Whether you need simple bars, tubes or more complex products, you can find what you are looking for at Chalco. We utilize cutting-edge craftsmanship and metal forging techniques to obtain parts that exceed your expectations.
Additionally, we have obtained ISO 9001 and NADCAP certification, ensuring excellence in special processes such as heat treatment and welding. Our products comply with standards including AMS (AMS 4127, AMS 4133, AMS 4143, AMS 4144), ASTM B247, MIL-A-22771, ISO 783, and EN 754.
Chalco Aluminum forging product type
Products in Chalco include forged bars, forged aluminum tubes, rolled forged rings, discs, hubs, blocks, shafts, and other forged shapes. We can also provide customized aluminum forging production services to meet your application needs.Quick Quote
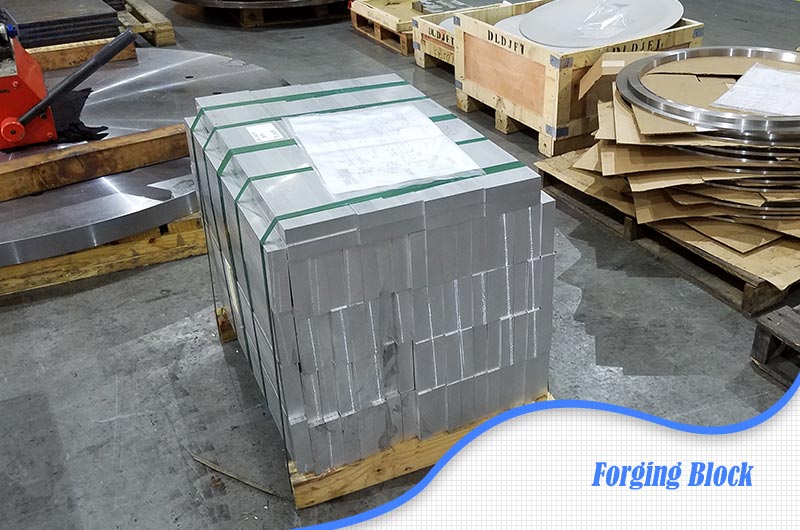
Forging block
High strength, high toughness and excellent machinability
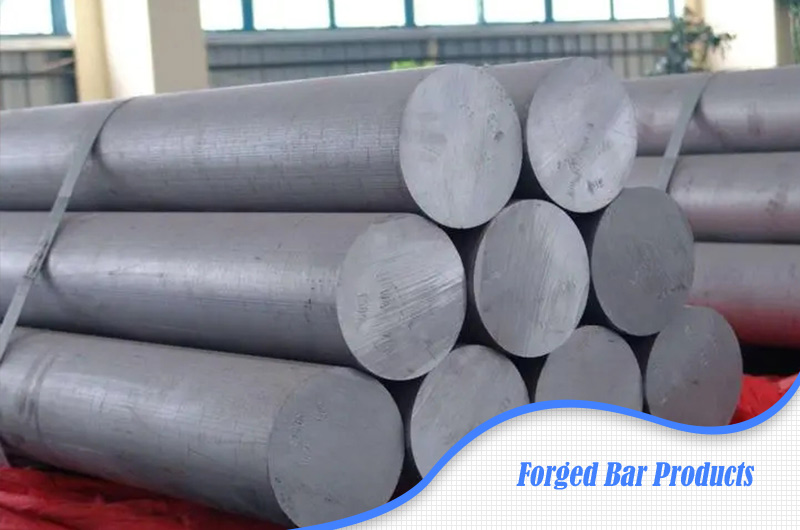
Forged aluminum bars
High strength, full size, high quality
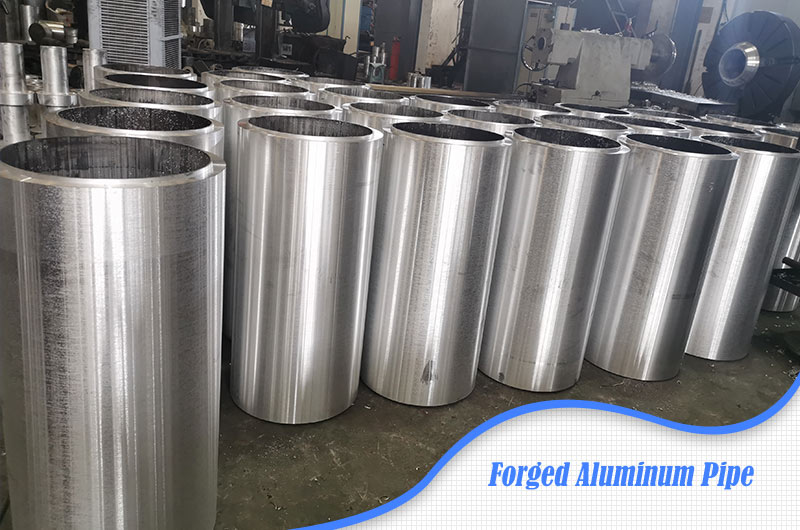
Forged aluminum tube
Outer diameter, inner diameter and wall thickness can be customized
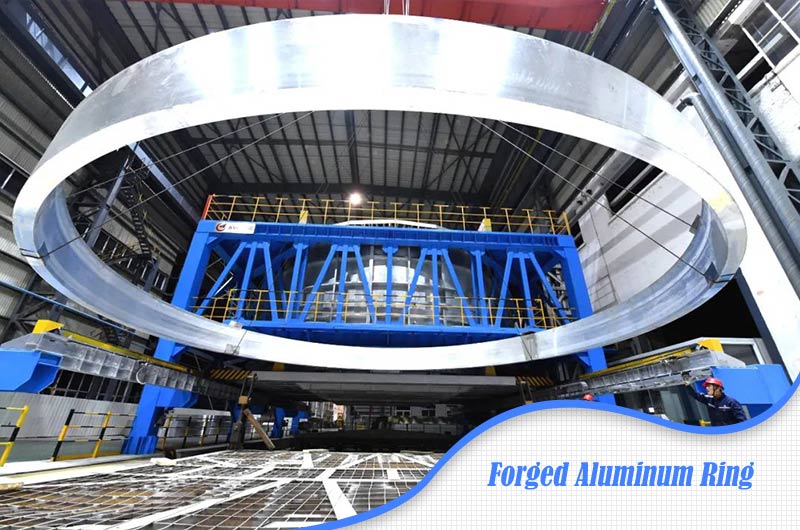
Forged aluminum ring
Large size, precise size, high strength
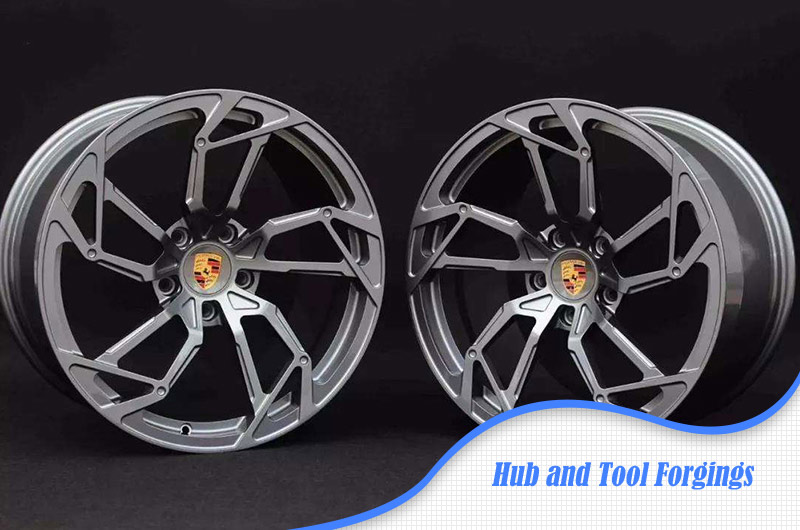
Hub and tool forgings
High safety, long-lasting durability, customizable appearance design
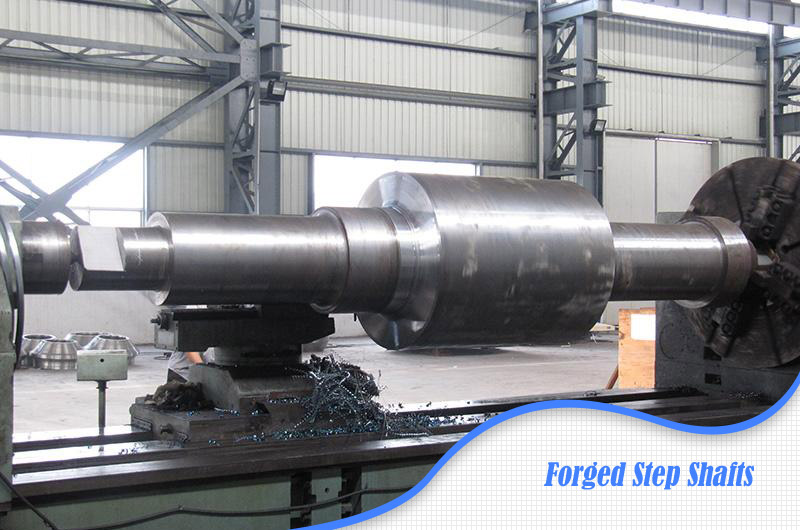
Forged crankshafts and rotor shafts
The sizes include round, square, rectangular, conical, etc.
What are the popular forging alloys?
6061 aluminum alloy: high weldability, formability, corrosion resistance.
6063 aluminum alloy: good surface finish, accurate forged tube dimensions.
6082 aluminum alloy: excellent strength, easy processing and forging, corrosion resistance.
7075 aluminum alloy: high tensile strength, excellent strength-to-weight ratio.
2024 aluminum alloy: good processability, strong corrosion resistance, good fatigue resistance.
7050 aluminum alloy: high strength, good toughness, corrosion resistance, resistance to strain corrosion cracking.
2618 aluminum alloy: High strength, high temperature resistance and good corrosion resistance.
7079 aluminum alloy: high yield strength, good mechanical properties.
Where are forgings used?
Chalco Aluminum Forging prides itself on producing high-quality aluminum forgings, particularly in the aerospace, defense, automotive and recreational motorsports sectors.
Aerospace Forging
Alloy:7075, 2024, 7050
application:Rocket adapters, combustion chambers, space bulkheads, commercial spacecraft flanges, missile casings, and fixed-wing aircraft landing gear components.
Contact us now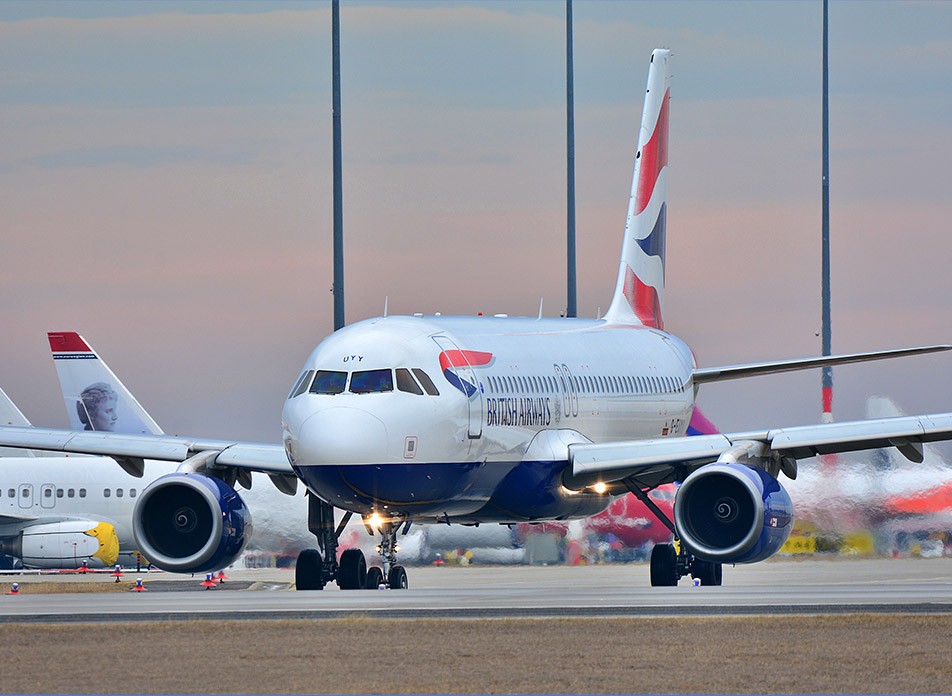
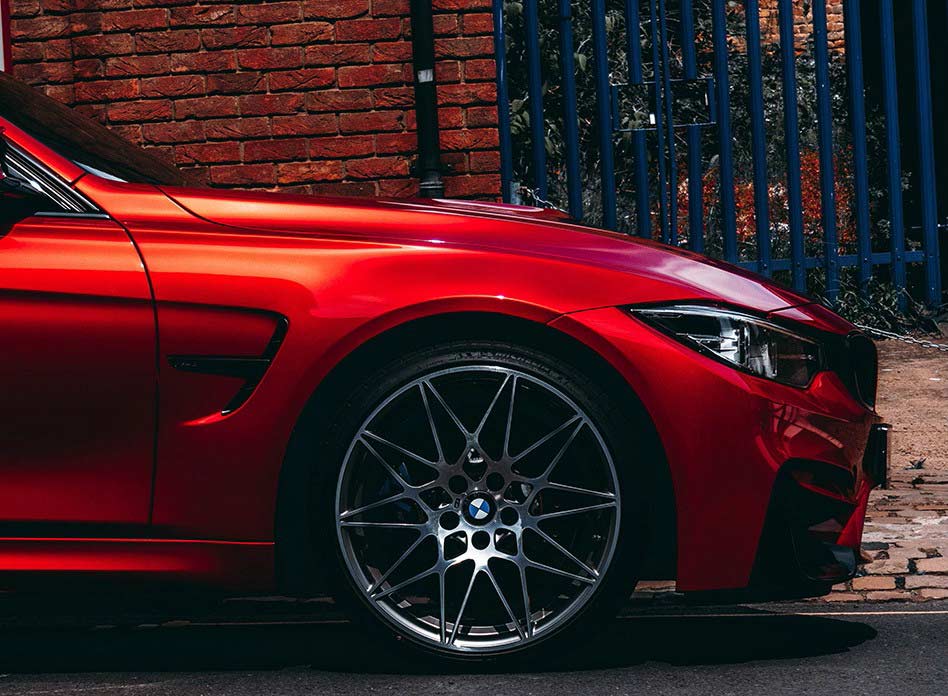
Automobile Forgings
Alloy:2618, 4032, 6061, 6082
application:Suspension, steering knuckle, transmission piston, connecting rod, wheel.
Contact us nowDefense Industry
Alloy:5083, 7075, 2024, 7039
application:Missile components, armored vehicles and weapon systems, launch tubes.
Contact us now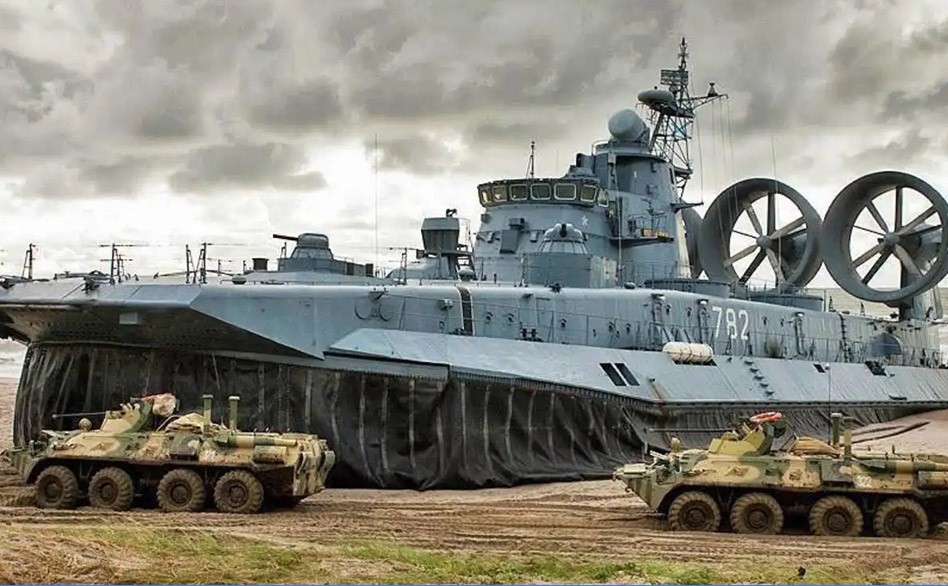
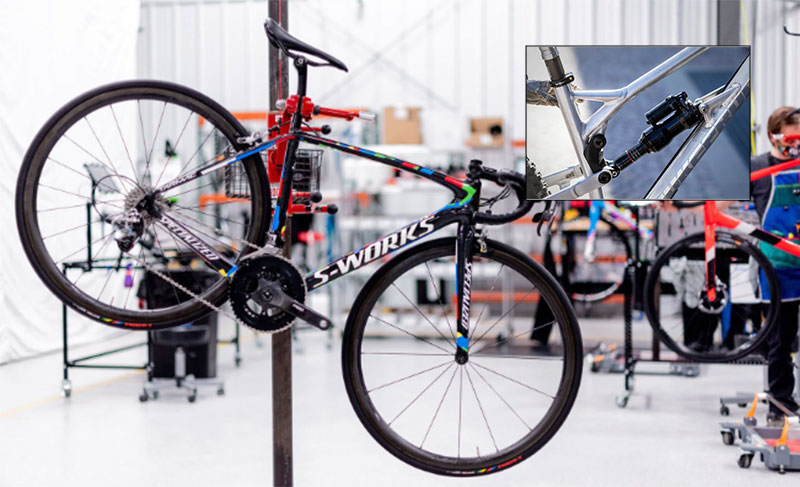
Daily Necessities
Alloy:6061, 6063, 2024, 7075
application:Semiconductors, sports equipment, bicycle frame components and high-quality frying pans.
Contact us nowClassification of common alloys for chalco aluminum forgings
1000 series aluminum forgings
Chalco has AS9100 certification produces 1xxx aerospace aluminum forgings according to BS 5 L34, BS 2 L87, EN 573-3, AMS 4120, ASTM B247, QQ-A-367, etc. standards. 1xxx aluminum alloy mainly includes forged bars, forged rings, wheel rims and other forged products, which are used in aircraft structural parts, engine parts, hydraulic systems and other parts.
-
1200-forging
1200 aluminum alloy mainly includes forged bars, forged rings, wheel rims and other forged products, which are used in aircraft structural parts, engine parts, hydraulic systems and other parts.
Thermal conductivity Good conductivity High temperature stability
2000 series aluminum forgings
2000 series aluminum alloys are used in many industries, including aerospace, national defense and power generation. The following are some typical 2 series alloy models for Chalco's aluminum forgings.
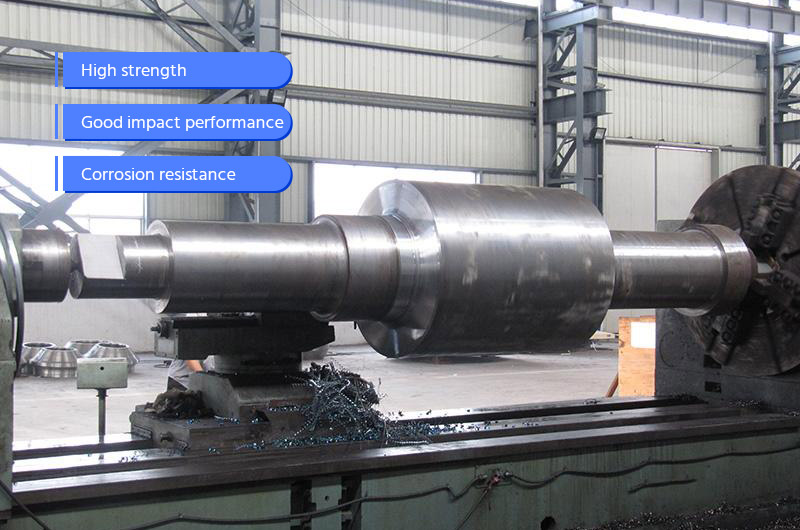
2A50-forging
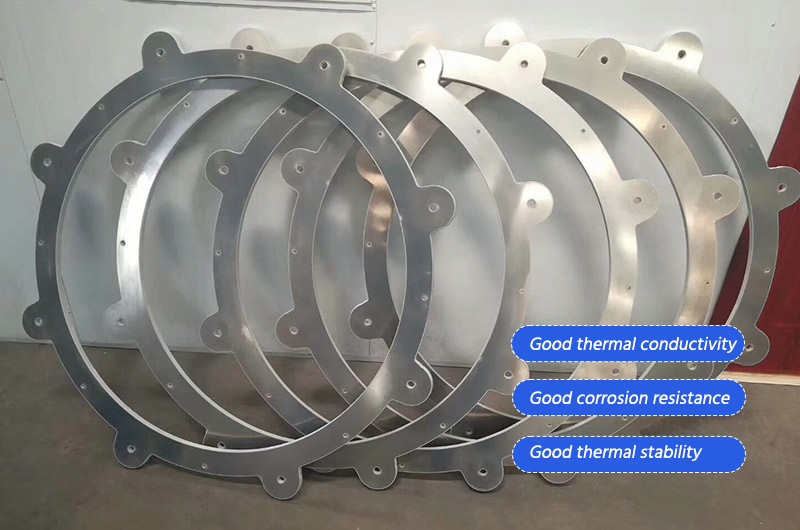
2A70-forging
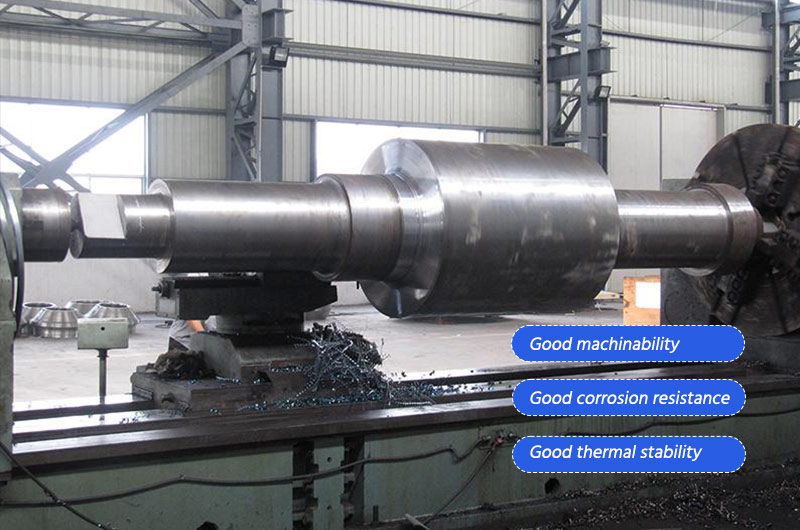
2B50-forging
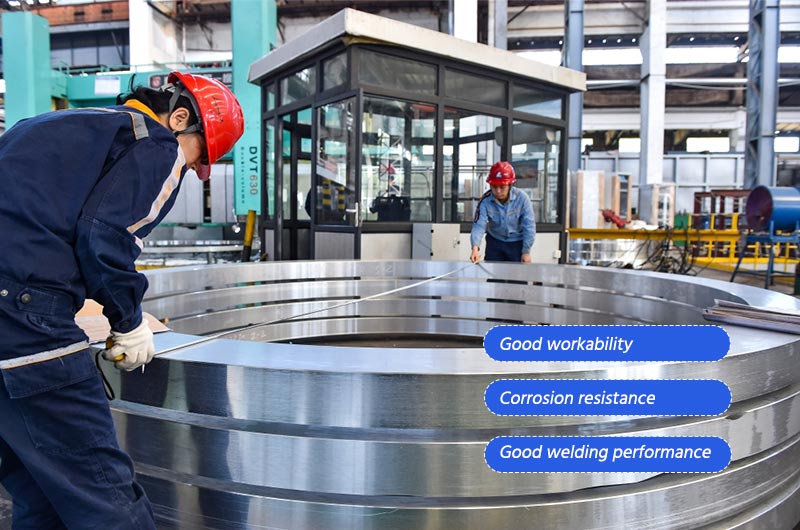
2618-forging
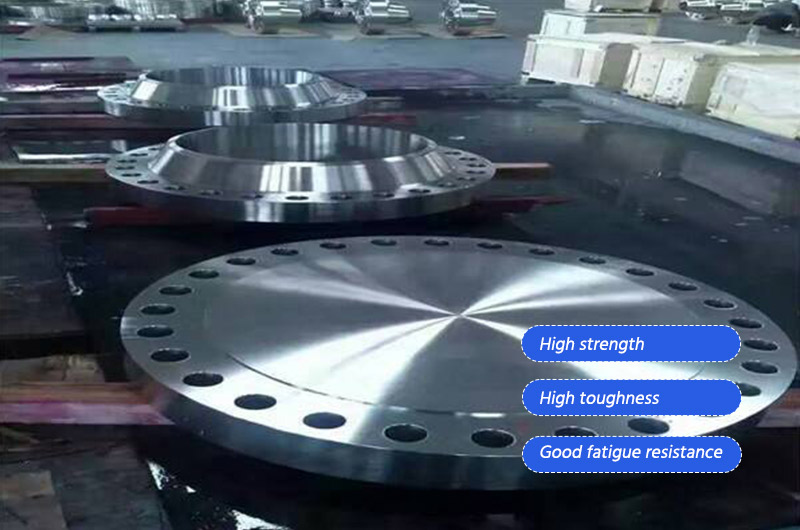
2025-forging
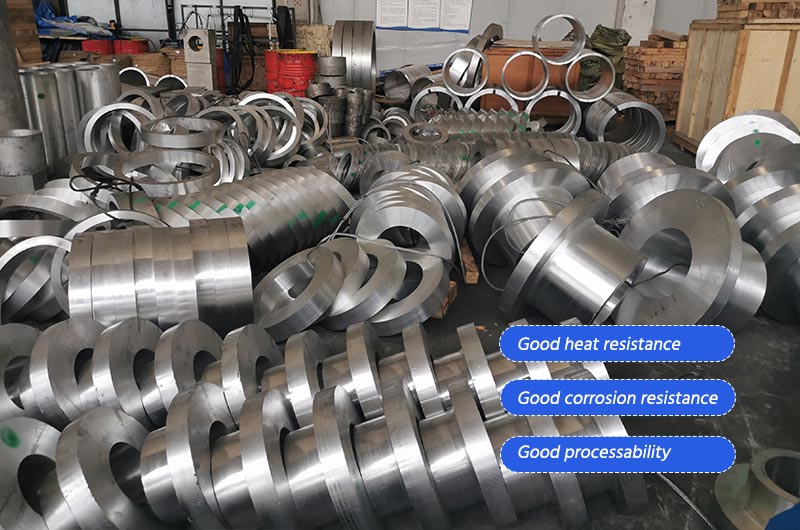
2018-forging
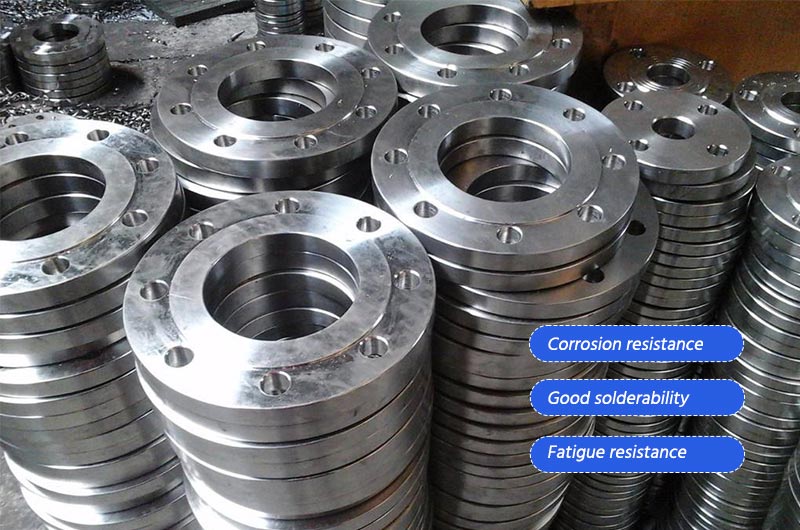
2219-forging
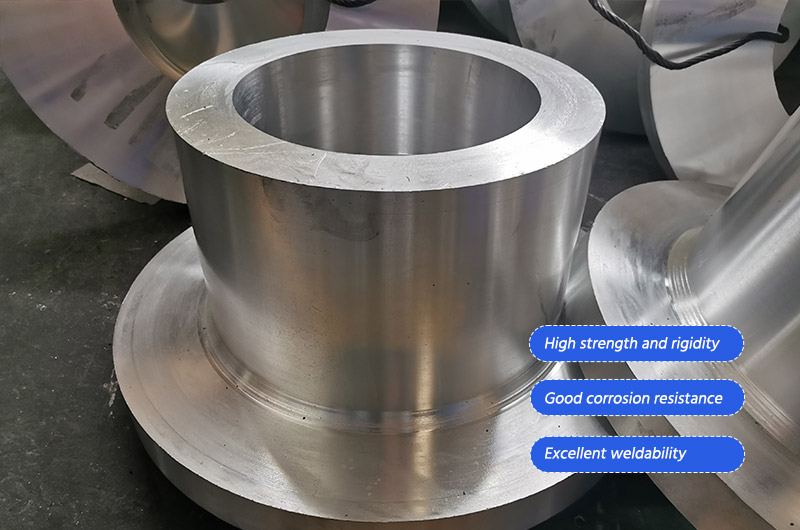
2014-forging
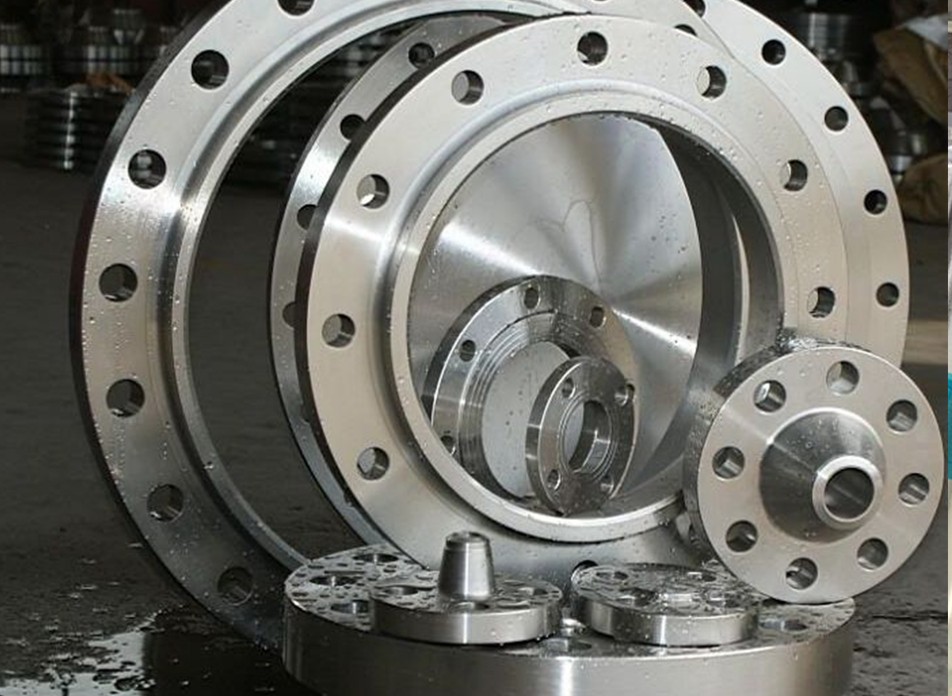
Forging Performance
4000 series aluminum forgings
4000 series aluminum alloy forgings are mainly used to manufacture materials for pistons and cylinders of steam engines, as well as complex forgings that work below 200 ℃ and bear heavy loads.Quick Quote
-
4032-forging
4032 aluminum forgings produced according to AMS 4145, QQ-A-367 4032 standards are usually used to manufacture forged pistons, forged compressor parts, wear-resistant parts, etc.
High strength Good wear resistance Good heat resistance
5000 series aluminum forgings
5000 series aluminum alloys are used in many industries, including various national defense departments. The following are some typical 5 series alloy models for Chalco's aluminum forgings.
6000 series aluminum forgings
6000 series aluminum alloys are used in many industries, including oil and gas, petrochemical and marine sectors. The following are some typical 6 series alloy models for Chalco's aluminum forgings.
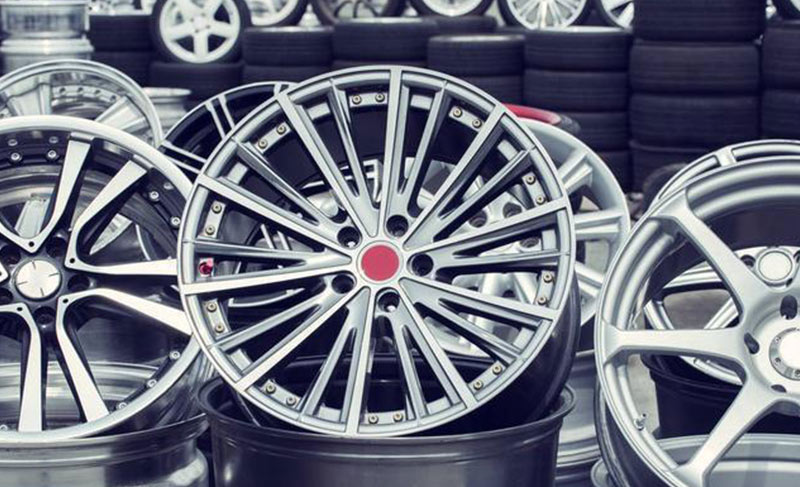
6061 6082 Wheel Hub Forging
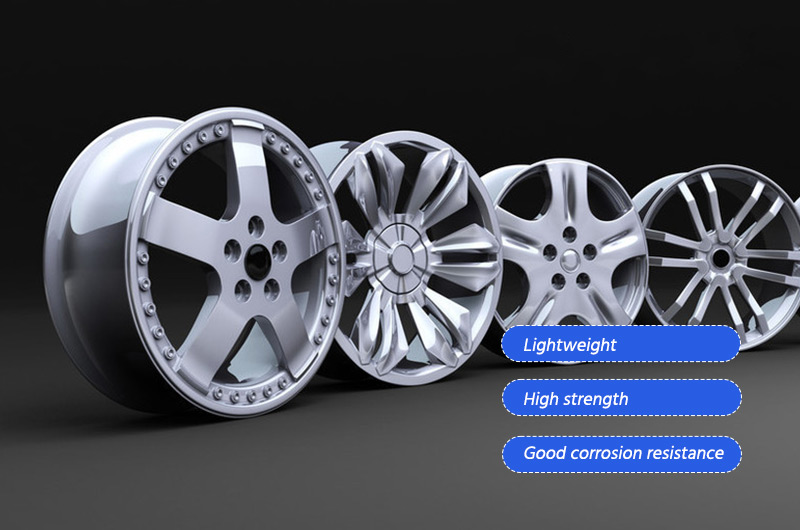
6a10-auto-forging
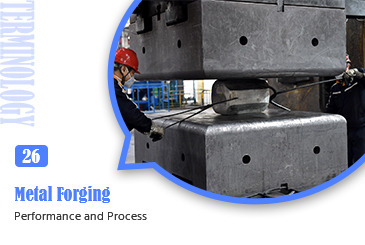
6082-auto-forging
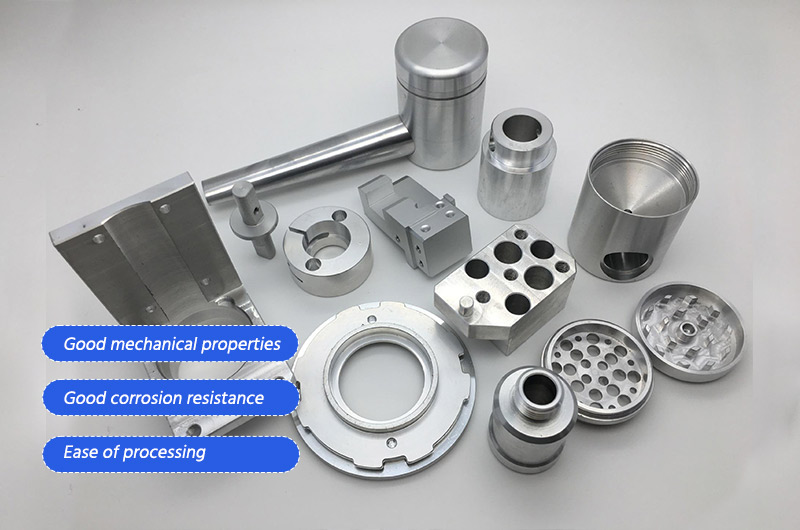
6061-auto-forging
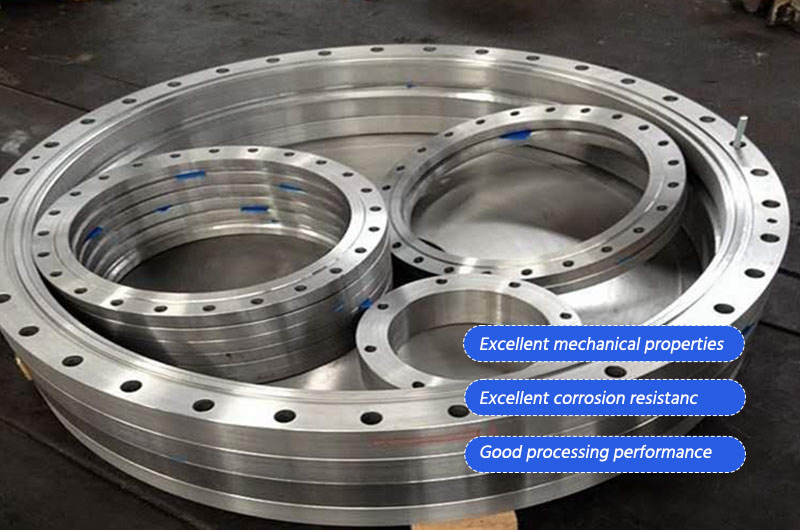
6a02-forging
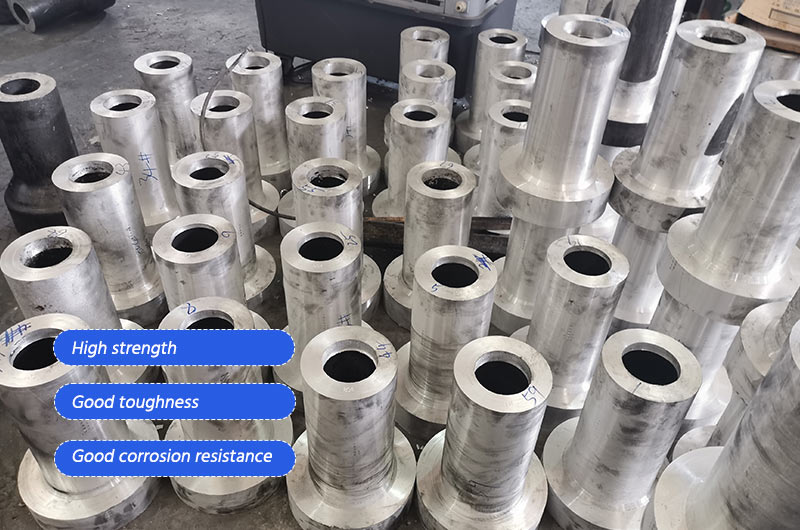
6082-forging
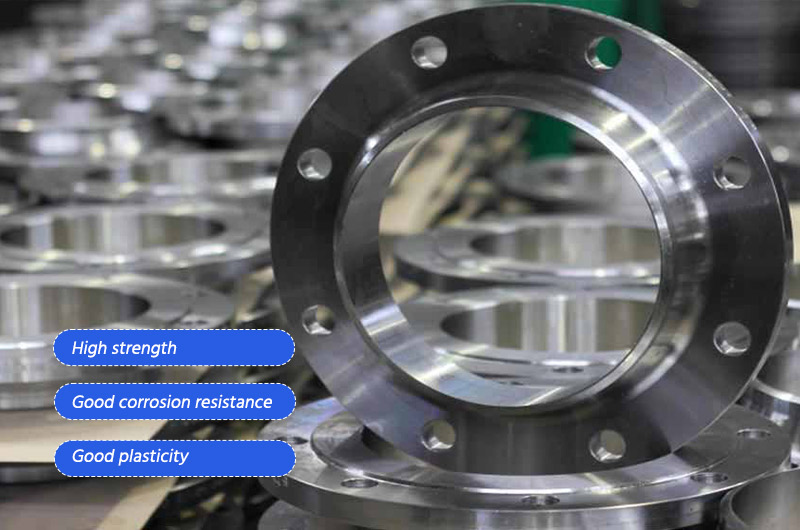
6061-forging
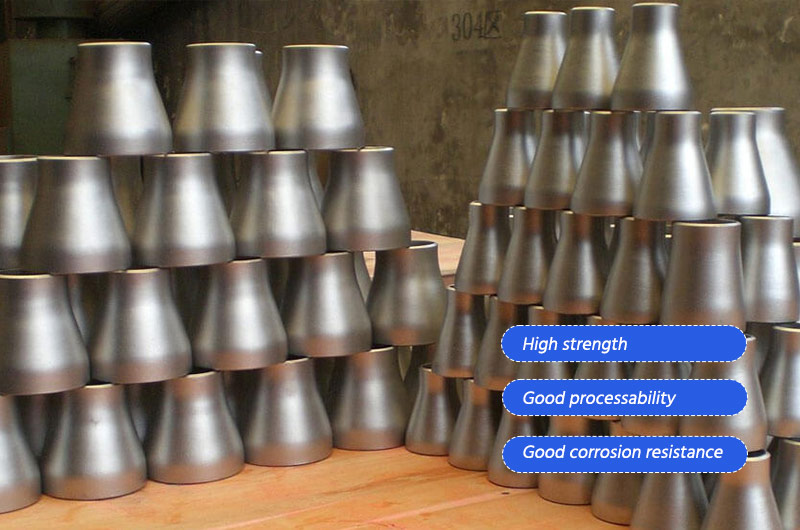
6151-forging
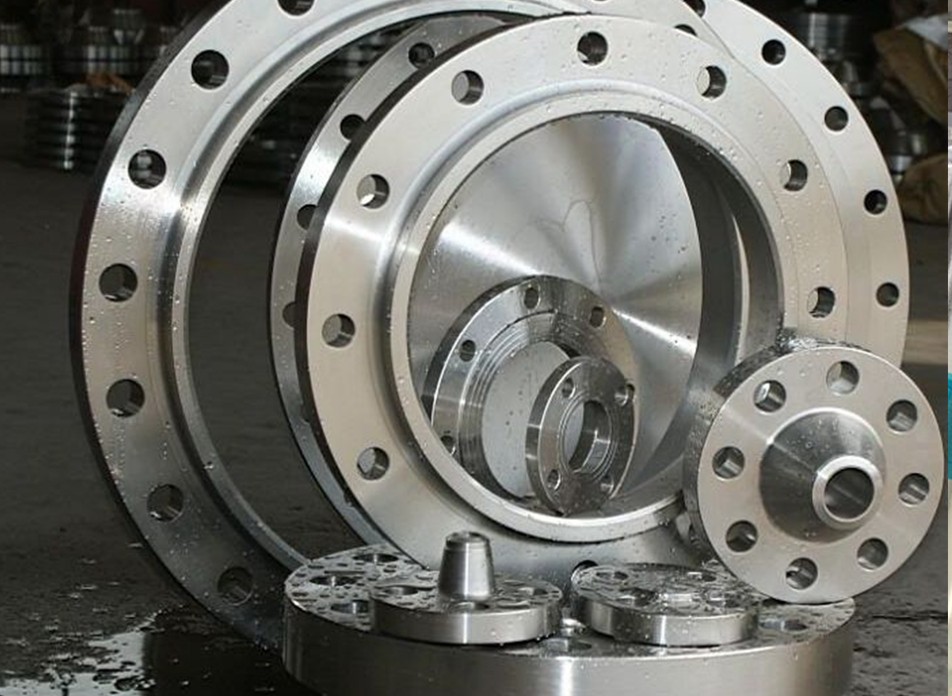
Forging Performance
7000 series aluminum forgings
7000 series aluminum alloys are used in many industries, including aerospace, national defense and racing. The following are some typical 7 series alloy models for Chalco's aluminum forgings.Quick Quote
What are the production processes of Aluminum forgings?
Aluminum forging offers a range of expertise types that can be adjusted to produce custom products based on your unique requirements. The overall classification of aluminum forging expertise can be divided into five main categories:
- Cold Forging: Aluminum cold forging shapes the material at room temperature and gives it improved strength and precision.
- Hot Forging: This methodology of hot forging aluminum is highly specialized since it demands increased temperatures to fasten the fluidity process to create complex structural designs.
- Drop Forging:Drop aluminum forging utilizes the force of gravity or mechanisms to create exact parts of increased strength and complexity.
- Rolled Ring Forging: Aluminum-molding rolled rings create the rings from one piece of stock by rolling and forming it. This option allows for transmitting more precise directions and p-stage processing.
- Open Die Forging: Aluminum open dies form any geometric shape of aluminum material in the forge. The process uses two flat dies, and heel-to-toe dies are the most common.
- Closed Die Forging: Aluminum closed dies shape the material and their connection in a more precise fashion using preset producers. It allows for the creation of any form on aluminum materials.
Understanding the Differences Between Forging and Casting
In forging, deformation of the material in solid form, often by hammering or pressing the material, creates the desired shape.In casting, metal is melted and poured or forced into a mold made in the shape of the desired item.
- Production flexibility: The open die forging process accommodates a wide range of production batches and enables short delivery times.
- Strength: Whether it is open die forging or closed die forging, the forging process is superior to casting in predictable strength characteristics, ensuring high strength of the parts.
- Prevention of defects: The grain flow direction produced by forging pre-processing is consistent with the direction of maximum strength, which improves defects such as dendritic structure and alloy segregation.
- Production reliability: The forging process is easier to control, ensuring product consistency and reliability.