What is 6061 Aluminum Slug?
6061 aluminum slugs, also known as flat round aluminum blanks, are widely used in aerosol cans, automotive components, battery enclosures, electronic housings, and industrial applications. Compared to 1000-series and 3000-series aluminum slugs, 6061 aluminum offers higher strength, better corrosion resistance, and improved machinability, making it ideal for high-pressure applications.
Chalco 6061 aluminum slug specifications & technical details
Standard Size Ranges:
- Diameter: 20mm – 116mm (Maximum up to 2000mm)
- Thickness: 0.5mm – 15.0mm (Customizable up to 150mm)
- Surface: Mill finish, tumbled, shot blasted, mirror polished, brushed, embossed, PE PVDF color coating, Teflon coating
- Specification: EN 573-3 (Chemical Composition), EN 570 (Mechanical Properties & Tolerances)
- Technical parameter: Click to check the [Technical Details Table]
High-Precision Manufacturing:
- CNC Machining – Guarantees precise dimensions with smooth surface finishes
- Heat Treatment – Uniform temperature control to eliminate internal stress and enhance mechanical properties
- Automated Inspection – Laser-measured dimensional accuracy for consistent quality
Chalco 6061 aluminum slug-multi product type selection
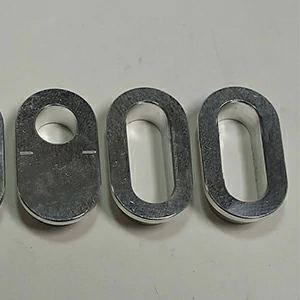
6061 CNC pressing aluminum slug
High-precision 6061 aluminum slug, CNC machined to ensure accurate dimensions and smooth surface. Widely used in high-precision parts in aerospace, automotive and other industries.
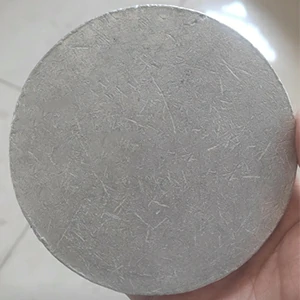
6061 large diameter aluminum slug
Thickness: 6-150mm; diameter:200-2000mm
Advanced production technology is used to ensure uniformity and cooling of aluminum alloy to avoid thermal stress and defects; temperature is uniform during heat treatment to improve mechanical properties. High-precision CNC equipment is used for subsequent processing to ensure size and surface quality as well as product stability and Superior performance.
-
Plain aluminum slug
Features: Standard round or square
Application: aerosol cans, packaging, etc.
Production: Simple stamping or casting
-
Rectangle aluminum slug
Features: Rectangular shape
Application: electronic components, automotive parts, etc.
Production: Requires custom rectangular mold
-
Oval aluminum slug
Features: Oval shape
Application: Aerosol cans, auto parts, etc.
Production: The production is difficult
-
Aluminum flat domed slug
Features: Flat top dome shape
Application: cosmetics, pharmaceutical packaging, etc.
Production: Dome height needs to be precisely controlled
-
Domed conical aluminum slug
Features: Conical appearance
Application: High strength components
Production: Special stamping or drawing processes are required
-
Domed spherical aluminum slug
Features: Spherical appearance
Application: pressure vessel, etc.
Production: More complicated, requiring die-casting or high-precision stamping
-
Aluminum slug with hole
Features: Aluminum blank with holes
Application: electronic components, parts, etc.
Production: stamping process plus hole processing
-
Aluminum slug concave shape with hole
Features: Concave with holes
Application: electronic packaging, automotive parts, etc.
Production: The production process is complicated
-
Aluminum punching slug
Features: Serrated periphery
Application: parts manufacturing, etc.
Production: Precision stamping, high precision.
-
Other shapes
We offer slugs in various shapes and processing options. If you have specific product requirements, please feel free to contact us!
Customization Available!
If your project requires specific dimensions, alloy grades, or surface treatments, we offer tailor-made aluminum slugs based on your exact needs. Contact us for a consultation!Quick Quote
Other aluminum blank products in Chalco - Choose the right product to your project
When purchasing aluminum blanks, one may be struggled to distinguish between aluminum slugs, blocks, circles, and billets, unsure which is the best fit for their specific project. Each of these aluminum preforms has unique processing methods, strength properties, and applications, making it essential to select the right one based on your manufacturing needs.
To help you make an informed decision, we've outlined the differences between these aluminum blanks, ensuring you choose the most suitable product for your production process.
-
Best for deep drawing, impact extrusion, and cold forming applications where lightweight, precision, and formability are required.
-
Ideal for CNC machining, milling, and heavy structural applications, commonly used in mold making and industrial components.
-
Perfect for cookware, signage, and decorative applications, where uniform thickness and easy stamping are needed.
-
Aluminum Billets
Best suited for extrusion, rolling, and forging, making them the top choice for aerospace, automotive, and heavy-duty applications.
Feature | Aluminum Slug | Aluminum Block | Aluminum Circle | Aluminum Billet |
Definition | Small, cylindrical or flat preforms mainly used for deep drawing & impact extrusion | Large, rectangular or square aluminum piece, typically CNC-machined | Flat, circular aluminum sheet, used for stamping or forming | Extruded or cast aluminum bar, used for forging or further extrusion |
Processing Method | Cold extrusion, deep drawing, impact forming | Milling, CNC machining, cutting, forging | Stamping, deep drawing, spinning | Extrusion, casting, forging, rolling |
Best for | Aerosol cans, battery enclosures, automotive parts | Mold making, machine parts, structural applications | Cookware, traffic signs, decorative applications | Aerospace components, automotive parts, industrial bars |
Common Alloys | 6061, 1070, 3003 | 6061, 7075, 5083, 2024 | 1050, 1100, 3003, 5052 | 6061, 6082, 7075, 2024 |
Surface Finish | Tumbled, shot blasted, anodized | Milled, polished, anodized, coated | Mill finish, polished, anodized, coated | Milled, extruded, heat-treated |
Chalco 6061 aluminum slug——various surface treatments available
Tumbled
Tumbling rotates aluminum blocks with abrasives to smooth surfaces, remove burrs, and sharp edges. This process enhances appearance, reduces defects, and improves subsequent processing efficiency.

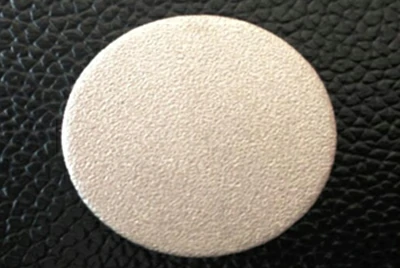
Shot blasting
Sandblasting and shot blasting use abrasives to clean and roughen aluminum surfaces, removing rust or oxides. Ideal for enhancing adhesion before coating, painting, or welding.
Bright
The bright aluminum slug, achieved through mechanical or chemical polishing, features high reflectivity and a smooth, shiny surface, widely used in aerosol cans, decoration, and lighting industries.
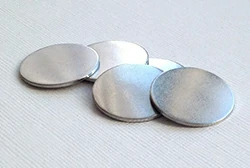
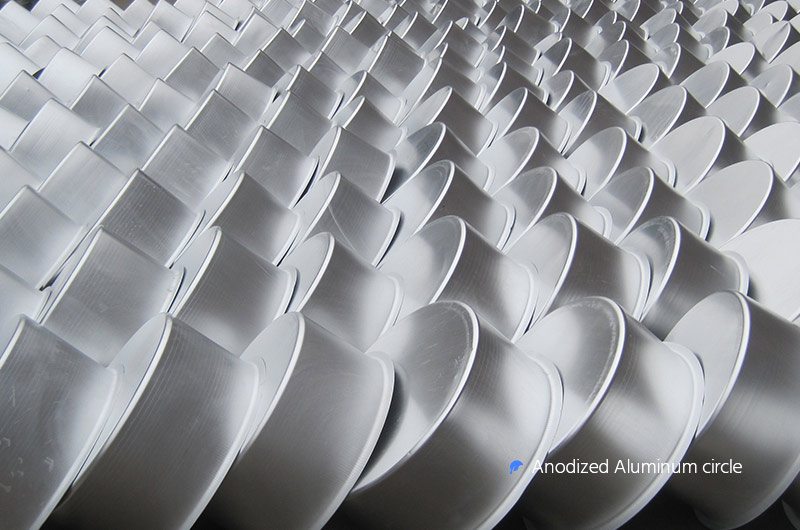
Anodizing & Color Coating
Creates a protective oxide layer that enhances corrosion resistance, durability, and aesthetics, making it ideal for consumer packaging and electronics.
Chalco 6061 Aluminum Slug – applicable to multiple industry fields
Aluminum slug is widely used in the automotive, electronics, packaging and aviation industries as an important raw material for manufacturing aerosol cans, electronic housings, automotive parts, etc. Chalco aluminum slug products have excellent uniformity and stability and can meet the needs of different industries. Quick Quote
6061 aluminum slug for equipment parts/industrial parts
Automotive safety parts
Car air conditioner end cover
Capacitor housing
Electrolytic container shell
Hard wall container
Contact us now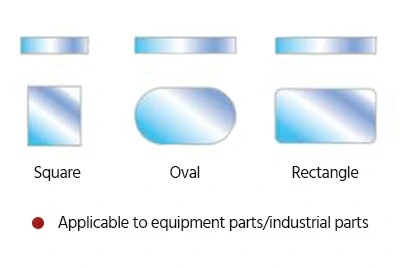
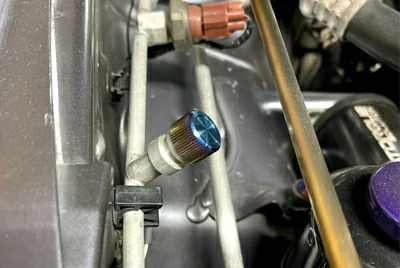
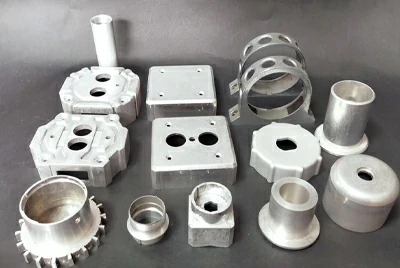
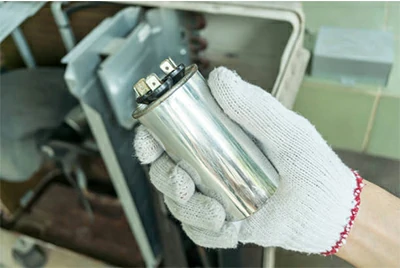
6061 aluminum slug for foldable hose products
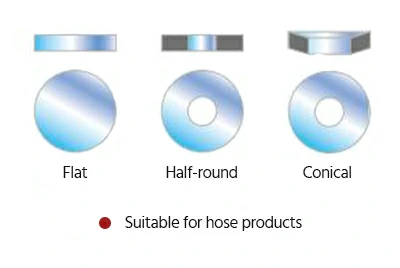
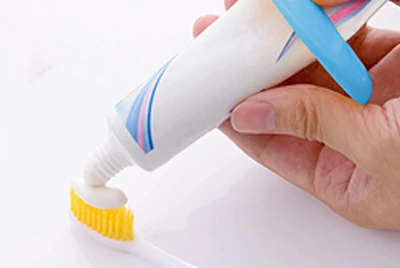
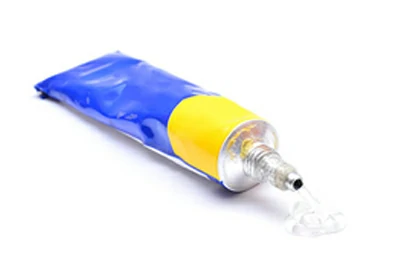
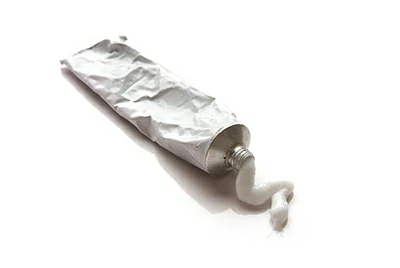
6061 aluminum slug for canned products
Aerosol Containers
Food and Beverage Containers
Medical Containers
Cosmetic Containers
Other aluminum bottles
Contact us now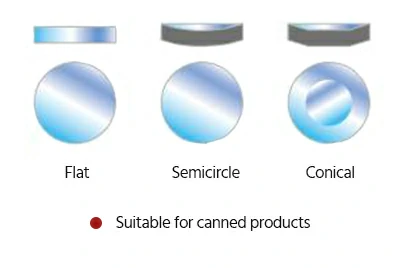
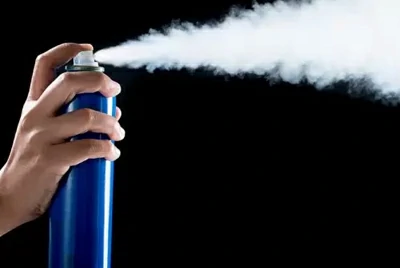
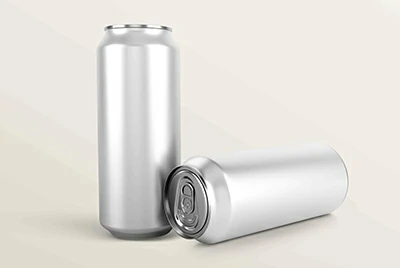
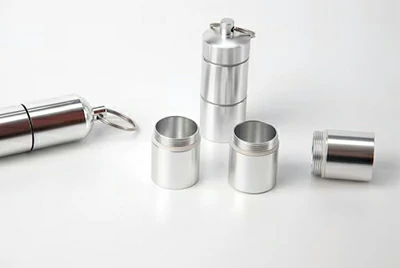
6061 Aluminum Slug for Heat Radiators
Used in stamping small electronic components, such as pin-type heat radiators, typically utilizing round or rectangular aluminum slugs. It is especially suitable for compact applications where extrusion processes are not feasible for small radiators.
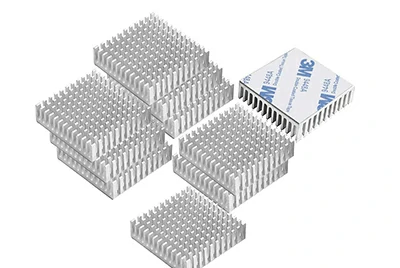
6061 Aluminum Slug for Cigarette Lighter Shell
Widely used in the production of cigarette lighter shells, aluminum components are lightweight and highly recyclable, contributing to reduced energy consumption.
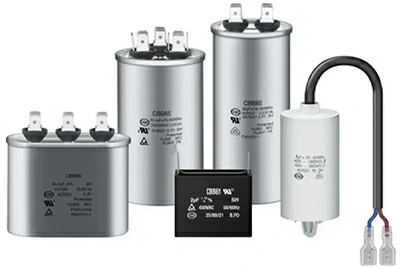
6061 Aluminum Slug for New Energy Battery Cases
Used in the production of new energy battery cases, it protects battery cells and ensures efficient energy storage, supporting the development of sustainable energy solutions.
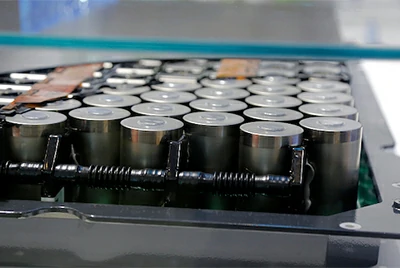
6061 Aluminum Slug for Mechanical Components
Suitable for manufacturing various mechanical components, offering high precision and reliability. These aluminum slugs are widely used in industrial equipment and mechanical structures.
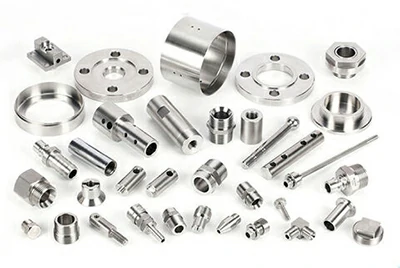
Why Choose 6061 Aluminum Slug?
- High Strength & Durability – Ideal for high-pressure applications, ensuring structural integrity and impact resistance for aerosol cans, automotive parts, and battery enclosures.
- Corrosion & Oxidation Resistance – Withstands moisture, chemicals, and oxidation, making it perfect for electronics, medical packaging, and industrial applications.
- Precision Machining – CNC-machined for tight tolerances and smooth surfaces, ensuring consistent quality and superior sealing performance.
- Lightweight & Eco-Friendly – Reduces material weight while maintaining strength, supporting energy-efficient and sustainable manufacturing.
- Customizable Shapes & Sizes – Available in various diameters, thicknesses, and custom designs, ensuring compatibility with deep drawing, cold extrusion, and stamping processes.
- Excellent Workability & Appearance – Offers good plasticity, easy stretching, and a smooth surface, meeting high aesthetic and performance standards.
- Certified Quality & Strict Standards – Complies with EN 570/573, RoHS, SGS, and ASTM standards, ensuring zero burrs, no surface defects, and uniform annealing for optimized hardness.
- Superior Performance Over Other Alloys – Compared to 1000-series and 3000-series aluminum slugs, 6061 offers higher strength, better corrosion resistance, and improved durability, making it the preferred choice for high-performance applications.


Chalco 6061 aluminum slug production and processing
In our foundry, we ensure that every slug meets high quality standards by strictly controlling the production process. We melt high-quality aluminum and internal material residues, and do not use secondary scrap that may affect product quality. Here is our aluminum slug production process:
1. Melting and Alloying: We alloy and treat the aluminum melt to ensure the accuracy and uniformity of its composition, guaranteeing product quality. The treated melt is then prepared for rotary casting to form narrow strip alloys.
2. Casting and Hot Rolling: During the casting stage, we use precision rotary casting to create narrow strip alloys. These are then processed through hot rolling mills to adjust the thickness and are wound into hot-rolled coils, serving as input material for manufacturing billets.
3. Cold Rolling and Laser Measurement: The hot-rolled coils are further processed through cold rolling mills. During cold rolling, the thickness of the strip is precisely measured using laser measurement equipment to ensure it meets quality standards and tolerance requirements.
4. Precision sawing: The sawing process for slugs involves using high-efficiency sawing equipment to precisely cut aluminum rods into aluminum slug blanks that meet specified dimensions and tolerances, providing a high-quality foundation for subsequent processing.
5. Stamping and Annealing: We use efficient stamping lines with advanced stamping machines, achieving speeds of up to 300 strokes per minute. After stamping, the billets are sent to an annealing furnace to reach the appropriate hardness, ensuring mechanical properties and formability.
5. Surface Treatment: Stamped aluminum billets can undergo sandblasting or rolling treatments as per customer requirements to ensure surface quality. We use advanced sandblasting machines for more delicate surface treatment, enhancing the product's appearance and performance.
6. Packaging and Storage: After surface treatment, the aluminum billets are packaged and stored in sealed warehouses to ensure they remain free from contamination and damage during transportation.
In addition, our production process is flexible, and we can customize various alloys according to customer needs, and we are able to manufacture aluminum billets of different thicknesses and diameters. Whether it is standard alloys or special alloys jointly developed according to buyer needs, we can provide high-quality and high-precision aluminum billet products, which are widely used in the automotive, electronics, packaging and other industries.
Through this entire set of rigorous production processes, we are able to ensure the quality and consistency of aluminum billets, meeting our customers' high requirements for precision, performance and appearance.
Chalco other aluminum slug product series
Chalco 6061 aluminum slug quality control
In aluminum billet production, ensuring high quality and consistency is our top priority. Through a series of precise quality control measures, we can provide aluminum billet products that meet high standards, especially for the automotive, electronics and packaging industries.
1. Alloy consistency and metallurgical pollution control
- Alloy Composition Control: We strictly monitor the chemical composition of aluminum alloys to ensure the consistency of each batch of materials.
- Metallurgical contamination inspection: By comparing the expected and actual weights of aluminum billets, metallurgical contamination can be quickly identified to avoid potential defects and ensure product quality.
2. Dimension and weight accuracy
- Precise dimensional control: Use high-precision measuring tools (such as laser measuring instruments) to ensure that the diameter, thickness and other dimensional tolerances of the aluminum billet are within strict ranges.
- Weight grading: A precision grader is used to check the weight of each aluminum billet to eliminate any deviations and ensure that each aluminum billet meets the specifications.
3. Surface quality and defect detection
- Surface finish inspection: Through visual inspection and automated testing equipment, ensure that there are no scratches, cracks or other defects on the surface of the aluminum blank.
- Surface defect screening: Use a high-power magnifying glass or X-ray to check tiny defects on the surface of the aluminum blank to ensure appearance and functional requirements.
4. Heat treatment and mechanical properties testing
- Uniform heat treatment control: Ensure uniform temperature distribution during heat treatment of aluminum billets to optimize their hardness and ductility.
- Mechanical properties test: Tensile test and hardness test are used to ensure that the aluminum billet meets the required strength and toughness requirements, which is particularly suitable for high-demand automobile and electronic products.
5. Reduce waste and improve production efficiency
- Precision grading and process improvement: Reduce waste in production, improve production efficiency and optimize process flow through weight grading system.
- Energy and cost control: During the production process, accurate control of weight and material consumption reduces energy costs and waste generation, supporting sustainable production.
6. Automated and data-driven quality management
- Automated testing system: Use automated equipment to record data in real time, monitor deviations in the production process, and make timely adjustments to ensure stable quality.
- Data analysis support: Through statistical process control (SPC), we use real-time data analysis to optimize production and quality management and drive continuous improvement.
Technical details table of chalco aluminum slug products
Tolerances on diameter of punched round aluminum slugs | |
Aluminum Slug Diameter/mm | Tolerances/mm |
≤10 | ±0.02 |
10-40 | ±0.03 |
40-60 | ±0.04 |
60-80 | ±0.05 |
80-120 | ±0.06 |
120-150 | ±0.08 |
150-200 | ±0.10 |
Hole diameter of punched round perforated aluminum slugs | |
Aluminum Slug Diameter/mm | Tolerances/mm |
≤10 | ±0.05 |
10-20 | ±0.07 |
≥20 | ±0.1 |
Tolerances on length and width of punched rectangular slugs | |
Length and width/mm | Tolerances/mm |
≤10 | ±0.05 |
10-20 | ±0.08 |
20-40 | ±0.10 |
40-60 | ±0.12 |
60-120 | ±0.14 |
120-150 | ±0.17 |
150-200 | ±0.20 |
Tolerances on thickness of punched rectangular slugs | |
Slugs thicknesses/mm | Tolerances/mm |
≤2.8 | ±0.03 |
2.8-6.5 | ±0.05 |
6.5-8.5 | ±0.07 |
8.5-10.5 | ±0.10 |
10.5-15 | ±0.14 |
15-20 | ±0.18 |
20-25 | ±0.22 |
25-30 | ±0.26 |
30-40 | ±0.30 |
Tolerances on diameter of sawn aluminum slugs | |
Aluminum Slug Diameter/mm | Tolerances/mm |
3-6 | 0 - 0.07 |
6-10 | 0 - 0.09 |
10-18 | 0 - 0.11 |
18-30 | 0 - 0.13 |
30-50 | 0 - 0.16 |
50-65 | 0 - 0.5 |
65-80 | 0 - 0.6 |
80-130 | 0 - 0.9 |
Tolerances on outside or inside diameter and wall thickness for sawn slugs | ||||||||
Outside diameter or inside diameter/mm | Tolerances for wall thicknesses/mm | |||||||
Size | Tolerances | 2.5-3 | 3-5 | 5-8 | 8-10 | 10-15 | 15-20 | 20-25 |
15-20 | ±0.25 | ±0.25 | - | - | - | - | - | - |
20-30 | ±0.30 | ±0.25 | ±0.30 | - | - | - | - | - |
30-50 | ±0.30 | ±0.30 | ±0.35 | ±0.40 | ±0.45 | - | - | - |
50-100 | ±0.50 | - | ±0.35 | ±0.45 | ±0.50 | ±0.55 | ±0.60 | - |
100-130 | ±0.70 | - | - | ±0.45 | ±0.50 | ±0.60 | ±0.60 | ±0.60 |
Tolerances on thickness of sawn slugs | ||||
Diameter or width | Tolerances for thicknesses/mm | |||
7 - 10 | 10 - 20 | 20 - 40 | 40 - 70 | |
≤15 | ±0.15 | ±0.15 | ±0.15 | ±0.20 |
15-30 | ±0.15 | ±0.20 | ±0.20 | ±0.25 |
30-70 | ±0.15 | ±0.20 | ±0.25 | ±0.30 |
70-100 | ±0.30 | ±0.35 | ±0.40 | ±0.45 |
100-130 | ±0.40 | ±0.45 | ±0.50 | ±0.60 |
Aluminum slug market prospects and sustainable development direction of Chalco slug products
Aluminum slug market prospects and development analysis
- Growing market demand: Aluminum slugs are widely used in industries such as automobiles, food and beverages, personal care, pharmaceuticals, paints and coatings, and electrical appliances. Especially in the automotive and consumer goods sectors, demand continues to grow.
- Diversified material sources: Common aluminum slugs on the market use different types of aluminum alloys and recycled aluminum raw materials (such as PCR, PIR, and green primary aluminum), which helps reduce dependence on natural aluminum resources and promote environmental protection and resource recycling.
- Technological innovation improves production efficiency: The production process of aluminum slugs is increasingly advanced, from efficient stamping technology to fine surface treatment technology, which has significantly improved the quality and production efficiency of aluminum slugs.
- Expansion of application areas: The rising demand for aluminum slugs in aerosol containers, automotive parts, electronic products and other fields has further promoted the expansion of the aluminum slug market.
Chalco aluminum slug's sustainable development strategy
- Use of recycled aluminum: Chalco actively uses PCR (post-consumer recycled aluminum) and PIR (post-industrial recycled aluminum) raw materials to reduce dependence on natural aluminum resources and promote the development of a circular economy.
- Efficient and environmentally friendly production process: By optimizing the production process of aluminum slugs, from smelting and casting to stamping and surface treatment, Chalco ensures that every link meets strict environmental requirements, reducing resource waste and carbon emissions in production.
- Low-carbon emission technology: We apply low-carbon emission production technology to improve energy efficiency and reduce environmental impact during the production process.
- Improve product recyclability: Chalco continues to innovate designs to make aluminum slugs more recyclable, in line with the global trend of green environmental protection.
Chalco can provide you the most comprehensive inventory of aluminum products and can also supply you customized products. Precise quotation will be provided within 24 hours.
Get a quote