Aluminum Oval Tubes are renowned for their unique elliptical cross-section, offering exceptional structural strength and design flexibility. Widely used in construction, automotive, aerospace, and other industries, their flat side design provides higher bending resistance in specific load directions, meeting the high-performance demands of modern engineering. Choosing Aluminum Oval Tubes means experiencing superior performance and expanded application possibilities.
Aluminum Oval Tube Specifications
Alloy | 6063, 6061, 5052, 7075, 6082, 6060, 3003 |
Temper | O, T5, T6, H14, H18 |
Major axis | 0.4" - 9.7"(10.16mm - 246.38mm) |
Minor axis | 0.188" - 4"(4.78mm - 101.6mm) |
Wall thickness | 0.0125" - 2.5"(0.32mm - 63.5mm) |
Length | 1 - 6m(custom cutting available) |
Tolerance | Architectural: ±0.5 mm High Precision: ±0.1 mm |
Standard | ASTM B221, ASTM B241, EN 755, ISO 9001, AS9100, NADCAP |
Chalco's Diverse Range of Oval Aluminum Extrusions
Chalco can provide a diverse selection of oval aluminum tubes, covering standard oval tubes, flat-sided oval tubes, as well as various types of seamless extruded tubes, thin-walled, thick-walled, and large-scale options to meet different industrial needs. Leveraging advanced extrusion technology and extensive production experience, we are able to offer customized solutions tailored to our customers'specific requirements.
Oval Aluminum Tube
Standard Oval Aluminum Tubes
Featuring an elliptical cross-section that delivers significant advantages in structural strength, design flexibility, and space utilization over conventional round aluminum tubes.
Contact us now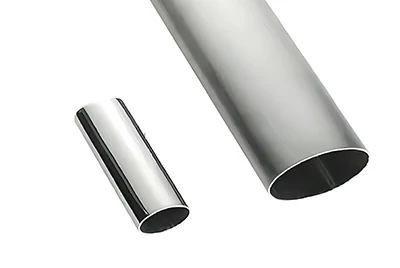
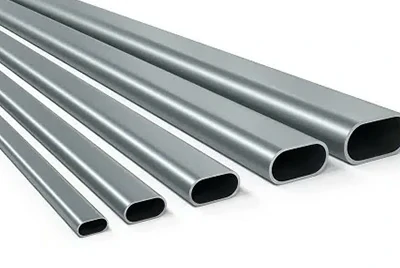
Elliptical Aluminum Tube
Flat Sided: Also known as Aluminium Flat Sided Oval Tube, these tubes have flat sides that provide increased bending resistance and enhanced spatial adaptability, ideal for applications such as radiator manufacturing where greater moment resistance is required.
Contact us nowMore types of oval tubes
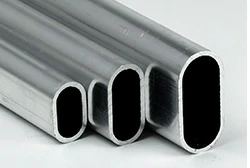
Thin-Walled Oval Aluminum Tubes
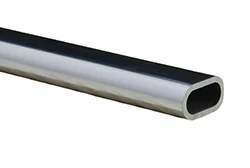
Thick-Walled Oval Aluminum Tubes
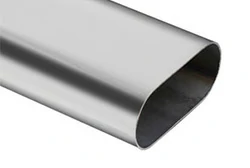
Large-Scale Oval Aluminum Tubes
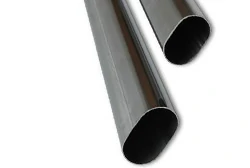
Seamless oval aluminum tubing
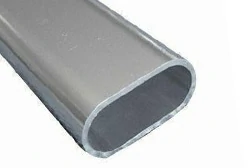
Structural oval aluminum tube
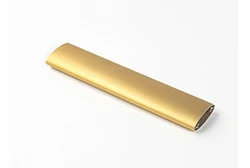
Anodized oval aluminum tube
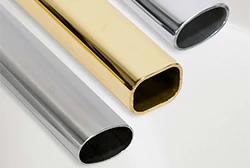
PVDF oval aluminum tube
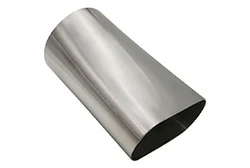
Oval to round aluminum tube
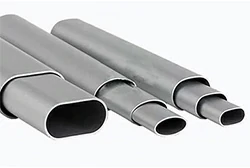
Telescopic oval aluminum tube
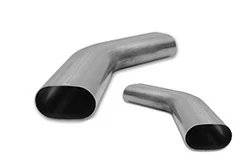
Custom oval aluminum tube bending
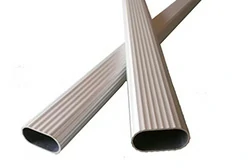
Decorative oval aluminum tube
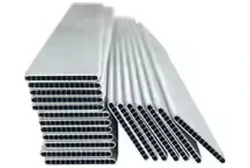
Oval aluminum tube for heat sink
Oval Aluminum Extrusion
Oval Aluminum Extrusions are aluminum profiles with an elliptical cross-section that offer excellent structural performance and aesthetically pleasing designs. They are widely used in construction, electronics, automotive, aerospace, and other fields.
Contact us now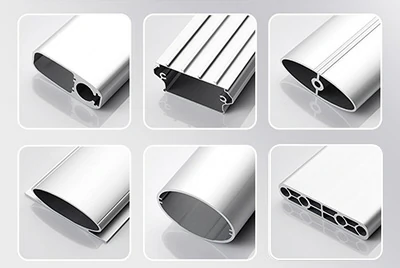
Oval Aluminum Extrusion
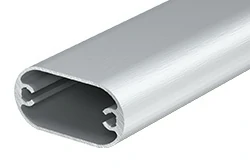
Oval aluminum tubing for furniture
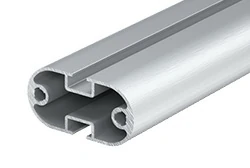
Oval Tubes with Slot for Handrail

Ovals with threaded channels
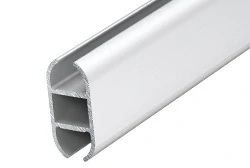
Ovals tube with openings on each end
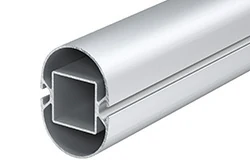
Ovals tube with grooves
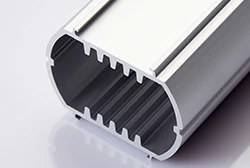
Large Oval Aluminum Extrusion


Most Popular Aluminum Oval Tubes
-
High surface finish, easily anodized, and excellent ductility (elongation ≥ 8%), widely used in building curtain walls, decorative profiles, furniture fittings, and electronic product housings.
-
High strength (tensile strength ≥ 310 MPa), moderate corrosion resistance, and good weldability; extensively used in automotive structural components, industrial equipment frames, and solar panel supports.
-
Ultra-high strength (tensile strength ≥ 572 MPa) with excellent fatigue resistance, making it ideal for aerospace components and high-performance machinery parts.
-
Stronger than 6061 with superior stress corrosion resistance, suitable for complex cross-section extrusions; widely applied in aerospace and marine components.
-
Moderate strength with outstanding corrosion resistance, especially against seawater, making it ideal for marine vessels and chemical equipment.
-
Excellent corrosion resistance (suitable for chemical environments) and good deep processing performance, widely used in chemical pipelines and refrigeration equipment.
Additionally, Chalco can provide oval aluminum tubes made from alloys such as 7003, 7005, 5083, 2024, 6060, etc., to meet diverse performance and property requirements in different applications. For specific needs, please contact us for customization.Quick Quote
Application Scenarios for Oval Aluminum Tubes
Construction & Decoration
Alloy: 6063, 6061
Surface Treatment: Anodizing, Powder Coating, Fluorocarbon Coating
Applications: Staircase handrails, railings, fences, frames, curtain wall sunshades, interior decoration
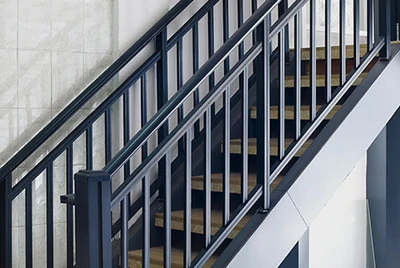
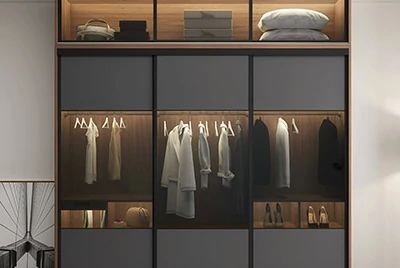
Furniture Manufacturing
Alloy: 6063-T5
Surface Treatment: Anodizing, Wood Grain Transfer
Wall Thickness: Thin-walled 0.32–2 mm
Applications: Furniture frames, wardrobe guides, shower curtain rods, towel racks, kitchen supports, adjustable track systems
Electronics Industry
Alloy: 5052, 6063
Surface Treatment: Anodizing, Electrophoretic Coating, Sandblasting
Colors: Gold, Champagne, Silver, White
Applications: Electronic product housings, heat sink assemblies, electronic components
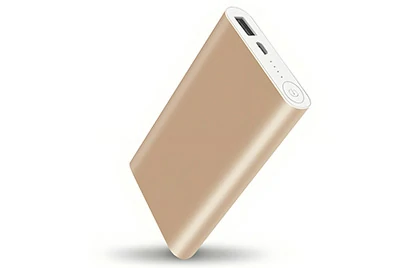

Marine Vessels
Alloy: 5052, 6061
Structure: Seamless
Standards: ASTM B241, ASTM B928
Applications: Boom platforms, ship bow railings, tower fabrication, T-shaped tops, tuna towers
Aerospace
Alloy: 6061, 7075
Structure: Seamless
Standards: ASTM B241, ISO 9001, AS9100
Applications: Aircraft structural components, interior parts, fuel pipelines, hydraulic pipelines

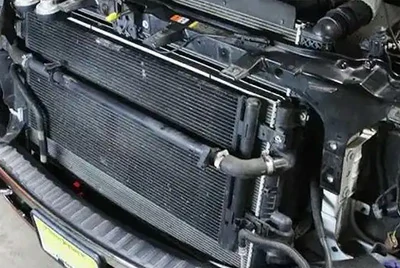
Automotive Manufacturing
Alloy: 6063-T5
Structure: Seamless
Applications: Car body structures, exhaust systems, mufflers, hydraulic system pipelines, luggage racks
Using oval tubes for radiator conduit installation can save up to 23% space.
Sports Equipment
Alloy: 6061, 7005, 7075
Surface Treatment: Anodizing, Powder Coating
Applications: Bicycle frames, trekking poles, tent supports, telescopic ladders
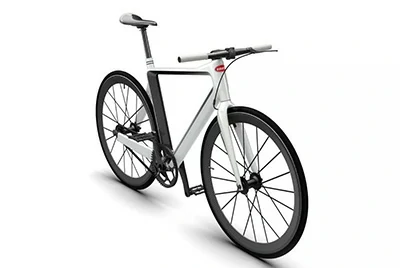
Customization and Deep Processing: Meeting Your Unique Needs
Our Oval Aluminum Tubes customization and deep processing services are designed to satisfy diverse requirements for both performance and aesthetics across various industries.
Surface Treatment Processes
- Anodizing: Forms a hard oxide film (10–25 μm thick) on the tube surface via electrochemical reaction, offering excellent wear resistance and insulation—ideal for outdoor architectural profiles and electronic housings.
- Powder Coating: Applies powder paint to the tube surface, typically with a coating thickness of 60–120 μm. With a wide range of colors available, this process meets decorative needs in furniture and display systems.
- Electrophoretic Coating: Creates a uniform coating on the tube surface with good salt spray corrosion resistance, suitable for automotive components and marine engineering.
- Brushing Treatment: Mechanically produces a fine texture on the tube surface, enhancing product feel; widely used in high-end consumer electronics and luxury packaging.
Deep Processing Services
- Precision Cutting: Employing laser or waterjet cutting technology with a precision of ±0.2 mm, meeting customized length and irregular end requirements.
- Bending and Forming: Utilizing cold bending or hot bending processes, the minimum bending radius can reach three times the tube diameter, suitable for manufacturing automotive exhausts and curved furniture frames.
- CNC Drilling: Uses computerized numerical control to accurately position multiple perforations, with tolerances controlled within ±0.1 mm, widely applied in producing mechanical assembly parts and heat sink brackets.
- Welding Processing: Using TIG or MIG welding techniques, with weld strength reaching over 90% of the base material, ideal for structural connections and pressure vessel fabrication.
Oval Aluminum Tube Size Chart
Standard Oval Aluminum Tube
Tube Diameter | Imperial (Inches) | Metric (Millimetres) | Tube Diameter | Imperial (Inches) | Metric (Millimetres) |
0.375″ | 0.44 x 0.26 | 11.2 x 6.7 | 1.125″ | 1.53 x 0.52 | 39.1 x 13.3 |
0.500″ | 0.60 x 0.36 | 15.3 x 9.3 | 1.125″ | 1.54 x 0.67 | 39.2 x 17.2 |
0.500″ | 0.65 x 0.28 | 16.5 x 7.2 | 1.125″ | 1.58 x 0.47 | 40.2 x 12.1 |
0.500″ | 0.66 x 0.30 | 16.9 x 7.8 | 1.250″ | 1.52 x 0.95 | 38.5 x 24.0 |
0.625″ | 0.74 x 0.48 | 19 x 12.3 | 1.250″ | 1.59 x 0.83 | 40.4 x 21.3 |
0.750" | 0.83 x 0.61 | 21.2 x 15.5 | 1.250″ | 1.59 x 0.87 | 40.6 x 22.3 |
0.875″ | 1.09 x 0.63 | 27.8 x 16.0 | 1.250" | 1.65 x 0.75 | 42.0 x 19.1 |
0.875″ | 1.15 x 0.52 | 29.4 x 13.3 | 1.250″ | 1.68 x 0.68 | 42.8 x 17.4* |
0.875″ | 1.08 x 0.52 | 27.6 x 13.4 | 1.375″ | 1.59 x 1.04 | 40.5 x 26.5 |
25mm | 1.28 x 0.66 | 32.6 x 16.8 | 1.375″ | 1.69 x 0.95 | 43.3 x 24.2 |
25mm | 1.31 x 0.62 | 33.4 x 15.9 | 1.500″ | 1.74 x 1.22 | 44.4 x 31.0 |
1.000″ | 1.14 x 0.79 | 29.0 x 20.0 | 1.500″ | 1.83 x 1.08 | 46.4 x 27.3 |
1.000″ | 1.26 x 0.64 | 32.1 x 16.5 | 1.500″ | 1.96 x 0.91 | 49.7 x 23.1 |
1.000″ | 1.31 x 0.53* | 33.4 x 13.5* | 1.500″ | 2.01 x 0.79 | 51.2 x 20.2 |
1.000″ | 1.33 x 0.57 | 33.8 x 14.5 | 1.500″ | 2.09 x 0.70 | 53.2 x 17.8 |
28mm | 1.33 x 0.87 | 33.8 x 22.3 | 1.500″ | 2.12 x 0.54 | 53.9 x 13.9 |
1.125″ | 1.37 x 0.77 | 34.8 x 19.5 | 1.750″ | 2.25 x 1.08 | 57.4 x 27.5 |
1.125″ | 1.46 x 0.70 | 37.3 x 18.0 | 2.000″ | 2.35 x 1.57 | 59.7 x 40.0 |
Flat-Sided Oval Aluminum Tube
Tube Diameter | Imperial (Inches) | Metric (Millimetres) | Tube Diameter | Imperial (Inches) | Metric (Millimetres) |
0.750" | 0.88 x 0.51 | 22.5 x 13 | 40.00mm | 1.90 x 1.14 | 46.2 x 29.0 |
0.875" | 1.02 x 0.59 | 25.9 x 15.1 | 40.00mm | 1.87 x 1.04 | 47.7 x 26.5 |
1.000″ | 1.24 x 0.60 | 31.5 x 15.2 | 1.500" | 1.75 x 1.00 | 45.0 x 25.0 |
1.000″ | 1.29 x 0.49 | 32.8 x 12.6 | 1.500″ | 1.96 x 0.71 | 50.0 x 18.2 |
1.125″ | 1.31 x 0.79 | 33.3 x 20.2 | 1.750" | 1.96 x 1.37 | 50.0 x 35.0 |
1.125″ | 1.45 x 0.59 | 36.9 x 15.0 | 1.625″ | 2.10 x 0.97 | 53.5 x 24.8 |
1.125″ | 1.51 x 0.51 | 38.5 x 13.0 | 1.750″ | 2.10 x 1.13 | 53.5 x 28.8 |
1.250″ | 1.53 x 0.78 | 39.0 x 20.0 | 1.750″ | 2.20 x 0.97 | 55.9 x 24.8 |
1.250" | 1.37 x 1.02 | 35.0 x 26.0 | 2.000″ | 2.35 x 1.57 | 59.7 x 40.0 |
Oval Aluminum Tube Purchasing Guide
Oval Aluminum Tubes are widely used in ship engineering, curtain wall construction, automotive manufacturing, and home decoration due to their unique cross-sectional design and structural advantages. When purchasing Oval Aluminum Tubes, please follow these professional recommendations to ensure precise material selection and reliable quality:
1. Clarify Your Needs and Application Scenarios
- Usage Classification: Determine the main purpose of the aluminum tube, such as structural support, decorative applications, or high-precision processing.
- Specification Requirements: Confirm the required outer diameter, wall thickness, length, and shape (e.g., standard oval or custom shape).
- Industry Standards: Ensure the selected product meets relevant international standards, such as ASTM B928, EN 755, ASTM B241, or AMS specifications, to satisfy industry requirements.
2. Choose the Appropriate Alloy Material
- 6061: Offers high strength and corrosion resistance, suitable for industrial and mechanical applications.
- 6063: Provides excellent surface treatment capabilities, commonly used in architectural decoration and electrical systems.
- 2024/7075: Possess ultra-high strength, ideal for aerospace applications.
- 5083/5052: Exhibit excellent corrosion resistance, suitable for marine engineering and chemical equipment.
3. Focus on Manufacturing Processes and Precision
- Manufacturing Process: Cold-drawn seamless oval tubes are ideal for high-precision, small-diameter tubes with superior surface quality and strict tolerances; extruded tubes offer cost-effectiveness, especially for large-diameter, thick-walled, or general precision requirements.
- Surface Treatment: Choose treatments such as anodizing, electrophoretic coating, or sandblasting to enhance durability and aesthetics.
4. Verify Supplier Qualifications
- Quality Control: Prefer suppliers with international quality management certifications (e.g., ISO 9001 or AS9100); ensure products meet industry standards (such as ASTM B241, ASTM B210, EN 754-8) and provide material performance test reports.
- Technical Capability: Prioritize manufacturers with backward extrusion equipment to better meet high-end application requirements; select suppliers capable of offering custom services for specific project needs.
5. Consider Logistics and Delivery Cycles
- For bulk orders, confirm the supplier’s inventory and delivery capabilities in advance to avoid production delays.
- Inquire about delivery times, packaging methods, and whether technical support is provided—especially for post-delivery maintenance and service of custom products. Understand transportation protection measures to ensure the aluminum tubes are not damaged during transit.
Following this guide will help you select the Oval Aluminum Tube products that best suit your project requirements, ensuring a smooth procurement process and project success.
FAQ
What Are the Advantages of Oval Aluminum Tubes Compared to Round Tubes?
- Structural Strength: The flat-sided design enhances bending resistance (improving bending strength by 15–20% at equal weight).
- Aerodynamics: Reduced wind resistance makes them suitable for applications such as building sunshades and ship structures.
- Space Utilization: Their shape fits narrow, elongated spaces more effectively (e.g., automotive radiator conduits).
Can Oval Aluminum Tubes Replace Round Tubes in Hydraulic Systems?
Yes, but you must calculate the equivalent cross-sectional area:
AOval=π×(Long Axis/2) × (Short Axis/2)
Ensure the pressure resistance matches; we recommend seamless cold-drawn tubes (tolerance ±0.05 mm).
How Can Cracking Be Prevented in Thin-Walled Oval Tubes (Wall Thickness < 2 mm) During Bending?
Process Choice: Prefer hot bending (heating to 200–300℃) or use a mandrel for support.
Alloy Recommendation: Select alloys with excellent deep processing properties, such as 3003-H14 or 6063-T5.
What Is Your Minimum Order Quantity?
For standard-sized stock oval tubes, there is no minimum order quantity—one tube can be sold. For custom production, our MOQ is 500 kg.
What Is the Typical Delivery Time for Custom Orders?
If you need standard-sized oval tubes, we prioritize matching our stock; delivery can be as fast as 3 days if available.
If standard sizes are required but out of stock, we can produce using existing molds with a delivery time of approximately 15 days.
For non-standard products requiring custom molds, the production cycle is typically 20–30 days.
What Information Is Needed for Custom Non-Standard Sections (e.g., Airfoil Shapes)?
- Mandatory Documents: Section drawings (in CAD/DWG format), required length/wall thickness, and application scenario description.
- Optional Support: Provide load parameters so the supplier can optimize the alloy and process.
Who Bears the Cost of Mold Development for Oval Extrusions?
Standard sizes are matched with existing company molds. For non-standard sizes requiring custom molds, the customer is responsible for the mold fee. For large orders, the mold fee may be waived; for small batch orders with long-term cooperation, we offer a "full quantity rebate” policy.
How Can the Cost of Oval Aluminum Tubes Be Reduced?
Bulk purchasing offers discounts; for example, orders ≥5 tons can enjoy approximately a 3% discount. Alternatively, based on the specific application, selecting 6063 Oval Aluminum Tubes instead of 6061 Oval Aluminum Tubes can reduce costs by about 15%.
How to Prevent Deformation of Large Oval Tubes During Sea Transport?
Typically, reinforced wooden crates combined with EPE impact cushioning are used. For tubes longer than 6 meters, a fixed frame is used with support points every 1.5 meters.