Köpük alüminyum, yüksek gözeneklilik, geniş özgül yüzey alanı, yüksek özgül mukavemet, yüksek özgül sertlik, iyi enerji emilimi, sönümleme ve şok emme performansı, korozyon direnci, yüksek sıcaklık dayanımı, elektromanyetik koruma, toksik olmayan, kolay işleme, kaplama yüzey işlemi vb. Mükemmel fiziksel ve mekanik özellikleri nedeniyle, köpük metal hem yapısal malzemeler hem de fonksiyonel malzemeler olarak kullanılabilir.
Köpük alüminyumun özellikleri
Köpük alüminyum, metal alüminyum matriste dağılmış çok sayıda kabarcığa sahip bir tür gözenekli malzemedir. Özel yapısı, birçok kompakt metalin sahip olmadığı özel özelliklere sahip olduğunu belirler.
Köpük alüminyumun yapısal özellikleri
Metal iskelet bileşimi ve gözenek yapısı, farklı ihtiyaçları karşılayabilecek şekilde kontrol edilebilir.
Geniş diyafram açıklığı: 0.3-7mm;
Çeşitlendirilmiş gözenek yapısı: kapalı hücreli, açık delikli ve mikro delikli köpük alüminyum;
Yüksek ve kontrol edilebilir gözeneklilik:% 63 -% 90;
Geniş özgül yüzey alanı: 10-45cm / cm2.
Köpük alüminyumun performans özellikleri
Hafif
Yoğunluk, metal alüminyumun sadece% 10 -% 40'ıdır;
Yüksek özgül sertlik
Bükülme sertliği çeliğin 1, 5 katıdır;
Yüksek sönümleme ve şok enerjisi emilimi
Sönümleme performansı, metal alüminyumun 5-10 katıdır;
İyi ses yalıtımı (kapalı delik) ve ses emilimi (delikten)
Akustik frekans 800~4000HZ arasında olduğunda, kapalı hücreli köpük alüminyumun ses yalıtım katsayısı 0.9'dan fazladır;
Ses frekansı 125 ~ 4000HZ arasında olduğunda, delikli köpük alüminyumun ses emme katsayısı 0.8'e ulaşabilir;
Mükemmel elektromanyetik koruma performansı
Elektromanyetik dalga frekansı 2.6 ~ 18 GHz arasında olduğunda. Köpük alüminyumun elektromanyetik koruma kapasitesi 60 ~ 90dB'ye ulaşabilir;
Düşük ısı iletkenliği
Kapalı hücreli köpük alüminyumun ısıl iletkenliği mermerinkine eşdeğerdir; Delikten köpük alüminyum, iyi bir ısı dağılımına sahiptir.
Köpüğün performansı esas olarak gözenekliliğine, gözenek çapına, gözenekliliğine, gözenek tipine, spesifik yüzey alanına ve diğer gözenek yapısı parametrelerine bağlıdır. Gözenek yapısı parametreleri esas olarak hazırlama sürecine bağlıdır.
Köpük alüminyumun hazırlama teknolojisi
Köpüğün hazırlama teknolojisi, yeni malzemeler alanında bir araştırma odağı haline gelmiştir. Aşağıdakiler, köpük alüminyumun hazırlama sürecine ayrıntılı bir giriştir:
1. Katı metal sinterleme yöntemi
Bu yöntemle üretilen köpük alüminyumun çoğu açık delikli bir yapıya sahiptir. Bunun nedeni, alüminyum parçacıklarının çoğunun sinterleme yoluyla birbirine bağlanması ve alüminyumun her zaman katı tutulmasıdır.
1.1 Toz metalurjisi köpürtme yöntemi
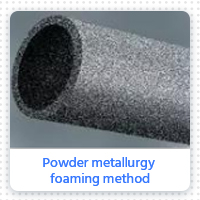
İşlem prensibi, alüminyum tozu ve köpürtücü ajan tozunu karıştırmak ve gaz geçirmez bir yapıya sahip bir preform elde etmek için sıkıştırmaktır. Preformun ısıtılması, köpürtücü ajanın ayrışmasına ve gazı serbest bırakmasına neden olacak ve preformu köpük alüminyum elde etmek için genişlemeye zorlayacaktır.
Toz metalurjisi köpürtme yönteminin proses akışı:
Özellikler: İlk olarak, diğer yöntemlerle karşılaştırıldığında, mevcut alaşım bileşimi daha kapsamlıdır, bu da köpük alüminyumun mekanik özelliklerini iyileştirmeye elverişlidir; İkincisi, karmaşık şekillere sahip bileşenleri doğrudan üretebilir.
Dezavantajı, bu yöntemin proses parametre aralığının dar olması, maliyetinin yüksek olması ve üretilen köpük alüminyumun boyutunun sınırlı olmasıdır.
1.2 Gevşek toz sinterleme
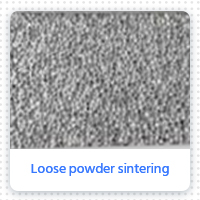
Bu yöntem çoğunlukla köpük bakır hazırlamak için kullanılır. Alüminyum tozunun yüzeyindeki yoğun oksit filmi, parçacıkların birlikte sinterlenmesini önleyeceğinden, gevşek toz sinterleme yöntemiyle köpük alüminyum hazırlamak nispeten zordur. Bu sırada, parçacıkların birbirine daha kolay yapışmasını sağlamak için oksit filmi deformasyon yoluyla yok edilebilir; Veya 595 ~ 625 ° C'de sinterleme yaparken ötektik alaşım oluşturmak için magnezyum, bakır ve diğer elementleri ekleyin.
Bu üretim yöntemi üç işlem içerir:
Özellikler: Avantajları basit süreç ve düşük maliyetlidir. Dezavantajları düşük gözeneklilik ve düşük malzeme mukavemetidir. Toz yerine elyaf kullanılırsa gözenekli malzemeler de elde edilebilir.
1.3 Bulamaç kalıplama yöntemi
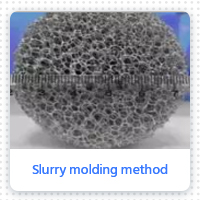
Bulamaç şekillendirme yöntemi, metal alüminyum tozu, köpürtücü ajan (hidroflorik asit, alüminyum hidroksit veya ortofosforik asit), reaksiyon katkı maddesi ve organik taşıyıcıdan oluşan bir süspansiyon oluşturmaktır. Köpük içeren bir duruma getirin ve ardından ısıtmak ve kızartmak için kalıba koyun. Daha sonra bulamaç yapışkan hale gelmeye başlar ve üretilen gazla birlikte genişlemeye başlar ve sonunda belirli bir mukavemete sahip köpük alüminyum elde eder.
Bulamaç doğrudan polimer köpüğün içine dökülürse, polimer malzeme ısıtılarak pirolize edilebilir ve açık hücreli köpük malzemesi sinterlemeden sonra da yapılabilir.
Bu üretim yöntemi şunları içerir:
Özellikler: Üretilen köpük alüminyum düşük mukavemete ve çatlaklara sahiptir.
1.4 Sinterleme çözünme yöntemi
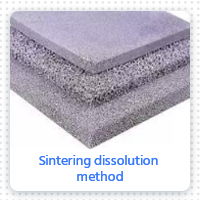
Alüminyum tozu ve tuz tozu eşit şekilde karıştırılır ve kütüklere preslenir. Presleme işlemi sırasında, tuz tozu temel olarak orijinal görünümünü korur. Alüminyum tozu plastik deformasyona uğrar ve sürekli bir ağ matrisi oluşturmak için tuz parçacıkları arasındaki boşluğu doldurur. Daha sonra, ağsı alüminyum matrisi bir bütün halinde birleştirmek için kütükler sinterlenir. Son olarak, sinterlenmiş kütük numunesi sıcak suya yerleştirilir ve kütükteki tuz parçacıkları, tek tip açık hücreli köpük alüminyum parçalar elde etmek için filtrelenir.
Süreç şunları içerir:
Özellikler: Avantajı, tuz tozunun şeklini ve parçacık boyutunu seçerek, deliklerin şeklinin ve boyutunun belirli bir aralıkta kontrol edilebilmesidir; Gözeneklilik, karışık tozun hacim oranı ile hassas bir şekilde kontrol edilebilir; Degrade köpük malzemeleri üretebilir; Net ürünler üretebilir; Ekipman basit ve seri üretimi gerçekleştirmek kolaydır.
Sınırlama, yalnızca %50~%80 gözenek aralığına sahip orta yoğunluklu köpük alüminyumun elde edilebilmesidir; Sodyum klorürün bitmiş üründe kalması kolaydır, bu da alüminyum bazın yerel korozyonuna neden olur; İşlem döngüsü uzundur.
1.5 İçi boş üç boyutlu iskelet yöntemi
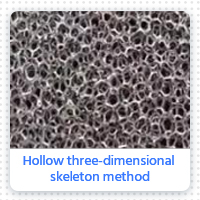
Sıvı metal, içi boş bir iskelet 3D ağ yapısına sahip bir seramiğe kalıplanır, soğutulur ve ardından iskelet çıkarılır.
Süreç şunları içerir:
Özellikler: Köpüğün gözenekliliği ayarlanabilir, işlem zahmetlidir, maliyeti biraz yüksektir ve ürün yelpazesi sınırlıdır, bu nedenle tanıtımı ve uygulaması sınırlıdır.
1.6 Fiber sinterleme
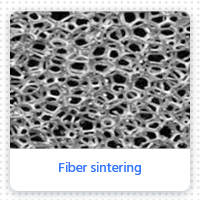
Bu yöntemin işlemi, önce mekanik çekme veya diğer yöntemlerle alüminyum tel elde etmek, daha sonra alüminyum teli bulamaç döküm veya mekanik keçe halkası ile keçe halkası haline getirmek ve ardından gerekli mukavemet ve gözenekliliği elde etmek için sinterlemektir.
Süreç aşağıdaki gibidir:
Elyaf sinterleme yönteminin avantajı, toz sinterlemeden daha yüksek gözeneklilik elde edebilmesidir. Malzemenin yapısal özellikleri maksimum gözeneklilikte tutulur. Aynı gözeneklilikte, bu yöntemle üretilen köpük alüminyumun mukavemeti ve tokluğu, toz metalurjisi yöntemiyle üretilenlerden daha yüksektir. Ancak bu yöntemin maliyeti yüksektir.
1.7 Bulamaç ıslatılmış sünger sinterleme yöntemi
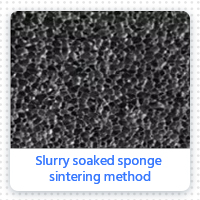
Yöntem, süngerimsi organik maddeleri istenen şekle sahip organik öncüler haline getirmek ve daha sonra nüfuz etmek için işlenecek metal alüminyum tozunu içeren bulamacı kullanmaktır (süspansiyonun taşıyıcısı su ve organik sıvıdır). Islatılmış organik öncü, çözücüyü uzaklaştırmak için kurutulur, sinterlenir ve yüksek gözenekliliğe ve üç boyutlu yapıya sahip köpük alüminyum elde etmek için soğutulur.
Süreç akışı kabaca aşağıdaki gibidir:
Özellikler: Esas olarak organik öncülerin seçimi ve ön işleminden, bulamacın bileşiminden, katkı maddelerinin seçiminden, sinterleme sıcaklığından ve diğer faktörlerden etkilenir.
2. Sıvı metalin katılaşması
Bu yöntem, sıvı alüminyumdan köpük yapısı üretmektir. Alüminyum sıvı ile doğrudan köpürtülebilir; Gözenekli malzemeler, köpük malzemelerin veya sıkıca paketlenmiş gözenek oluşturucu maddelerin dökümüyle de elde edilebilir.
2.1 Doğrudan üfleme köpürme yöntemi
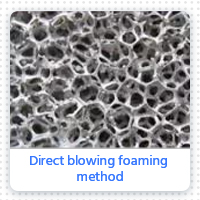
İlk olarak, erimiş metale SiC, Al2O3 vb. ekleyin ve eriyik viskozitesini iyileştirmek için eşit şekilde dağıtın. Ardından eriyiğin dibine gaz (nitrojen, inert gaz vb.) üfleyin. Sıvı metalde çok sayıda gözenek oluşur ve daha sonra soğutulur ve katılaşır.
Özellikler: ürünlerin sürekli hazırlanması gerçekleştirilebilir; Ekipman için basit gereksinimler; Ürünün gözenekliliği kontrol edilebilir; Düşük maliyetli.
2.2 Köpürtücü ajan köpürtme yöntemi
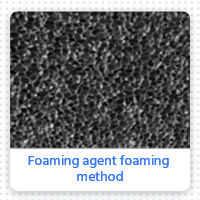
Alüminyum eriyiğin içine köpürtücü madde ekleyin ve eşit şekilde karıştırın. Köpürtücü ajanın gaz üretmek üzere ayrışmasını sağlamak için ısıtın. Gaz genişler ve köpürür. Soğuduktan sonra köpük metal elde edilir. Kullanılan köpürtücü ajan genellikle TiH2 veya ZrH2 gibi metal hidrittir.
Özellikler: basit ekipman gereksinimleri, düşük maliyet ve sürekli ürün hazırlığı. Kısa köpürme zaman aralığı, köpürme sıcaklığının zor kontrolü, eşit olmayan kabarcık dağılımı, zayıf ürün tekrarlanabilirliği vb.
2.3 Sızıntı dökümü
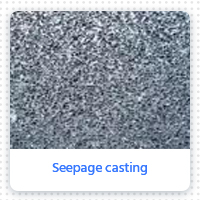
Süzülme dökümü, çıkarılabilir parçacıkları (NaCl gibi) kalıba istiflemek, bunları kütüklere bastırmak, ön ısıtmadan sonra metal dökmek ve ardından birbirine bağlı deliklere sahip bir delikli köpük yapısı hazırlamak için parçacıkları çıkarmaktır.
Süreç prensibi:
Vakum Sızıntı Yöntemi Cihazının Şematik Diyagramı
Özellikler: Hazırlama işlemi, kontrol edilebilir gözenek çapı parametrelerine, yüksek delik oranına, geniş spesifik yüzey alanına, düşük maliyete sahiptir ve büyük ölçekli endüstriyel üretim için uygundur. Dezavantajı, sıvı metalin yüksek yüzey gerilimi nedeniyle, parçacıkların tamamen ıslanamaması, dolayısıyla parçacıklar arasındaki boşluğun tamamen doldurulamamasıdır.
2.4 Yatırım dökümü
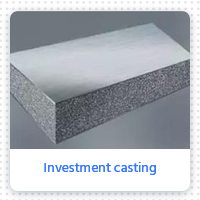
Hassas döküm yöntemi, refrakterin boşluğunu doldurmak için kalıplanmış polimer köpük malzemeyi sıvı refrakterin içine daldırmaktır. Refrakter sertleştikten sonra, ısıtma, orijinal köpük malzemenin şekli ile üç boyutlu bir çerçeve oluşturmak için köpük malzemeyi buharlaştıracak ve ayrıştıracaktır. Erimiş alüminyumu döküm kalıbına dökün, katılaşmadan sonra refrakteri çıkarın ve ardından deliklerden üç boyutlu ağ ile köpük alüminyum elde edin.
Süreç prensibinin şematik diyagramı:
Hassas döküm ile hazırlanan gözenekli malzemelerin şematik diyagramı
Avantajları: çeşitli köpük metaller hazırlanabilir; Açılış yapısı, iyi üretim tekrarlanabilirliği ve nispeten kararlı yoğunluk.
Dezavantajları: düşük çıktı; yüksek fiyat.
2.5 Katı-gaz ötektik katılaşma
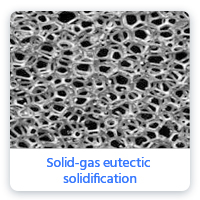
Birçok metal sıvı, gazlarla (hidrojen gibi) ötektik sistemler oluşturabilir. Bu metaller yüksek basınçlı bir hidrojen atmosferinde eritilirse, aşırı doymuş hidrojen içeren tek tip bir eriyik elde edilebilir. Sonraki soğutma ve katılaşma işleminde, eriyik ötektik dönüşüme uğrayacak ve katı ve gaz fazlarına ayrışacaktır. Yönlü katılaşma sırasında, hidrojenin katı faz ve sıvı fazdaki çözünürlüğü büyük ölçüde farklılık gösterdiğinden, aşırı doymuş hidrojen, kabarcıklar oluşturmak için katı fazdan ayrılacak ve böylece gerekli köpük alüminyumu elde edecektir.
Süreç Prensibinin Şematik Diyagramı:
Gözenekli Malzemelerin Hazırlanması için Katı Gaz Ötektik Katılaşma Sürecinin Şematik Diyagramı
Özellikler: İzotropik ve anizotropik gözenek şekillerine sahip yüksek gözenekli köpük alüminyum, soğutma koşullarının (basınç, soğutma hızı, ısı yayma yönü) hassas bir şekilde kontrol edilmesiyle elde edilebilir.
2.6 Top besleme yöntemi
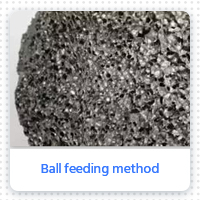
Bilye malzemesi ekleme yöntemi, alüminyum alaşım eriyiğine parçacıklar veya içi boş bilyeler eklemek ve karıştırmayı güçlendirmektir. Ve alüminyum alaşımı ve parçacıklarının kompozitini elde etmek için eriyik hala bağıl akıştayken döküm. Daha sonra alüminyum alaşım kolektifindeki çözünür parçacıklar çözülür ve uzaklaştırılır ve son olarak bağlı gözenekli bir köpük alüminyum elde edilir.
Süreç akışı kabaca aşağıdaki gibidir:
Özellikler: Sıvı metalin yüzey gerilimi yüksektir ve parçacıklar veya içi boş toplar tamamen ıslatılamaz, bu nedenle parçacıklar arasındaki boşluklar tamamen doldurulamaz. Elde edilen köpük alüminyumun yapısal sürekliliği zayıftır.
3. Metal biriktirme
3.1 Elektrodepozisyon
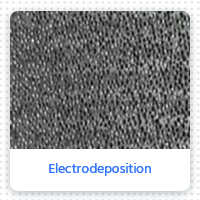
Prensip, köpük alüminyumun, katot olarak ön işleme tabi tutulmuş köpük plastik ve anot olarak endüstriyel saf alüminyum levha ile alkil alüminyum çözeltisi içinde elektrolizle kaplanmasıdır.
Elektrodepozisyon yönteminin proses akışı:
Özellikler: kolay kontrol edilebilir gözenek yapısı, küçük gözenek boyutu, düzgün gözenek boyutu, yüksek gözeneklilik ve ısı yalıtımı ve sönümleme özellikleri, döküm yöntemiyle üretilen köpük alüminyumdan daha iyidir. Bununla birlikte, bu yöntem uzun bir süreye, karmaşık bir çalışmaya, biraz yüksek maliyete ve sınırlı ürün kalınlığına sahiptir, bu nedenle popülerleşmesi ve uygulaması sınırlıdır.
3.2 Buhar fazı buharlaşma biriktirme yöntemi
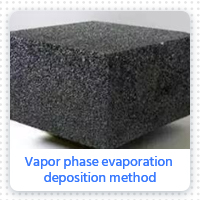
Bu yöntem, metal alüminyumu yüksek inert bir atmosferde (102~104Pa) yavaşça buharlaştırmaktır. Buharlaşan metal atomları, inert gaz molekülleri ile çarpışır ve saçılır, hızla kinetik enerji kaybeder. Bu işlem makroskopik görünümde metal buharı sıcaklığı düştükçe gösterilir. Daha sonra buharlaşan metal atomları, substrata ulaşmadan önce atomik kümeler oluşturmak için birbirleriyle birleşir, böylece buharlaşma işleminde "metal dumanı" görülebilir. Bu kümeler soğumaya ve inert gazla alt tabaka üzerinde birikmeye devam eder. Düşük sıcaklıktaki atomların göç etmesi veya yayılması zor olduğundan, "metal duman" parçacıkları içi boş bir köpük yapısı oluşturmak için gevşek bir şekilde istiflenir.
Süreç Prensibinin Şematik Diyagramı:
Buhar Fazı Evaporatif Biriktirme İşleminin Şematik Diyagramı
Özellikler: Metal köpüğün oluşumu, metal malzemeler, ısıtma gücü, inert gaz basıncı, buharlaşma kaynağı ısıtıcısının tipi ve alt tabakaya olan uzaklığı ve alt tabaka malzemeleri gibi birçok faktörden etkilenir. Isıtma gücü, inert gaz basıncı ve inert gaz debisi en önemli kontrol parametreleridir.
3.3 Sıçrama biriktirme
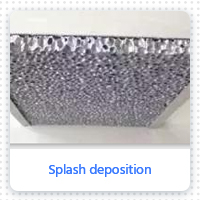
Sıçrama biriktirme, püskürtme teknolojisini kullanarak tozu inert gazla alüminyum alaşımlı metal üzerine eşit şekilde püskürtmektir. Daha sonra metalin erime noktasına kadar ısıtılır, böylece metale eklenen gaz genişler ve düzgün dağılmış ve yoğun delikler oluşturur. Soğuduktan sonra yoğun ağa sahip köpük alüminyum ürünlerden yapılmıştır.
Süreç prensibinin şematik diyagramı:
Sıçrama biriktirmenin şematik diyagramı
Özellikler: Biriktirme sırasında inert gazın kısmi basıncı kontrol edilerek, elde edilen ürünün gözeneklerinin hacim oranı kontrol edilebilir.
3.4 Erimiş tuz galvanik kaplama
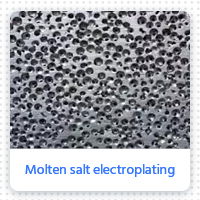
Köpük alüminyum, katot olarak köpüklü plastik ve anot olarak alüminyum levha ile erimiş tuz içinde elektrodepozisyon ile hazırlanır.
Süreç prensibinin şematik diyagramı:
Elektrokaplama İşlemi Prensibinin Şematik Diyagramı
Özellikler: köpük alüminyum yüksek gözenekliliğe ve hatta gözeneklere sahiptir.
4. Diğerleri
Aşağıdaki yöntemler esas olarak bilimsel araştırma veya küçük seri deneme üretimi için kullanılır ve endüstriyel üretimde yaygın olarak kullanılmaz.
4.1 İkincil köpürme yöntemi
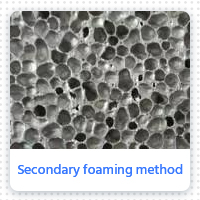
İkincil köpürtme yöntemi, toz metalurjisi köpürtme yöntemi ve eriyik köpürtme yönteminin avantajlarını birleştiren bir köpük alüminyum hazırlama yöntemidir. Teknik işlem, alüminyum eriyiğine viskozite arttırıcı ajan (Ca, Al2O3, vb.) eklemek ve eşit şekilde karıştırmaktır. Uygun sıcaklık ve viskozite koşulları altında köpürtücü ajan (ön işleme tabi tutulmuş TiH2) ekleyin. Düzgün bir şekilde dağılır ve eriyik, köpürme öncüsü elde etmek için TiH2 ayrışmadan önce hızlı soğutma ve katılaşma için kalıba dökülür. Köpürme öncüsü belirli bir sıcaklığa ısıtıldığında, öncüdeki TiH2 ayrışmaya ve köpürmeye başlar ve son olarak köpük alüminyum hazırlanır.
4.2 Metal içi boş bilye yöntemi
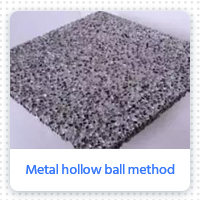
Yöntem, metal içi boş küreleri sinterleme yoluyla birbirine bağlayarak gözenekli bir yapı oluşturmaktır. Metal içi boş küreler, polimer kürelerin yüzeyinde bir metal tabakasının kimyasal sentezi ve elektrodepozisyonu ile elde edilebilir ve daha sonra polimer küreler çıkarılır.
Köpük alüminyumun birçok hazırlama işlemi vardır ve her yöntemin kendine göre avantajları ve dezavantajları vardır. Pratik üretimde, eriyik köpürtme yöntemi, süzülme döküm yöntemi, toz metalurjisi köpürtme yöntemi ve elektrokimyasal yöntem yaygın olarak kullanılmaktadır. Diğer işlemler esas olarak bilimsel araştırma veya küçük seri deneme üretimi için kullanılır.
Köpük alüminyum uygulaması
Arabalarda köpük alüminyum uygulaması
Otomotiv endüstrisinde köpük alüminyum uygulaması, aşağıdaki şekilde gösterildiği gibi, esas olarak hafif yapı, enerji emme yapısı ve sönümleyici ısı transfer yapısını içerir. Üç daire farklı uygulama alanlarını temsil eder ve dairenin dışındaki karakterler, üç uygulama alanına karşılık gelen köpük alüminyumun avantajlarını ve özelliklerini gösterir. İki dairenin üst üste binen kısmı, köpük alüminyumun çift işlevli entegrasyonunu temsil eder. İdeal uygulama, üç daire tesadüfü ile temsil edilen çok işlevli entegrasyondur.
Bu köpük alüminyum, "sıvı metale gaz üfleme" yöntemi ile üretilir. Bu işlemde, matris malzemesi (dövme alüminyum veya dökme alüminyum alaşımı) genellikle geleneksel döküm ekipmanı ile eritilir ve daha sonra% 10 ~% 30 (hacim) viskozite arttırıcı ajan (SiC veya Al2O3 partikülleri) eklenir ve viskozite arttırıcı ajan bir karıştırıcıda karıştırılarak eşit olarak dağıtılır.
Karışık eriyiği hunili bir kaba dökün ve dağılmış küçük kabarcıklar oluşturmak için gazı küçük bir ağızlıktan karıştırıcıya enjekte edin. Kabarcık boyutu, gaz akış hızı, karıştırıcı tasarımı (nozul sayısı ve boyutu) ve karıştırma hızı ayarlanarak kontrol edilebilir. Kabarcıklar yüzeye çıkar ve toplanır.
Kabarcıklarla çevrili seramik parçacıklar, gözenek duvarını stabilize edebilir ve kabarcıkların uygun arayüzlerle birleşmesini geciktirebilir; Aynı zamanda eriyik viskozitesini artırabilir ve kabarcıkların yükselme hızını yavaşlatabilir. Sıvı metal köpük, konveyör bant boyunca taşınır ve kapalı hücreli köpük elde etmek için aynı anda soğutulur ve katılaştırılır.
Köpüğün bağıl yoğunluğu esas olarak karıştırma hızı, gaz akış hızı, eriyik ve katılaşma koşullarındaki partikül sayısı gibi proses parametrelerinden etkilenir. Otomobil ürünlerinin dolgu maddesi olarak köpük alüminyum, Alman GAOFISHER otomobillerinde yaygın olarak kullanılmaktadır.
Kalko köpük alüminyum mükemmel performansa sahiptir. Chalco köpük alüminyumdan yapılmış motor kaputu, yolcuları etkili bir şekilde koruyabilen 11m/s kafa şeklinin etkisine dayanabilir. Chalco köpük alüminyum dolgulu darbe enerjisi emme kutusu, 5m / s'nin etkisine dayanabilir.
Chalco köpük alüminyum ile doldurulmuş A ve B kolonlarının eğilme mukavemeti, içi boş kolonların üç katıdır. Kalko köpük alüminyum, karmaşık nervürlü yapıyı dökebilir, böylece kalıp tasarımını ve işleme yöntemlerini basitleştirir.
Chalco köpük alüminyumun ana performans parametreleri:
bağıl yoğunluk ρ / ρS = 0.02GPa ~ 0.2GPa,
Young modülü E=0.02GPa~210GPa,
kayma modülü G=0.01GPa~1.0GPa,
eğilme modülü Ef=0.03GPa~3.3GPa,
Poisson oranı υ= 0.31~0.34,
Basınç dayanımı σ C = 0.04MPa ~ 7.0MPa,
çekme mukavemeti σ T = 0105MPa ~ 8.5MPa,
termal iletkenlik λ= 0.3W/(m・K)~10W/(m・K).
Köpük alüminyum sandviç yapıdan yapılmış otomobil parçalarının arabalara uygulanması şekilde gösterilmiştir.
Şekilde tanımlanan uygulamalara ek olarak, köpük alüminyum, ön uzunlamasına kiriş, arka boyuna kiriş, tampon ve şasi arasındaki darbe enerjisi absorpsiyon yapısında, iç cihazlar ve dekoratif parçalar, çamurluk, üst kapak plakası, üst kapak uzunlamasına kirişi, arka diyafram, biyel kolu, piston, alt kontrol kolu, şanzıman dişlisi, silindir bloğu, fren silindiri pistonu, susturucu vb.
Yüksek hızlı demiryolu ve taşımacılıkta köpük alüminyum uygulaması
Yüksek hızlı trenin çarpışma önleyici yapısı
Etkili çarpışma önleyici yapıya sahip olmayan trenler nedeniyle yüksek hızlı trenlerin çarpışma tehlikesi ciddi güvenlik gizlidir. Alüminyum tüp enerji emici kolon dolgulu alüminyum köpük kullanarak aşağıda gösterilen lokomotif kafası çarpışma önleyici yapı, aşağıda gösterilen vagonlar arasındaki çarpışma önleyici yapı, tren hızı 70Km'nin altında olduğunda, çarpışma önleyici yapı tüm darbe enerjisini emebilir, böylece tren yolcuların can güvenliğini sağlamak için tampon ve duracaktır.
Yüksek hızlı tren hattında alüminyum köpükten yapılmış ses bariyeri
Şu anda yüksek hızlı demiryolu hattının ses bariyeri sahte bir üründür, ses emici kutusu 140 mm kalınlığındadır, 100 ~ 200Hz düşük frekanslı gürültü frekansı için uygundur, ses emme ve gürültü azaltma işlevine sahip değildir, ancak Yüksek hızlı Demiryolu hattı gürültüsü yüksek frekanstır (1000 ~ 2000Hz frekansı). Alüminyum köpük ses kutusu, 10 ~ 15 mm kalınlığında köpük alüminyum ses emme levhasından ve ortada katlanmış tip galvanizli çelik bölme levhasından yapılmıştır, boşluğu 0 ~ 30 mm'dir. Arka panel, aşağıda gösterildiği gibi 1 mm kalınlığında galvanizli levhadan yapılmıştır. 500Hz ~ 2000Hz Yüksek Hızlı Ray gürültüsünün frekansını uyarlamak için bu tür bir ses bariyeri, 20 dB'den fazla gürültü azaltılabilir.
Alüminyum köpükten yapılmış güvenlik okul otobüsü
Güvenlik okul otobüsü çarpışma önleyici kirişten önce ve sonra, yüzeyi 1 ~ 2 mm kalınlığında çelik levhadan yapılmış, alüminyum köpükle doldurulmuş alüminyum boru absorpsiyon kolonu kullanılarak yapılır. Çarpışma önleyici ışın, okul otobüsü çarpıştığında darbe enerjisinin çoğunu emebilir. Gövde dik kolon ve çapraz kiriş, alüminyum köpük ile doldurulmuş kare çelik borudan yapılmıştır, devrilme önleme kabiliyeti iki katına çıkacaktır.
Otoyolda alüminyum köpük ses bariyeri
Alüminyum köpük ses bariyeri birçok şehirde inşa edilmiştir, alüminyum köpük emme levhası
800mmx 2000mm, boşluğu 70mm, gürültü 20dB azaltılabilir.
Askeri sanayide köpük alüminyum uygulaması
Hafif füze rögar kapağı
Betonarme malzemelerden yapılmış füze rögar kapağı, ağırlığı 600 tondan fazla, çok ağır, açılma ve kapanma zorluğuna ulaşıyor. Zırh plakası ve alüminyum köpükten yapılmış yeni füze rögar kapağı, patlamaya karşı dayanıklılığı 10000Mpa'dan fazla, anti zırh delme kabiliyetini orijinal kapaktan daha fazla yapabilir ve ağırlığı 1/6'ya düşürülebilir.
Alüminyum köpükten yapılmış savaş zamanı hızlı montajlı geniş açıklıklı köprü
Savaş zamanında, zırhlı kuvvetlerin nehrin karşısına geçmek ve hendek boyunca hızlı montaj destek köprüsüne ihtiyacı vardır. Yurtiçinde ve yurtdışında hızlı montaj destek köprüsü çelikten imal edilmiş olup, maksimum uzunluğu 53 metredir. 70 metre uzunluğundaki köprü, aşağıda gösterildiği gibi alüminyum köpük malzemelerden imal edilebilir.
Hafif patlama kapısı
Mevcut patlamaya dayanıklı kapı, betonarme ve çelik levha yapısını benimser, toplam kalınlığı 300 ~ 400 mm'dir. Patlama kapısının maksimum vuruntu önleme kabiliyeti yaklaşık 3Mpa'dır, ancak ağırlığı 20 ~ 30 tondur, bu nedenle açma ve kapama zorluğu. Alüminyum köpükten yapılmış hafif patlamaya dayanıklı kapı yapısı, paneli 5 mm kalınlığında karbon çelik levhadan yapılmıştır ve ara alüminyum köpük yaklaşık 100 mm kalınlığındadır. Bu tür 870 patlama kapısının vuruntu önleme özelliği 1000Mpa'dan fazla ulaşır, ancak ağırlığı birkaç tona düşer.
Uçak gemisinin alüminyum köpüklü sandviç uçuş güvertesi
Uçak, uçak gemisi uçuş güvertesine indiğinde, geri tepme etkisi nedeniyle, kablo eki tarafından kolayca tutuklanamaz, bu da bazı uçakların güvertede duramamasına neden olur. Alüminyum köpük sandviç uçuş güvertesi kullanılarak, uçak sıçrama yüksekliği% 50'den fazla azaltılır, bu da uçağın düzgün kaymasını sağlar ve kablo eki ile tutuklanma şansını artırır. Ek olarak, patlama direnci ve füze karşıtı savaş yeteneği önemli ölçüde geliştirilecektir.
Alüminyum köpükten yapılmış ağır ekipman havadan tampon tablası
Rus havadaki 20 tonluk ekipman, 4 metre yüksekliğinde büyük balonu benimsiyor, iniş sırasında sabit değil. Doldurma köpüğü alüminyum alüminyum boru enerji emici kolon kullanılarak, ağır ekipman havadaki tampon pedi, yüksekliği yaklaşık 500 mm'dir, düzgün iniş ve güvenlik ekipmanı sağlamak için 20 ton ekipman düşürülebilir.