diameter square tubes can be used as bases and support structures for installing shipboard equipment, ensuring safe and secure equipment fixation. Common alloys: 5059, 6082.
Machinery equipment industry
Common alloys:6061, 6063, 6082, 7075
With their excellent lightweight, high strength, and corrosion resistance, large-diameter square tubes are widely used in the manufacturing of machinery equipment. They serve as crucial components such as frames, brackets, and rails, enhancing equipment accuracy, stability, and service life.
Contact us now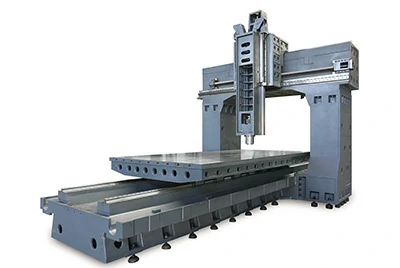
- Machine tool columns/beams: Large-diameter aluminum square tubes can be used as machine tool columns and beams. Their lightweight and high stiffness ensure the accuracy and stability of machine tools. Common alloys: 6061, 6082.
- Conveyor frames: Large-diameter aluminum square tubes can be used for conveyor frames in automated equipment. Their high hardness and corrosion resistance make them suitable for harsh environments. Common alloys: 6061, 6063.
- Robot links: Robot links made of large-diameter aluminum square tubes are lightweight, strong, and fatigue-resistant, improving the robot's movement speed and flexibility. Common alloys: 6061, 7075.
Chalco's large diameter aluminum tubes: a range of production capabilities
-
Φ1320mm Large Seamless Diameter Aluminum Pipe
Chalco utilizes a vertical extrusion process to produce large-diameter seamless aluminum round pipes with a maximum outer diameter of 1320mm and a length of up to 12mm, filling the gap in the market for high-performance, extra-large diameter aluminum pipes that were previously limited to the forging process.
-
Large Diameter Aluminum Pipe
Chalco possesses robust capabilities in aluminum pipe production, offering a wide range of products including large-diameter extruded aluminum pipes, forged aluminum pipes, vertically extruded aluminum pipes, and spiral welded pipes. Equipped with advanced production equipment and processes, Chalco can customize various specifications and alloys of aluminum pipe products to meet diverse customer needs.
-
Φ500-1000mm Large Diameter Aluminum Forged Pipe
Chalco produces large-diameter aluminum forged pipes with diameters ranging from 500 to 1000mm, offering exceptional strength, corrosion resistance, and fatigue resistance. These pipes are suitable for demanding applications in aerospace, marine engineering, and other industries.
-
Max.1580mm Ultra diameter spiral weld pipe
Chalco exclusively innovates low-temperature spiral welding technology and introduces world-leading advanced equipment to produce patented products - spiral weld pipe and its accessories. Machinable aluminum pipe diameter is Φ 219-1580mm.
Chalco can provide you the most comprehensive inventory of aluminum products and can also supply you customized products. Precise quotation will be provided within 24 hours.
Get a quote