As an expert in the aluminum industry with many years of experience, Chalco has innovatively introduced a series of high-performance Aluminum Composite Panels through its outstanding aluminum processing technology. Chalco Aluminum Composite Panels perfectly combine the lightweight, robust, and versatile properties of aluminum and are widely used in aerospace, construction, and transportation sectors, providing you with superior material solutions.Quick Quote
What Is an Aluminum Sandwich Panels?
An Aluminum Sandwich Panels is a revolutionary composite material composed of two outer layers of aluminum and a lightweight core material "sandwiched” in between. This ingenious "sandwich” structure endows the panel with exceptional performance:
- Lightweight Yet Strong: It harnesses the lightness and strength of aluminum, significantly reducing structural load.
- Multifunctional: The core imparts thermal insulation, sound insulation, fire resistance, and energy absorption properties, meeting diverse application needs.
- Aesthetically Pleasing and Durable: The aluminum surface is attractive, weather-resistant, and corrosion-resistant, ensuring long-lasting durability.
Aluminum Sandwich Panels are widely used in aerospace, military industries, rail transportation, modern architecture, and advertising displays, making them the ideal choice for high-performance materials in various sectors.
As a professional aluminum supplier, Chalco deeply understands the differentiated performance requirements across industries. We have selected a variety of core materials and facings to develop five series of Aluminum Sandwich Panels, with customizable aluminum facings—each with its own distinct features to suit your specific application scenarios:
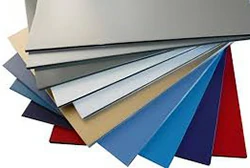
With a polyethylene core, this lightweight panel is ideal for interior and exterior decoration, wall cladding, facades, vehicle interiors, and signage.
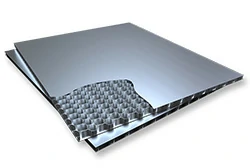
Featuring a hexagonal aluminum honeycomb core, it offers excellent stability and is widely used in subway cars, train stations, ceilings, and partitions.
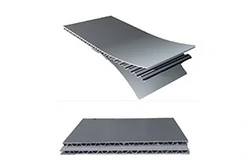
Aluminium Corrugated Core Panel(ACCP)
Featuring an aluminum corrugated core, it is more cost-effective than honeycomb cores and finds wide use in roof panels and vehicle side panels.

Featuring an aluminum foam core, it delivers sound, energy, and shock absorption. Used in aerospace, military, automotive, and construction sectors.

These panels cost less than honeycomb aluminum yet maintain robust structure - ideal for curtain walls, shipbuilding, interior decoration...
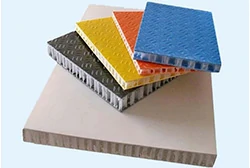
Customized Panel
Panel color, surface treatment, and deep processing can be customized to meet personalized design and functional requirements for various applications.
Aluminum Composite Panel(ACP)
Aluminum Composite Panel(ACP) is a composite material made of two layers of aluminum sheets and an intermediate core material (such as polyethylene, mineral-filled material, or a honeycomb structure).
Contact us now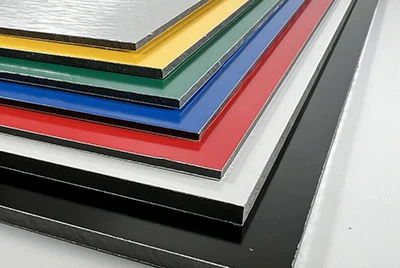
Structure of Aluminum Composite Panel(ACP)
- Surface Layer: Two painted or coated aluminum sheets (typically with a thickness of 0.2~0.5mm), with surface treatments including fluorocarbon resin (PVDF), polyester resin (PE), mirror finish, brushed, wood grain transfer, etc.
- Core Material: The intermediate layer is made of lightweight materials such as polyethylene (PE), fire-retardant mineral core (FR), foamed PVC, or fireproof mineral fillers.
- Adhesive: Thermoplastic or thermosetting adhesive ensuring a firm bond between the core and the aluminum sheets.
Specifications of Aluminum Composite Panel(ACP)
Panel Alloy | 3003, 5052, 5005, 6061 |
Thickness | 2mm-6mm |
Standard Sizes | Metric: 1220x2440mm, 1250x2500mm, 1500x3000mm; Imperial: 4' x 8', 4' x 10', 48”x96”, 60”x120”, Customizable |
Custom Sizes | Width: 1000mm, 1220mm, 1250mm, 1500mm, 1800mm; Length: Maximum 6500mm, Customizable |
Panel Thickness | 0.2mm, 0.3mm, 0.5mm, 1mm, Customizable |
Tolerance | Length: ±4mm; Width: ±2mm; Thickness: ±0.2mm (2-4mm); ±0.3mm (5-6mm) |
Panel Surface Type | PVDF, PE, Mirror, Brushed, Oxidized, Matte, etc. |
Core Material Type | Non-Toxic Polyethylene (LDPE), PVC, PE, Flame-Retardant Core (FR) |
Standards | EN 13501-1, ASTM E84 |
Chalco Offers Various Functions of Aluminum Composite Panel(ACP)
-
Fire-Resistant Aluminum Composite Panel
Utilizes a mineral-filled fire-resistant core to provide outstanding fire protection, making it suitable for high-rise buildings and sensitive areas.
-
Signage Aluminum Composite Panel
The panel is relatively thin (0.2-0.3mm), specifically designed for signage and advertising. It is widely used for indoor and outdoor signage, exhibitions, displays, and store decorations.
-
Lightweight Aluminum Composite Panel
Featuring a thinner profile (2-3mm), it is lightweight, easy to install, and offers excellent rigidity—ideal for signage, interior walls, and lightweight external applications.
-
Heavy Duty Aluminum Composite Panel
Employs a thicker aluminum skin (0.8mm) to deliver outstanding tensile and yield strength, perfect for applications requiring high strength.
-
Reflective Aluminum Composite Panel
Boasts a polished surface with high reflectivity, suitable for designs and constructions that demand enhanced reflectivity and striking visual effects.
-
Brushed Aluminum Composite Panel
Undergoes a brushing process to achieve a metallic texture, making it widely applicable for interior decoration and high-end furniture.
-
Anodizing Aluminum Composite Panel
Features an anodized surface treatment that enhances corrosion resistance and weatherability, ideal for building facades, outdoor advertising, and caravans.
-
PVDF Aluminum Composite Panel
Coated with a variety of colors to meet diverse design requirements, it is extensively used for building exteriors and advertising signage.
-
Wooden Aluminum Composite Panel
Offers over 20 wood grain options, making it popular for public exhibition halls, banks, hotels, and interior decoration.
-
Extra Wide Aluminum Composite Panel
With a thickness of 6-20mm and a maximum width of 2m, it is perfect for large outdoor billboards, building curtain walls, and other expansive applications.
Why Choose Aluminum Composite Panel(ACP)?
- Lightweight and High Strength: It weighs only 1/3~1/5 of a solid aluminum panel, yet offers excellent impact resistance and bending strength, making it ideal for large-scale installations.
- Cost-Effective: More economical than pure metal or stone, with lower processing and transportation costs.
- Flexible Design: Supports a variety of colors (solid, metallic, wood grain/stone pattern), surface finishes (high gloss, matte, mirror, brushed) and custom sizes.
- Durability: Weather-resistant, corrosion-resistant, and UV-resistant, ensuring a long service life (over 20 years outdoors).
- Versatile Functionality: Optional fire-resistant core (A级不燃) and thermal-sound insulation core materials to meet different requirements.
- Easy Processing: Can be cut, bent, or punched, and is compatible with UV printing, engraving, and silk screen printing.
Application Fields Of Aluminum Composite Panel(ACP)
- Building Facades: Used for exterior curtain walls, roofs, ceilings, and interior partitions, providing both aesthetics and functionality.
- Advertising Signage: Widely used for outdoor billboards, lightboxes, POP displays, signboards, and display panels.
- Interior Decoration: Applied to interior walls, ceilings, and partitions to enhance spatial beauty.
- Transportation: Suitable for RV/bus interiors, ship decks, and metro station decorations.
- Furniture Manufacturing: Used for furniture surface decoration, offering a variety of design options.
Aluminum Honeycomb Panel
The Aluminum Honeycomb Panel is a composite material composed of two layers of aluminum sheets and an intermediate honeycomb aluminum core. Its honeycomb structure, inspired by natural honeycombs, provides excellent strength and rigidity while maintaining lightweight characteristics.
Contact us now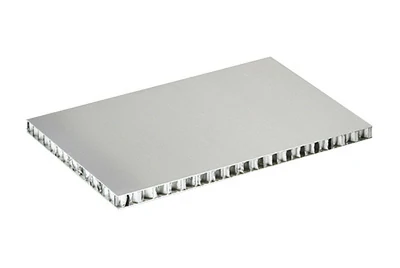
Structure Composition of Aluminum Honeycomb Panel
- Surface Layer: Pre-painted aluminum sheets (commonly used alloys AA3003/AA5005, thickness 0.03~0.08mm).
- Core Material: Honeycomb aluminum core (thickness 6~25mm, hexagonal cell structure).
- Adhesive: Brazing bonding and high-performance adhesives (ensuring a firm bond between the core and the surface layers).
Specifications of Aluminum Honeycomb Panel
Panel alloy | 5052, 5005, 6061, 6082, 7075 |
Honeycomb core alloy | 3003, 3105, 5052, 5056 |
Bond method | Brazing, adhesive |
Panel thickness | 0.125”, 0.25”, 0.375”, 0.5”, 0.625”, 0.75”, 1” |
Honeycomb core thickness | 0.045”, 0.17”, 0.245”, 0.42”, 0.55”, 0.67”, 0.92” |
Total thickness | 10mm, 15mm, 20mm, 25mm |
Standard size | 1200x2400mm, 1220x2440mm, 1250x2500mm, 1500x3000mm 2000x6000mm |
Panel surface type | PVDF, polyester (PE), mirror, brushed, oxidized, matte, etc. |
Standard | ASTM B209, AMS-QQ-A-250, AMS-C-7438, ASTM E84, EN 13501-1 A2 |
Chalco Offers Various Types of Aluminum Honeycomb Panel
-
Brazed Aluminum Honeycomb Panel
Utilizes a brazing process to bond the honeycomb core with the aluminum sheets, delivering excellent strength and high-temperature resistance. Widely used in aerospace and high-temperature environments.
-
Anodizing Aluminum Honeycomb Panel
Enhances corrosion resistance and weatherability through anodizing treatment, making it ideal for outdoor environments.
-
Perforated aluminum honeycomb Panel
Features perforated surfaces to improve breathability and decorative appeal, commonly applied in building curtain walls and interior decoration.
-
Checkered aluminum honeycomb panels
Exhibits checkered designs on the surface for anti-slip and decorative effects, extensively used in floor and wall decoration.
-
Curved fireproof honeycomb panel
Combines a curved design with fireproof properties, suitable for marine vessels, buildings, and furniture, offering both aesthetics and safety.
-
Custom Shaped Aluminum Honeycomb Panel
Provides various shapes (curved, circular, and spherical) and sizes per customer requirements to meet specific design needs.
Why Choose Aluminum Honeycomb Panel?
- Lightweight and High Strength: With a low density (approximately 45kg/m³), the honeycomb structure maintains high strength while being significantly lighter than a solid aluminum panel of the same thickness.
- Stable and Anti-Deformation: The honeycomb structure offers high bending rigidity and excellent surface flatness, ensuring long-term resistance to warping.
- Excellent Thermal and Acoustic Insulation: The porous structure of the honeycomb core effectively reduces the transmission of heat and sound.
- Fire Resistance: Both the core material and aluminum skins are non-combustible, achieving a fire rating of A2 and complying with building codes.
- Multifunctionality: Supports bending and forming (curved designs), surface coatings (PVDF/PE coatings), and customizable sizes and thicknesses.
- Recyclability: The Aluminum Honeycomb Panel is 100% recyclable, meeting sustainable development requirements.
Application Fields of Aluminum Honeycomb Panel
Building Decoration
Exterior Cladding, Aluminum Curtain Wall
Ceiling, Interior Partition, Artistic Shaped Walls
Alloy: 3003, 3101
Contact us now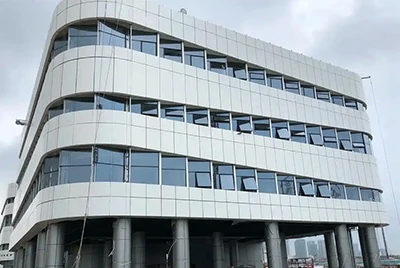
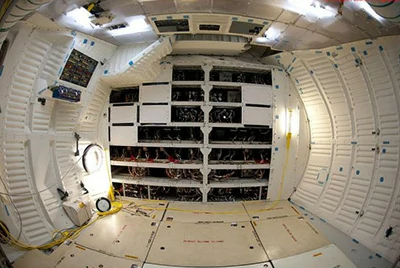
Aerospace
Aircraft Control Surfaces, Engine Compartments, Aircraft Cabin Walls
Energy Absorbers, Satellite Components
Alloy: 5052, 5056
Contact us nowMarine Vessels
Ship Decks, Structural Partitions
Ship Interiors, Wall Panels
Thickness: 10-20mm
Contact us now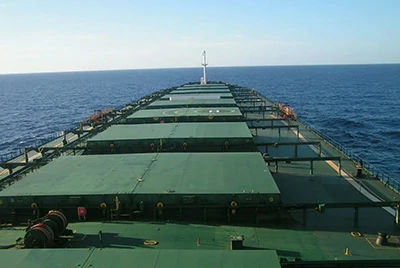
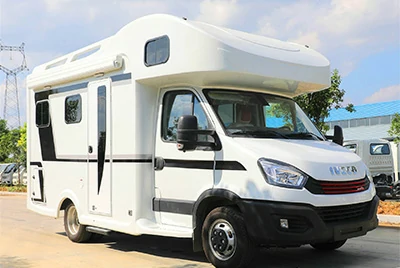
Transportation
High-Speed Rail/Metro Car Interiors
RV Bodies, Bus Wall Panels
Thickness: 10-20mm
Contact us nowIndustrial and Furniture
Elevator Interiors, Exhibition Booth Frames
High-End Furniture Panels, All-Aluminum Furniture, Storage Cabinets
Thickness: 6-10mm
Contact us now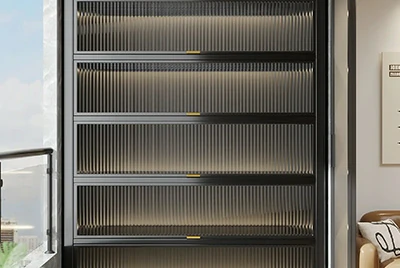
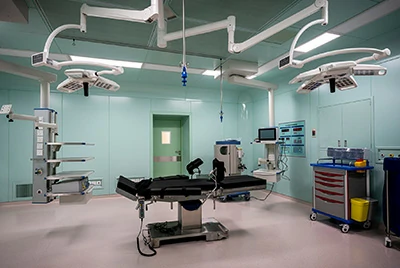
Medical Cleanliness
Hospital Operating Rooms, Sterile Wards
Laboratory Partitions, Cleanroom Wall Panels
Thickness: 10-15mm (Easy to Clean)
Contact us nowAluminium Corrugated Core Panel(ACCP)
Aluminium Corrugated Core Panel (ACCP) is a sandwich structure with a corrugated aluminum core bonded to two aluminum sheets using high-strength adhesive. Its innovative design replaces traditional honeycomb or foam cores, combining lightweight properties with high strength.
Contact us now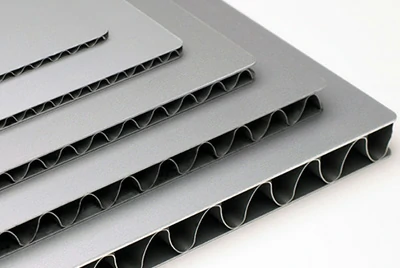
Structure Composition Of Aluminium Corrugated Core Panel(ACCP)
- Surface Layer: Pre‐painted or powder‐coated aluminum sheets.
- Core Material: Corrugated aluminum sheet, cold‐formed into a ripple or curved structure.
- Adhesive: Brazing, thermosetting two-component resin adhesive, ensuring a firm bond between the core and the panel's curved adhesive surface.
Specifications Of Aluminium Corrugated Core Panel(ACCP)
Panel alloy | 3003, 3105, 5052, 5005 |
Honeycomb core alloy | 1050, 1060, 3003 |
Bond method | Brazing, Adhesive (Polyurethane) |
Panel thickness | 0.3mm, 0.55mm, 0.75mm, 0.9mm, 1.0mm |
Corrugated core thickness | 0.2mm, 0.3mm, 0.5mm |
Nominal height of fluted core | 2mm, 4mm, 6mm, 8mm, 12mm, 16mm, 20mm, 22mm, 25mm |
Standard dimensions | 1000x2050mm, 1200x2400mm, 1220x2440mm, 1250x2500mm, 1500x3000mm, Tolerance ± 5mm, customizable size |
Weight | 4.02kg/㎡, 4.23kg/㎡, 4.33kg/㎡, 4.54kg/㎡, 4.80kg/㎡, 5.0kg/㎡, |
Panel surface type | Fluorocarbon (PVDF), polyester (PE), mirror, brushed, oxidation, matte, etc. |
Standard | ASTM B209, AMSQQ-A-250, EN 13501-1 A2 |
Why Choose Aluminium Corrugated Core Panel(ACCP)?
- Fire Resistance: Utilizes a pure aluminum core that complies with strict fire safety standards (A2), making it suitable for projects with high fire protection requirements.
- Sound Absorption And Noise Reduction: The specially designed V-shaped core causes sound to reflect off the panel and attenuate.
- Lightweight And High Strength: Weighing only 4.3~5kg/m² (80% lighter than honeycomb panels), it offers compressive and bending strength comparable to solid aluminum while significantly reducing weight.
- Acoustic Performance: The corrugated structure reflects sound waves, enhancing sound insulation by ≥35dB, ideal for noise-sensitive environments (e.g., concert halls, highways).
- Thermal Performance: Corrugated channels form air layers that provide excellent thermal insulation and low thermal conductivity, reducing building energy consumption.
- Cost Efficiency: Lower in cost than honeycomb panels, and its lightweight nature reduces the need for support structures (e.g., purlins), thereby lowering overall costs.
- Environmentally Friendly: The all-metal structure is 100% recyclable, meeting sustainable development requirements.
- Processability: Easy to cut, perforate, and bend, supporting the fabrication of non-standard shapes (curved, contoured) to suit complex architectural designs.
Application Fields Of Aluminium Corrugated Core Panel(ACCP)
Building And Decoration
Exterior Curtain Walls, Ventilated Facades, Sunshades, Awnings
Ceilings, Interior Partitions, Artistic Shaped Walls
Sound Barriers (Highways, Theaters)
Contact us now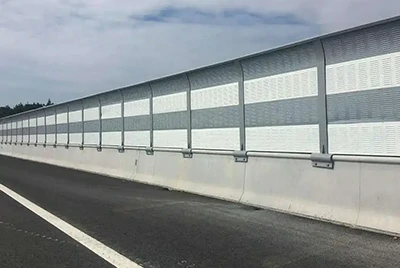
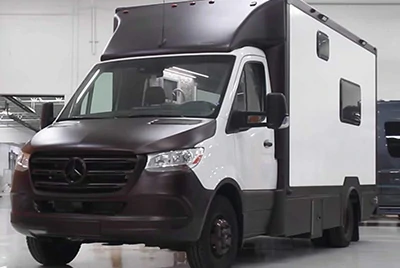
Transportation
High-Speed Rail/Metro Ceilings, Raised Floors
RV Bodies, Partition Walls, Ship Cabins
Commercial Vehicle Exteriors
Contact us nowIndustry And Energy
Equipment Protective Covers, Acoustic Rooms
Solar Panel Backsheets, Heat Exchanger Casings
Contact us now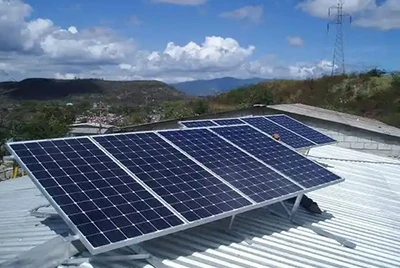
As is well known, Aluminium Corrugated Core Panel(ACCP) and Honeycomb Core Panel are both lightweight, high-strength materials commonly used in construction, transportation, and aerospace. What similarities do they share, and what are the significant differences?
Click here to view the Aluminium Corrugated Core Panel(ACCP) vs. Honeycomb Core Panel.
Foam Sandwich Panel Aluminum Foam Sandwich Panel(AFS)
Aluminum Foam Sandwich Panel(AFS) is a composite material composed of two layers of aluminum alloy sheets and an intermediate foam aluminum core. Its unique sandwich structure endows it with excellent properties such as lightweight, high strength, thermal insulation, and sound absorption.
Contact us now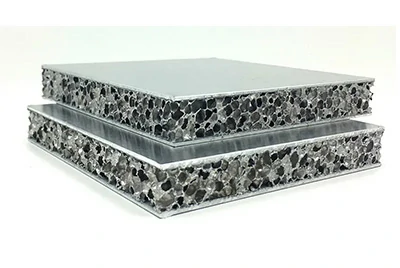
Specifications Of Aluminum Foam Sandwich Panel(AFS)
Panel Alloy | 5052, 5005, 6061, 6082, 7075 |
Foam Aluminum Alloy | 3003, 3105, 5052, 5056 |
Bonding Method | Brazing, Adhesive |
Panel Thickness | 0.125”, 0.25”, 0.375”, 0.5”, 0.625”, 0.75”, 1” |
Foam Aluminum Thickness | 0.045”, 0.17”, 0.245”, 0.42”, 0.55”, 0.67”, 0.92” |
Total Thickness | 10mm, 15mm, 20mm, 25mm |
Standard Sizes | 1200x2400mm, 1220x2440mm, 1250x2500mm, 1500x3000mm 2000x6000mm |
Panel Surface Types | Fluorocarbon (PVDF), Polyester (PE), Mirror, Brushed, Anodized, Matte, etc. |
Standards | ASTM B209, ASTM E8 |
Why Choose Aluminum Foam Sandwich Panel(AFS)?
- Lightweight And High Strength: Density is only 1/5-1/10 that of steel per unit volume, yet its compressive strength is 10 times that of polyurethane foam, and its rigidity far exceeds that of traditional metals.
- Energy Absorption And Shock Reduction: The porous structure can absorb impact energy (such as collisions, explosions), with dynamic compression energy absorption efficiency 5-10 times higher than that of solid materials.
- Structural Stability: The sandwich structure of the foam aluminum sandwich panel provides excellent bending rigidity and stability.
- Thermal Insulation And Sound Absorption: The closed-cell foam structure offers good thermal insulation and sound absorption, making it suitable for environments requiring heat insulation and noise reduction.
- Fire Resistance: Thanks to the high melting point of aluminum alloy, the foam aluminum sandwich panel exhibits excellent fire resistance, making it suitable for locations with high fire safety requirements.
- Eco-Friendly And Recyclable: Aluminum is 100% recyclable, and the production process is pollution-free, meeting the demands of a circular economy.
Chalco Offers Various Types Of Aluminum Foam Sandwich Panel(AFS)
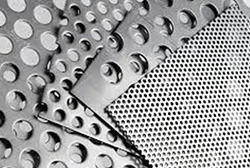
Perforated Foam Aluminum Sandwich Panel
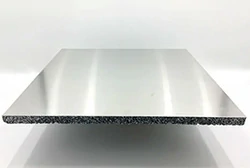
Brazed Foam Aluminum Sandwich Panel
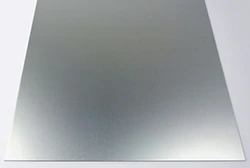
Anodized Foam Aluminum Sandwich Panel
Application Fields Of Aluminum Foam Sandwich Panel(AFS)
- Aerospace: Used in aircraft fuselages, rocket thermal insulation layers, etc., providing lightweight and thermal insulation solutions.
- Defense And Military Industry: Employed for impact-resistant structures in military vehicles, bulletproof armor, and explosive protective layers.
- Nuclear Power: Applied in containers for radioactive materials, controlled nuclear fusion test devices, and nuclear fuel protective equipment.
- Marine: Serves as cabin sound insulation panels and explosion-proof decks, enhancing the vessel's sound insulation and protective performance.
- Automotive: Utilized in vehicle body structures, bumpers, collision energy absorption zones, and battery protection casings to improve safety and reduce weight.
- Construction: Applied in building facades, interior decoration, ceilings, and decorative composite panels.
- All-Aluminum Furniture: Used for cabinets, bathroom vanities, wine cabinets, and decorative panels.


Aluminium Beaded Core Panels
Aluminium Beaded Core Panels (ABCP) are ultra-thin sandwich-structured panels composed of aluminium outer panels and a core filled with beaded or granular aluminium material, bonded using adhesive or brazing techniques.
Contact us now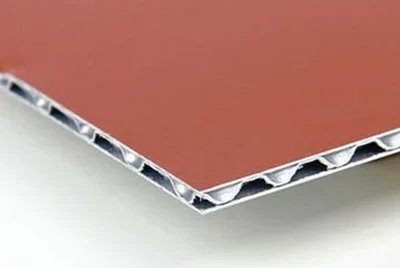
Structure of Aluminium Beaded Core Panels
- Surface Layer: Pre-coated PVDF fluorocarbon aluminium sheets (Common alloy AA3003, thickness 0.5–0.7mm), providing weather resistance and decorative effects.
- Core Material: Beaded aluminium particles or spherical core, compressed into a lightweight high-strength support structure through a special process.
- Bonding Method: Thermosetting resin adhesive or brazing, ensuring a strong bond between the core and panel.
Why Choose Aluminium Beaded Core Panels?
- Fire Safety: Compared to traditional ACP panels, the full aluminium core achieves A-grade non-combustibility, ensuring maximum fire resistance.
- Structural Strength: The unique beaded core design enhances mechanical strength, ensuring stability and durability.
- Ultra-Thin Structure: Scientifically compressed to a minimum thickness of just 4mm, making it the thinnest sandwich composite panel compared to aluminium honeycomb panels.
- Versatility: Supports stone texture, wood grain, mirror finish, and other surface treatments, meeting diverse design needs.
- Eco-Friendly & Recyclable: Made of 100% recyclable aluminium, with a pollution-free production process, meeting green building standards.
Applications of Aluminium Beaded Core Panels
Building Facades & Interior Walls: Used for high-rise building exteriors and interior walls, providing aesthetic appeal and functional benefits.
Roofs & Ceilings: Suitable for roof panels, suspended ceilings, and walkway roofs, offering fire resistance and thermal insulation.
Billboards & Signage: Used in advertising boards and signage, ensuring excellent visual impact and durability.
Transportation Infrastructure: Applied in high-speed rail & marine interiors, and highway barriers, providing enhanced safety.
Are You Looking for an Aluminum Supplier?
If you need a professional aluminum supplier to provide you with high-quality, cost-effective aluminum, we will be your best choice.
Available Panel Types for Aluminium Sandwich Panels
Choosing the right panel type is crucial for performance and aesthetics. The surface finish, machining options, and color selection directly impact durability, functionality, and visual appeal.
Surface Finish & Texture
Surface finishes not only enhance appearance but also improve corrosion resistance and weather durability. Common surface treatments include:
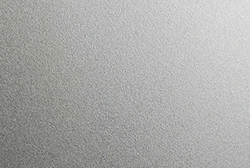
Polished
Smooth, high-gloss surface, ideal for premium decoration.
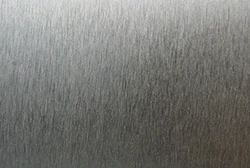
Brushed
Features fine linear textures, providing aesthetic appeal and scratch resistance.
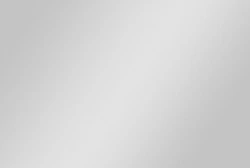
Mirror
Highly reflective, mirror-like surface achieved through fine polishing.
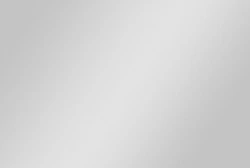
Anodized
Forms a hard oxide layer, enhancing corrosion resistance and abrasion durability.
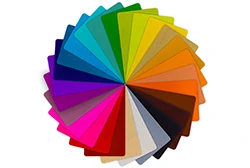
Coated (PVDF/PE)
Available in various colors, meeting diverse design requirements.
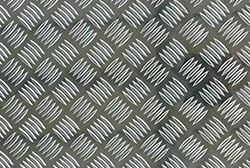
Embossed
Patterns created via roller pressing, improving anti-slip properties and decorative appeal.
Machining Options
The machining process determines the panel's customization and adaptability. Chalco provides the following processing services:
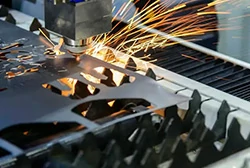
Cutting
Utilizes laser, plasma, or waterjet cutting for precise dimensions and shapes.
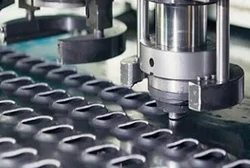
Perforation
Creates ventilation, drainage, or aesthetic perforations.
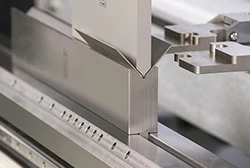
Bending
Achieved via mechanical or thermal methods, allowing custom angles and designs.
Available Color Options
The color and texture of the panel impact aesthetics and harmonization with surroundings. Common choices include:
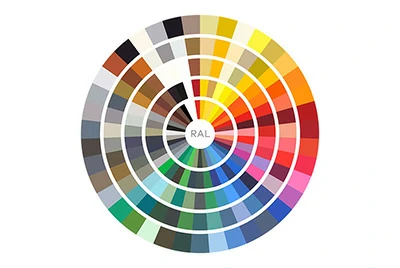
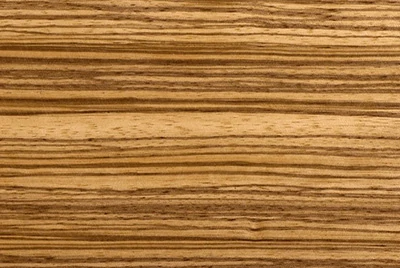
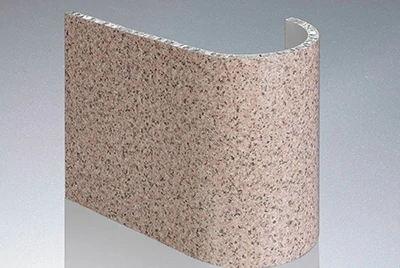
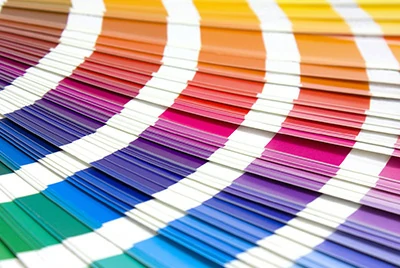
Why Choose Chalco Aluminum Sandwich Panels?
Choosing Chalco Aluminum Sandwich Panels means experiencing an extraordinary solution that exceeds expectations—powered by our unparalleled advantages:
1. Authoritative Certifications, Globally Trusted Quality
Chalco has been dedicated to the aluminum materials industry for many years, accumulating deep technical expertise and production experience. As a trusted aluminum expert, we rigorously control product quality. All our aluminum sandwich panels comply with international standards such as ASTM B209, AMSQQ-A-250, AMS-C-7438 and are certified by ISO 9001, ISO 14001, ensuring outstanding quality and stable performance.
2. Comprehensive Coverage, Unlimited Customization
We offer five series of aluminum sandwich panels to satisfy diverse application requirements.
Product Series | Core Advantages | Typical Applications |
ACP Aluminum Composite Panel | Cost-effective, rich in colors | Building facades, advertising signage |
Aluminum Honeycomb Panel | Lightweight, high strength, impact-resistant | Aerospace, rail transit |
Corrugated Core Panel | Superior sound insulation, long-span support | High-speed rail platforms, sound barriers |
Aluminum Foam Panel | Energy absorption, electromagnetic shielding | Automotive energy-absorbing box, bulletproof armor |
Bead Core Panel | Ultra-thin, fire-resistant, high cost-performance | Renovation of old buildings, marine interiors |
Advanced Customization: Supports customization of core density (±0.01g/cm³), panel thickness (0.2~6mm), and curved design (R≥50mm) with a 7-day rapid prototyping process.Quick Quote
3. Industry Benchmark, Defining Performance Standards
Lightweight Revolution: Achieves up to 70% weight reduction compared to solid aluminum panels, with a 50% strength increase (based on tested data), thereby lowering building loads and transportation costs.
Integrated Functionality:
- A2 Fire Resistance – 15-minute extreme fire endurance test with no molten drips (EN 13501-1 certified).
- 35dB+ Sound Insulation – Corrugated core panels effectively block highway noise to create a quiet environment.
- -40°C Cold Resistance – Arctic expedition-grade thermal insulation performance with a temperature tolerance span of 100°C.
Flexible Design: Offers over 100 standard colors and supports multiple surface treatments such as wood grain, stone grain, anodizing, brushed, mirror, PE, PVDF, etc.
4.Professional Service, Worry-Free Experience
We provide comprehensive professional services—from pre-sales consultation and design planning to customized production, installation guidance, and after-sales support. The Chalco expert team is with you every step of the way. Choosing Chalco means selecting not only high-quality aluminum sandwich panels but also a reliable, worry-free professional service experience.Quick Quote
5.Eco-Friendly, Sustainable Development
Chalco Aluminum Sandwich Panels are manufactured using 100% recyclable aluminum, reducing the production carbon footprint by 60% compared to traditional processes. The insulated core reduces building energy consumption by 30%, meeting green building and sustainable development standards and adding green value to your projects.
Corrugated Core Panel vs. Honeycomb Panel
Dimension | Aluminum Corrugated Core Panel (ACCP) | Aluminum Honeycomb Panel |
Core Structure | Corrugated aluminum core (water ripple/arc shape) | Hexagonal honeycomb aluminum core (bionic honeycomb structure) |
Material Composition | All-aluminum structure (panel + corrugated core) | All-aluminum structure (panel + honeycomb core) |
Weight (kg/m²) | 4.3~5.0 (6mm thick) | 5.5~7.0 (10mm thick) |
Compressive Strength (MPa) | 80~100 (core shear strength) | 1.0~1.5 (core shear strength, panel support dependent) |
Bending Stiffness | Superior (corrugated structure disperses stress) | Depends on honeycomb density; at high density, approximates corrugated |
Fire Resistance | A2 (non-combustible) | A2 (non-combustible) |
Sound Insulation | 35dB↑ (corrugated reflects sound waves) | 25~30dB (honeycomb primarily absorbs sound) |
Thermal Insulation | Air layer insulation (better when sealed in cold regions) | Honeycomb air chamber insulation, slightly inferior to corrugated |
Surface Flatness | Extremely high (ensured by cold bending process) | High (depends on honeycomb uniformity) |
Processing Difficulty | Easy to cut and bend, supports irregular curved surfaces | Requires specialized tools to cut honeycomb core; complex shapes increase cost |
Cost (per same area) | 30%~50% lower (simple core manufacturing process) | Higher (complex honeycomb core production process) |
Eco-Friendliness | 100% recyclable | 100% recyclable |
Typical Applications | Building facades, sound barriers, lightweight vehicles | Aerospace, high-end architecture, explosion-proof structures |
- Corrugated Core: Formed by cold bending into waves, creating continuous curved support with strong shear resistance—ideal for large-span structures (e.g., building exteriors).
- Honeycomb Core: Hexagonal cells disperse load evenly, providing superior isotropic strength and compressive energy absorption (e.g., aircraft cabin crash protection).
2. Lightweight & Cost-Effectiveness
- Corrugated Panels: Lighter (20%~30% lighter than honeycomb panels) and lower in cost, making them ideal for large-area applications with tight budgets (e.g., subway station ceilings).
- Honeycomb Panels: Offer a better balance of lightweight and high strength, but are more expensive and mainly used in high-end applications (e.g., satellite brackets).
3.Sound & Thermal Insulation
- Corrugated Panels: The corrugated structure reflects sound waves, delivering significantly improved sound insulation (e.g., concert hall soundproof walls).
- Honeycomb Panels: Primarily absorb sound, making them suitable for mid-to-low frequency noise environments (e.g., computer room noise reduction).
4.Processing & Design
- Corrugated Panels: Support complex curved surfaces (e.g., arched facades) and are easy to process, ideal for innovative architectural designs.
- Honeycomb Panels: Require high-precision processing equipment, but core density can be customized (e.g., high-density honeycomb for bulletproof armor).
In summary, both corrugated sandwich panels and honeycomb sandwich panels are essential materials in modern lightweight engineering. Selection should consider cost, performance requirements, and process adaptability. Corrugated panels tend to favor cost efficiency and acoustic optimization, while honeycomb panels focus on high-end strength and multifunctional integration.
Chalco can provide you the most comprehensive inventory of aluminum products and can also supply you customized products. Precise quotation will be provided within 24 hours.
Get a quote