The 1070 high-conductivity aluminum wire, with its 99.7% purity, excellent electrical conductivity, lightweight design, and corrosion resistance, is an ideal choice to meet the high demands of modern lightning protection systems.
Conductivity 1070 Aluminum Wire Specifications
Standards: ASTM B211, ASTM B232, ASTM B221, EN 573-3, ASTM B416-98, GB/T 3195, AS1222, IEC61089
Certifications: NEMA, UL 467, ISO 9001, UL, RoHS, SGS, MSDS
Popular products of conductivity 1070 aluminum wire
Cross-section options for conductivity 1070 aluminum wire
1070 Aluminum Round Wire
1070 aluminum round wire is commonly used in general lightning protection down conductor systems.
Contact us now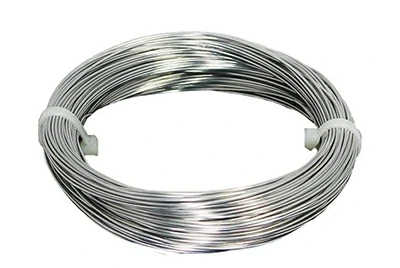
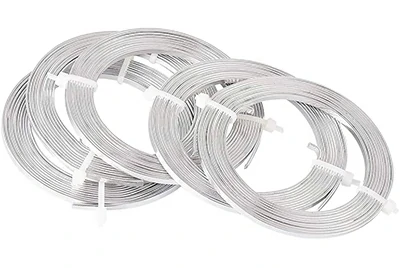
1070 Aluminum Oval / Flat Wire
1070 aluminum flat/oval wire is suitable for lightning protection systems that require higher current capacity and stronger mechanical strength.
Contact us nowWe also offer various 1070 conductivity aluminum wires in square, hexagonal, star, and trapezoidal cross-sections, and they can be customized according to your specific application needs.
Conductivity 1070 aluminum wire sizes and tolerances
Our 1070 aluminum wire is available in a diameter range from 0.8mm to 45mm, meeting the needs of various application scenarios.Quick Quote
Common diameters:
- 1.6mm: Suitable for lightning protection systems in small residential or low-load electrical equipment.
- 3mm: Ideal for lightning down conductors in small buildings.
- 4mm: Used in lightning protection systems for medium and small-sized buildings.
- 6mm: Widely used in lightning down conductors for regular residential and commercial buildings.
- 8mm: Suitable for lightning down conductors in medium to large buildings and high-rise structures.
- 10mm: Suitable for high-rise buildings and large industrial facilities, capable of handling larger lightning currents.
Diameter range and tolerance table:
Diameter (mm) | Tolerance (mm) |
0.80 - 0.99 | ±0.02 |
1.00 - 1.99 | ±0.03 |
2.00 - 2.99 | ±0.04 |
3.00 - 5.00 | ±0.05 |
Other composite metal products for lightning protection down conductors
Aluminum clad steel wire
Aluminum clad steel wire
Aluminum clad steel wire offers advantages such as higher current-carrying capacity, reduced energy loss, and improved mechanical strength.
Contact us now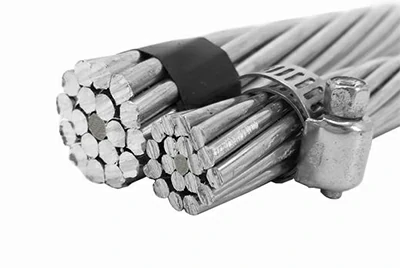
Aluminum clad steel wire offers advantages such as higher current-carrying capacity, reduced energy loss, and improved mechanical strength.
- Aluminum ratio: 5% - 25% (customizable as needed)
- Elongation: Not less than 1%, with good flexibility and adaptability
- Torsion performance: No breakage after 20 twists
- Conductivity: 14% - 40%, selectable based on requirements
- Weight: 5% lighter than steel
- Service life: Long-lasting and suitable for prolonged exposure to environmental conditions
Data sheet for aluminum-clad steel wire for lightning protection down conductors:
Clas | 14% IACS | 20.3% IACS A | 20.3% IACS B | 23% IACS | 27% IACS | 30% IACS | 35% IACS | 40% IACS |
Sectional Ratio of Al (%) | 13 | 25 | 25 | 30 | 37 | 43 | 52 | 62 |
Sectional Ratio of St (%) | 87 | 75 | 75 | 70 | 63 | 57 | 48 | 38 |
Weight Ratio of AL (%) | 5 | 10.4 | 10.4 | 12.9 | 16.9 | 20.7 | 27.3 | 36.1 |
Weight Ratio of ST (%) | 95 | 89.6 | 89.6 | 87.1 | 83.1 | 79.3 | 72.7 | 63.9 |
Copper-clad aluminum wire
Copper-clad aluminum wire
In lightning protection systems, copper-clad aluminum wire is used as a substitute for copper and aluminum conductors.
Contact us now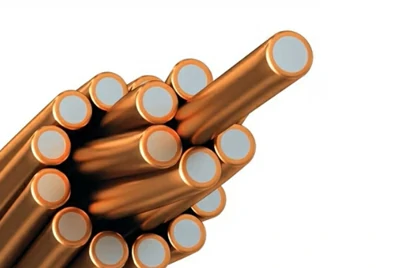
- Weight: 0.160 kg/m
- Diameter: 8mm
- Coating: Minimum 70 microns of copper coating
- Standards: TS EN 62305, TS EN 62561, NFC 17-102 / 2011
1070 galvanized aluminum wire
1070 galvanized aluminum wire
1070 galvanized aluminum wire is coated with a layer of zinc on its surface to enhance corrosion resistance and mechanical strength.
Contact us now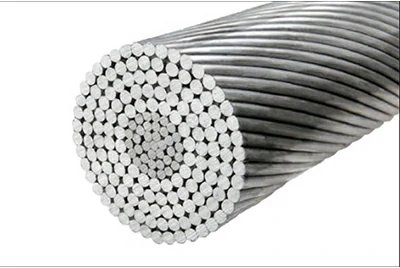
Common diameters: 3mm, 4mm, 6mm, 8mm (custom sizes available)
Why is galvanized aluminum wire used for lightning protection down conductors?
- Corrosion resistance: The zinc coating provides excellent corrosion protection, preventing the aluminum wire from being eroded and extending its service life.
- Mechanical strength: The galvanized layer improves the wire's tensile strength, abrasion resistance, and hardness.
- Cost-effectiveness: Compared to copper conductors, aluminum and galvanized aluminum wires are more affordable while offering good durability, making them a cost-effective solution.
Related aluminum products in lightning protection down systems
1070 aluminum welding wire
Used for welding aluminum components in lightning protection systems, ensuring good conductivity at the contact points.
Contact us now
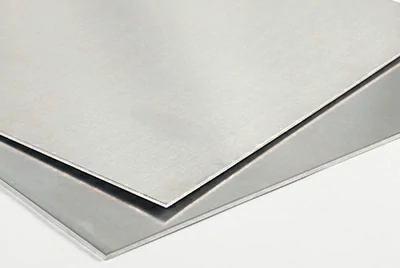
1070 aluminum plate
Used to manufacture various aluminum fittings in lightning protection systems.
Contact us now6082 T6 socket bolts
Connect the receiver and down conductor, safely conducting the lightning current.
Contact us now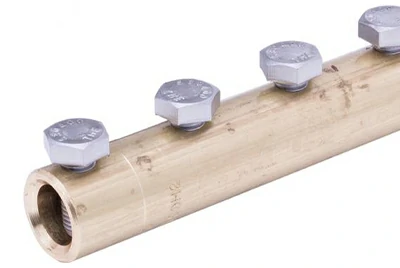
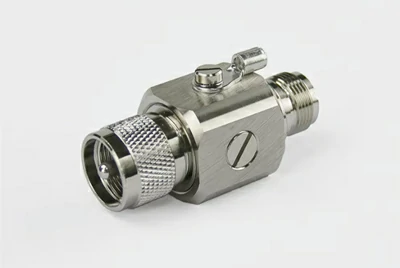
1070 cable connectors
Terminate the down conductor to the grounding system, ensuring safe dissipation of the lightning current.
Contact us nowConductivity 1070 aluminum wire chemical elements
Chemical Element | % Standard | % Actual |
Si | 0.20 max | 0.07 |
Fe | 0.25 max | 0.102 |
Cu | 0.03 max | 0.002 |
Mn | 0.03 max | 0.0015 |
Mg | 0.03 max | 0.001 |
Zn | 0.07 max | 0.008 |
Ti | 0.03 max | 0.002 |
Other (Each) | 0.03 max | - |
Others (Total) | - | - |
Aluminium (Al) | 99.7 min | 余量 |
Physical properties of conductivity 1070 aluminum wire
Physical Property | Value |
Electrical Conductivity: Equal Volume | 61 % IACS |
Electrical Conductivity: Equal Weight (Specific) | 200 % IACS |
Density | 2.70 g/cm³ |
Melting Point | 640 °C |
Thermal Expansion | 23 x10^-6 /K |
Thermal Conductivity | 230 W/m.K |
Specific Heat Capacity | 900 J/kg-K |
Modulus of Elasticity | 68 GPa |
Shear Modulus | 26 GPa |
Mechanical properties of conductivity 1070 aluminum wire
Diameter (mm) | Hard state | Annealed state | ||
Tensile strength (Kgf/mm²) | Elongation (%) | Tensile strength (Kgf/mm²) | Elongation (%) | |
0.80-1.00 | 16.5 min | 1.0 min | 7.5 min | 10 min |
1.01-1.50 | 16.0 min | 1.2 min | 7.5 min | 12 min |
1.51-2.00 | 16.0 min | 1.5 min | 7.5 min | 12 min |
2.01-3.00 | 16.0 min | 1.5 min | 7.5 min | 15 min |
3.01-4.00 | 15.0 min | 1.5 min | 7.5 min | 18 min |
4.01-4.50 | 15.0 min | 2.0 min | 7.5 min | 18 min |
4.51-5.00 | 15.0 min | 2.0 min | 7.5 min | 18 min |
Advantages of conductivity 1070 aluminum wire
- Excellent conductivity: With 99.7% pure aluminum, it has extremely high conductivity, efficiently conducting lightning current, reducing resistance, and protecting equipment.
- Lightweight: Aluminum is lighter than copper, reducing installation labor intensity and transportation costs.
- Cost-effective: Cheaper than copper conductors, providing a high-cost performance solution.
- Corrosion resistance: Aluminum is naturally corrosion-resistant, maintaining good performance even in humid and salty environments.
- Durability and long-term performance: It maintains stable performance even after long-term exposure to external environments, reducing the frequency of replacements.
- Easy installation: Optimized ring winding design allows pipe installers/plumbers to work effectively.
High conductivity 1070 aluminum wire for lightning protection finished products and applications
Lightning protection down conductor stranded wire
Stranded wire is more suitable for high-load lightning protection systems that require large-scale and long-distance installations.
Contact us now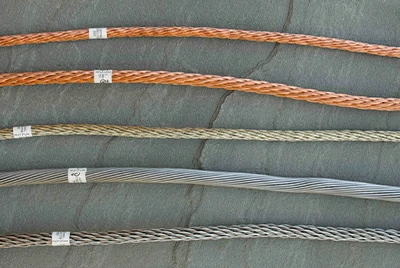
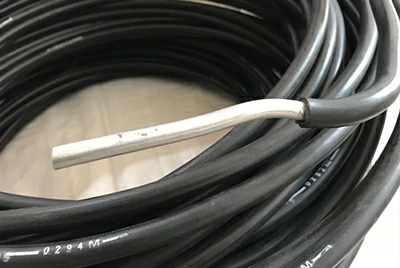
Lightning protection down conductor single wire
It requires high conductivity, especially suitable for simple installations.
Contact us nowReal-life use case:
In the lightning protection system of a seaside high-rise residential building, the customer chose 1070 aluminum wire as the down conductor due to the strong corrosive effect of salt mist and moisture on metal materials.
The high conductivity of aluminum ensures that the lightning current is quickly conducted, while the corrosion resistance of the aluminum wire is well-suited to the harsh seaside environment, reducing maintenance costs.Quick Quote
Factors affecting the conductivity of 1070 aluminum wire
The conductivity of aluminum wire is primarily influenced by factors such as purity, microstructure, and processing. Below are brief explanations of some key factors:
1. Purity of aluminum: The higher the purity of aluminum, the better its conductivity. Impurities such as silicon and iron in aluminum reduce conductivity, while minimizing these impurities can significantly enhance its electrical performance.
2. Cold rolling process: During the cold rolling process, the aluminum grains may elongate or stretch, and these grain structures can affect conductivity.
3. Grain boundaries: The boundaries between grains affect the flow of electrons, which can lead to a reduction in conductivity.
4. Alloying in aluminum: The addition of alloying elements during processing can cause an increase in lattice dislocations, which raises resistance.
5. Severe cold deformation: In the process of severe cold deformation, the grain orientation of the aluminum wire may shift from disordered to ordered, which can also impact conductivity.
Conductivity 1070 aluminum wire surface
- Smooth surface: The surface is flat and smooth, with no folds, bubbles, burrs, or sharp edges.
- No corrosion spots: There are no corrosion spots, ensuring long-term durability.
- No scratches or damage: The surface is free from scratches, dents, or other damage, ensuring the wire's strength and electrical conductivity.
Conductivity 1070 aluminum wire anodizing and welding
Anodizing enhances the corrosion resistance and surface hardness of the aluminum wire, making it highly suitable for lightning protection systems.
Welding is allowed, but the welded area must be within the acceptable deviation range and maintain the same mechanical strength and conductivity as the original material.
Chalco provides comprehensive quality inspection reports
We offer detailed quality inspection reports to ensure every 1070 aluminum wire meets stringent quality standards, including:
- Rust inspection: A mandatory item to ensure the aluminum wire surface is free of rust and meets corrosion resistance requirements.
- Vertical tensile test: The aluminum wire should withstand a vertical tensile force of 49N to guarantee its mechanical strength during use.
- Diameter tolerance and ovality deviation: Strict tolerance control to ensure the aluminum wire's dimensions meet the requirements.
- Bend test: The aluminum wire must pass a bend test of no less than 10 times to ensure it does not break easily during use.
- Chemical composition analysis: Ensures the aluminum wire complies with industry-standard chemical composition requirements for high conductivity and durability.
- Traceability records: Fully traceable, ensuring each batch of products has detailed inspection records for quality tracking and management.
Conductivity 1070 aluminum wire packaging and transportation
- Packaging specifications: Each aluminum wire coil weighs 20 kg. For 8mm aluminum wire, there are 18 coils per pallet (360 kg); for 10mm aluminum wire, there are 16 coils per pallet (320 kg).
- Safety protection: High-strength packaging materials are used to prevent damage during transportation, ensuring the aluminum wire remains intact.
- Efficient loading and unloading: The packaging design facilitates forklift handling, improving logistics efficiency and reducing labor costs.
- Cost-effective logistics: Optimized pallet space to reduce transportation costs and enhance economic efficiency.
Our packaging method ensures that the aluminum wire remains safe and intact during transportation, providing customers with an efficient and reliable logistics experience.
Selection of high conductivity aluminum wire alloys for lightning protection
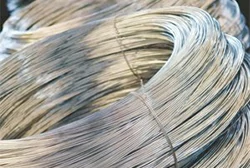
6101 Aluminum Wire
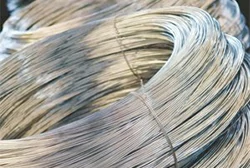
1060 Aluminum Wire
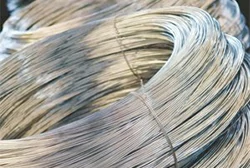
1370 Aluminum Wire
Alloy | Conductivity | Strength | Corrosion resistance |
6101 | 60% IACS | High (better than 1070) | Good |
1060 | 62% IACS | Lower | Excellent |
1350 | 62% IACS | Lower | Good |
Differences between 1070 lightning protection down conductor made of aluminum, steel, and copper
Material | Corrosion Resistance | Advantages | Disadvantages |
Copper | Good, but can corrode with sulfides | Excellent conductivity | Expensive, heavy |
Aluminum | Good, for environments with low sulfur and chlorides | Good conductivity, low cost | Not suitable for underground or concrete environments |
Galvanized steel | Average, poor in chloride environments | High strength, low cost | Lower conductivity, prone to corrosion |
Stainless steel | Excellent, for various corrosive environments | Excellent corrosion resistance, long lifespan | Lower conductivity, expensive |