6061 aluminum - excellent forging alloy
6061 aluminum alloy is widely used in aerospace, automotive, shipbuilding, energy and other fields in forging manufacturing due to its high strength, corrosion resistance and excellent processing performance. Its excellent heat treatment ability and lightweight characteristics make it an ideal choice for high-load structures.
Compared with other aluminum alloys, 6061 has both strength and corrosion resistance, supports T6/T651 heat treatment, is easier to weld than 2xxx and 7xxx series, and has better processability than 5xxx series. Compared with other forged alloys, 6061 has uniform structure, stable mechanical properties, is more corrosion-resistant than 2xxx series, more suitable for humid environments than 7xxx series, and suitable for a variety of manufacturing processes.
- High strength & lightweight: close to the strength of some steel materials, lighter weight, and improved load-bearing capacity.
- Excellent corrosion resistance: long-term weather resistance, suitable for marine, aviation and other environments.
- Superior processability: Supports CNC & welding, easier to process than 2xxx and 7xxx.
- Excellent heat treatment capability: T6/T651 improves hardness and fatigue resistance, extending service life.
- Environmentally friendly and recyclable: low-carbon manufacturing, suitable for new energy & green transportation.
Chalco relies on advanced forging technology and strict quality control system to provide 6061 aluminum alloy forgings in various shapes and specifications to meet the needs of different industries. Whether it is standard basic forgings, structural forgings, flange connectors, or high-precision custom forgings, Chalco can provide high-quality products to help customers achieve high-performance application goals.
Chalco 6061 aluminum standard basic forgings
In industries such as machinery manufacturing, aerospace, rail transportation, shipbuilding, and energy equipment, the materials of structural parts, supporting parts, and load-bearing parts must have high strength, good fatigue resistance, and excellent machinability. 6061 aluminum alloy has become an ideal material for basic forging applications due to its excellent mechanical properties and corrosion resistance.
Chalco uses advanced free forging, rotary forging, die forging and rolling processes to provide high-quality 6061 aluminum alloy basic forgings that can meet standard machining and high-precision customization needs. The following are the main product categories we provide:
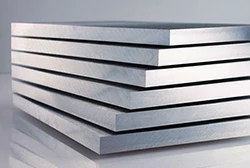
6061 aluminum forging plate
It adopts free forging process, has high strength and impact resistance, and is suitable for aerospace, shipbuilding and high-strength structural parts.
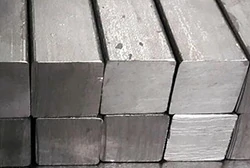
6061 aluminum forged block
Manufactured through free forging process, it has uniform structure and is suitable for precision CNC machining; widely used in mold manufacturing and high-precision mechanical parts.
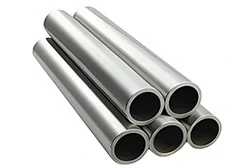
6061 al forged tube pipe
It adopts seamless forging technology, has high pressure resistance and corrosion resistance, and is widely used in aerospace, high-pressure pipelines and military fields.
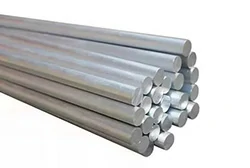
6061 aluminum forged bar rod
It adopts free forging & rolling process, has excellent fatigue resistance and machinability, and is suitable for high-load applications such as mechanical transmission shafts and load-bearing components.
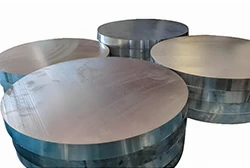
6061 aluminum forged disc
It adopts open forging & rotary forging process, has uniform mechanical properties and excellent wear resistance, and is suitable for flywheels, pressure vessel end covers and rotating parts.
Chalco 6061 aluminum structural forgings
Chalco 6061 aluminum alloy structural forgings are designed for high-load structures and precision mechanical parts, with excellent fatigue resistance and mechanical strength. Using advanced free forging, rotary forging and die forging processes to ensure high-precision and high-durability products, they are widely used in aerospace, shipbuilding, wind power generation, automotive transmission and other fields.
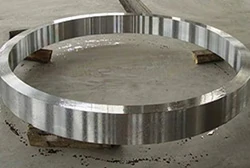
6061 large diameter forged ring
Diameter can reach 10 m, meeting the strict requirements of high-end fields such as aerospace, wind power, shipbuilding, and military industry.
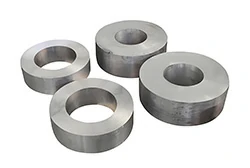
6061 aluminum forging ring
Rolling forging & rotary forging process is adopted, with uniform structure and no welds, which improves fatigue resistance and is used for structural parts.
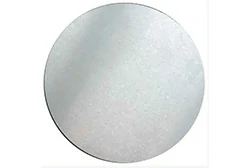
6061 aluminum forged circle
Free forging & die forging, high strength, wear resistance, suitable for aircraft wheels, automobile clutch discs, high-speed rotating parts.
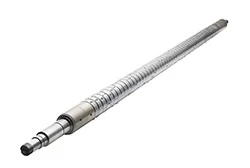
6061 aluminum forged shaft
Free forging & rotary forging processes have high torque load and fatigue resistance, and are used in aviation propulsion systems, ship propulsion shafts, motor spindles, etc.
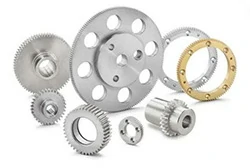
6061 aluminum forged gear
Die forging & free forging processing, high hardness, wear resistance, widely used in automobile gearboxes, engineering machinery transmission systems, industrial equipment.
Chalco 6061 aluminum flanges & connection forgings
In industries such as high-pressure fluid transportation, aerospace, and shipbuilding, the sealing, strength, and corrosion resistance of connection parts are crucial. 6061 aluminum alloy is an ideal material for manufacturing high-performance flanges and connection forgings due to its excellent mechanical properties, corrosion resistance, and lightweight properties.
Chalco provides various specifications of 6061 aluminum alloy flanges and pipe connectors, using closed die forging technology to ensure high strength, high precision and stable performance to meet the needs of harsh industrial environments.
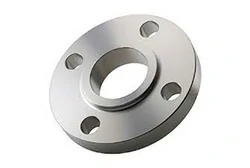
6061 aluminum forged flange
Closed die forging, high pressure resistance, corrosion resistance, widely used in aerospace, petrochemical and other fields.
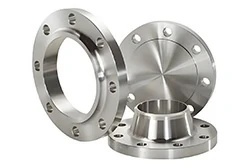
6061 al high pressure flange
Closed die forging can adapt to extreme environments and is often used in high-demand industries such as nuclear power and chemical industry.

6061 aluminum forging joint
Closed die forging, high strength, fatigue resistance, suitable for oil pipelines, marine engineering and other structures.
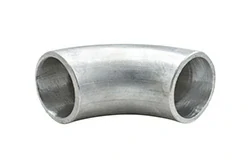
6061 aluminum forged elbow
Closed die forging, with high pressure resistance and corrosion resistance, used in ocean, oil and gas transportation, and high-pressure hydraulic pipelines.
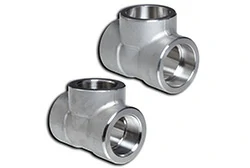
6061 aluminum forged tee
Closed die forging, uniform structure, strong pressure resistance, suitable for oil, natural gas and industrial pipelines.
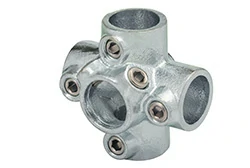
6061 aluminum forged cross
Closed die forging, high strength, suitable for complex pipeline connections, widely used in aerospace, chemical industry and engineering equipment.
Chalco 6061 high-precision forgings
In the aerospace, military, racing and other industries, materials not only need to have extremely high strength and fatigue resistance, but also need to meet stringent requirements such as lightweight, precision machining and resistance to extreme environments. 6061 aluminum alloy is an ideal material for high-end precision forgings due to its excellent mechanical properties, machinability and corrosion resistance.
Chalco uses advanced rotary forging, precision forging and free forging processes to provide high-strength, high-precision 6061 aluminum alloy forgings for the high-end manufacturing field to meet customers' needs for extreme performance.
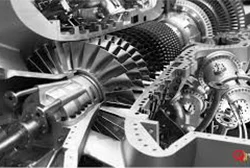
6061 Aerospace forgings
Chalco Aluminum could produce 2024 T351 T851 aircraft aluminum sheet……
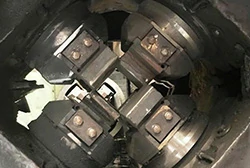
6061 Military grade forgings
Rotary forging & free forging, impact and corrosion resistance, suitable for armor protection and military vehicles.
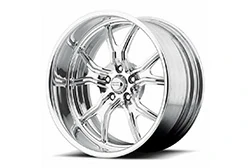
Racing forgings
Rotary forging & free forging, ultra-high strength, widely used in racing car suspension and brake systems.
Chalco 6061 aluminum forging production - open forging, die forging, rotary forging, precision forging
Chalco has an advanced forging production system, covering open forging, die forging, rotary forging, precision forging and other processes to meet the strict requirements of 6061 aluminum alloy forgings in different fields. We have leading production advantages in the industry with high-precision equipment, automated production and strict quality control.
Open die forging
Suitable for large size and high strength forgings, such as forging blocks, forging bars, forging circles and forging tubes.
- Extra large forging capacity: the maximum single piece weight can reach 5 tons and the size can reach 5 meters.
- Uniform internal structure: high temperature homogenization treatment is adopted to ensure consistent mechanical properties.
- High-precision machining: Equipped with CNC pre-machining & heat treatment technology to improve machining efficiency.
Closed die forging
Suitable for high-precision, complex-shaped forgings, such as flanges, gears, and aviation parts.
- High-precision molds: Self-developed high-wear-resistant mold steel ensures dimensional consistency and mold life.
- Batch production capacity: 1000 tons - 4000 tons die forging equipment, supporting large-scale and efficient production.
- Microstructure optimization: using isothermal forging & rapid cooling technology to improve mechanical properties.
Precision forging
Suitable for high-end customized forgings in aerospace, military industry, racing, etc.
- Extreme tolerance control: dimensional tolerance can reach ±0.02mm to ensure precise fit.
- Lightweight design: Adopt near-net-shape technology to reduce subsequent machining losses.
- Aerospace-grade quality control: Strictly implement AMS, ASTM, and ISO standards to meet demanding application requirements.
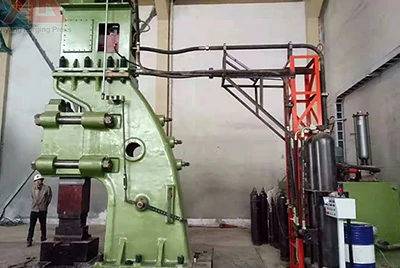
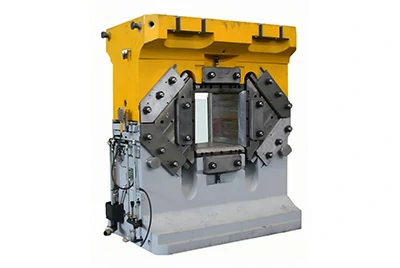
Radial forging & ring rolling
Suitable for high-strength and high fatigue-resistant parts such as forged rings, forged disks and forged shafts.
- Extra-large diameter forging ring: up to 10 meters in diameter, suitable for aviation, wind power, and rocket components.
- No-weld structure: avoids welding stress concentration and improves fatigue resistance and corrosion resistance.
- Intelligent CNC rotary forging: automatically adjusts pressure and speed to improve material uniformity.
Processing capabilities of Chalco 6061 aluminum forgings
Chalco has a complete 6061 aluminum alloy forging processing system, covering forging, heat treatment optimization, precision machining and surface treatment, ensuring that the product has excellent strength, corrosion resistance and dimensional accuracy.
Heat treatment - the key to strengthening the performance of 6061 forgings
The mechanical properties of 6061 aluminum alloy forgings can be optimized through heat treatment. Chalco uses high-precision heat treatment furnaces to achieve uniform temperature control & rapid cooling technology to ensure that forgings achieve optimal mechanical properties while reducing residual stress and improving dimensional stability. Chalco provides a variety of heat treatment states to meet different working conditions:
- 6061 T6/T651 strengthening treatment: After solution treatment & artificial aging, it achieves the highest strength and hardness, suitable for high-load structural parts such as aviation, automobiles, and mechanical equipment.
- 6061 T4 softening treatment: Only solution treatment is performed, which has better ductility and is suitable for subsequent bending, welding and cold working applications, such as aviation structural parts and complex shape parts.
- 6061 T42 reheat treatment: After T4 softening treatment, it is naturally aged to a stable state. It is suitable for structural parts that require subsequent forming and strengthening, such as rail transit components and ship parts.
- 6061 T62 medium strength treatment: The performance is between T6 and T4, taking into account certain strength and ductility, suitable for mechanical parts subject to dynamic loads.
Machining (CNC machining & turning, milling, grinding and drilling) - achieving high precision and complex shapes
- CNC precision machining: Adopt five-axis CNC machine tools to ensure high-precision processing of complex shapes with a tolerance of up to ±0.02mm.
- Turning & Milling: Suitable for parts such as shafts, flanges, forging plates, etc. , to ensure dimensional consistency and reduce subsequent assembly errors.
- Drilling & Tapping : Applicable to structural parts that require threaded connections, such as forged flanges and pipe fittings, to ensure a tight fit.
Surface treatment—— improve durability & aesthetics
- Anodizing - Improves corrosion resistance, suitable for marine engineering & aviation parts.
- Powder Coating & Electrophoresis - Enhances aesthetics and protection, widely used in rail transportation & mechanical equipment.
- Mechanical polishing & fine grinding - Provides glossy & matte finishes, suitable for decorative forgings & high-end industrial parts.
Precision assembly & welding——providing one-stop processing services
- Welding process (TIG/MIG) : Suitable for forged pipes and structural parts that need to be assembled by welding to ensure high-strength connections.
- Riveting & Pre-assembly : We can provide flange & connection forging assembly, saving customers' processing time and improving production efficiency.
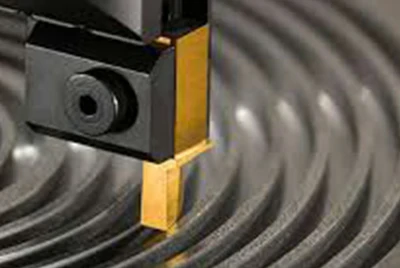
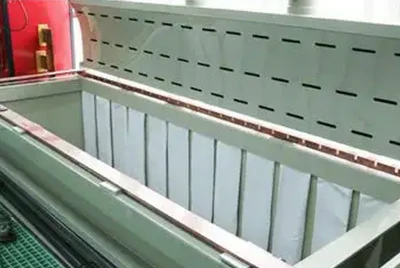
Chalco 6061 aluminum alloy forgings application areas
Chalco 6061 forgings are widely used in many demanding industries. With stable product quality, strong production capacity and international certification, we provide reliable aluminum alloy solutions to customers around the world.
Aerospace
6061 aluminum forgings are widely used in aerospace structures to reduce overall weight and improve fuel efficiency due to their high strength-to-weight ratio, fatigue resistance, and good weldability.
- Aircraft Frames – 6061 forgings are used to manufacture fuselage frames, providing strength support and reducing weight.
- Fuselage stiffeners – used to strengthen the fuselage structure and improve shock and vibration resistance.
- Satellite Structural Support – For spacecraft brackets, ensuring structural stability and withstanding extreme temperature changes.
Partners: Boeing, Airbus, Klin Aerospace
Automobile & Rail Transit
With the advancement of the trend of lightweight automobiles, 6061 aluminum alloy forgings have become a key material for new energy vehicles and rail transit due to their high strength, strong corrosion resistance and high recyclability.
- Chassis – 6061 forgings are used in chassis systems of electric vehicles and high-performance fuel vehicles to increase rigidity and reduce vehicle weight.
- Bumper – Provides high energy absorption capacity to improve vehicle collision safety.
- Battery bracket – 6061 material can improve the rigidity of battery support and enhance the safety of battery pack, and is particularly suitable for new energy vehicles.
- Window frames & lightweight roof racks – Using 6061 forgings can reduce vehicle weight and improve fuel economy or driving range.
Partners: Tesla, Ford, GM, BYD
Marine & Ship
6061 aluminum alloy has excellent corrosion resistance and high strength in marine environments and is suitable for marine engineering and shipbuilding.
- Hull structure – 6061 aluminum forgings are used to manufacture lightweight, high-strength hull frames to reduce fuel consumption and increase speed .
- Door Frames – For corrosion resistant, high strength marine door and gangway brackets.
- Offshore platform support – 6061 material has excellent seawater corrosion resistance and is suitable for offshore drilling platforms and wind power support systems.
Partners: CSIC, CCS (China Classification Society)
New Energy & Electricity
In the new energy industry, 6061 aluminum alloy has become an important material for wind power, solar energy, and battery energy storage systems due to its good conductivity, stable structure, and corrosion resistance.
- Wind turbine frame – 6061 aluminum is used for wind turbine brackets and rotating parts to improve the overall structural strength.
- Photovoltaic bracket – 6061 material is lightweight and corrosion-resistant, suitable for solar photovoltaic brackets to extend service life.
- Battery Energy Storage System – Used in energy storage battery brackets and housings to improve heat dissipation efficiency and system safety.
Partners: BYD, Tesla Energy Storage, LONGi Solar
Architecture & Structure
In modern construction and infrastructure construction, 6061 aluminum forgings are widely used in high-rise buildings and bridge projects due to their excellent strength, weather resistance and plasticity.
- Curtain wall frame – 6061 aluminum is used in curtain wall systems to provide a high-strength frame while taking into account aesthetics and durability.
- Bridge supports – 6061 aluminum alloy can reduce structural weight, improve durability and corrosion resistance, suitable for light bridges or pedestrian bridges.
- Decorative Profiles – 6061 has good machinability and anodizing properties, suitable for architectural decoration and supporting structures.
Partners: Vanke, China State Construction Engineering Corporation
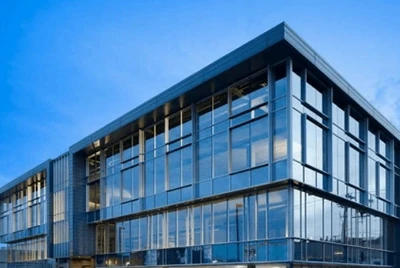
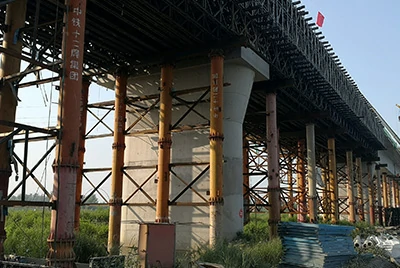
Why recommend Chalco as your 6061 aluminum alloy forgings supplier?
- The world's leading aluminum processing manufacturer with full-process forging and deep processing capabilities
- Powerful production equipment and technology, providing full coverage of die forging, free forging and rotary forging
- Rich industry experience, long-term supply to aviation, rail transit, new energy, military industry and other fields
- Strict quality control, in compliance with international standards such as ASTM, AMS, GB, etc.
- Global supply and fast delivery to meet the market needs of different countries and regions
- Contact us today for a quote and technical support on Chalco 6061 High Performance Forgings!