Aluminum Slug is an aluminum alloy material produced through stamping, deep drawing, and forming processes, widely used across various industries, especially in sectors like packaging, automotive, electronics, and medical fields.
As a professional aluminum supplier, Chalco’s Aluminum Slug offers excellent deep drawing performance, outstanding machinability, and superior mechanical properties, making it suitable for manufacturing aluminum bottles, aluminum cans, aerosol cans, bottle caps, capacitor housings, and more.
- 1. Introduction to Aluminum Slug
- 2. Alloy Products of Aluminum Slug
- 3. Applications of Aluminum Slug
- 4. Shapes of Aluminum Slug
- 5. Surface Treatment of Aluminum Slug
- 6. Production Methods for Aluminum Slug
- 7. Aluminum Slug Gallery
- 8. Why Choose Chalco's Aluminum Slug
- 9. Purchasing Guide for Aluminum Slug
- 10. Frequently Asked Questions
Introduction to aluminum slug
Alloys: 1050, 1060, 1070, 1100, 3003, 3102, 6060, 6061, 6063, 6082
Diameter: 5-150mm (Common diameters: 20, 25, 27, 40, 45, 50, 54, 63.5, 74, 75, 85, 89, 90, 116 mm)
Thickness: 2-30mm
Shapes: Round, Oval, Column, Rectangle
Surface Shapes: With or without hole, Flat, Concave (Domed), Conical
Surface Treatment: Mil finish, Bright, Polishing, Coated, Tumbled, Blasted, Vibrated
Production Methods: Punched, Sawing
Standards: EN 573, EN 570, ROHS, SGS
Aluminum slug alloy products
Aluminum slug - aluminum pure
-
1100 Aluminum Slug
Contains a small amount of copper to increase the alloy's strength. Offers good formability and conductivity. Widely used in automotive parts, electronic product enclosures, etc.
Aluminum slug - aluminum alloy
-
3102 Aluminum Slug
Contains manganese and copper, offering good weldability and corrosion resistance. Perfect for manufacturing thin-walled products, especially for containers with detailed requirements.
-
6060 Aluminum Slug
Contains magnesium and silicon, providing good strength, corrosion resistance, and excellent extrudability. Suitable for manufacturing high-end packaging and automotive parts.
-
6082 Aluminum Slug(High Strength)
Contains manganese, providing high strength and corrosion resistance. Suitable for applications with high strength requirements, such as automotive structural parts, industrial machinery components, etc.
Applications of aluminum slug
Aluminium slug for containers
Our aluminum slugs can be used to manufacture a variety of end products, such as collapsible tubes, medicine tubes, cosmetic containers, aerosol cans, aluminum bottles, capacitor housings, automotive oil filter housings, marker pen tubes, bottle caps, and more.
Aluminium Slug for Aerosol Cans
Aluminum aerosol cans, made from a single aluminum piece without side seams, offer high compressive strength and air resistance. They are commonly used for personal care products, detergents, insecticides, automotive items, and industrial aerosols.
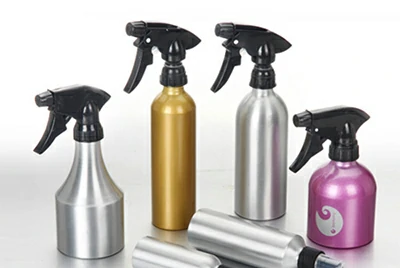
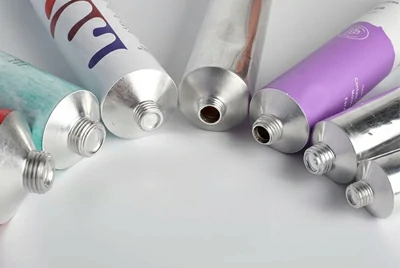
Aluminum Slugs for Collapsible Tubes
Aluminum collapsible tubes, formed from a single punched aluminum slug, eliminate the need for shoulder-body connections, reducing quality risks. With excellent light-blocking, moisture-proof, and gas barrier properties, they are widely used for packaging cosmetics, pharmaceuticals, food, and daily products like toothpaste, paint, and shoe polish.
Aluminium Slug for cosmetic tube
Cosmetic tubes, also known as cream aerosol cans, are typically used for packaging various cosmetic and cream products, such as lipstick tubes, mascara tubes, makeup brush handles, face cream jars, and shaving cream tubes.
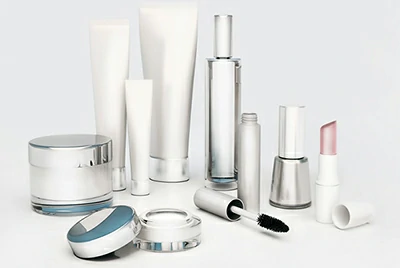
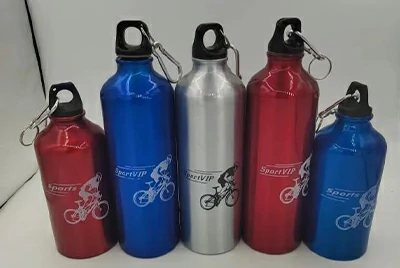
Aluminium Slug for Monobloc Bottles
Aluminum bottles are made from 7cm diameter slugs, shaped through punching and molding. The interior is coated with a chemically inert polymer and baked for safe liquid storage. These bottles are commonly used for sports water bottles, beverage bottles, and more.
Aluminium Slug for Beverage/Food Container
Mainly used in the production of various food and beverage packaging, such as aluminum beer bottles, cream aerosol cans, and beverage aerosol cans.
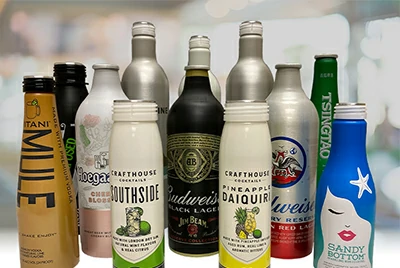
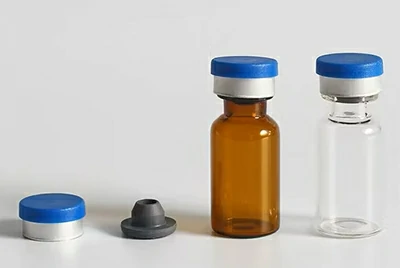
Aluminium Slug for pharmaceutical Packaging
Aluminum pharmaceutical packaging preserves the safety, effectiveness, and stability of medications by not reacting with them. Lightweight, strong, and easy to clean, it is ideal for packaging ointments, creams, and gels.
Aluminum Slugs for Packaging Closure
Primarily used in the production of various metal bottle caps, such as screw caps, flip-top caps, and dispensing caps.
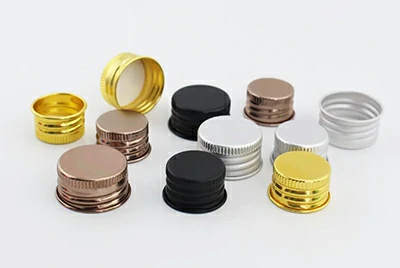
Aluminum slug for punched parts
Aluminum Slug for Automotive Parts
Widely used in the production of automotive fuel filter housings, valves, cylinders, pistons, hydraulic filter housings, airbag system components, and more. Aluminum parts are lightweight and highly recyclable, contributing to reduced energy consumption.
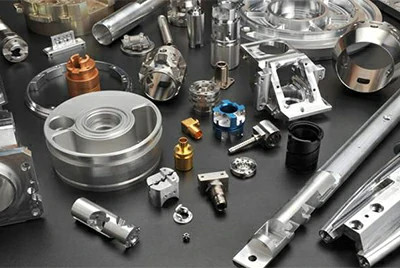
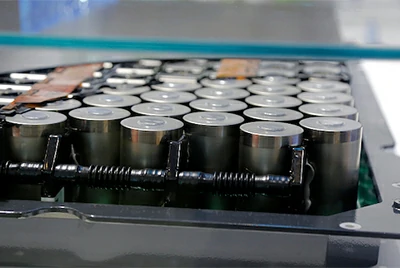
Aluminium Slug for New Energy Battery Case
Used in the production of new energy battery cases, protecting battery cells and ensuring efficient energy storage to support the development of sustainable energy solutions.
Aluminium Slug for Capacitor Shell
Aluminum capacitor housings are lightweight, corrosion-resistant, and non-toxic. With low density and excellent ductility, they offer production advantages and ensure the durability and protection of internal components, making them crucial for capacitors.
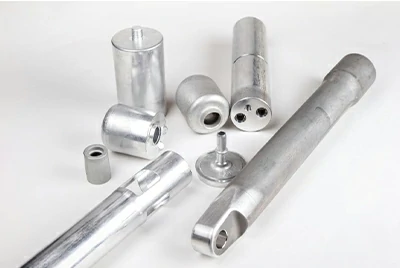
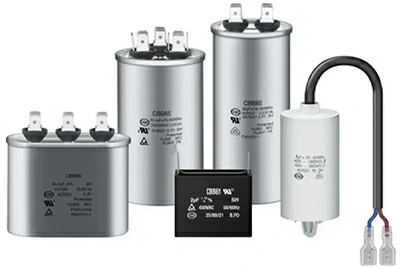
Aluminium Slug for Electronic Components
Used for various electronic components, aluminum slugs offer lightweight and corrosion-resistant properties, ensuring the reliability and longevity of electronic devices.
Aluminum Slug for gas cylinders
Aluminum gas cylinders, with gas-tight properties and high internal pressure resistance, are used for high-purity gases, medical oxygen, and fire extinguisher shells. Weighing only 1/4 of steel cylinders, they form a natural oxide layer for enhanced corrosion resistance and are non-magnetic.
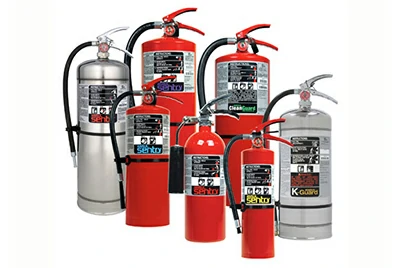
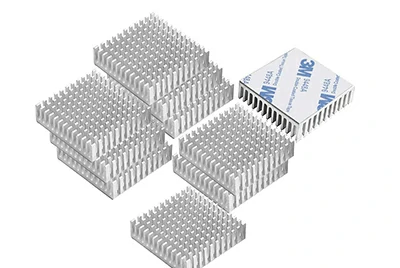
Aluminum Slug for heat radiator
Used in stamping small electronic components like pin-type heat radiators, typically using round or rectangular aluminum slugs. Ideal for compact applications where extrusion is not feasible, especially in small radiators.
Aluminum Slugs for Cigarette Lighter Shell
Widely used in the production of automotive fuel filter housings, valves, cylinders, pistons, hydraulic filter housings, airbag system components, and more. Aluminum parts are lightweight and highly recyclable, contributing to reduced energy consumption.
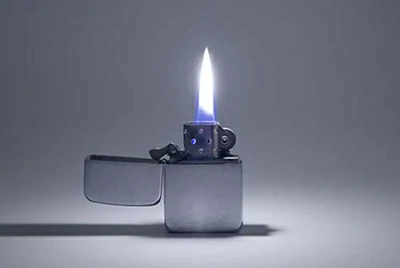
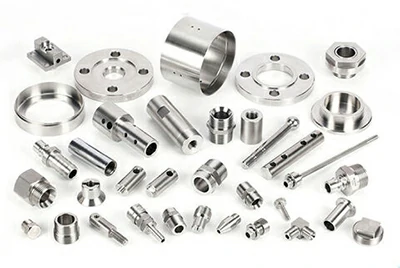
Aluminum Slug for Mechanical Components
Suitable for manufacturing various mechanical components, offering high precision and reliability. These aluminum slugs are widely used in industrial equipment and mechanical structures.
Which shape of aluminum slug is suitable for your products?
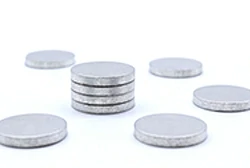
Flat Aluminum Slug
Widely used in aerosol cans, industrial packaging, and air conditioning mufflers where high precision and a flat surface are required.
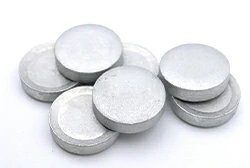
Round Aluminum Slug
Used in capacitor housings, piston components, bumper sensors, and bottle caps, offering high processing accuracy and excellent formability.
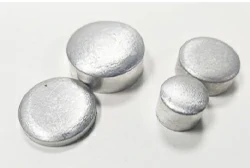
Domed Aluminum Slug
Domed aluminum slugs are suitable for products requiring a hollow or domed design, such as containers or airbag components.
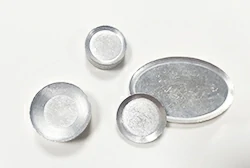
Concave Aluminum Slug
Suitable for products with a concave design, such as cosmetic packaging, beverage bottle caps, dryers, and clutch components.
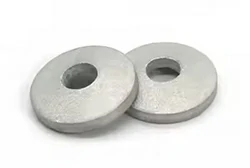
Aluminum Slug with Hole
Suitable for aluminum collapsible tubes, suspension components, pharmaceutical tubes, cigar tubes, and more.
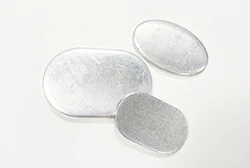
oval aluminum slugs
Suitable for aluminum component extrusion, oil filter housings, filter core assemblies, and more.
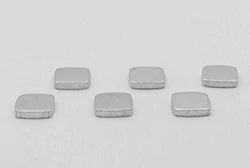
Column Aluminum Slug
Suitable for extrusion or stamping, are commonly used in automotive and electronic products.
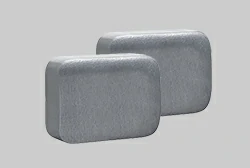
Rectangle Aluminum Slug
Narrow radius slugs and heat sinks, used primarily for mass production packaging, offer high efficiency and stable processing.
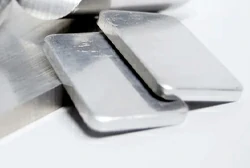
Strip shape Aluminium Slugs
Commonly used for manufacturing long-strip industrial parts, such as components for auto radiators and air conditioning systems.
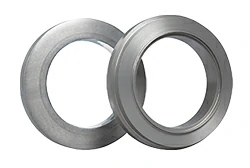
Large Center Hole Aluminum Slug
With a prominent center hole, these slugs are ideal for extrusion or assembly and are commonly used in transmission piston manufacturing.
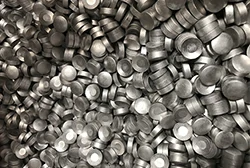
Aluminum Slug Granule
Typically refers to small aluminum granules, often used in the production of oral solution containers, caps, and other small extruded parts.
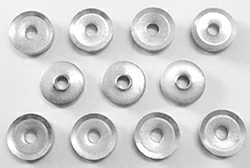
Special Through-Hole Aluminum Slug
Trumpet-shaped hole slugs prevent embedding into the cavity and are commonly used for shoe polish and toothpaste tube production.
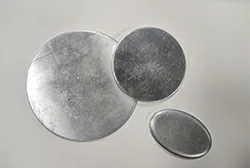
large diameter aluminum Slug
Slugs with a diameter over 180mm and thickness under 8mm, used for manufacturing glue boxes, paint tubes, and automotive touch-up tubes.
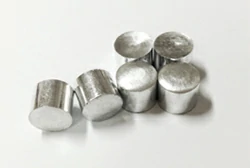
Extra thick aluminum Slug
Slugs with small diameters and large thicknesses, are commonly used for marker pen and cigar tube production.
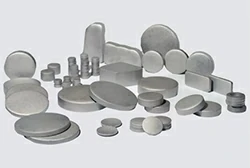
Multiple Radius Aluminum Slug
We can also customize molds based on your specific requirements to produce other special shapes and surface aluminum slugs.
What type of surface treatment do you need for your aluminum slug?
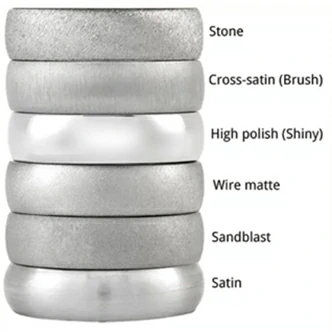
Surface Treatment
We offer a variety of surface treatments, including Mil finish (rolled surface), Bright, Polishing, Coured, Tumbled, Blasted, and Vibrated, to meet the strict appearance and performance requirements of different industries.
After bright processing, the surface quality is effectively improved (smooth, burr-free), making it ideal for appearance parts.
After coarse processing, the aluminum slug combines better with lubricating oils, improving the efficiency of the stamping process.
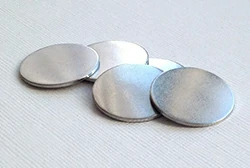
Brigh Aluminum Slug
The bright surface, achieved by mechanical or chemical polishing, provides a higher reflectivity.
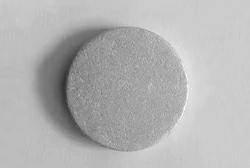
Blasted Aluminum Slug
This treatment involves high-speed abrasive blasting to remove the oxide layer, increasing surface roughness and enhancing adhesion.
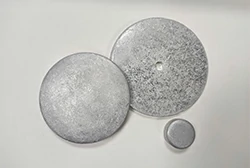
Tumbled Aluminum Slug
The slug is placed in a drum containing abrasives and rolled to achieve surface roughening.
Production methods of aluminum slug
Chalco offers two different production methods for Aluminum Slug: Stamping and Saw Cutting. Each method has its unique process flow to ensure high-quality and high-performance products.
Stamping production process
Smelting: We first melt high-quality aluminum ingots (AA1070 alloy, 99.7% purity) into molten aluminum. The molten aluminum undergoes degassing, refining, and filtration before entering the casting wheel to ensure purity. The use of aluminum ingots, compared to direct use of molten aluminum, offers better performance with fewer impurities, ensuring higher product quality and consistency. The furnace temperature is strictly controlled, and all atmospheric emissions comply with environmental regulations.
Continuous Casting and Rolling: We use a ring-type casting and rolling machine to produce high-quality aluminum strips from molten aluminum. This process not only maintains excellent mechanical properties and consistency in the aluminum material but also enhances deep-drawing capabilities, reducing the risk of cracking after stamping. The casting wheel runs at speeds of up to 7 meters per minute, producing strips with a width of up to 180mm and thickness up to 20mm.
Stamping: High-precision stamping machines are used to process the aluminum strip into Aluminum Slug. We strictly control the dimensions and shapes of each batch, typically using multiple high-speed stamping machines, each equipped with unwinding and straightening machines to ensure no deviation in the strip during the stamping process. Accurate lubrication is applied to improve stamping efficiency. Stamping waste is recycled to ensure the environmental sustainability and efficiency of the production.
Annealing: Annealing is carried out in a box-type annealing furnace at 530°C for approximately 10 hours to ensure uniform internal structure and improve the product's ductility and fatigue resistance. We use a tunnel-type electric heating annealing furnace with a processing time of about 8 hours to ensure each batch of aluminum slugs meets the minimum strength and optimal ductility.
Surface Treatment: Rolling or shot blasting is used to ensure the surface roughness of the aluminum slugs meets the standards for applying cold extrusion lubricants. The rolling treatment is done by placing the slugs into a rotating drum, while shot blasting is done by spraying aluminum shot on the rotating belt. The surface treatment time typically ranges from 12 to 15 minutes, depending on the slug size.
Packaging: The finished aluminum slugs are packaged based on customer requirements. Each batch undergoes strict inspection and weighing before packaging in cardboard boxes, with each box weighing 25kg. These boxes are then placed on wooden pallets, with each pallet holding 45 boxes for a total weight of 1125kg. The products are securely plastic-wrapped for safe export transportation.
Saw cutting production process
Bar Preparation: Chalco uses hot-extruded bars or precision drawn bars, made from EN AW-1xxx, EN AW-3xxx, EN AW-5xxx, and EN AW-6xxx series aluminum alloys to ensure consistency in formability and deep-drawing performance.
Precision Saw Cutting: High-productivity, high-quality saw cutting equipment is used to accurately cut the bars to the required thickness and diameter. Especially when using drawn bars, tight tolerances are maintained to meet the strictest quality and technical standards.
Annealing: After cutting, the slugs are annealed according to the customer’s specified annealing procedure to adjust the material's hardness and machinability, ensuring the final product's quality and stability.
Surface Treatment: Methods such as shot blasting or vibration are used to process the surface, ensuring smoothness and consistency of the aluminum slug surface, making it suitable for subsequent processing and applications.
Packaging and Storage: The treated aluminum slugs are packaged and stored to prevent damage during transportation and ensure timely delivery to customers.
Gallery of aluminum slug


Why choose Chalco's aluminum slug?
1. Advanced Production Equipment and Technology
Chalco uses imported equipment and internationally advanced technology to ensure that our products meet international standards. We have a full range of production lines, from casting to surface treatment, including continuous casting and rolling, stamping, annealing, and shot blasting equipment. This allows us to meet the diverse needs of our customers and maximize product quality.
2. Strict Quality Control and Certifications
Our products are certified by ISO 9001 and ISO 14001. The stamped aluminum slugs comply with EN 573 and EN 570 standards, while saw-cut aluminum slugs meet EN 754, EN 755, and EN 10204 standards, as well as certifications like ROHS and REACH. This ensures that our products are safe and environmentally friendly, and meet the highest quality standards.
3. Strong Production Capacity
Chalco operates multiple production lines, equipped with furnaces, continuous casting and rolling, annealing furnaces, shot blasting machines, and vibration equipment. For base materials under 10mm, we can cast up to 140 tons per day, with a monthly production capacity exceeding 3000 tons. This significantly enhances both production efficiency and product quality, enabling us to meet large-scale production demands.
4. Customized Services and Solutions
Chalco offers comprehensive customization services based on customer needs, providing tailored solutions in terms of production methods, sizes, shapes, and surface treatments. We cater to the unique requirements of various industries, ensuring that all product manufacturing processes are traceable, and quality remains stable.
5. Technological Innovation and R&D
We continually invest in research and development to drive technological innovation. By improving our processes and developing new alloy materials, our R&D team is committed to offering customers market-leading Aluminum Slug solutions. These innovations help customers improve product performance and enhance their market competitiveness.
6. Environmental Protection and Sustainability
Chalco strictly adheres to international environmental protection standards, with all production processes certified under ISO 14001. We use green production technologies to reduce energy consumption and actively promote resource recycling and reuse (such as recycling stamped scrap into molten aluminum). We are dedicated to creating a sustainable production system.
Are You Looking for an Aluminum Supplier?
If you need a professional aluminum supplier to provide you with high-quality, cost-effective aluminum, we will be your best choice.
Guide to purchasing aluminum slug
1. Alloy selection
The alloy type of Aluminum Slug determines its performance and application range. We offer a variety of alloy grades, including 1050, 1060, 1070, 3003, 6060, and more, suitable for different requirements such as mechanical strength, corrosion resistance, and formability.
For example, 1050 and 1070 alloys are ideal for food packaging, 3003 is commonly used for automotive parts, and 6061 is suitable for high-strength structural applications. Customers should choose the appropriate alloy based on the final application to ensure optimal product performance.
2. Shape selection
From the shape, the aluminum slugs can be separated as flat round, semicircular, conical, square, rectangular, oval, perforated, and non-porous type.
- Non-porous flat round, semi-circular, conical types are suitable for processing canned products.
- Flat round, perforated semi-circular, conical types are suitable for processing tube products.
- The square, oval, and rectangular types are suitable for processing parts.
Shape | ||
![]() |
![]() |
![]() |
3.Dimensions and tolerances (EN 570)
The dimensions and tolerances of Aluminum Slug are vital for subsequent processing and forming. We provide various production methods and specifications for aluminum slugs, including different thicknesses and diameters, and can offer high-precision tolerance control based on customer requirements. This ensures the product is suitable for high-standard processing. Below are the tolerance tables for different shapes and production methods:
Circular Aluminum Slugs: Diameter tolerance
Tolerances on diameter of punched aluminum slugs | |
Aluminum Slug Diameter/mm | Tolerances/mm |
≤10 | ±0.02 |
10-40 | ±0.03 |
40-60 | ±0.04 |
60-80 | ±0.05 |
80-120 | ±0.06 |
120-150 | ±0.08 |
150-200 | ±0.10 |
Tolerances on diameter of sawn aluminum slugs | |
Aluminum Slug Diameter/mm | Tolerances/mm |
3-6 | 0 - 0.07 |
6-10 | 0 - 0.09 |
10-18 | 0 - 0.11 |
18-30 | 0 - 0.13 |
30-50 | 0 - 0.16 |
50-65 | 0 - 0.5 |
65-80 | 0 - 0.6 |
80-130 | 0 - 0.9 |
Aluminum Slugs with Holes: Hole diameter tolerance
Hole diameter of punched aluminum slugs | |
Aluminum Slug Diameter/mm | Tolerances/mm |
≤10 | ±0.05 |
10-20 | ±0.07 |
≥20 | ±0.1 |
*The above tolerances apply to stamped aluminum slugs with holes that do not exceed 40% of the slug diameter and with thickness no more than two-thirds of the hole diameter. Eccentricity of the hole must not exceed 0.15mm.
Tolerances on outside or inside diameter and wall thickness for sawn slugs | ||||||||
Outside diameter or inside diameter/mm | Tolerances for wall thicknesses/mm | |||||||
Size | Tolerances | 2.5-3 | 3-5 | 5-8 | 8-10 | 10-15 | 15-20 | 20-25 |
15-20 | ±0.25 | ±0.25 | - | - | - | - | - | - |
20-30 | ±0.30 | ±0.25 | ±0.30 | - | - | - | - | - |
30-50 | ±0.30 | ±0.30 | ±0.35 | ±0.40 | ±0.45 | - | - | - |
50-100 | ±0.50 | - | ±0.35 | ±0.45 | ±0.50 | ±0.55 | ±0.60 | - |
100-130 | ±0.70 | - | - | ±0.45 | ±0.50 | ±0.60 | ±0.60 | ±0.60 |
*The above tolerances apply to hole saw cut blocks made from round tube with or without extrusion seam.
Rectangular Aluminum Slugs: Length and width tolerance
Tolerances on length and width of punched rectangular slugs | |
Length and width/mm | Tolerances/mm |
≤10 | ±0.05 |
10-20 | ±0.08 |
20-40 | ±0.10 |
40-60 | ±0.12 |
60-120 | ±0.14 |
120-150 | ±0.17 |
150-200 | ±0.20 |
Rectangular Aluminum Slugs: Thickness tolerance
Tolerances on thickness of punched slugs | |
Slugs thicknesses/mm | Tolerances/mm |
≤2.8 | ±0.03 |
2.8-6.5 | ±0.05 |
6.5-8.5 | ±0.07 |
8.5-10.5 | ±0.10 |
10.5-15 | ±0.14 |
15-20 | ±0.18 |
20-25 | ±0.22 |
25-30 | ±0.26 |
30-40 | ±0.30 |
*The tolerances apply only to slugs with a maximum thickness not exceeding half the diameter (in the case of round slugs) or not exceeding half the width (in the case of rectangular slugs).
Saw-cut Aluminum Slugs: Parallelism and verticality tolerance
Tolerances on thickness of sawn slugs | ||||
Diameter or width | Tolerances for thicknesses/mm | |||
7 - 10 | 10 - 20 | 20 - 40 | 40 - 70 | |
≤15 | ±0.15 | ±0.15 | ±0.15 | ±0.20 |
15-30 | ±0.15 | ±0.20 | ±0.20 | ±0.25 |
30-70 | ±0.15 | ±0.20 | ±0.25 | ±0.30 |
70-100 | ±0.30 | ±0.35 | ±0.40 | ±0.45 |
100-130 | ±0.40 | ±0.45 | ±0.50 | ±0.60 |
4.Surface and edge quality
Slight scores, spallings or discolourations result from the manufacturing process. Scratches, scour
marks, indentations and other damage due to mechanical action cannot always be avoided.
An assessment of whether such defects are acceptable shall be based on the following:
- Large scores, spallings, cracks and damaged areas, incomplete slugs, flaking, formation of blisters and inclusions of foreign matter are not permitted. Slight damage due to production process, such as edge deformations, are unavoidable and hence is permitted.
- Slight scores, indentations and edge deformations, and discolourations due to a heat treatment or surface treatment, such as scouring or blasting, are unavoidable and hence are permitted.
5.Surface treatment
Surface treatment directly affects the appearance and performance of Aluminum Slug in processes like stamping and deep drawing. We offer a variety of surface treatments, primarily categorized into bright and roughened finishes.
After roughening, the aim is to improve the lubrication properties for better stamping efficiency. We provide coated, blasted, and tumbled surface treatments to meet the surface quality requirements of different industries.
The choice of surface treatment should take into account the final product's aesthetics, durability, and ease of subsequent processing.
6.Hardness requirements
Chemical symbols | Brinell hardness HB | Chemical symbols | Brinell hardness HB |
EN AW.1098 | 18 | ENAW-5005A | 37 |
EN AW-1080A | 19 | EN AW-5305 | 33 |
EN AW-1070A" | 21 | EN AW-5505 | 33 |
EN AW-1050A" | 23 | EN AW-5110 | 27 |
EN AW-1200 | 25 | EN AW-5210 | 27 |
EN AW-2011 | 50 | ENAW-5754 | 58 |
EN AW-3102 | 23 | EN AW-6060 | 35 |
EN AW-3103 | 33 | EN AW-6061 | 40 |
EN AW-3207 | 25 | EN AW-6082 | 40 |
7.Packaging
To ensure the integrity and quality of Aluminum Slug during transportation and storage, we offer professional packaging services. Each packaging unit is carefully designed to prevent damage or contamination during transit.
- Packaging: Sturdy cardboard boxes are used for packaging, with each box holding 25kg.
- Pallets: Each pallet holds 45 boxes, with a total weight of 1125kg.
- Material: Wooden pallets, with dimensions of 1.1 x 1.1 x 1.1 meters.
FAQ
What is the minimum order quantity (MOQ) for aluminum slug?
The MOQ depends on the specifications and type of Aluminum Slug in your order.
Standard Sizes: We can often match our existing molds, and if the required size is close to an existing mold, the MOQ can be very small (500kg).
Custom Sizes: For non-standard sizes or custom molds, the MOQ will be higher, as mold costs are significant and ordering a small quantity would be uneconomical.
How do you ensure the quality of your aluminum slug products?
Chalco implements strict quality control procedures from raw materials to finished products. Each batch has a unique identification code, ensuring traceability throughout the process.
All outgoing Aluminum Slug products meet international standards such as EN 573, EN 570, and EN 10204, guaranteeing high quality and reliability.
How do you ensure timely delivery of aluminum slug?
We are committed to responding quickly to customer demands. The usual delivery time depends on the order quantity and specific requirements, typically ranging from 15 to 30 days. We have a stable raw material supply chain and efficient production capacity (up to 140 tons of casting per day), ensuring that orders are delivered on time.