Qu’est-ce que l’anodisation de l’aluminium ?
Le processus d’anodisation de l’aluminium et des alliages d’aluminium est un processus qui utilise des produits en aluminium ou en alliage d’aluminium comme anodes, les place dans une solution d’électrolyte pour l’électrification, puis utilise l’électrolyse pour former un film d’oxyde d’aluminium sur leurs surfaces.
Après le traitement d’anodisation, la surface de l’aluminium peut générer de plusieurs microns à des centaines de microns de film anodisé. Par rapport au film d’oxyde naturel de l’alliage d’aluminium, sa résistance à la corrosion, sa résistance à l’usure et ses propriétés décoratives ont été considérablement améliorées. Soumission rapide
Pourquoi l’anodisation de l’aluminium est-elle essentielle ?
Afin de surmonter les défauts de dureté de surface et de résistance à l’usure des alliages d’aluminium, d’élargir le champ d’application et de prolonger la durée de vie, la technologie de traitement de surface est indispensable dans l’utilisation des alliages d’aluminium, et l’oxydation anodique est la technologie la plus largement utilisée et la plus réussie.
Les films d’aluminium en métal anodisé peuvent modifier l’état et les propriétés de surface, tels que la coloration de surface, l’amélioration de la résistance à la corrosion, l’amélioration de la résistance à l’usure et de la dureté et la protection des surfaces métalliques. En raison de ces propriétés particulières, il a été largement utilisé dans tous les aspects.
Quel est le principe de l’anodisation de l’aluminium ?
Le principe de l’anodisation de l’aluminium est essentiellement le principe de l’électrolyse de l’eau.
L’aluminium et ses alliages sont placés dans l’électrolyte correspondant (tel que l’acide sulfurique, l’acide chromique, l’acide oxalique, etc.) comme anodes pour l’électrolyse dans des conditions spécifiques et sous l’action du courant imposé. Aluminiumou son alliage de l’anode est anodisé, et une fine couche d’anodisation de l’aluminium se forme à la surface, avec une épaisseur de 5 à 30 microns et un film anodisé dur de 25 à 150 microns. Soumission rapide
L’aluminium anodisé ou son alliage a amélioré sa dureté et sa résistance à l’usure, qui peut atteindre 250 ~ 500 kg / mm2. Il a une bonne résistance à la chaleur, le point de fusion du film anodisé dur est jusqu’à 2320K. Il a une excellente isolation et la tension de résistance à la panne est jusqu’à 2000V. Il a amélioré la résistance à la corrosion et ne se corrodera pas après des milliers d’heures dans le brouillard salin ω= 0, 03 NaCl.
Il y a beaucoup de micropores dans le film anodisant mince, qui peut absorber divers lubrifiants, et convient à la fabrication de cylindres de moteur ou d’autres pièces résistantes à l’usure. La membrane a une forte capacité d’adsorption microporeuse et peut être colorée en diverses belles couleurs. Les métaux non ferreux ou leurs alliages (tels que l’aluminium, le magnésium et leurs alliages) peuvent être anodisés. Cette méthode est largement utilisée dans les pièces mécaniques, les pièces d’avions et d’automobiles, les instruments de précision et les équipements radio, les nécessités quotidiennes et la décoration architecturale.
Le processus d’anodisation de l’aluminium est divisé en trois types.
Type I - Anodisation à l’acide chromique
En utilisant de l’acide chromique comme électrolyte, il produit le revêtement le plus fin, avec une épaisseur d’environ 2, 5 micromètres (0, 0001 pouce). Bien que le revêtement soit mince, sa résistance à la corrosion est comparable à celle d’autres procédés. Le revêtement est généralement plus foncé et ne peut pas être coloré.
Type II - Anodisation à l’acide sulfurique
En utilisant de l’acide sulfurique dilué comme électrolyte, c’est le procédé le plus couramment utilisé. L’épaisseur du revêtement varie de 5, 1 à 30, 5 micromètres (0, 0002-0, 0012 pouce). Suivant généralement les spécifications de l’industrie telles que MIL-A-8625Type II, Classe 1 (non teint) ou Classe 2 (teint). Ce type de revêtement est plus dur que le type I et est facile à teindre.
Type III - Anodisation à couche dure
En utilisant de l’acide sulfurique comme électrolyte, il produit un revêtement plus épais par rapport au type II, allant généralement de 12, 7 à 50, 8 micromètres (0, 0005 à 0, 002 pouce). Ce type de revêtement est plus dur que l’acier à outils et est utilisé dans des applications nécessitant des niveaux élevés de résistance à l’usure. Soumission rapide
Bien qu’il ne soit pas coloré, le traitement de surface assombrira la surface de la pièce, avec des couleurs allant du gris clair au gris foncé ou au brun.
Quelles sont les couleurs disponibles en aluminium anodisé ?
L’aluminium anodisé est disponible en différentes couleurs, notamment le noir, le rouge, le bleu, le vert, le gris, le marron et l’or. Sa nature poreuse lui permet d’absorber efficacement les colorants, et l’étanchéité ultérieure aide à prévenir la perte de couleur pendant l’utilisation.
Bien que l’aluminium anodisé puisse être teint dans presque toutes les couleurs, une correspondance précise des couleurs est souvent peu pratique. Attendez-vous à un certain degré de variation de couleur dans la cohérence des couleurs des pièces anodisées. Soumission rapide
Si les pièces subissent un sablage avant l’anodisation, la surface plus rugueuse résultante produira une finition mate.
Quels types d’aluminium peuvent être anodisés ?
Tous les types d’aluminium ne peuvent pas être anodisés efficacement.
Série 5XXX
Les alliages de la série 5XXX (tels que le 5052) produisent une couche d’oxyde solide et transparente lors de l’anodisation. Les produits courants de cette série comprennent ceux utilisés dans les applications de construction, de soudage et d’éclairage. Soumission rapide
Série 6XXX
Les alliages de la série 6XXX sont d’excellents candidats pour l’anodisation. La couche d’oxyde produite après l’anodisation est transparente et offre une excellente protection.
En raison de leurs propriétés mécaniques exceptionnelles et de leur facilité d’anodisation, les alliages de la série 6XXX, y compris 6061 (bar), 6061 (tube), 6061 (feuille), 6063 (bar) et 6063 (tube), sont couramment utilisés dans la construction et les applications structurelles. Soumission rapide
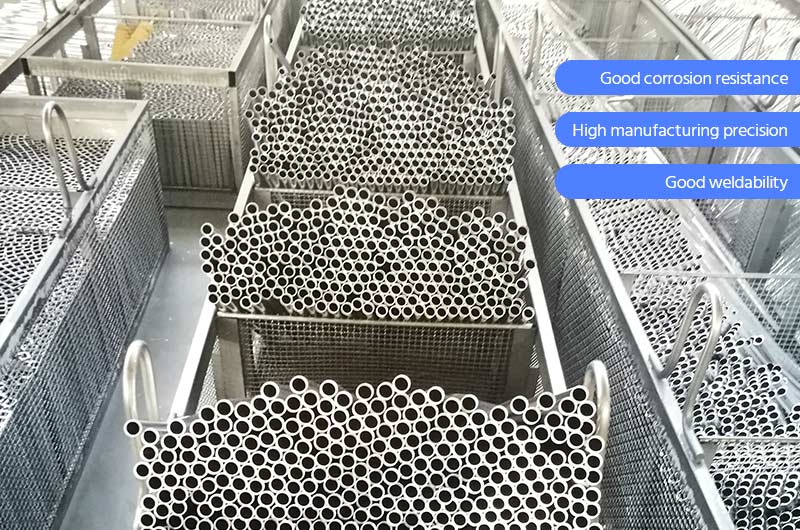
6061-tube-aluminium
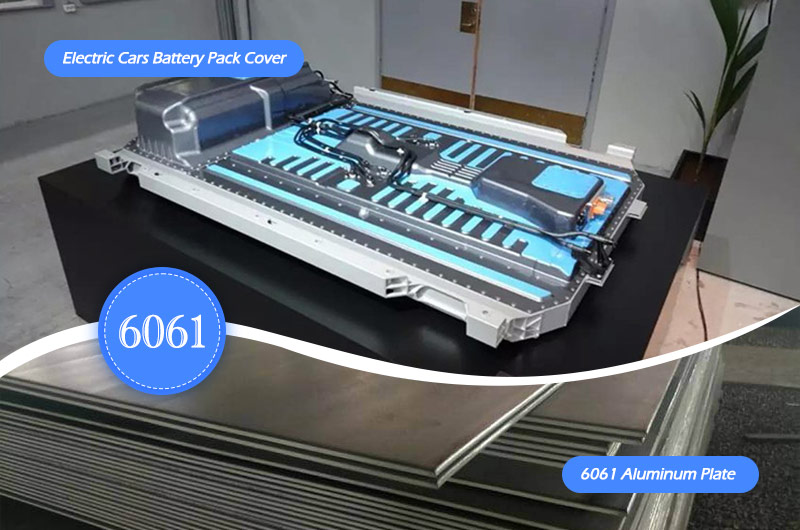
6061-plaque-aluminium
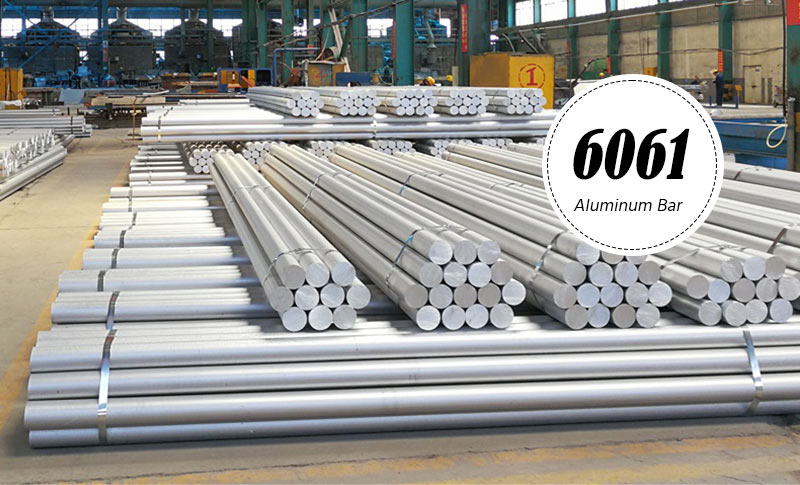
6061-barre en aluminium
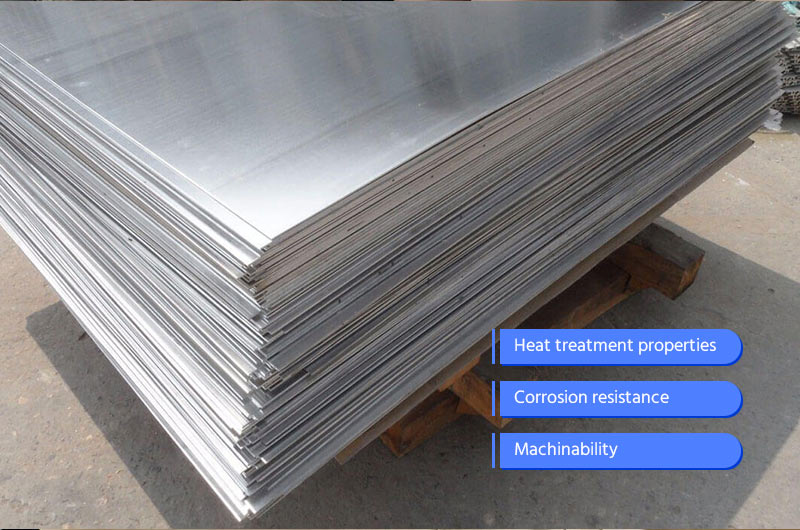
6063-tôle d’aluminium
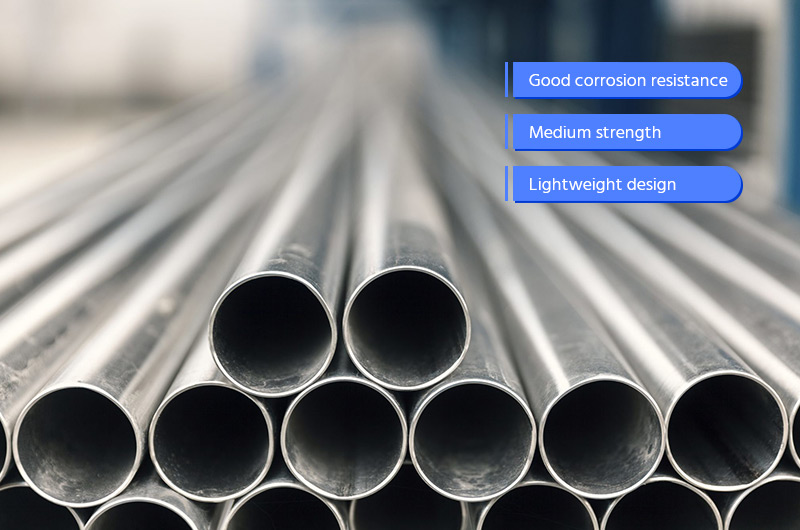
6063-tube-aluminium
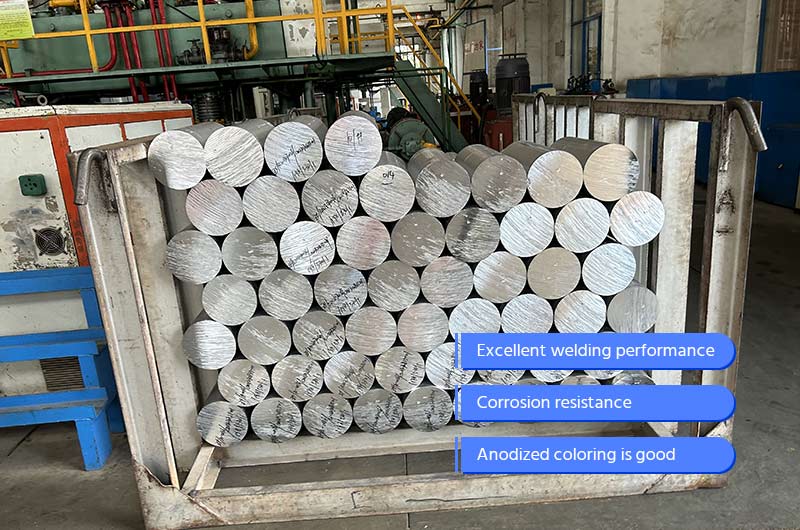
6063-tige-aluminium
Série 7XXX
Les alliages d’aluminium de la série 7XXX contiennent principalement du zinc comme principal élément d’alliage. Ils sont parfaitement adaptés au processus d’anodisation, produisant une couche d’oxyde transparente qui offre une excellente protection. Ils sont couramment utilisés dans les applications automobiles.
IMPORTANT : Même dans les séries 5XXX et 6XXX recommandées, tous les alliages ne conviennent pas à l’anodisation. Certains peuvent ne pas produire des résultats optimaux. Il est préférable de consulter le fabricant ou l’expert en finition métallique pour déterminer quel alliage d’aluminium est le mieux adapté à vos besoins spécifiques en matière d’anodisation.
Produits anodisés populaires
L’aluminium anodisé est un matériau vraiment polyvalent qui peut être utilisé pour créer une grande variété de produits. Sa durabilité, sa résistance à la corrosion et son aspect attrayant en font un choix populaire pour de nombreuses applications différentes.
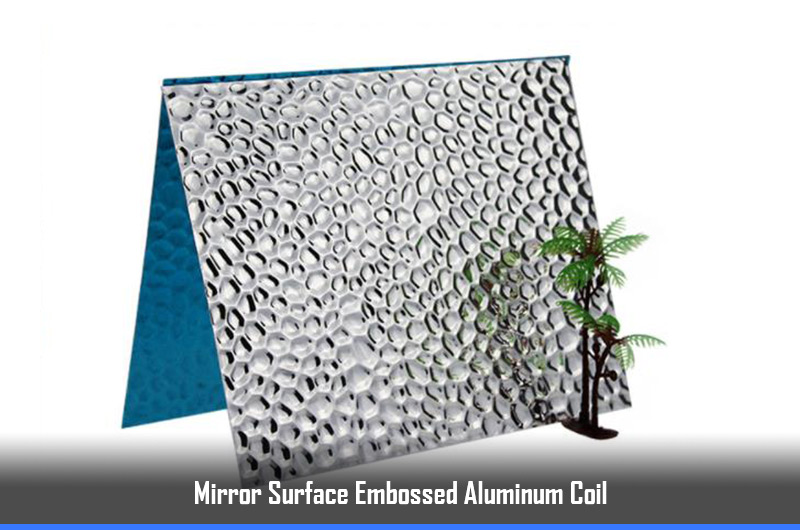
bobine en stuc gaufré
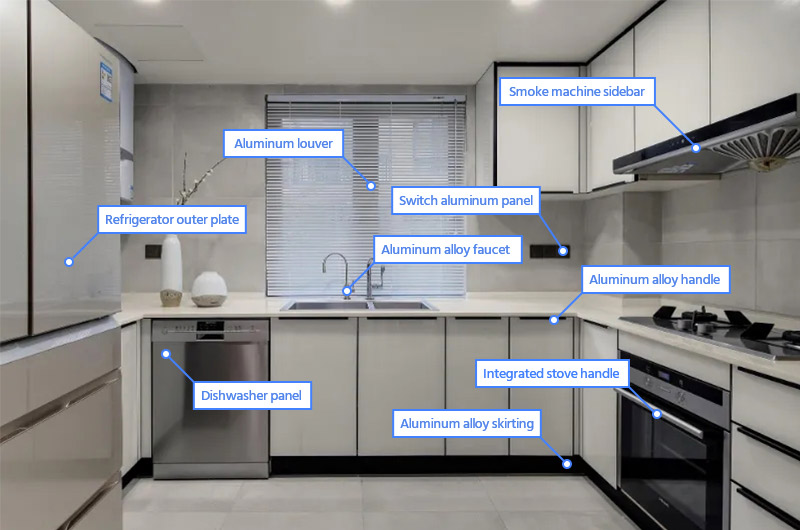
aluminium dans la cuisine
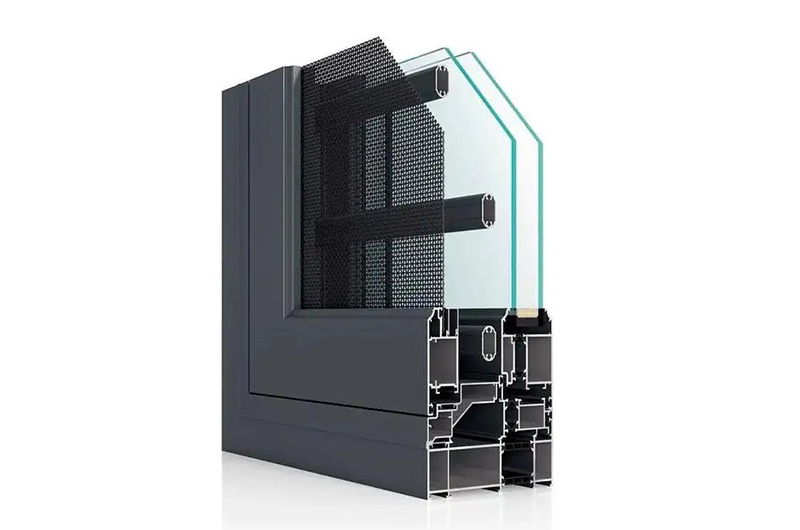
porte-fenêtre-profilé en aluminium
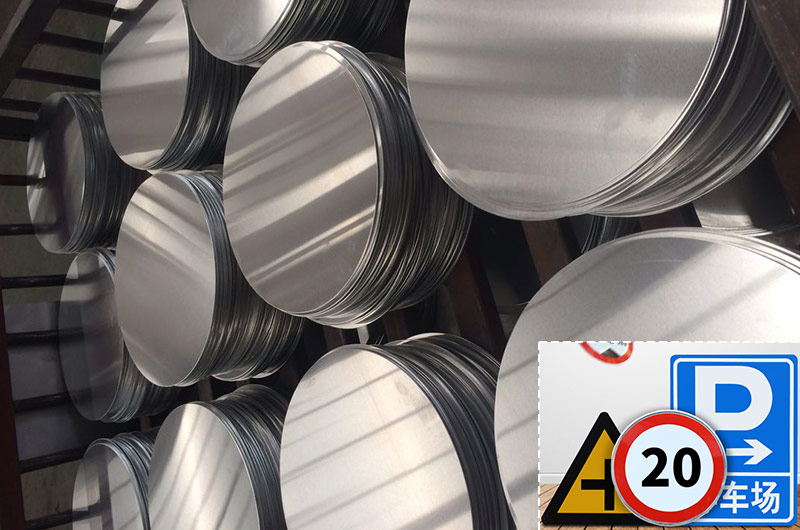
Panneau en aluminium vierge
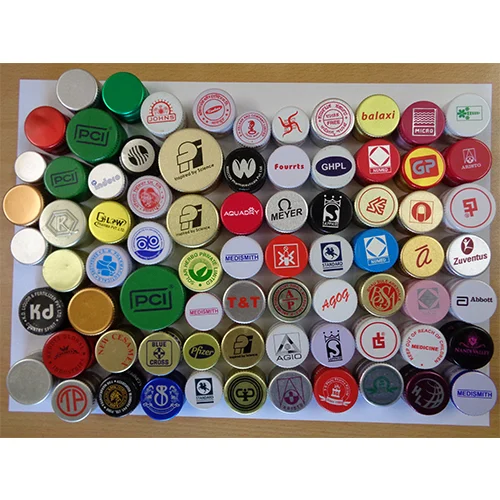
8011
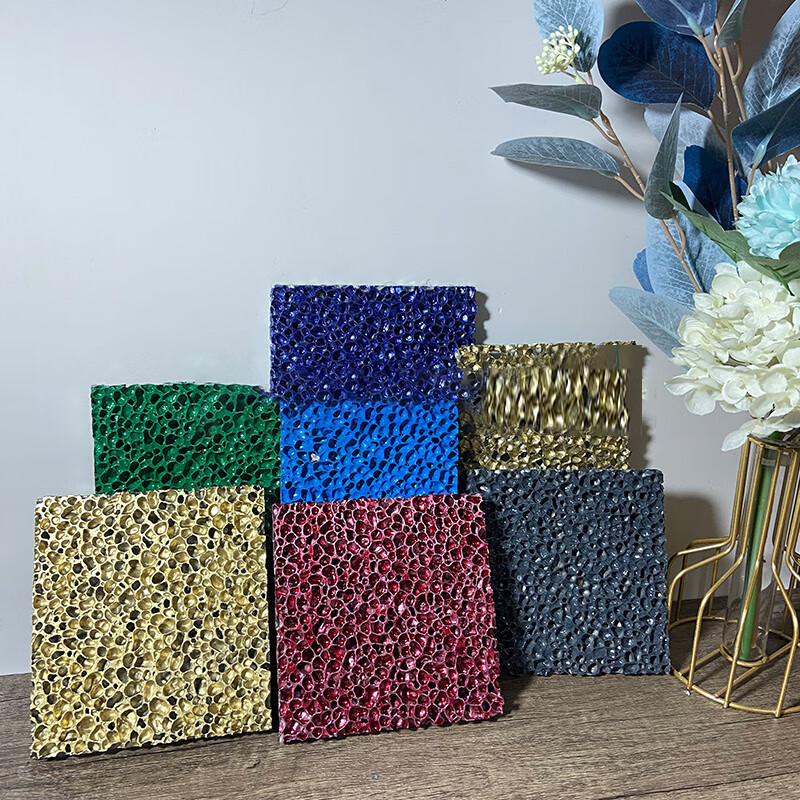
plaque de mousse poreuse
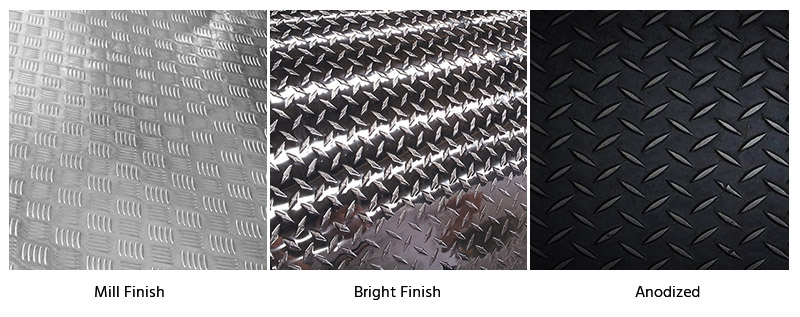
plaque à carreaux de bande de roulement
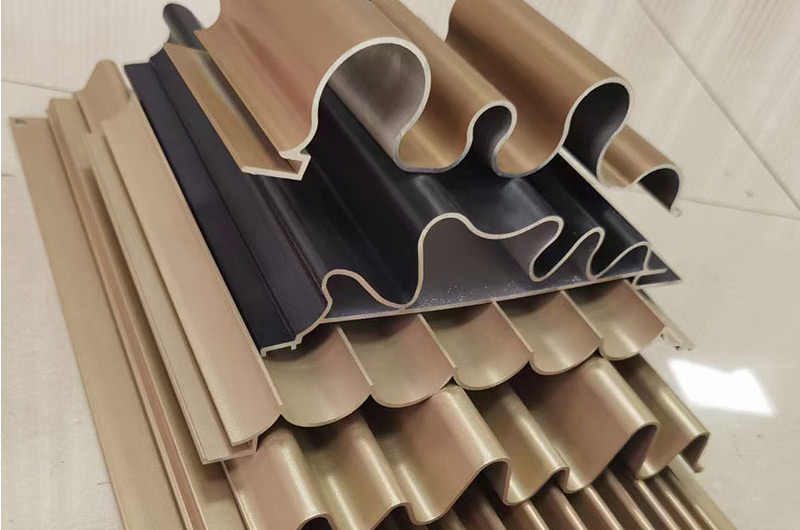
en tôle ondulée
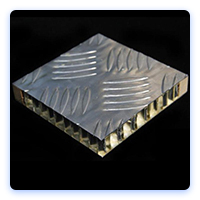
aluminium-nid d’abeille
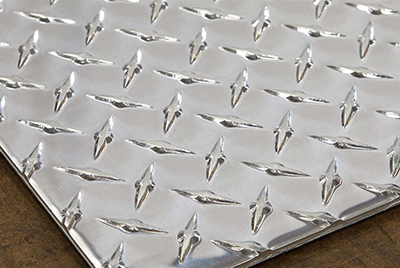
plaque diamantée
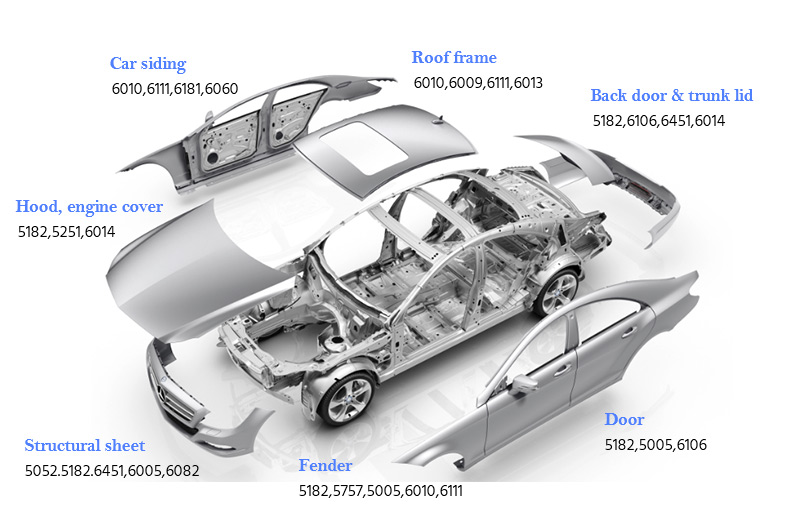
auto-carrosserie-panneau-aluminium
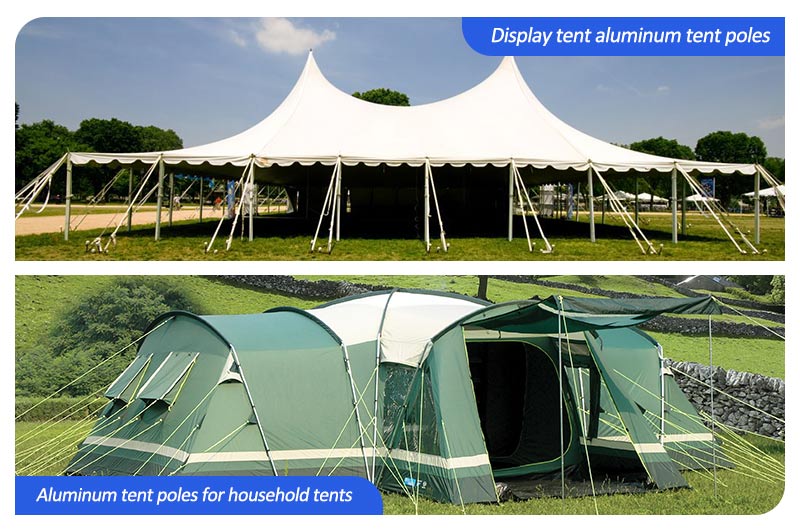
mât de tente
Différences entre l’anodisation et le revêtement en poudre
Anodisation
- Procédé chimique qui crée une couche d’oxyde durable sur des surfaces métalliques, principalement de l’aluminium.
- Améliore la résistance à la corrosion et la dureté de surface.
- Peut être clair ou coloré, offrant des options esthétiques.
- Fournit une finition uniforme qui est intégrée à la surface métallique.
- Résistant à la décoloration, à l’écaillage et aux rayures.
- Convient aux applications extérieures en raison de sa durabilité.
- Options de couleurs limitées par rapport au revêtement en poudre.
Poudre
- Revêtement moins cher que l’anodisation
- Application électrostatique de poudre sèche sur des surfaces métalliques, suivie d’un durcissement dans un four.
- Fournit un revêtement plus épais par rapport aux revêtements liquides traditionnels.
- Offre une large gamme d’options de couleurs, y compris des finitions métalliques et texturées.
- Peut être utilisé pour créer des effets décoratifs tels que des finitions brillantes, mates et satinées.
- Résistant aux chocs, aux produits chimiques et aux intempéries.
- Nécessite une bonne préparation de surface pour une adhérence optimale.
- Peut nécessiter des retouches périodiques ou un nouveau revêtement au fil du temps, en particulier dans les zones à forte usure.
Ces différences mettent en évidence les avantages et les applications distincts de chaque méthode de revêtement en fonction de facteurs tels que la durabilité, l’esthétique et les options de couleurs. Soumission rapide
L’application de l’anodisation de l’aluminium
- Établi et cadre antistatiques sur la ligne d’assemblage.
- Les matériaux de décoration du bâtiment tels que les murs-rideaux, les bâtiments, les bureaux, les centres commerciaux, les plafonds métalliques, etc.
- Produits électroniques 3C tels que les coques de téléphone portable et les coques d’ordinateur.
- Appareils ménagers et meubles, tels que panneau électrique, panneau d’armoire, panneau de réfrigérateur, panneau de meubles, etc.
- L’anodisation de l’aluminium est également largement utilisée dans les pièces mécaniques, les pièces d’avions et d’automobiles, les instruments de précision et les équipements radio, les coques de machines, les lampes et l’éclairage, l’artisanat, la décoration intérieure, les enseignes, la décoration automobile et d’autres industries.