Precision Drawn Aluminum Tube is a type of aluminum alloy tube precisely manufactured through the cold drawing process, known for its high precision and excellent surface quality. It is widely used in industrial and engineering applications due to these qualities.
- Tolerance: ±0.02mm
- Surface Roughness: ≤Ra0.2μm
The product features lightweight, high strength, and excellent corrosion resistance, making it ideal for high-demand applications in sectors such as medical devices, automotive industry, aerospace, CNC machining, and telescopic applications, where performance requirements are stringent.
Click to view the Precision Drawn Aluminum Tube Product Guide
Dimensions of precision drawn aluminum tube
Parameters | Scope |
Outer diameter | 3mm - 220mm |
Wall thickness | 0.3mm - 10mm |
Length | 3m, 4m, 6m (customizable) |
Outer diameter tolerance | ±0.1mm |
Wall thickness tolerance | ±0.05mm |
Surface roughness | ≤Ra0.2μm |
Straightness | ≤0.3mm/M |
Recent collaboration cases
Below are some specific cases of the precision aluminum tubes we recently produced, showcasing our capabilities in tight tolerances, high surface quality, and customized services.
We maintain close cooperation with clients from various industries, covering aerospace, industrial machinery, shipbuilding, and many other fields.
Our clients include those in the aerospace sector, CNC machining businesses, and small to medium-sized end customers (due to confidentiality agreements, further details cannot be disclosed).
-
2024 T3 Precision Drawn Aluminum Tube
Dimensions: 25mm (OD) x 2.5mm x 495mm
Standard: ASTM B210, WW-T-700/3
Quantity: 4.5 tons
Precision Drawn Seamless Thin-Walled -
2A12 T4 Precision Aluminum Tube
Dimensions: 34mm(OD) x 1.0mm x 3000mm, 165mm(OD) x 2.0mm x 5000mm
Standard: GJB 2379A-2015, GB/T 3190-2020
Wall Thickness Tolerance: ±0.15mm Quantity:8tons
Thin-Walled Seamless Drone Applications -
2A11 T4 Precision Drawn Aluminum Tube
Dimensions: 42mm(OD) x 1.0mm x 3000mm
Standard: GJB 2379A-2015, GB/T 3190-2020
Quantity: 5.5 tons
Thin-Walled Seamless CNC Machining -
5083 H32 Precision Drawn Aluminum Tube
Dimensions: 60mm(OD) x 5.0mm x 6020mm
Standard: ASTM B210,
Quantity: 12 tons
Cold Drawn Seamless Marine Applications -
6005 T6 Precision Drawn Aluminum Tube
Dimensions: 64mm(OD) x 3.5mm x 1400mm, 90mm(OD) x 3.5mm x 1600mm, 115mm(OD) x 3.5mm x 1600mm
Standard: EN 573, EN 754
Quantity: 3.5 tons for each specification, totaling 10.5 tons
Cold Drawn Thin-Walled Mechanical Components -
5A02 O Precision Drawn Aluminum Tube
Dimensions: 90mm(OD) x 1.5mm x 3000mm
Standard: GJB 2379A-2015
Quantity: 4 tons
Cold Drawn Thin-Walled Aerospace Applications -
5083 O Precision Aluminum Tube
Dimensions: 166mm(OD) x 3.0mm x 6020mm, 219mm(OD) x 3.0mm
Standard: GB/T 6893-2010
Quantity: 8 tons
Thin-Walled Seamless Military Applications
We offer customized precision drawn aluminum tubes in various alloy conditions, covering a wide range of specifications, including different diameters, wall thicknesses, and lengths. Whether you need small-diameter high-precision tubes or large-sized structural tubes, we can meet your requirements. We look forward to your inquiry to provide the same high-quality solutions and support the growth of your business.
Are You Looking for an Aluminum Supplier?
If you need a professional aluminum supplier to provide you with high-quality, cost-effective aluminum, we will be your best choice.
Precision drawn aluminum tube product guide
What is a precision aluminum tube?
A Precision Drawn Aluminum Tube is a high-quality aluminum tube produced through a precision cold-drawing process. This process involves multiple precise drawing steps at room temperature, using high-precision molds and strict process control to achieve:
- High dimensional accuracy: Dimensional tolerances are controlled within a minimal range to ensure critical dimensions such as inner and outer diameters, and wall thickness meet strict technical requirements.
- Excellent surface quality: The surface is smooth and free of visible scratches, dents, or oxidation spots, often requiring no additional surface treatment.
- Enhanced mechanical properties: Through cold working and possible intermediate annealing, the strength, hardness, and toughness of the aluminum tube are improved, meeting specific application requirements.
Our featured precision aluminum tubes
High Strength Precision Drawn Aluminum Tubes
Alloy:6061, 6082, 7075, 2024
Condition:T6, T6511
Applications:Bicycle frames, aircraft fuel conduits, aerospace seat components, optical instrument parts, etc.
Ultra-Thin Wall Precision Drawn Aluminum Tubes
Alloy:6061, 6063, 7075
Wall Thickness:≥0.5mm
OD/Wall Thickness Ratio:>30
Tolerance:±0.02mm
High Surface Precision Aluminum Tubes
Alloy: 6060, 6061, 6063, 6082, 3003, 7075
Surface Roughness:Ra0.2μm
Applications:Medical components, outdoor equipment, appearance parts

Precision Drawn Aluminum Coils
Alloy:1070, 1100, 3003, 3103
OD: 4-28mm
Wall Thickness:0.3-1.5mm
Applications:Air conditioning systems, fuel systems, cooling systems
Precision Drawn Aluminum Telescopic Tubes
Alloy: 6001, 6063, 6005, 7003, 7075
Processing Method:Extrusion, Drawing
Applications:Tripods, trekking poles, tent poles, fishing rods
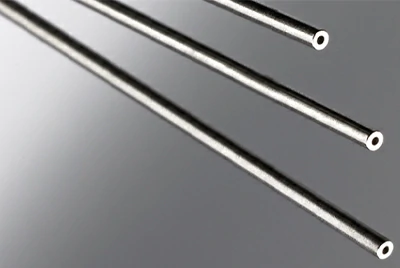
Small Diameter Precision Aluminum Tubes
Diameter:3-10mm
Wall Thickness:0.3-2mm
Applications:Headphone parts, makeup tubes, precision parts, CNC machining
Production process of precision aluminum tube
Aluminum Ingot Melting: The aluminum ingot is heated to its melting point, turning into liquid aluminum. During this process, temperature control is critical to ensure the aluminum melt is pure. This reduces impurities and enhances the quality of the aluminum material.
Casting of Billets: The molten aluminum is poured into molds to form aluminum billets. The mold design and cooling speed are crucial for the internal quality of the aluminum billets. Proper control of these factors ensures a denser structure in the billets, which facilitates subsequent processing.
Extrusion: The cast aluminum billets are fed into an extrusion press, where they are forced through specific molds under high pressure to form the basic shape of the tube. Extrusion determines the tube's external shape and dimensions, as well as its internal structure and strength.
Cold Drawing: After extrusion, the tube undergoes further cold drawing to achieve more precise dimensions and better surface quality. The cold drawing process involves multiple stretches that improve the dimensional accuracy, reduce wall thickness errors, and make the surface smoother. Cold drawing also refines the internal structure, enhancing strength and toughness.
Heat Treatment: Depending on the requirements, the cold-drawn tubes may undergo heat treatment, such as annealing or solution treatment. The purpose of heat treatment is to optimize the material's internal structure, eliminate internal stresses created by cold working, and enhance its strength and ductility.
Surface Treatment: Aluminum tubes undergo surface treatment to improve their corrosion resistance and appearance. Common surface treatments include anodizing, polishing, and powder coating. Anodizing creates a protective layer on the aluminum tube's surface, increasing its corrosion resistance. Polishing results in a smoother surface, and powder coating adds decorative qualities.
Inspection and Packaging: After all processing is complete, the finished products undergo rigorous inspection, including measurement of dimensions, surface quality checks, and testing of mechanical properties. Qualified products are then packaged with protective materials to ensure they are not damaged during transportation.
Advantages of precision drawn aluminum tubes
- High Precision and Small Tolerances: Dimensional precision is high, with tolerances controlled within ±0.02mm, ensuring product consistency.
- Excellent Surface Quality: The surface is smooth, free from voids, vibrations, or defects, and the surface roughness can reach below Ra0.2μm.
- Lightweight and High Strength: The aluminum alloy material is lightweight yet strong, making it easy to transport and install.
- Good Corrosion Resistance: Aluminum alloys possess natural corrosion resistance, making them suitable for a variety of environments.
- Ease of Fabrication and Forming: The material can be bent, welded, and cut easily to meet complex design requirements.
- High Consistency: Batch production ensures high consistency in products, ensuring reliability in subsequent assembly and use.
Best applications of precision aluminum tubes
Aerospace and Defense: Used to manufacture lightweight, high-strength aerospace conduits, radar communication fittings, and seat system components.
Medical Equipment: Used in the production of wheelchairs, stretchers, and medical instrument parts, requiring high precision and superior surface quality.
Automotive Manufacturing: Used in shock absorbers, suspension tubes, engine manifolds, hydraulic cylinders, and pneumatic systems, offering high strength and excellent machinability.
CNC Applications: CNC machining requires strict dimensional accuracy for tubing, and using tight-tolerance precision aluminum tubes reduces steps like boring and makes programming and automated production easier.
Telescopic Applications: Telescopic tubing requires uniform wall thickness, small tolerances, and good straightness to ensure smooth telescoping. Using precision aluminum tubes improves yield and is suitable for applications such as antennas, measuring rods, tripods, fishing rods, trekking poles, and tent poles.
Heat Transfer Applications: In HVAC systems, automotive cooling systems, and solar thermal applications, precision aluminum tubes are widely used due to their small tolerances and excellent thermal conductivity.


Recommended products related to precision aluminum tube
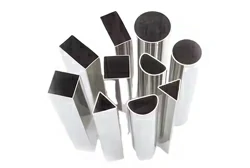
Customized precision aluminum Tubes
Chalco can provide you the most comprehensive inventory of aluminum products and can also supply you customized products. Precise quotation will be provided within 24 hours.
Get a quote